Importance of PCB Inspection
PCB inspection is critical to ensuring the reliability and performance of the end product. Some of the key reasons for performing incoming inspection on PCBs include:
- Identifying any defects or non-conformities early in the process
- Verifying that the PCBs match the design requirements
- Preventing defective boards from being used in assembly
- Providing feedback to the PCB manufacturer on quality issues
- Documenting inspections for traceability and compliance purposes
Skipping or shortcutting the incoming inspection process can lead to major problems down the line, such as product failures, recalls, returns, and damage to the company’s reputation. Investing the time upfront to thoroughly inspect PCBs pays off in higher quality and reliability.
Incoming Inspection Process Flow
The exact flow of the PCB incoming inspection process can vary between companies, but generally follows these high-level steps:
- Receiving of PCB panels/boards from fabrication facility
- Visual inspection
- Automated optical inspection (AOI)
- Electrical testing
- Other specialized tests (e.g. solderability, cleanliness)
- Final review and approval or rejection
- Documentation and reporting
Let’s take a closer look at each of these steps in the process.
1. Receiving
When a shipment of PCBs arrives from the manufacturer, the first step is logging them into the quality system. Key information to record includes:
- Purchase order and work order numbers
- Quantity received
- Date code and lot/batch numbers
- Manufacturer part number and revision
- Any visual damage to packaging
An initial count should be done to verify the received quantity matches the shipper and purchase order. The boards should be handled carefully, especially if not shipped in individual packaging.
2. Visual Inspection
The next step is visually inspecting the PCBs for any obvious issues. This is typically done on a sample basis, examining a subset of the boards in detail. Inspectors use magnification, lighting, and other visual aids to look for defects such as:
- Laminate material flaws (cracks, discoloration, measling)
- Drilled hole size, breakout, and plating issues
- Circuit pattern flaws (width, spacing, etching, cuts)
- Solder mask and silkscreen problems
- Bow and twist outside of specifications
- Foreign debris or contamination
The sample size for visual inspection depends on the lot size, historical quality data, and criticality of the PCBs. Typical sampling plans are:
Lot Size | Sample Size |
---|---|
2 to 50 | 2 |
51 to 90 | 3 |
91 to 150 | 5 |
151 to 280 | 8 |
281 to 500 | 13 |
501 to 1200 | 20 |
1201 to 3200 | 32 |
3201 to 10,000 | 50 |
If the sample yields any defects, additional samples may need to be inspected. If the number of defects exceeds the acceptable quality limit (AQL), the entire lot may be rejected.
3. Automated Optical Inspection (AOI)
For higher volume PCBs, automated optical inspection (AOI) equipment is often used to scan the boards for defects. AOI systems use high-resolution cameras and advanced image processing algorithms to detect issues at much higher speeds than human inspectors.
AOI systems compare the PCBs to the CAD data and look for a variety of defects such as:
- Tombstoning, billboarding, lifting of components
- Bridging or insufficient solder
- Missing, misaligned or incorrect parts
- Solder balls, webbing or splatter
- Component body and lead defects
The AOI program must be set up with the proper lighting, camera angles, component libraries, and inspection criteria. After scanning, the AOI system generates a report of the identified defects for further review. False failures are common with AOI, so suspected defects often need to be verified by a human.
4. Electrical Testing
Electrical testing verifies the PCB’s conductivity, continuity, isolation and other electrical properties. Common electrical tests include:
- Flying probe test – Uses moving test probes to check for shorts, opens and resistance
- Boundary scan test – Uses JTAG interface to test connectivity and functionality of digital components
- In-circuit test (ICT) – Uses a bed-of-nails fixture to access and test each net on the board
- Functional test – Applies power and stimulus to the board to test overall functionality
The specific electrical tests required depend on the type and complexity of the PCB. Generally, the more complex the board, the more extensive the testing needs to be. Simpler boards may only require basic continuity and isolation testing.
5. Specialized Tests
Depending on the end-use requirements, PCBs may need to undergo additional tests beyond the standard visual, optical and electrical inspections. Some examples include:
- Solderability testing – Measures the ease of soldering the PCB pads and holes
- Cleanliness testing – Checks for ionic contamination that could lead to corrosion
- Thermal stress testing – Subjects boards to repeated heating and cooling cycles
- Microsectioning – Cross-sections boards to examine internal structure and plating
- Peel strength testing – Measures the adhesion of the copper foil to the laminate
- Impedance testing – Verifies the controlled impedance of high-frequency boards
These specialized tests often require destructive testing of sample boards, as the tests render the boards unusable. The need for these tests is determined by the PCB design requirements and the demands of the end application.
6. Final Review and Disposition
After all the inspections and tests are complete, the results are reviewed to make a final determination on the acceptability of the PCBs. If the boards pass all the criteria, they are approved and released for assembly.
If any defects are found, they are evaluated for severity and potential impact. Minor issues that do not affect functionality may be accepted with a deviation. More significant defects may require rework by the PCB manufacturer if feasible. If the defects are severe enough, the entire lot may be rejected and returned to the manufacturer.
7. Documentation
Throughout the incoming inspection process, it’s important to document the results for traceability and continuous improvement purposes. Key information to record includes:
- Inspection and test data
- Defects found and their severity
- Disposition (accepted, reworked, rejected)
- Inspector and date of inspection
- Corrective actions taken
This documentation helps identify trends in PCB Quality over time and provides a record of inspections in case of any future issues or audits. Many companies use quality management software to store and analyze this inspection data.
Sampling Plans
As mentioned earlier, most incoming PCB inspection is done on a sample basis rather than checking 100% of the boards. The sample sizes are chosen to provide a statistically valid representation of the entire lot.
