Introduction to QFP Packages and Solder Paste
Quad Flat Package (QFP) is a surface-mounted integrated circuit package with leads extending from each of the four sides. QFP packages are widely used in various electronic applications due to their compact size, high lead count, and good thermal and electrical performance. To ensure reliable solder joints between the QFP leads and the printed circuit board (PCB) pads, it is crucial to apply the correct volume of solder paste during the assembly process.
Solder paste is a mixture of tiny solder particles suspended in a flux matrix. It is applied to the PCB pads prior to component placement and acts as both the electrical and mechanical connection between the component leads and the PCB pads during the reflow soldering process. The volume of solder paste applied to each pad directly affects the quality and reliability of the resulting solder joint.
Importance of Solder Paste Volume
Applying the optimal amount of solder paste is essential for several reasons:
-
Sufficient solder joint strength: An adequate volume of solder paste ensures that the solder joint has enough solder material to form a strong and reliable connection between the QFP lead and the PCB pad.
-
Preventing solder bridging: Excessive solder paste can lead to solder bridging, where solder inadvertently connects adjacent leads or pads, causing short circuits and potentially damaging the device.
-
Minimizing solder voids: Insufficient solder paste can result in solder voids, which are small gaps or pockets within the solder joint that can weaken the connection and lead to intermittent or complete failure of the joint.
-
Ensuring proper wetting: The right amount of solder paste promotes proper wetting, allowing the molten solder to flow evenly across the surfaces of the lead and pad, creating a strong and reliable bond.
Factors Affecting Solder Paste Volume
Several factors influence the optimal solder paste volume for QFP packages, including:
1. Lead Pitch and Size
The lead pitch, which is the distance between the centers of adjacent leads, and the size of the leads themselves play a significant role in determining the appropriate solder paste volume. Smaller lead pitches and sizes require less solder paste to form reliable joints, while larger pitches and sizes may need more solder paste to ensure adequate coverage and strength.
Common QFP lead pitches and their typical solder paste volumes:
Lead Pitch | Typical Solder Paste Volume (per lead) |
---|---|
0.5 mm | 0.2-0.4 mm³ |
0.4 mm | 0.1-0.3 mm³ |
0.3 mm | 0.05-0.2 mm³ |
2. PCB Pad Design
The design of the PCB pads, including their size, shape, and surface finish, can affect the amount of solder paste required. Larger pads may accommodate more solder paste, while smaller pads may need less. The shape of the pad, such as rectangular or oval, can also influence the solder paste volume and the resulting solder joint shape.
3. Stencil Thickness and Aperture Design
Solder paste is typically applied to the PCB using a stencil, which is a thin metal sheet with openings (apertures) that correspond to the PCB pads. The thickness of the stencil and the design of the apertures directly impact the volume of solder paste deposited on each pad.
Thicker stencils deposit more solder paste, while thinner stencils deposit less. The aperture design, including its size, shape, and wall tapering, also affects the solder paste volume and release characteristics.
Common stencil thicknesses and their impact on solder paste volume:
Stencil Thickness | Impact on Solder Paste Volume |
---|---|
0.1 mm | Low |
0.15 mm | Medium |
0.2 mm | High |
4. Solder Paste Properties
The properties of the solder paste itself, such as the alloy composition, particle size distribution, and viscosity, can influence the optimal solder paste volume. Different solder paste formulations may have varying printability, slump resistance, and reflow characteristics, which can affect the amount of solder paste needed for reliable joints.
Calculating Solder Paste Volume
To determine the optimal solder paste volume for a QFP package, several methods can be employed:
1. Manufacturer Recommendations
QFP package manufacturers often provide guidelines for solder paste volume based on the lead pitch and size of their specific packages. These recommendations serve as a good starting point for determining the appropriate solder paste volume.
Example manufacturer recommendations for solder paste volume:
QFP Package | Lead Pitch | Recommended Solder Paste Volume (per lead) |
---|---|---|
64-lead QFP | 0.5 mm | 0.3 mm³ |
100-lead QFP | 0.4 mm | 0.2 mm³ |
144-lead QFP | 0.3 mm | 0.1 mm³ |
2. Empirical Testing
Conducting empirical tests using different solder paste volumes can help determine the optimal amount for a specific QFP package and PCB design. By assembling test boards with varying solder paste volumes and evaluating the resulting solder joints, engineers can identify the volume that yields the best results in terms of joint strength, reliability, and appearance.
