Introduction to PCB Layers
Printed Circuit Boards (PCBs) are the backbone of modern electronics. They are used in almost every electronic device, from smartphones and computers to medical equipment and aerospace systems. PCBs are made up of multiple layers of conductive and insulating materials, each serving a specific purpose. In this article, we will explore the 7 working layers in a typical PCB and their functions.
What is a PCB?
A PCB is a flat board made of insulating material, such as fiberglass or plastic, with conductive tracks, pads, and other features etched onto its surface. These conductive elements are typically made of copper and are used to electrically connect various components, such as resistors, capacitors, and integrated circuits (ICs), to form a complete circuit.
Why are PCB Layers Important?
PCB layers are essential for several reasons:
- They allow for more complex circuit designs by providing additional routing space.
- They help to minimize electromagnetic interference (EMI) by separating sensitive signals from noise sources.
- They improve signal integrity by reducing crosstalk and providing controlled impedance.
- They enable better heat dissipation by distributing power and ground planes throughout the board.
The 7 Working Layers in a PCB
A typical PCB consists of the following 7 working layers:
- Top Layer
- Ground Plane
- Power Plane
- Signal Layer 1
- Signal Layer 2
- Bottom Layer
- Solder Mask
Let’s take a closer look at each layer and its function.
1. Top Layer
The top layer is the uppermost layer of the PCB and is where most of the components are mounted. This layer contains the majority of the signal traces, which are the conductive paths that carry electrical signals between components. The top layer also includes component pads, which are the areas where components are soldered to the board.
Top Layer Design Considerations
When designing the top layer, several factors must be taken into account:
- Component placement: Components should be placed in a logical and efficient manner to minimize the length of signal traces and reduce the risk of signal integrity issues.
- Trace width and spacing: The width and spacing of signal traces must be carefully controlled to ensure proper signal integrity and to prevent short circuits.
- Copper pour: Unused areas of the top layer are often filled with a copper pour, which is connected to ground to provide additional shielding and reduce EMI.
2. Ground Plane
The ground plane is a solid layer of copper that is connected to the ground of the circuit. Its primary function is to provide a low-impedance return path for electrical currents and to minimize EMI by shielding sensitive signals from external noise sources.
Ground Plane Design Considerations
When designing the ground plane, several factors must be taken into account:
- Placement: The ground plane should be placed as close to the signal layers as possible to minimize the loop area and reduce EMI.
- Cutouts: Cutouts may be required in the ground plane to accommodate through-hole components or to reduce the capacitance between the ground plane and adjacent signal layers.
- Stitching vias: Stitching vias are small vias that are used to connect the ground plane to the top and bottom layers of the PCB. They help to minimize EMI and improve signal integrity by providing a low-impedance return path for high-frequency signals.
3. Power Plane
The power plane is a solid layer of copper that is connected to the power supply of the circuit. Its primary function is to distribute power evenly throughout the board and to provide a low-impedance supply path for electrical currents.
Power Plane Design Considerations
When designing the power plane, several factors must be taken into account:
- Placement: The power plane should be placed as close to the signal layers as possible to minimize the loop area and reduce EMI.
- Cutouts: Cutouts may be required in the power plane to accommodate through-hole components or to reduce the capacitance between the power plane and adjacent signal layers.
- Decoupling capacitors: Decoupling capacitors are used to provide a local supply of charge to fast-switching circuits and to reduce noise on the power supply. They should be placed as close to the power pins of ICs as possible.
4. Signal Layer 1
Signal layer 1 is a layer of the PCB that contains additional signal traces. It is used to route signals that cannot be accommodated on the top or bottom layers due to space constraints or signal integrity requirements.
Signal Layer 1 Design Considerations
When designing signal layer 1, several factors must be taken into account:
- Signal routing: Signals should be routed in a manner that minimizes crosstalk and signal integrity issues. This may involve the use of differential pairs, controlled impedance traces, or guard traces.
- Trace width and spacing: The width and spacing of signal traces must be carefully controlled to ensure proper signal integrity and to prevent short circuits.
- Vias: Vias are used to connect signal traces on different layers of the PCB. They should be placed in a manner that minimizes signal integrity issues and reduces EMI.
