Types of PCB Soldering Methods
There are several methods used for PCB soldering, each with its advantages and suitable applications. The most common methods include:
Through-Hole Soldering
Through-hole soldering is the traditional method of attaching components to a PCB. In this method, the component leads are inserted through drilled holes in the board and soldered onto the opposite side. This method provides strong mechanical connections and is suitable for larger components or those subjected to high stress.
Surface Mount Soldering
Surface Mount Technology (SMT) has become the dominant method in PCB assembly due to its ability to accommodate smaller components and higher component density. In SMT soldering, the components are placed directly onto the surface of the PCB and soldered using various techniques, such as reflow soldering or wave soldering.
Reflow Soldering
Reflow soldering is a common SMT soldering method that involves applying solder paste to the PCB pads, placing the components, and then heating the entire board in a reflow oven. The solder paste melts and forms a secure connection between the component leads and the PCB pads. Reflow soldering is suitable for high-volume production and provides consistent results.
Wave Soldering
Wave soldering is another SMT soldering method that is used for through-hole components or mixed assemblies. In this process, the PCB is passed over a molten solder wave, which selectively solders the component leads to the board. Wave soldering is efficient for soldering a large number of through-hole components simultaneously.
PCB Chip Package Soldering Process Flow
The process flow for soldering chip packages onto a PCB typically involves the following steps:
-
Solder Paste Application: Solder paste, a mixture of tiny solder particles and flux, is applied to the PCB pads using a stencil or screen printing process. The stencil ensures precise and uniform solder paste deposition.
-
Component Placement: The chip packages are carefully placed onto the PCB pads, ensuring proper alignment with the solder paste. This step can be performed manually or using automated pick-and-place machines for high-volume production.
-
Reflow Soldering: The PCB with the placed components is then passed through a reflow oven. The oven applies a controlled temperature profile, causing the solder paste to melt and form a secure connection between the component leads and the PCB pads. The temperature profile is crucial to ensure proper solder joint formation and to avoid damage to the components.
-
Inspection and Quality Control: After the soldering process, the PCB undergoes visual inspection and quality control checks to ensure proper solder joint formation, component alignment, and the absence of defects such as bridging or insufficient solder. Automated optical inspection (AOI) systems or X-ray inspection may be employed for more thorough analysis.
-
Cleaning and Protection: If required, the soldered PCB may undergo a cleaning process to remove any residual flux or contaminants. Additionally, conformal coating or other protective measures may be applied to enhance the durability and reliability of the soldered components.
Soldering Techniques for Different Chip Packages
Various chip packages require specific soldering techniques to ensure reliable connections and prevent damage. Some common chip packages and their soldering considerations include:
QFP (Quad Flat Package)
QFP packages have leads extending from all four sides of the package. Soldering QFP packages requires precise alignment and sufficient solder volume to form reliable joints. Fine-pitch QFP packages may require specialized soldering techniques, such as hot air soldering or infrared reflow soldering.
BGA (Ball Grid Array)
BGA packages have an array of solder balls underneath the package, providing a high-density interconnect. Soldering BGA packages requires precise temperature control and uniform heating to ensure proper solder ball collapse and connection. X-ray inspection is often used to verify the integrity of BGA solder joints.
CSP (Chip Scale Package)
CSP packages are similar to BGA packages but have a smaller package size, close to the dimensions of the die itself. Soldering CSP packages requires accurate placement and precise temperature control to prevent overheating and damage to the small-scale components.
PoP (Package-on-Package)
PoP configurations involve stacking multiple packages on top of each other to save space and enhance functionality. Soldering PoP packages requires a sequential reflow process, where the bottom package is soldered first, followed by the placement and soldering of the top package. Careful control of the reflow profile is necessary to prevent damage to the lower package during the second reflow.