3. Calculation Based on Aperture Volume
The solder paste volume can also be calculated based on the volume of the stencil aperture and the area ratio (AR) between the aperture and the PCB pad. The area ratio is the ratio of the aperture area to the pad area, and it affects the transfer efficiency of the solder paste from the stencil to the pad.
The aperture volume can be calculated using the following formula:
Aperture Volume = Aperture Length × Aperture Width × Stencil Thickness
The solder paste volume deposited on the pad can then be estimated using the area ratio:
Solder Paste Volume = Aperture Volume × Area Ratio
Example calculation for a rectangular aperture and pad:
Parameter | Value |
---|---|
Aperture Length | 0.6 mm |
Aperture Width | 0.3 mm |
Stencil Thickness | 0.15 mm |
Pad Length | 0.7 mm |
Pad Width | 0.4 mm |
Aperture Volume = 0.6 mm × 0.3 mm × 0.15 mm = 0.027 mm³
Pad Area = 0.7 mm × 0.4 mm = 0.28 mm²
Aperture Area = 0.6 mm × 0.3 mm = 0.18 mm²
Area Ratio = 0.18 mm² ÷ 0.28 mm² = 0.643
Solder Paste Volume = 0.027 mm³ × 0.643 = 0.017 mm³
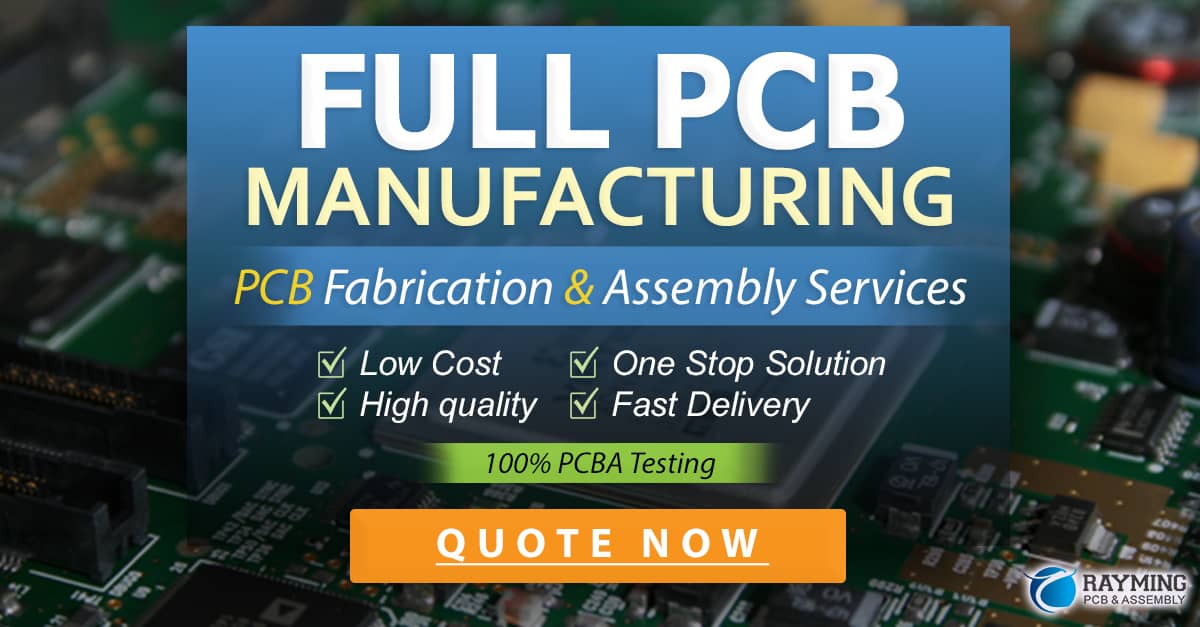
Controlling Solder Paste Volume
To ensure consistent and reliable solder paste deposition, several control measures can be implemented:
1. Stencil Design Optimization
Optimizing the stencil design, including aperture dimensions and wall tapering, can help achieve the desired solder paste volume and improve the transfer efficiency. Proper aperture design ensures that the solder paste releases cleanly from the stencil and deposits evenly on the pads.
