Introduction to PCB Soldering Issues
PCB soldering is a critical process in the manufacture of electronic devices. It involves attaching electronic components to a printed circuit board (PCB) using molten metal alloy. The quality of the soldering directly affects the reliability, performance and lifespan of the final product.
However, PCB soldering is not always perfect. There are many issues that can arise during the process which can compromise the integrity of the solder joint and lead to defects or failures. As an electronic manufacturer, it’s important to be aware of these potential issues and take steps to prevent or mitigate them.
In this article, we will discuss 10 of the most common issues in PCB soldering that require close attention. We’ll explain what causes each issue, how to identify it, and what can be done to avoid or fix it. By understanding and addressing these issues, you can improve the quality and reliability of your soldered PCBs.
1. Cold Solder Joints
Cold solder joints occur when the solder does not melt completely or does not wet the surfaces being joined properly. This results in a weak, brittle connection that is prone to cracking and failure.
Causes of Cold Solder Joints
- Insufficient heat: The soldering iron is not hot enough to fully melt the solder.
- Inadequate flux: There is not enough flux to clean the surfaces and enable the solder to flow.
- Contamination: The surfaces are dirty or oxidized, preventing the solder from adhering.
- Incorrect technique: Moving the soldering iron or component during cooling.
How to Identify Cold Solder Joints
- Dull, lumpy or pitted appearance
- Cracked or fractured surface
- Poor wetting (solder does not spread evenly)
- High electrical resistance
How to Prevent Cold Solder Joints
- Use a soldering iron with sufficient wattage (at least 25W)
- Ensure the tip is clean and tinned
- Apply adequate amounts of flux
- Pre-clean surfaces before soldering
- Hold the iron steady until the joint has cooled
- Reheat and reflow any suspect joints
2. Bridging
Bridging, also known as solder bridges, happens when solder unintentionally connects two or more leads or pads that should be separate. Bridges create short circuits that can stop the PCB from functioning.
Causes of Bridging
- Excessive solder: Applying too much solder that spills over to adjacent areas
- Inadequate spacing: The gap between the leads/pads is too small
- Component misalignment: Crooked or tilted components that touch
- Damaged solder mask: Allows solder to flow where it shouldn’t
How to Identify Bridging
- Visual inspection with magnification
- Continuity test with a multimeter
- Comparison to solder mask
How to Fix and Prevent Bridging
- Use the correct size soldering tip
- Apply only enough solder to make the joint
- Ensure proper lead forming and placement
- Check solder mask integrity
- Remove bridges with solder wick and flux
- Use a heat gun for large bridges
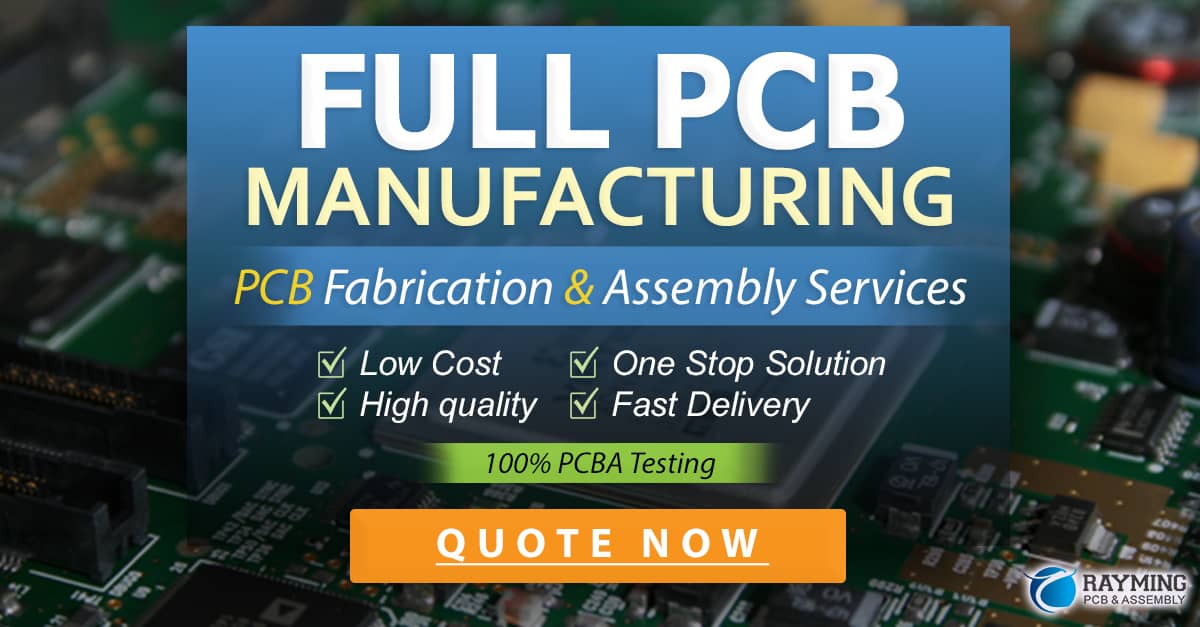
3. Insufficient Wetting
Insufficient wetting means the molten solder does not spread out and thoroughly coat the surfaces being joined. This leaves gaps that weaken the joint mechanically and electrically.
