Introduction to Flexible PCB
Flexible printed circuit boards (PCBs) have revolutionized the electronics industry by providing a versatile and compact solution for interconnecting electronic components in a wide range of applications. Unlike traditional rigid PCBs, flexible PCBs are made from thin, pliable materials that allow them to bend, fold, and conform to various shapes and sizes. This unique characteristic has made flexible PCBs indispensable in the design and manufacturing of compact, lightweight, and portable electronic devices.
What is a Flexible PCB?
A flexible PCB, also known as a flex circuit or flexible printed wiring board (FPC), is a type of printed circuit board that consists of a thin, flexible substrate with conductive traces and components mounted on its surface. The substrate is typically made from a flexible polymer material, such as polyimide or polyester, which provides excellent electrical insulation and mechanical stability.
Advantages of Flexible PCBs
Flexible PCBs offer several advantages over traditional rigid PCBs:
- Space Savings: Flexible PCBs can be bent, folded, and twisted to fit into tight spaces, allowing for more compact and lightweight device designs.
- Improved Reliability: The flexibility of the substrate reduces stress on components and solder joints, resulting in improved reliability and longer product life.
- Enhanced Signal Integrity: Flexible PCBs can be designed with controlled impedance and shorter signal paths, minimizing signal loss and interference.
- Reduced Assembly Costs: Flexible PCBs can integrate multiple circuit layers and components into a single, flexible assembly, reducing the number of connectors and simplifying the assembly process.
Applications of Flexible PCB
Flexible PCBs find applications in various industries and products where space constraints, weight reduction, and flexibility are critical factors. Some common applications include:
Consumer Electronics
Flexible PCBs are widely used in consumer electronics, such as smartphones, tablets, wearables, and digital cameras. They enable the design of slim, compact, and feature-rich devices by allowing the electronics to conform to the device’s shape and maximize the available space.
Medical Devices
Medical devices, such as implantable sensors, hearing aids, and diagnostic equipment, benefit from the use of flexible PCBs. The flexibility and biocompatibility of the substrate materials make them suitable for applications that require direct contact with the human body or need to adapt to its contours.
Automotive Electronics
In the automotive industry, flexible PCBs are used in various applications, such as instrument clusters, infotainment systems, and sensors. They provide a reliable and space-efficient solution for integrating electronics into the limited space available in modern vehicles.
Aerospace and Defense
Flexible PCBs are essential in aerospace and defense applications, where weight reduction, reliability, and performance are critical. They are used in avionics, satellite systems, and military equipment, where they must withstand harsh environmental conditions and meet stringent reliability requirements.
Design Considerations for Flexible PCB
Designing flexible PCBs requires careful consideration of several factors to ensure optimal performance and reliability. Some key design considerations include:
Material Selection
Choosing the right substrate material is crucial for the performance and reliability of a flexible PCB. Factors such as the operating temperature range, chemical resistance, and mechanical properties must be considered when selecting the substrate material. Common substrate materials include polyimide, polyester, and flexible polyethylene terephthalate (PET).
Trace Width and Spacing
The width and spacing of the conductive traces on a flexible PCB must be carefully designed to ensure proper electrical performance and signal integrity. The trace width and spacing depend on factors such as the current carrying capacity, signal frequency, and manufacturing constraints.
Bend Radius
The bend radius is a critical parameter in the design of flexible PCBs. It determines the minimum radius at which the PCB can be bent without causing damage to the substrate or components. The bend radius depends on the substrate material, copper thickness, and the number of layers in the PCB.
Strain Relief
Strain relief features, such as stiffeners and adhesives, are often incorporated into flexible PCB designs to minimize stress on components and solder joints during bending and flexing. These features help to improve the reliability and longevity of the PCB.
