Introduction to HDI PCB Technology
High Density Interconnect (HDI) PCBs have revolutionized the electronics industry by enabling the creation of smaller, lighter, and more powerful devices. HDI PCBs feature finer lines and spaces, smaller vias, and higher connection pad density compared to traditional PCBs. This advanced technology allows for the miniaturization of electronic components and the development of highly complex circuits.
Benefits of HDI PCBs
- Reduced size and weight
- Improved signal integrity
- Enhanced electrical performance
- Increased reliability
- Cost-effective for high-volume production
HDI PCB Design Considerations
When designing HDI PCBs, several factors must be taken into account to ensure optimal performance and manufacturability.
Signal Integrity
Signal integrity is crucial in HDI PCB design. To maintain signal quality, designers should consider the following:
- Controlled impedance
- Differential pair routing
- Minimizing crosstalk and electromagnetic interference (EMI)
Layer Stack-up
The layer stack-up of an HDI PCB plays a significant role in its performance. A typical HDI PCB stack-up may include:
Layer | Description |
---|---|
Top Layer | Signal layer, components, and fine-pitch BGAs |
Ground Plane | Provides shielding and reduces EMI |
Signal Layers | Internal signal routing layers |
Power Plane | Distributes power to components |
Bottom Layer | Signal layer, components, and fine-pitch BGAs |
Via Types and Placement
HDI PCBs utilize various types of vias for interconnections between layers:
- Microvia: Blind or buried vias with diameters less than 150 microns
- Buried via: Connects internal layers without reaching the surface
- Through-hole via: Connects all layers from top to bottom
Via placement is critical to ensure proper signal routing and to avoid manufacturing issues. Designers should adhere to manufacturer guidelines for via size, spacing, and aspect ratio.
HDI PCB Manufacturing Process
The manufacturing process for HDI PCBs is more complex than traditional PCBs due to the smaller features and higher density. The process typically involves the following steps:
- Material selection
- Drilling and plating of microvias
- Patterning and etching of circuit layers
- Lamination of multiple layers
- Drilling and plating of through-hole vias
- Surface finishing (e.g., ENIG, HASL, or OSP)
- Solder mask application
- Silkscreen printing
- Electrical testing and inspection
Material Selection
The choice of materials for HDI PCBs is critical to ensure reliability and performance. Common materials include:
- FR-4: A glass-reinforced epoxy laminate with good mechanical and electrical properties
- High-Tg FR-4: An enhanced version of FR-4 with better thermal stability
- Polyimide: A high-performance material with excellent thermal and chemical resistance
Surface Finishes
Surface finishes protect the exposed copper on PCBs and provide a solderable surface. Popular surface finishes for HDI PCBs include:
- ENIG (Electroless Nickel Immersion Gold): Provides excellent solderability and shelf life
- ENEPIG (Electroless Nickel Electroless Palladium Immersion Gold): Offers improved wire bonding capabilities
- OSP (Organic Solderability Preservative): A cost-effective option for short-term storage
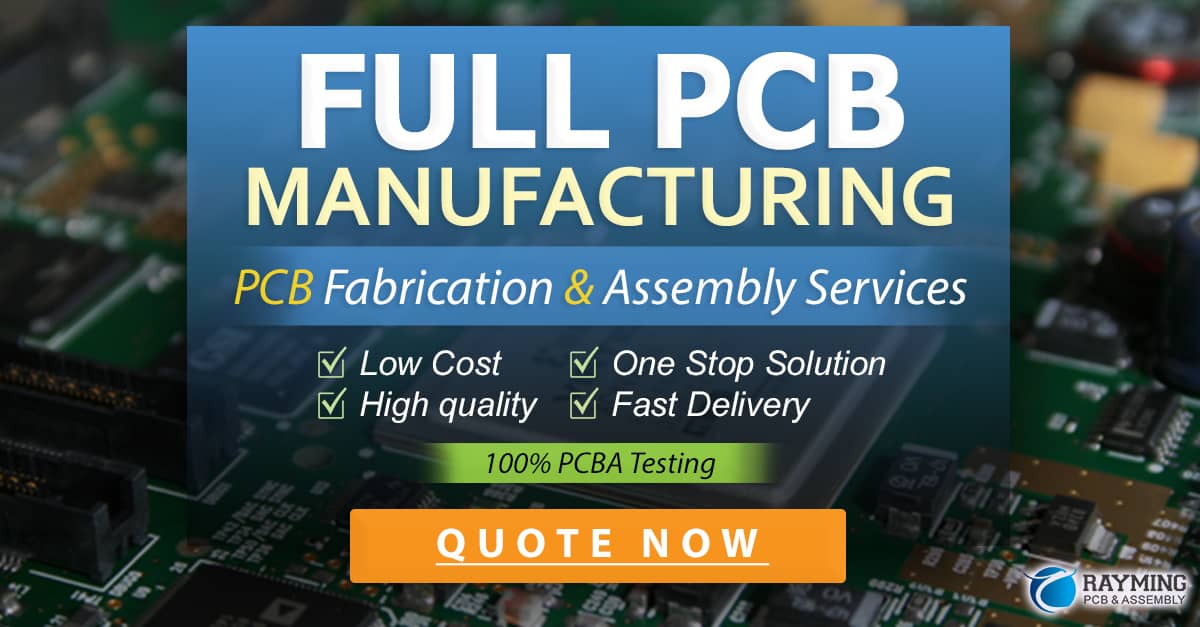
Choosing the Right HDI PCB Manufacturer
Selecting a reliable and experienced HDI PCB manufacturer is essential for the success of your project. When choosing a manufacturer, consider the following factors:
Technical Capabilities
Ensure that the manufacturer has the necessary equipment and expertise to produce HDI PCBs with your required specifications, such as:
- Minimum line width and spacing
- Microvia and buried via capabilities
- Layer count and stack-up options
- Surface finish options
Quality Control and Certifications
A reputable HDI PCB manufacturer should have a robust quality control system in place and hold relevant industry certifications, such as:
- ISO 9001: Quality management system
- ISO 14001: Environmental management system
- UL (Underwriters Laboratories) certification
- IPC (Association Connecting Electronics Industries) standards compliance
Communication and Support
Effective communication and support are critical when working with an HDI PCB manufacturer. Look for a manufacturer that offers:
- Responsive and knowledgeable sales and technical support teams