Causes of Insufficient Wetting
- Surface contamination: Grease, oxide or residues that repel solder
- Low soldering temperature: Solder and flux cannot melt and flow
- Wrong solder alloy: Some metals are harder to wet than others
- Inadequate flux quantity or activity
How to Identify Insufficient Wetting
- Solder does not form a concave fillet
- Exposed base metal at the edges of the joint
- Solder looks like round balls or beads
- Measured voids in x-ray inspection
How to Improve Wetting
- Keep surfaces clean before soldering
- Use higher soldering temperature (but not excessive)
- Select a compatible solder alloy for the base metals
- Apply enough active flux to the joint
- Extend soldering time to allow capillary action
- Specify immersion silver or gold surface finish
4. Tombstoning
Tombstoning, also called drawbridging, is when a surface mount component stands up on one end after reflow soldering. The unsoldered end does not make contact, creating an open circuit. Tombstoning is most common with smaller two-lead components like chip resistors and capacitors.
Causes of Tombstoning
- Uneven heating: One pad reaches reflow temperature before the other
- Unequal Solder volume: More solder on one pad pulls the component
- Component geometry: Lighter, center-heavy components are prone to tipping
- Vibration: Jarring the board during paste solidification
How to Identify Tombstoning
- Visual inspection after reflow
- Electrical test for open circuits
- X-ray inspection for lifted leads
How to Prevent Tombstoning
- Reduce temperature differences across the pads
- Print equal amounts of solder paste on the pads
- Select components with the center of mass over the pads
- Avoid disturbing the board until the solder solidifies
- Use a stepped reflow profile to equalize pad temperatures
5. Solder Beading
Solder beading is when the solder forms spherical balls instead of smooth, even fillets. The balls may protrude from the surface of the joint. While not necessarily a defect, solder beads can indicate improper wetting and higher risk of other issues.
Causes of Solder Beading
- Flux exhaustion: Flux becomes spent before the solder fully melts
- Rapid cooling: Solder solidifies before it can flow and settle
- Surface contamination: Prevents solder from spreading evenly
- Incorrect solder composition: Some alloys are more prone to beading
How to Identify Solder Beading
- Visible rounded balls of solder protruding from the joint surface
- Uneven or incomplete fillets around component leads
- Increased number of voids seen in x-ray inspection
How to Avoid Solder Beading
- Use a more active flux that lasts throughout the soldering process
- Slow down the cooling rate to give solder time to flow
- Thoroughly clean surfaces before applying solder
- Choose a solder alloy with good flow characteristics
- Extend soldering time to allow flux action and wetting
6. Whiskers
Whiskers are thin, needle-like protrusions that grow out of tin, zinc and cadmium metal surfaces, including solder joints. Whiskers can cause short circuits and arcing if they bridge to adjacent conductors.