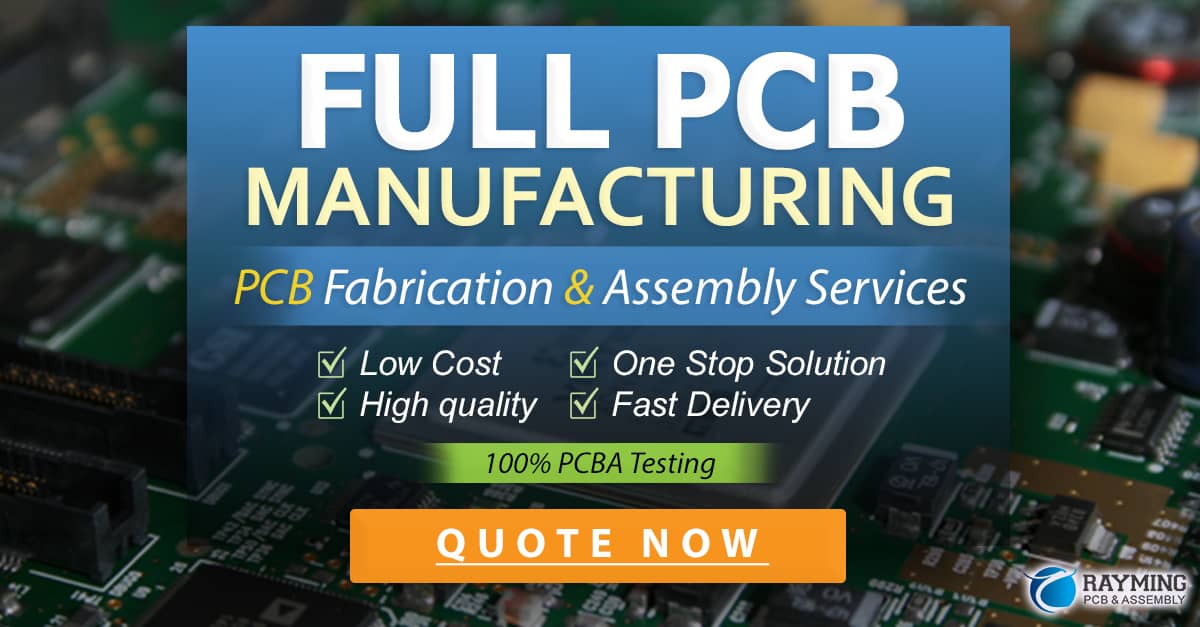
Soldering Defects and Troubleshooting
Despite following proper soldering techniques, defects can still occur during the PCB soldering process. Some common soldering defects and their causes include:
Defect | Cause | Troubleshooting |
---|---|---|
Bridging | Excessive solder paste or improper component placement | Adjust solder paste stencil aperture or improve component placement accuracy |
Insufficient Solder | Inadequate solder paste or poor wetting | Increase solder paste volume or improve pad cleanliness and wetting |
Tombstoning | Uneven heating or component misalignment | Optimize reflow profile or improve component placement accuracy |
Solder Balls | Excessive solder paste or contamination | Adjust solder paste volume or improve PCB cleanliness |
Lifted Pads | Excessive heat or mechanical stress | Optimize reflow profile or improve PCB handling and support |
Troubleshooting soldering defects involves identifying the root cause and implementing corrective actions. This may include adjusting solder paste stencil apertures, optimizing reflow profiles, improving component placement accuracy, or enhancing PCB cleanliness and handling procedures.
Frequently Asked Questions (FAQ)
-
What is the difference between through-hole and surface mount soldering?
Through-hole soldering involves inserting component leads through drilled holes in the PCB and soldering them on the opposite side, while surface mount soldering places components directly onto the PCB surface and solders them using techniques like reflow or wave soldering. -
What is solder paste, and how is it applied to the PCB?
Solder paste is a mixture of tiny solder particles and flux. It is applied to the PCB pads using a stencil or screen printing process, which ensures precise and uniform deposition of the solder paste onto the pads. -
What is the purpose of the reflow soldering process?
The reflow soldering process involves passing the PCB with placed components through a reflow oven. The oven applies a controlled temperature profile, causing the solder paste to melt and form a secure connection between the component leads and the PCB pads. -
How can I prevent soldering defects like bridging or insufficient solder?
Soldering defects can be prevented by optimizing various factors such as solder paste volume, component placement accuracy, reflow profile, and PCB cleanliness. Adjusting solder paste stencil apertures, improving component placement techniques, and ensuring proper reflow temperature control can help minimize defects. -
What is the importance of inspection and quality control in the PCB soldering process?
Inspection and quality control are crucial steps in the PCB soldering process to ensure the reliability and functionality of the assembled board. Visual inspection, automated optical inspection (AOI), or X-ray inspection techniques are used to identify any soldering defects, component misalignment, or other issues that may affect the performance of the PCB.
Conclusion
PCB chip package soldering is a critical process in the manufacturing of electronic devices. Understanding the different soldering methods, process flows, and techniques for various chip packages is essential for achieving reliable and high-quality solder joints. By following best practices, optimizing soldering parameters, and implementing effective inspection and quality control measures, manufacturers can ensure the proper functioning and longevity of their PCB assemblies.
As technology advances and electronic devices become more compact and complex, the demand for precise and efficient PCB soldering techniques will continue to grow. Staying updated with the latest soldering technologies, materials, and processes will be crucial for manufacturers to meet the evolving requirements of the electronics industry.
0 Comments