Understanding PCB Traces
Definition and Purpose
A PCB trace, also known as a copper trace or a conductive track, is a thin strip of copper or other conductive material that is etched onto the surface of a PCB. These traces serve as the electrical pathways that connect various components on the board, allowing signals and power to flow between them. PCB traces are essentially the “wires” of a PCB, facilitating the transfer of electrical currents and enabling the proper functioning of the electronic circuit.
Composition and Materials
PCB traces are typically made of copper, which is an excellent conductor of electricity. Copper is chosen for its high conductivity, durability, and relatively low cost compared to other conductive materials. The copper used for PCB traces is usually electrodeposited or rolled onto the substrate material of the PCB, such as FR-4 (a glass-reinforced epoxy laminate).
In some specialized applications, other materials may be used for PCB traces. For example, in high-frequency circuits or RF (radio frequency) applications, traces may be made of materials with better high-frequency performance, such as gold or silver. However, copper remains the most common choice for the majority of PCB designs.
PCB Trace Characteristics
Width and Thickness
The width and thickness of PCB traces are critical factors that influence their electrical properties and current-carrying capacity. Trace width refers to the horizontal dimension of the trace, while thickness refers to the vertical dimension or the amount of copper deposited on the PCB surface.
Trace width is typically measured in mils (thousandths of an inch) or millimeters. The choice of trace width depends on several factors, including the current requirements of the circuit, the desired resistance, and the available space on the PCB. Wider traces can carry more current and have lower resistance, but they also occupy more space on the board.
Trace thickness, on the other hand, is measured in ounces of copper per square foot (oz/ft²) or microns (µm). The standard thickness for PCB traces is 1 oz/ft², which corresponds to a thickness of approximately 35 µm. Thicker traces can handle higher currents and provide better mechanical stability, but they also increase the manufacturing cost and may require special considerations during the PCB fabrication process.
Length and Resistance
The length of a PCB trace directly affects its electrical resistance. As the length of a trace increases, so does its resistance. This relationship is governed by the equation R = ρL/A, where R is the resistance, ρ (rho) is the resistivity of the material, L is the length of the trace, and A is the cross-sectional area of the trace.
Designers must carefully consider the length of PCB traces to ensure that the resistance remains within acceptable limits. Excessive resistance can lead to voltage drops, signal degradation, and power dissipation, which can negatively impact the performance and reliability of the electronic circuit.
To minimize the impact of trace length on resistance, designers may employ various techniques, such as using wider traces, using thicker copper, or optimizing the placement of components to reduce the overall trace length.
Impedance and Capacitance
In addition to resistance, PCB traces also exhibit impedance and capacitance, which are important characteristics in high-speed and high-frequency circuits.
Impedance refers to the total opposition to the flow of alternating current (AC) in a circuit, taking into account both resistance and reactance. In PCB design, controlling the impedance of traces is crucial for maintaining signal integrity and preventing reflections or distortions. The characteristic impedance of a trace depends on factors such as the trace geometry, the dielectric constant of the substrate material, and the proximity to other traces or planes.
Capacitance, on the other hand, is the ability of a trace to store electrical charge. PCB traces, along with the surrounding dielectric material, form small capacitors that can affect the propagation of signals. Excessive capacitance can lead to signal delays, crosstalk, and other issues that degrade the performance of the circuit.
To manage impedance and capacitance, PCB designers use various techniques, such as controlling the trace geometry, adjusting the spacing between traces, using ground planes, and employing impedance matching techniques.
PCB Trace Design Considerations
Current-Carrying Capacity
One of the primary considerations in PCB trace design is the current-carrying capacity, also known as the ampacity. The ampacity of a trace determines the maximum amount of current that can safely flow through it without causing excessive heating or damage to the PCB.
The current-carrying capacity of a trace depends on several factors, including the trace width, thickness, ambient temperature, and the maximum allowable temperature rise. Designers use established guidelines and formulas, such as the IPC-2152 standard, to calculate the appropriate trace width for a given current requirement.
