Introduction to PCB Thickness
Printed Circuit Board (PCB) thickness is a crucial factor in the design and manufacturing of electronic devices. It plays a significant role in determining the overall performance, reliability, and durability of the final product. In this comprehensive article, we will delve into the intricacies of PCB thickness, exploring its various aspects, considerations, and best practices.
Understanding PCB Thickness
PCB thickness is measured in mils (thousandths of an inch) or millimeters. The thickness of a PCB is determined by the number of layers it contains and the thickness of each individual layer. A typical PCB consists of multiple layers of conductive copper foil laminated together with insulating material, such as FR-4 or polyimide.
The standard thicknesses for PCBs range from 0.4mm to 3.2mm, with the most common being 1.6mm. However, the specific thickness required for a PCB depends on various factors, including the application, the components used, and the manufacturing process.
PCB Thickness (mm) | PCB Thickness (mils) | Common Applications |
---|---|---|
0.4 | 15.75 | Flexible PCBs |
0.8 | 31.5 | High-density designs |
1.6 | 63 | Most common thickness |
2.4 | 94.5 | High-power applications |
3.2 | 126 | Extreme environments |
Factors Influencing PCB Thickness Choice
1. Application Requirements
The intended application of the PCB is a primary factor in determining the appropriate thickness. For example, PCBs used in automotive or aerospace industries may require thicker boards to withstand harsh environments and vibrations. On the other hand, consumer electronics often prioritize thinner PCBs to enable sleek and compact designs.
2. Component Compatibility
The components used on the PCB also influence the thickness choice. Surface-mount devices (SMDs) and fine-pitch components require thinner PCBs to ensure proper soldering and avoid excessive heat buildup. Through-hole components, on the other hand, can accommodate thicker PCBs.
3. Manufacturing Capabilities
The manufacturing capabilities of the PCB fabricator play a crucial role in determining the achievable PCB thickness. Advanced manufacturing techniques, such as high-density interconnect (HDI) technology, enable the production of thinner PCBs with finer traces and smaller vias. However, not all fabricators have the same capabilities, so it’s essential to consider their limitations when selecting PCB thickness.
PCB Layer Stackup and Thickness
The layer stackup of a PCB refers to the arrangement and composition of the various layers within the board. It includes the conductive layers (copper), insulating layers (dielectric), and any additional layers such as solder mask or silkscreen.
Common Layer Stackups
1. Single-Layer PCB
A single-layer PCB consists of a single conductive layer, typically copper, laminated onto an insulating substrate. These PCBs are the thinnest and most cost-effective option, suitable for simple circuits and low-density designs.
2. Double-layer PCB
Double-layer PCBs have two conductive layers, one on each side of the insulating substrate. They offer more routing options and higher component density compared to single-layer PCBs. Double-layer PCBs are commonly used in a wide range of electronic devices.
3. Multi-layer PCB
Multi-layer PCBs consist of three or more conductive layers, alternating with insulating layers. They provide increased routing density, better signal integrity, and improved EMI shielding. Multi-layer PCBs are used in complex electronic systems, such as smartphones, computers, and medical devices.
Layer Thickness Considerations
The thickness of each layer in the PCB Stackup contributes to the overall thickness of the board. The copper layer thickness is typically expressed in ounces per square foot (oz/ft²), with common thicknesses being 0.5oz, 1oz, and 2oz. Thicker copper layers are used for high-current applications or to improve heat dissipation.
The insulating layers, or dielectric, also have varying thicknesses. The most common dielectric material is FR-4, with thicknesses ranging from 0.1mm to 0.4mm. The choice of dielectric thickness depends on the desired impedance, signal speed, and insulation requirements.
PCB Thickness and Signal Integrity
Signal integrity is a critical aspect of PCB design, as it ensures the reliable transmission of signals between components. PCB thickness plays a significant role in maintaining signal integrity.