- Clear and timely communication throughout the project
- Flexibility to accommodate design changes or revisions
- Rapid prototyping and quick-turn production options
HDI PCB Testing and Inspection
To ensure the quality and reliability of HDI PCBs, thorough testing and inspection are essential. Common testing and inspection methods include:
- Flying probe test: Checks for open circuits, short circuits, and other manufacturing defects
- Automated optical inspection (AOI): Uses cameras and image processing to detect surface defects
- X-ray inspection: Identifies internal defects, such as voids or misaligned vias
- Thermal cycling: Evaluates the PCB’s ability to withstand temperature fluctuations
- Microsectioning: Examines the internal structure and quality of vias and plated through-holes
Applications of HDI PCBs
HDI PCBs find applications in various industries and products that require high-density, high-performance electronics, such as:
- Smartphones and tablets
- Wearable devices
- Medical devices and implantables
- Aerospace and defense systems
- Automotive electronics
- Internet of Things (IoT) devices
- High-performance computing and data centers
As technology continues to advance, the demand for HDI PCBs is expected to grow, driving innovations in design, materials, and manufacturing processes.
Future Trends in HDI PCB Technology
The electronics industry is constantly evolving, and HDI PCB technology is no exception. Some of the future trends in HDI PCBs include:
- Increasing density: As devices become smaller and more powerful, HDI PCBs will need to accommodate even higher component densities and finer feature sizes.
- Advanced materials: The development of new, high-performance materials will enable HDI PCBs to operate in more demanding environments and support higher frequencies.
- Embedded components: Integrating passive components, such as resistors and capacitors, within the PCB Layers can further reduce the size and improve the performance of HDI PCBs.
- 3D packaging: Stacking multiple HDI PCBs in a 3D package can provide even greater density and functionality in a compact form factor.
- Additive manufacturing: The use of 3D printing technologies for PCB fabrication may enable the creation of complex, non-planar HDI structures and reduce waste in the manufacturing process.
Frequently Asked Questions (FAQ)
-
What is the difference between HDI PCBs and traditional PCBs?
HDI PCBs have finer lines and spaces, smaller vias, and higher connection pad density compared to traditional PCBs. This allows for the miniaturization of electronic components and the development of highly complex circuits. -
What are the benefits of using HDI PCBs?
The benefits of using HDI PCBs include reduced size and weight, improved signal integrity, enhanced electrical performance, increased reliability, and cost-effectiveness for high-volume production. -
What should I consider when choosing an HDI PCB manufacturer?
When choosing an HDI PCB manufacturer, consider their technical capabilities, quality control and certifications, communication and support, and ability to accommodate your specific requirements. -
What testing and inspection methods are used for HDI PCBs?
Common testing and inspection methods for HDI PCBs include flying probe tests, automated optical inspection (AOI), X-ray inspection, thermal cycling, and microsectioning. -
What are some of the future trends in HDI PCB technology?
Future trends in HDI PCB technology include increasing density, advanced materials, embedded components, 3D packaging, and the use of additive manufacturing techniques.
Conclusion
HDI PCBs have become an essential component in the development of advanced electronic devices, enabling the creation of smaller, lighter, and more powerful products. By understanding the design considerations, manufacturing processes, and testing requirements for HDI PCBs, designers and engineers can leverage this technology to create innovative solutions across various industries.
When selecting an HDI PCB manufacturing partner, it is crucial to choose a company with the necessary technical expertise, quality control measures, and customer support to ensure the success of your project. By staying informed about the latest trends and advancements in HDI PCB technology, you can position yourself to take advantage of the exciting opportunities that lie ahead in the world of electronics.
0 Comments