5. Signal Layer 2
Signal layer 2 is another layer of the PCB that contains additional signal traces. It is used to route signals that cannot be accommodated on the other layers due to space constraints or signal integrity requirements.
Signal Layer 2 Design Considerations
The design considerations for signal layer 2 are similar to those for signal layer 1. However, signal layer 2 is often used for high-speed signals or critical signals that require extra shielding or isolation.
6. Bottom Layer
The bottom layer is the lowermost layer of the PCB and is where additional components and connectors are mounted. It also contains signal traces and component pads, similar to the top layer.
Bottom Layer Design Considerations
When designing the bottom layer, several factors must be taken into account:
- Component placement: Components should be placed in a logical and efficient manner to minimize the length of signal traces and reduce the risk of signal integrity issues.
- Trace width and spacing: The width and spacing of signal traces must be carefully controlled to ensure proper signal integrity and to prevent short circuits.
- Mounting holes: Mounting holes are used to secure the PCB to an enclosure or chassis. They should be placed in a manner that provides adequate support for the board and does not interfere with components or signal traces.
7. Solder Mask
The solder mask is a thin layer of polymer that is applied to the top and bottom layers of the PCB. Its primary function is to protect the copper traces and pads from oxidation and to prevent solder bridges from forming between adjacent pads during the soldering process.
Solder Mask Design Considerations
When designing the solder mask, several factors must be taken into account:
- Coverage: The solder mask should cover all areas of the PCB that are not intended to be soldered, including the gaps between pads and traces.
- Apertures: Apertures are openings in the solder mask that expose the pads and other areas where components will be soldered. They should be sized and shaped appropriately to ensure proper soldering and prevent solder bridges.
- Color: The solder mask color is usually green, but other colors such as black, blue, and red are also available. The choice of color is mainly for aesthetic purposes, but it can also be used for functional reasons, such as to indicate the type of PCB or to improve contrast for optical inspection.
PCB Layer Stackup
The arrangement of the 7 working layers in a PCB is known as the layer stackup. The layer stackup is an important consideration in PCB design, as it affects signal integrity, EMI, and manufacturing costs.
A typical 4-layer PCB stackup is shown below:
Layer | Material | Thickness (mm) |
---|---|---|
Top Layer | Copper | 0.035 |
Dielectric 1 | FR-4 | 0.2 |
Ground Plane | Copper | 0.035 |
Dielectric 2 | FR-4 | 0.7 |
Power Plane | Copper | 0.035 |
Dielectric 3 | FR-4 | 0.2 |
Bottom Layer | Copper | 0.035 |
In this stackup, the top and bottom layers are used for signal routing, while the inner layers are used for power and ground planes. The dielectric layers are made of FR-4, a type of fiberglass-reinforced epoxy laminate that is commonly used in PCB fabrication.
The thickness of each layer is carefully controlled to ensure proper signal integrity and to meet the requirements of the intended application. For example, high-speed digital circuits may require thinner dielectric layers to minimize signal reflections and improve signal quality.