Here’s an example table showing the relationship between trace width and current-carrying capacity for 1 oz/ft² copper thickness at an ambient temperature of 25°C and a maximum temperature rise of 10°C:
Trace Width (mm) | Current-Carrying Capacity (A) |
---|---|
0.2 | 0.5 |
0.4 | 1.0 |
0.8 | 2.0 |
1.6 | 4.0 |
3.2 | 8.0 |
It’s important to note that these values are approximate and may vary depending on the specific PCB design and environmental conditions.
Signal Integrity and Routing
Maintaining signal integrity is another crucial aspect of PCB trace design. Signal integrity refers to the ability of a trace to transmit a signal accurately and reliably from the source to the destination without distortion, reflection, or interference.
To ensure signal integrity, designers must carefully route the traces on the PCB, taking into account factors such as trace length, impedance matching, crosstalk, and electromagnetic interference (EMI). Some key considerations for signal integrity include:
- Minimizing trace length: Shorter traces have lower resistance, capacitance, and inductance, which helps to preserve signal quality and reduce delays.
- Impedance matching: Ensuring that the impedance of the trace matches the impedance of the source and load devices to prevent reflections and signal distortions.
- Crosstalk reduction: Minimizing the coupling between adjacent traces to prevent crosstalk, which can cause signal interference and errors.
- EMI mitigation: Implementing proper grounding, shielding, and filtering techniques to reduce the impact of EMI on sensitive signals.
Proper routing techniques, such as using balanced differential pairs, maintaining consistent trace geometries, and providing adequate spacing between traces, can help to optimize signal integrity in PCB designs.
Manufacturing Constraints
PCB trace design must also take into account the manufacturing constraints and limitations of the PCB fabrication process. Some key manufacturing considerations include:
- Minimum trace width and spacing: PCB manufacturers have specific guidelines for the minimum trace width and spacing that can be reliably produced. Designers must adhere to these guidelines to ensure manufacturability and avoid issues such as short circuits or open circuits.
- Copper thickness: The choice of copper thickness affects the current-carrying capacity and the ability to manufacture fine-pitch traces. Thicker copper may require special processing steps and increase the manufacturing cost.
- Via size and placement: Vias, which are conductive holes that connect traces on different layers of the PCB, must be designed with appropriate sizes and placement to ensure reliable connections and avoid manufacturing defects.
- Solder mask and silkscreen: The application of solder mask and silkscreen layers on the PCB can impact the trace design, requiring adequate clearances and adherence to manufacturing tolerances.
Designers must collaborate closely with PCB manufacturers and follow established design rules and guidelines to ensure that the PCB traces can be reliably and cost-effectively manufactured.
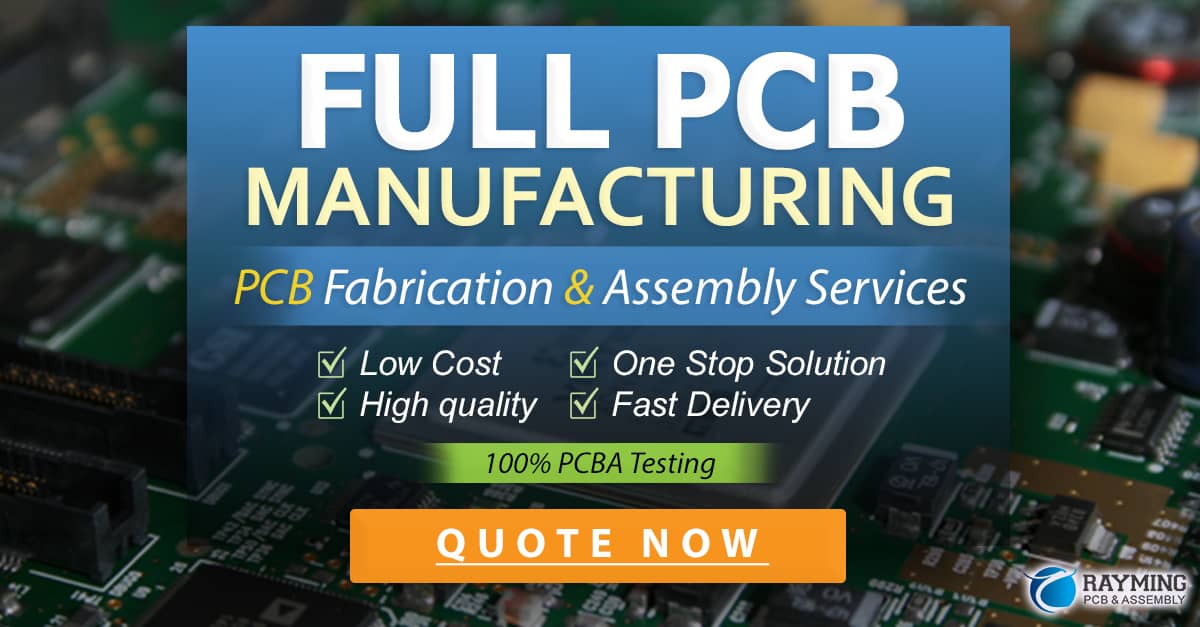
PCB Trace Simulation and Verification