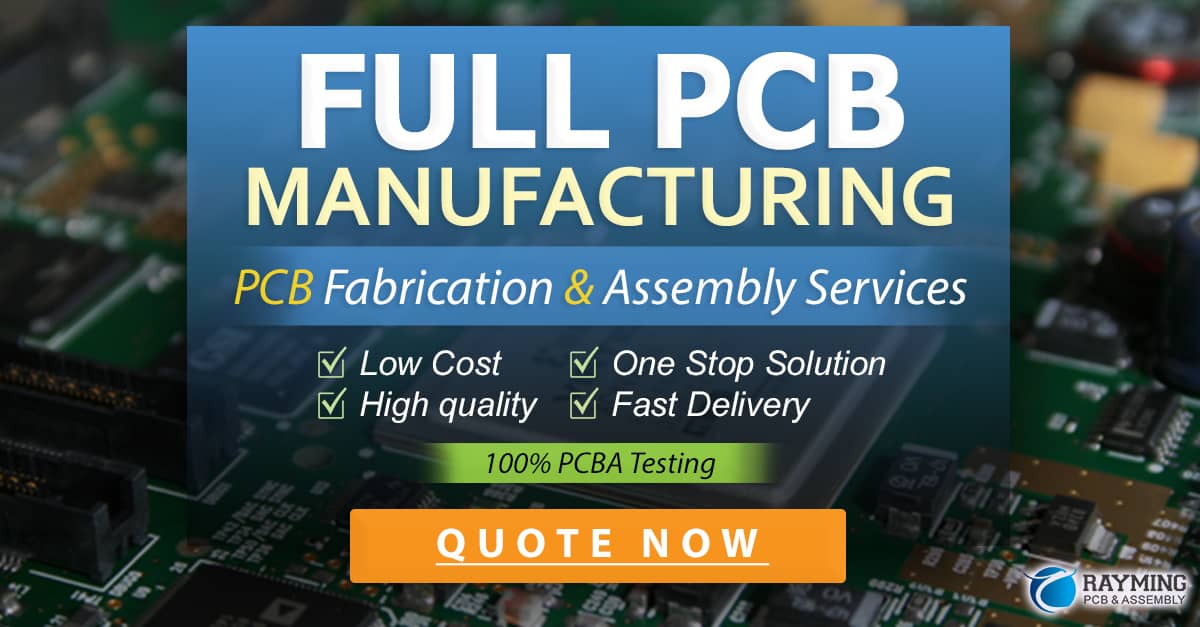
Manufacturing Process of Flexible PCB
The manufacturing process of flexible PCBs involves several steps, including:
- Substrate Preparation: The flexible substrate material is cleaned and treated to ensure proper adhesion of the conductive layers.
- Conductor Patterning: The conductive traces are patterned onto the substrate using techniques such as photolithography, screen printing, or etching.
- Lamination: Multiple layers of the patterned substrate are laminated together using adhesives and heat and pressure.
- Component Mounting: Electronic components are mounted onto the flexible PCB using surface mount technology (SMT) or through-hole mounting.
- Coverlay Application: A protective coverlay is applied to the PCB to provide insulation and protection against environmental factors.
- Singulation: The individual flexible PCBs are cut and separated from the panel using methods such as die-cutting or laser cutting.
Flexible PCB vs. Rigid PCB
While flexible PCBs offer several advantages over traditional rigid PCBs, it is essential to understand the differences between the two types to make an informed decision when selecting a PCB for a specific application.
Characteristic | Flexible PCB | Rigid PCB |
---|---|---|
Substrate Material | Thin, flexible polymer (e.g., polyimide, polyester) | Rigid, fiberglass-reinforced epoxy laminate (e.g., FR-4) |
Thickness | Typically 0.05 mm to 0.25 mm | Typically 0.8 mm to 3.2 mm |
Flexibility | Can be bent, folded, and twisted | Cannot be bent or flexed |
Space Savings | Allows for compact and lightweight designs | Limited by the rigid nature of the substrate |
Reliability | Improved reliability due to reduced stress on components and solder joints | More susceptible to stress-induced failures |
Cost | Generally higher than rigid PCBs due to specialized materials and manufacturing processes | Lower cost for high-volume production |
Frequently Asked Questions (FAQ)
-
Q: What is the typical thickness of a flexible PCB?
A: Flexible PCBs typically range in thickness from 0.05 mm to 0.25 mm, depending on the substrate material and the number of layers. -
Q: Can flexible PCBs be used in high-temperature applications?
A: Yes, flexible PCBs can be designed to withstand high temperatures by selecting appropriate substrate materials, such as polyimide, which can operate at temperatures up to 200°C. -
Q: How do flexible PCBs improve signal integrity compared to rigid PCBs?
A: Flexible PCBs can be designed with controlled impedance and shorter signal paths, minimizing signal loss and interference. The reduced stress on components and solder joints also contributes to improved signal integrity. -
Q: Are flexible PCBs more expensive than rigid PCBs?
A: In general, flexible PCBs are more expensive than rigid PCBs due to the specialized materials and manufacturing processes involved. However, the cost difference can be justified by the benefits of space savings, improved reliability, and enhanced performance. -
Q: Can flexible PCBs be used in applications that require frequent bending or flexing?
A: Yes, flexible PCBs are designed to withstand repeated bending and flexing. However, the number of flex cycles a PCB can endure depends on factors such as the substrate material, copper thickness, and the design of strain relief features.
Conclusion
Flexible PCBs have become an essential component in the design and manufacturing of compact, lightweight, and reliable electronic devices. Their unique ability to bend, fold, and conform to various shapes and sizes has enabled the development of innovative products across various industries, from consumer electronics to medical devices and aerospace applications.
When designing flexible PCBs, careful consideration must be given to material selection, trace width and spacing, bend radius, and strain relief to ensure optimal performance and reliability. The manufacturing process of flexible PCBs involves specialized techniques and materials that contribute to their higher cost compared to rigid PCBs.
As the demand for smaller, more feature-rich, and reliable electronic devices continues to grow, the importance of flexible PCBs in the electronics industry will only increase. By understanding the advantages, applications, and design considerations of flexible PCBs, engineers and manufacturers can leverage this technology to create innovative and high-performance products that meet the evolving needs of the market.
0 Comments