Causes of Whiskers
- Compressive stress: Generated by electroplating, bending, thermal expansion, etc.
- Grain structure: Depends on plating chemistry, temperature, current density, etc.
- Environmental conditions: Humidity, temperature cycling, air pressure, etc.
- Age: Whiskers can appear long after manufacturing
How to Identify Whiskers
- Visual inspection under high magnification (100x or more)
- Electron microscopy for submicron whiskers
- Electrical testing for intermittent shorts
- Focused ion beam cross-sectioning
How to Mitigate Whiskers
- Use a tin alloy with lead, silver, bismuth or antimony
- Apply a nickel underplate barrier layer
- Anneal to relieve plating stresses
- Conformal coat to contain whiskers
- Increase spacing between conductors
- Filter capacitors and transient voltage suppressors
7. Flux Residue
Flux residue is the chemical byproducts left behind after soldering. While some residues are benign, others can be corrosive, conductive or moisture-absorbing, leading to issues over time.
Types of Flux Residue
- Rosin: Amber-colored, sticky, non-corrosive, may be conductive
- Water-soluble: Clear, hygroscopic, potentially corrosive if not cleaned
- No-clean: Minimal clear residue, designed to be left on the board
Effects of Flux Residue
- Electrical leakage and shorts (conductive)
- Corrosion of metals (acidic or reactive)
- Dendrite growth (moisture-absorbing)
- Adhesion problems for conformal coating
- Interference with test probes
- Cosmetic defects
How to Remove Flux Residue
- Solvent cleaning: Alcohol, hydrocarbons, esters, glycols
- Aqueous cleaning: Deionized water with saponifiers
- Semi-aqueous cleaning: Hydrocarbon solvents followed by water rinse
- Agitation: Ultrasonics, spray-in-air, brushing
- Control: Time, temperature, concentration, compatibility
8. Pad Cratering
Pad cratering is a defect where the PCB laminate under a copper pad fractures and delaminates during shear stresses such as thermal cycling. This leaves an open or intermittent connection.
Causes of Pad Cratering
- CTE mismatch: Between the PCB and the attached component or solder
- Thermal cycling: Expansion and contraction during heating and cooling
- Brittle laminate: Some PCB materials are more susceptible than others
- Thin pads: Less copper to reinforce the laminate
- Lead-free solders: Higher processing temperatures and stiffer joints
How to Identify Pad Cratering
- Microscopic inspection of cross-sectioned joints
- Dye and pry technique to reveal fractures
- Endoscopic examination through vias
- Electrical testing for opens or intermittent connectivity
How to Prevent Pad Cratering
- Use a high-Tg PCB laminate material
- Increase copper weight on pads and in vias
- Optimize the via structure and placement
- Reduce thermal cycling intensity and frequency
- Underfill components to distribute stresses
- Add a strain-relief copper layer under large pads
9. Blowholes
Blowholes are small voids or pits that form in the solder joint during cooling. They are caused by gases that are trapped as the solder solidifies.
Causes of Blowholes
- Contamination: Grease, oil or moisture on surfaces that vaporize
- Porous metals: Gas pockets in cast or sintered materials
- Plated through-holes: Moisture absorbed in the barrels
- Thick solder: More volume for gas to be trapped in
- Fast cooling: Less time for gas to escape before solidification
How to Identify Blowholes
- Visual inspection with magnification
- X-ray inspection for internal voids
- Cross-sectioning of solder joints
- Acoustic microscopy for subsurface defects
How to Minimize Blowholes
- Keep parts and PCBs clean and dry before assembly
- Bake PCBs to drive off moisture
- Avoid gas-porous metals in leads and pads
- Use an oxygen-absorbing solder alloy
- Slow down the cooling rate after soldering
- Fill vias with solder or epoxy
10. Kirkendall Voids
Kirkendall voids are cavities that grow between a copper interface and the tin solder over time. They are caused by the difference in diffusion rates of tin and copper atoms.