Impedance Control
Impedance is the measure of opposition to the flow of electrical current in a circuit. Controlling impedance is essential for maintaining signal integrity and preventing reflections and distortions. PCB thickness, along with other factors such as trace width and spacing, influences the characteristic impedance of the traces.
Thinner PCBs allow for tighter impedance control, as the distance between the trace and the reference plane (ground or power) is reduced. This is particularly important for high-speed digital signals and RF applications.
Crosstalk and EMI
Crosstalk occurs when signals from one trace interfere with signals on adjacent traces. It can lead to signal distortion and errors in communication. Thicker PCBs with wider spacing between traces can help minimize crosstalk.
Electromagnetic interference (EMI) is another concern in PCB design. EMI can cause unintended radiation and disrupt the functioning of nearby electronic devices. Proper PCB thickness, along with techniques such as ground planes and shielding, can help mitigate EMI issues.
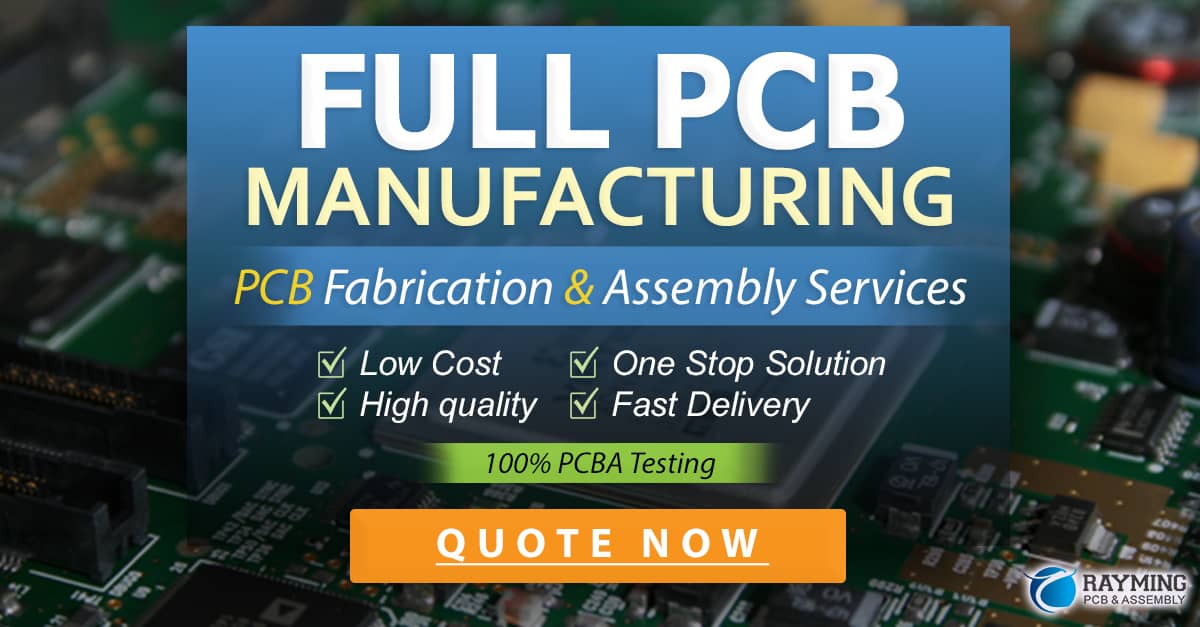
PCB Thickness and Thermal Management
Thermal management is crucial for the reliable operation and longevity of electronic devices. PCBs play a vital role in dissipating heat generated by components.
Thermal Conductivity
The thermal conductivity of the PCB material determines its ability to transfer heat away from components. FR-4, the most common PCB material, has a relatively low thermal conductivity compared to metals like copper or aluminum.
Thicker PCBs provide better thermal conductivity, as they have more material to distribute and dissipate heat. However, increasing PCB thickness solely for thermal management purposes may not always be practical or cost-effective.