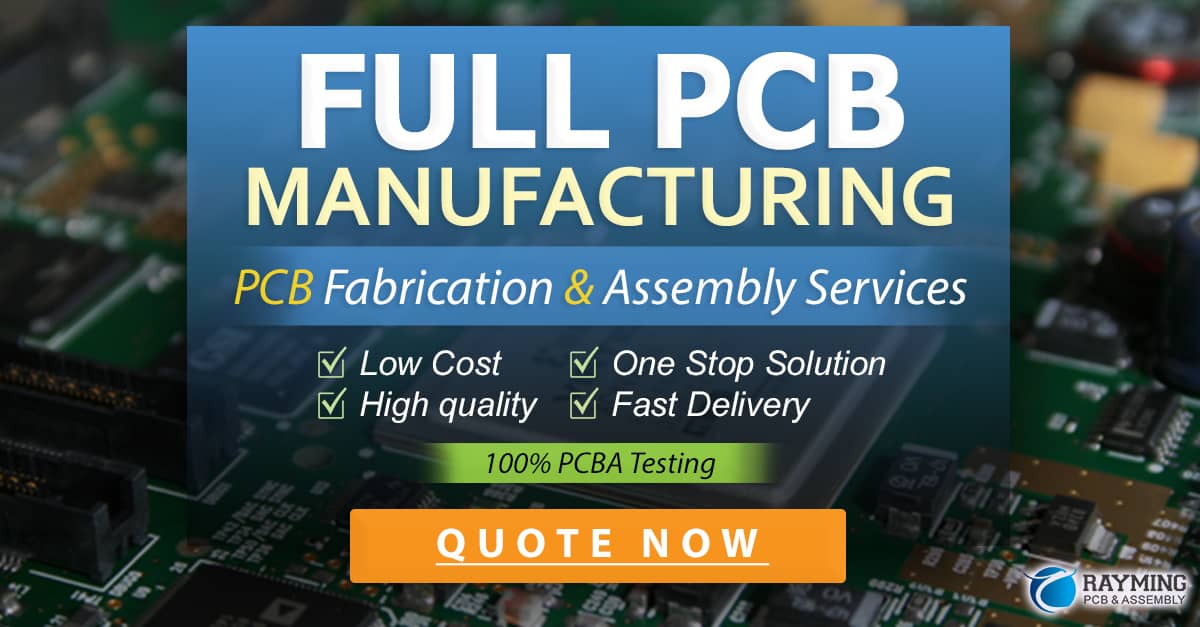
PCB Layer Design Guidelines
When designing a PCB, there are several guidelines that should be followed to ensure proper functionality and reliability:
- Use a ground plane: A solid ground plane should be used to provide a low-impedance return path for electrical currents and to minimize EMI.
- Use a power plane: A solid power plane should be used to distribute power evenly throughout the board and to provide a low-impedance supply path for electrical currents.
- Minimize signal layer changes: Signal traces should be routed on as few layers as possible to minimize vias and reduce signal integrity issues.
- Use controlled impedance: Controlled impedance traces should be used for high-speed signals to minimize reflections and improve signal quality.
- Avoid splitting planes: Power and ground planes should not be split or cut out unless absolutely necessary, as this can create signal integrity issues and increase EMI.
- Use stitching vias: Stitching vias should be used to connect the ground plane to the top and bottom layers of the PCB to minimize EMI and improve signal integrity.
- Follow manufacturer’s guidelines: The manufacturer’s guidelines for PCB design and fabrication should be followed to ensure proper functionality and reliability.
Frequently Asked Questions (FAQ)
- What is the purpose of the solder mask layer in a PCB?
-
The solder mask layer serves to protect the copper traces and pads from oxidation and prevents solder bridges from forming between adjacent pads during the soldering process.
-
Why is it important to have a ground plane in a PCB?
-
A ground plane provides a low-impedance return path for electrical currents and helps to minimize electromagnetic interference (EMI) by shielding sensitive signals from external noise sources.
-
What is the difference between a power plane and a ground plane?
-
A power plane is connected to the power supply of the circuit and distributes power evenly throughout the board, while a ground plane is connected to the ground of the circuit and provides a low-impedance return path for electrical currents.
-
How does the PCB layer stackup affect signal integrity?
-
The PCB layer stackup affects signal integrity by determining the spacing between signal layers and the reference planes (power and ground). Proper spacing and arrangement of layers can minimize crosstalk, reduce EMI, and improve signal quality.
-
What are some common design guidelines for PCB layers?
- Some common design guidelines for PCB layers include using a solid ground plane, using a solid power plane, minimizing signal layer changes, using controlled impedance for high-speed signals, avoiding splitting planes, using stitching vias, and following the manufacturer’s guidelines for PCB design and fabrication.
Conclusion
PCB layers are a critical aspect of PCB design and fabrication. The 7 working layers in a typical PCB – top layer, ground plane, power plane, signal layers, bottom layer, and solder mask – each serve a specific purpose and must be designed carefully to ensure proper functionality and reliability.
By understanding the role of each layer and following proper design guidelines, PCB designers can create boards that meet the requirements of their intended application while minimizing signal integrity issues, EMI, and manufacturing costs.
As PCB technology continues to advance, the importance of proper layer design will only increase. By staying up-to-date with the latest design techniques and manufacturing processes, PCB designers can ensure that their boards are able to meet the ever-increasing demands of modern electronics.
0 Comments