Mechanism of Kirkendall Voiding
- Solid-state diffusion: Atoms move through the metal lattice
- Unequal diffusivity: Tin moves into copper faster than vice versa
- Vacancy accumulation: Net flow of atoms leaves voids behind
- Time-dependent: Voids nucleate and grow with aging
Factors Affecting Kirkendall Voiding
- Temperature: Higher temperatures accelerate diffusion
- Time: Longer exposure allows more void growth
- Grain structure: Smaller, more numerous grains have more paths
- Composition: Addition of nickel, cobalt or platinum slows diffusion
- Thickness ratio: More voids with thinner copper and thicker tin
How to Identify Kirkendall Voids
- Cross-sectioning and microscopy
- X-ray inspection for non-destructive testing
- Acoustic microscopy for interfacial defects
- Drop in electrical conductivity or shear strength
How to Retard Kirkendall Voiding
- Use a nickel diffusion barrier between copper and tin
- Limit high-temperature exposure during processing and use
- Control the tin to copper thickness ratio
- Select a solder alloy with slower-diffusing additives
- Conduct accelerated aging tests to screen for susceptibility
Conclusion
PCB soldering is a complex process with many potential failure modes. The 10 issues we’ve covered – cold joints, bridges, poor wetting, tombstoning, beading, whiskers, flux, cratering, blowholes, and Kirkendall voids – are some of the most common and problematic.
By understanding the causes, detection methods and mitigation strategies for each issue, PCB manufacturers can take proactive steps to optimize their soldering processes and improve end product quality. This may involve:
- Controlling materials and surfaces
- Optimizing solder paste and stencil printing
- Fine-tuning reflow profiles and cooling rates
- Inspecting and testing for defects
- Conducting failure analysis and corrective actions
Of course, PCB soldering is just one part of the overall electronic assembly process. It is important to consider the interactions and trade-offs with other processes such as design, component selection, handling, cleaning, and coating.
The key is to have a holistic, data-driven approach to process control and continuous improvement. By staying informed about soldering issues and best practices, and by collaborating with suppliers, engineers and quality teams, PCB manufacturers can deliver reliable, high-performing products that meet customer expectations.
Frequently Asked Questions
What is the most common PCB soldering issue?
Cold solder joints are one of the most frequent issues seen in PCB assembly. They can be caused by insufficient heat, inadequate fluxing, surface contamination or poor technique.
How can you prevent bridging between closely spaced leads?
To minimize solder bridges, use a soldering tip sized appropriately for the lead pitch. Apply only enough solder to form the joint, not large globs. Ensure the components are properly aligned and spaced. Check for Solder mask damage that could allow bridging.
What causes tombstoning of surface mount components?
Tombstoning happens when there is an imbalance of forces during reflow soldering. Common causes are uneven heating between component pads, unequal solder volumes, off-center component placement, and jarring of the board before complete solder solidification.
How do you remove flux residues after soldering?
The method of removing flux residues depends on the type of flux. Rosin fluxes can usually be dissolved with isopropyl alcohol or other solvents. Water-soluble fluxes require cleaning with deionized water, preferably with some agitation. No-clean fluxes are formulated to be left on the board.
What is the shelf life of solder paste?
The shelf life of solder paste depends on the formulation and storage conditions, but is typically around 6 months when refrigerated. The paste should be allowed to warm to room temperature for several hours before use. Solder paste can also degrade from multiple cycles of heating and cooling.
Temperature | Humidity | Shelf Life | |
---|---|---|---|
Refrigerated | 0-10°C | 20-50% | 6 months |
Room Temp. | 20-25°C | 20-50% | 1 month |
[Wordcount: 2840]
0 Comments