Thermal Vias
Thermal vias are plated through-holes that are used to transfer heat from components to other layers or to an external heat sink. They provide a low-resistance path for heat flow and help improve thermal dissipation.
The effectiveness of thermal vias depends on factors such as via size, pitch, and placement. Thicker PCBs allow for larger and more numerous thermal vias, enhancing thermal management capabilities.
Best Practices for Selecting PCB Thickness
Selecting the appropriate PCB thickness involves balancing various factors and requirements. Here are some best practices to follow:
-
Consider the application: Evaluate the specific needs of your application, such as environmental conditions, reliability requirements, and space constraints. Choose a PCB thickness that aligns with these requirements.
-
Consult with the manufacturer: Engage with your PCB manufacturer early in the design process. They can provide valuable insights into their manufacturing capabilities, material options, and recommended thicknesses based on your design.
-
Optimize layer stackup: Carefully plan your layer stackup to achieve the desired electrical and mechanical properties. Consider the number of layers, copper thickness, and dielectric thickness to meet your requirements.
-
Conduct signal integrity analysis: Perform signal integrity simulations and analysis to ensure that your chosen PCB thickness and layer stackup maintain signal integrity and minimize issues like crosstalk and EMI.
-
Evaluate thermal requirements: Assess the thermal management needs of your design. If necessary, consider using thicker PCBs or incorporating thermal management techniques such as thermal vias or heat sinks.
-
Balancing cost and performance: Strive for a balance between cost and performance when selecting PCB thickness. Thicker PCBs may offer better performance but can also increase manufacturing costs. Evaluate the trade-offs and make an informed decision based on your project’s priorities.
Frequently Asked Questions (FAQ)
-
What is the most common PCB thickness?
The most common PCB thickness is 1.6mm (63 mils). This thickness provides a good balance between mechanical strength, electrical performance, and manufacturing ease for a wide range of applications. -
Can I use different thicknesses for different layers in a multi-layer PCB?
Yes, it is possible to use different thicknesses for different layers in a multi-layer PCB. This is known as a hybrid stackup. Hybrid stackups allow for optimizing the thickness of each layer based on its specific requirements, such as signal integrity or power handling. -
How does PCB thickness affect the cost?
Generally, thicker PCBs are more expensive to manufacture than thinner ones. This is because thicker PCBs require more material, longer processing times, and may have higher manufacturing complexity. However, the overall cost impact also depends on other factors such as the PCB size, layer count, and production volume. -
What are the challenges of using very thin PCBs?
Very thin PCBs, such as those below 0.8mm, can pose challenges in manufacturing and handling. They may be more prone to warping or damage during assembly and require specialized equipment and processes. Thin PCBs also have limitations in terms of power handling and thermal management capabilities. -
How do I determine the right PCB thickness for my design?
Determining the right PCB thickness for your design involves considering various factors, such as the application requirements, component compatibility, signal integrity, thermal management, and manufacturing capabilities. It’s recommended to consult with your PCB manufacturer and follow best practices to select the most suitable thickness for your specific project.
Conclusion
PCB thickness is a critical aspect of electronic design and manufacturing. It influences various factors, including signal integrity, thermal management, and mechanical stability. Understanding the complexities of PCB thickness and making informed decisions based on application requirements and manufacturing capabilities is essential for creating reliable and high-performance electronic devices.
By considering the factors discussed in this article, such as layer stackup, impedance control, thermal management, and best practices, designers can optimize their PCB designs and ensure the success of their projects. Engaging with PCB Manufacturers and leveraging their expertise can further streamline the design process and achieve the desired outcomes.
As technology advances and electronic devices continue to push the boundaries of performance and miniaturization, the importance of PCB thickness will only continue to grow. Staying up-to-date with the latest developments and best practices in PCB design and manufacturing is crucial for engineers and designers to stay ahead in this ever-evolving field.
0 Comments