To optimize PCB trace design and ensure the desired performance, designers often employ simulation and verification tools. These tools allow engineers to analyze and validate the electrical behavior of traces before committing to physical prototypes.
SPICE Simulation
SPICE (Simulation Program with Integrated Circuit Emphasis) is a widely used software tool for simulating the electrical characteristics of PCB traces and circuits. SPICE simulation allows designers to model the behavior of traces under various conditions, such as different frequencies, load impedances, and signal levels.
By running SPICE simulations, designers can analyze key parameters such as voltage drops, signal propagation delays, and impedance matching. This helps to identify potential issues and optimize the trace design for better performance and reliability.
Signal Integrity Analysis
Signal integrity analysis tools, such as eye diagrams and S-parameters, are used to assess the quality and integrity of signals transmitted through PCB traces. These tools help designers to visualize and quantify the impact of trace design on signal quality.
Eye diagrams provide a graphical representation of the signal waveform, allowing designers to evaluate parameters such as signal amplitude, jitter, and rise/fall times. S-parameters, on the other hand, characterize the frequency-dependent behavior of traces, including reflection, transmission, and crosstalk.
By performing signal integrity analysis, designers can fine-tune the trace design to minimize signal distortions, ensure adequate signal margins, and optimize the overall system performance.
Electromagnetic Compatibility (EMC) Analysis
EMC analysis tools are used to assess the electromagnetic compatibility of PCB traces and ensure compliance with relevant EMC standards and regulations. These tools simulate the electromagnetic fields generated by traces and predict their impact on nearby components and systems.
EMC analysis helps designers to identify potential sources of EMI, such as high-speed traces or poorly terminated connections, and implement appropriate mitigation techniques. This may involve adjusting trace routing, adding shielding or filtering components, or modifying the PCB stack-up to reduce electromagnetic coupling.
By conducting EMC analysis, designers can ensure that the PCB traces do not cause electromagnetic interference issues and meet the required EMC performance criteria.
PCB Trace Manufacturing and Inspection
Once the PCB trace design is finalized and validated, the next step is to manufacture the physical PCB. The manufacturing process involves several key steps to ensure the accurate and reliable fabrication of traces.
PCB Fabrication Process
The PCB fabrication process typically includes the following steps:
- Substrate preparation: The PCB substrate, usually FR-4, is cut to the required size and shape.
- Copper cladding: A thin layer of copper is laminated onto the substrate using heat and pressure.
- Photoresist application: A photosensitive material is applied to the copper surface.
- Exposure and development: The photoresist is exposed to light through a photomask, which defines the trace pattern. The unexposed areas are then chemically developed and removed.