2. Solder Paste Inspection (SPI)
Solder Paste Inspection (SPI) systems use 2D or 3D imaging techniques to measure the volume, height, and area of solder paste deposits on the PCB pads after stencil printing. SPI allows for real-time monitoring and correction of solder paste volume inconsistencies, ensuring that each pad receives the appropriate amount of solder paste.
3. Stencil Cleaning and Maintenance
Regular cleaning and maintenance of the stencil are essential for maintaining consistent solder paste deposition. Solder paste residue can accumulate on the stencil surface and aperture walls, affecting the paste release and volume. Proper cleaning procedures, such as using automated stencil cleaners or manual cleaning with appropriate solvents, help ensure optimal solder paste transfer.
4. Print Process Control
Controlling the print process parameters, such as squeegee pressure, speed, and separation distance, can help achieve consistent solder paste volume. Proper squeegee pressure ensures even solder paste distribution across the stencil, while appropriate speed and separation distance help prevent solder paste slumping or smearing.
Troubleshooting Solder Paste Volume Issues
When encountering issues related to solder paste volume, several troubleshooting steps can be taken:
1. Insufficient Solder Paste Volume
If the solder paste volume is insufficient, resulting in weak or incomplete solder joints, consider the following actions:
– Increase the stencil thickness to deposit more solder paste
– Enlarge the aperture dimensions to allow more solder paste to be deposited
– Adjust the print process parameters, such as increasing squeegee pressure or reducing print speed, to improve solder paste transfer
2. Excessive Solder Paste Volume
If the solder paste volume is excessive, leading to solder bridging or large solder balls, consider the following actions:
– Reduce the stencil thickness to deposit less solder paste
– Decrease the aperture dimensions to limit the amount of solder paste deposited
– Adjust the print process parameters, such as reducing squeegee pressure or increasing print speed, to decrease solder paste transfer
3. Inconsistent Solder Paste Volume
If the solder paste volume is inconsistent across the PCB, resulting in varying solder joint quality, consider the following actions:
– Ensure proper stencil cleaning and maintenance to prevent solder paste buildup or contamination
– Verify the alignment between the stencil and the PCB to ensure accurate solder paste deposition
– Monitor the print process parameters to maintain consistent settings throughout the production run
Frequently Asked Questions (FAQ)
-
What is the impact of insufficient solder paste volume on QFP solder joints?
Insufficient solder paste volume can lead to weak or incomplete solder joints, resulting in poor electrical and mechanical connections between the QFP leads and the PCB pads. This can cause intermittent failures, increased resistance, or even complete joint failure. -
How does excessive solder paste volume affect QFP assembly?
Excessive solder paste volume can cause solder bridging, where solder inadvertently connects adjacent leads or pads, leading to short circuits. It can also result in large solder balls or solder spatter, which may cause contamination or damage to nearby components. -
What are the common causes of inconsistent solder paste volume?
Inconsistent solder paste volume can be caused by various factors, such as improper stencil cleaning or maintenance, misalignment between the stencil and the PCB, and variations in print process parameters like squeegee pressure or speed. -
How can solder paste inspection (SPI) systems help control solder paste volume?
SPI systems use 2D or 3D imaging to measure the volume, height, and area of solder paste deposits on PCB pads after stencil printing. This allows for real-time monitoring and correction of solder paste volume inconsistencies, ensuring that each pad receives the appropriate amount of solder paste. -
What steps can be taken to troubleshoot solder paste volume issues?
To troubleshoot solder paste volume issues, consider adjusting the stencil thickness, aperture dimensions, or print process parameters like squeegee pressure and speed. Ensure proper stencil cleaning and maintenance, verify the alignment between the stencil and the PCB, and monitor the print process parameters for consistency.
Conclusion
Achieving the optimal solder paste volume is crucial for ensuring reliable and high-quality solder joints in QFP assembly. By understanding the factors that influence solder paste volume, such as lead pitch, PCB pad design, stencil thickness, and aperture design, engineers can determine the appropriate volume for their specific application.
Implementing control measures, such as stencil design optimization, solder paste inspection, and print process control, helps maintain consistent solder paste deposition. When issues arise, troubleshooting steps can be taken to address insufficient, excessive, or inconsistent solder paste volume.
By carefully considering and managing solder paste volume, manufacturers can produce reliable and robust QFP assemblies, minimizing defects and ensuring optimal performance of the final electronic product.
0 Comments