- Etching: The exposed copper areas are chemically etched away, leaving the desired trace pattern.
- Resist stripping and cleaning: The remaining photoresist is stripped off, and the PCB is cleaned.
- Inspection and testing: The fabricated PCB undergoes visual inspection and electrical testing to ensure the quality and functionality of the traces.
Throughout the fabrication process, strict quality control measures are implemented to maintain the required trace dimensions, spacing, and electrical characteristics.
Trace Inspection Techniques
To ensure the quality and reliability of PCB traces, various inspection techniques are employed during and after the manufacturing process. Some common trace inspection techniques include:
- Visual inspection: Manual or automated visual inspection is performed to check for visible defects, such as incomplete etching, shorts, or open circuits.
- Automated optical inspection (AOI): AOI systems use high-resolution cameras and image processing algorithms to detect trace defects and deviations from the design specifications.
- Electrical testing: Continuity and isolation testing are performed to verify the electrical integrity of traces and ensure the absence of shorts or open circuits.
- Microsectioning: Destructive cross-sectional analysis of traces is sometimes performed to assess the trace dimensions, copper thickness, and adherence to the substrate.
- X-ray inspection: X-ray imaging is used to examine the internal structure of traces, particularly in multi-layer PCBs, to detect voids, delamination, or other hidden defects.
These inspection techniques help to identify and rectify any manufacturing defects or deviations, ensuring that the PCB traces meet the required quality standards and performance specifications.
Frequently Asked Questions (FAQ)
-
What is the difference between a PCB trace and a wire?
A PCB trace is a conductive pathway etched onto the surface of a printed circuit board, while a wire is a standalone conductor that is typically insulated and used for point-to-point connections. PCB traces are fixed and integral to the PCB, whereas wires are flexible and can be routed separately. -
Can PCB traces be repaired if damaged?
In some cases, damaged PCB traces can be repaired using techniques such as jumper wires, conductive epoxy, or manual soldering. However, the feasibility and reliability of the repair depend on the extent and location of the damage. In severe cases, it may be necessary to replace the entire PCB. -
What is the minimum trace width that can be manufactured?
The minimum trace width depends on the PCB manufacturing capabilities and the chosen fabrication process. Typical minimum trace widths range from 0.1 mm to 0.2 mm (4 to 8 mils) for standard PCB manufacturing. Advanced processes, such as high-density interconnect (HDI) or micro-via technology, can achieve even smaller trace widths. -
How do I calculate the current-carrying capacity of a PCB trace?
The current-carrying capacity of a PCB trace can be calculated using established formulas and guidelines, such as the IPC-2152 standard. The calculation takes into account factors such as trace width, thickness, ambient temperature, and maximum allowable temperature rise. Online calculators and design tools are available to assist with these calculations. -
What is the purpose of a ground plane in PCB trace design?
A ground plane is a large copper area on a PCB layer that serves as a low-impedance return path for electrical currents. Ground planes help to reduce electromagnetic interference, provide shielding, and maintain signal integrity by minimizing voltage differences and providing a stable reference for signals. They also improve the heat dissipation and mechanical stability of the PCB.
Conclusion
PCB traces are the fundamental building blocks of printed circuit boards, serving as the electrical pathways that connect components and enable the functioning of electronic devices. Understanding the characteristics, design considerations, and manufacturing processes of PCB traces is essential for creating reliable, high-performance electronic products.
This article has provided a comprehensive overview of PCB traces, covering their composition, electrical properties, design considerations, simulation and verification techniques, and manufacturing processes. By gaining a deep understanding of PCB traces, designers and engineers can make informed decisions, optimize their designs, and ensure the successful fabrication and operation of electronic systems.
As technology advances and electronic devices become increasingly complex, the importance of well-designed and manufactured PCB traces will only continue to grow. By staying up-to-date with the latest techniques, standards, and best practices in PCB trace design, engineers can push the boundaries of electronic innovation and create products that meet the ever-evolving demands of the market.
0 Comments