The most common sampling standards used are:
- ANSI/ASQ Z1.4 – General inspection level II
- MIL-STD-105E – General inspection level II
- Squeglia C=0 plan
These standards provide tables that give the sample size based on the lot size and desired inspection level. They also define the acceptance quality limit (AQL) which is the maximum percent defective that is allowed.
Some common PCB AQL levels are:
- 0.1% for critical defects that would cause product failure
- 0.4% for major defects that could cause problems but not complete failure
- 1.0% for minor defects that don’t affect function but are cosmetic issues
The tighter the AQL, the larger the sample sizes need to be to have confidence in catching any defects. The choice of AQL depends on the critical of the PCB and the risk posed by defects.
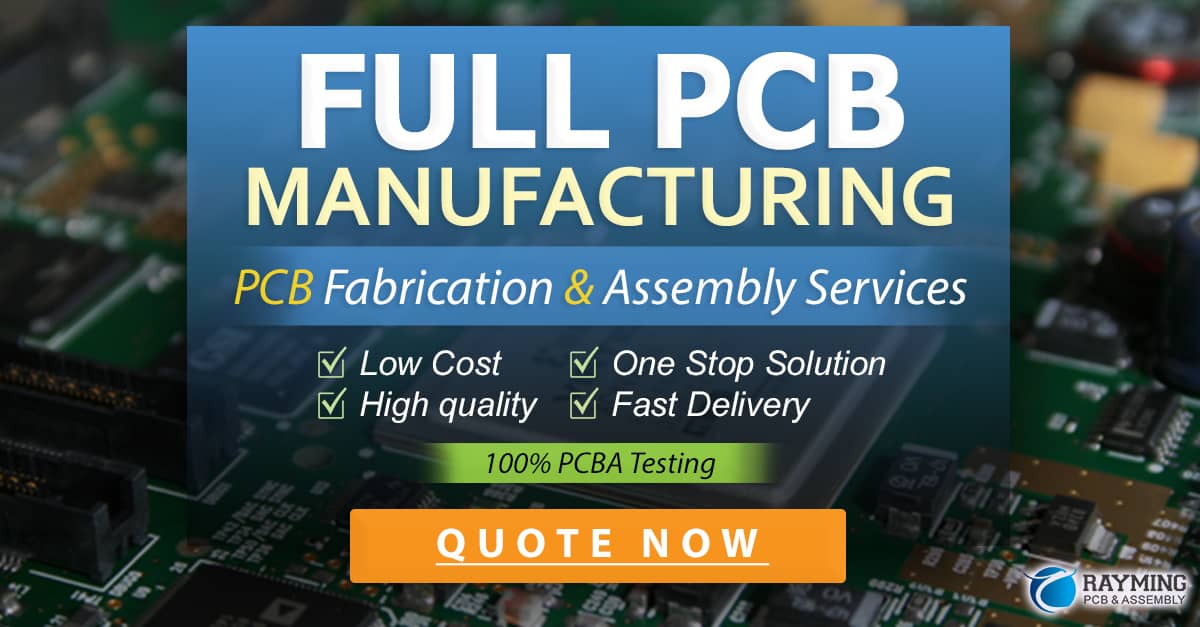
Inspection Equipment
To perform incoming PCB inspection, a variety of equipment is needed. Some key tools include:
- Magnification lenses and microscopes
- Cameras and video inspection systems
- Lighting (bright field, dark field, polarized)
- Automatic optical inspection (AOI) machines
- Flying probe and in-circuit test (ICT) equipment
- X-ray and scanning acoustic microscopy for non-visible defects
- Ionic contamination testers
- Solderability testers
- Cross-sectioning and Micro-Sectioning equipment
The specific equipment required depends on the types of PCBs being inspected and the defects being screened for. More advanced equipment is needed for denser and more complex boards with fine pitch components.
Challenges and Best Practices
Incoming PCB inspection can be a challenging process due to the increasing complexity of boards and the pressure to get products to market quickly. Some of the key challenges include:
- Keeping up with ever-shrinking component and feature sizes
- Inspecting for new types of defects
- Balancing the need for both speed and quality
- Managing false failures from automated inspection
- Staying current on the latest inspection standards and techniques
To overcome these challenges, it’s important for companies to invest in the right equipment, training, and processes for their needs. Some best practices include:
- Clearly defining the inspection criteria and AQLs
- Maintaining golden sample boards for comparison
- Regularly calibrating and maintaining inspection equipment
- Analyzing inspection data for trends and improvement opportunities
- Collaborating closely with PCB manufacturers on quality expectations
- Staying up to date on industry inspection standards and best practices
By following these practices and continuously improving the inspection process, companies can ensure a high level of PCB quality and reliability.
FAQ
What is the difference between AOI and visual inspection?
Visual inspection is done by human eye, using magnification and lighting aids to examine PCBs for defects. AOI (automated optical inspection) uses cameras and software to automatically scan PCBs for defects at high speed. AOI can inspect more boards in less time, but may have more false failures that need human review.
What is the acceptable quality level (AQL) for PCBs?
The AQL is the maximum percent of defective boards that is considered acceptable in a lot. It varies based on the type and severity of the defects. Typical PCB AQLs are 0.1% for critical defects, 0.4% for major defects, and 1.0% for minor defects. The tighter the AQL, the more inspection is required.
How do you choose a sample size for PCB inspection?
Sample sizes are determined by industry standard sampling plans such as ANSI/ASQ Z1.4 or MIL-STD-105E. These plans give the required sample size based on the lot size and the desired inspection level (how many defects you are willing to accept). Larger lots and tighter AQLs require larger sample sizes.
What are some common PCB Defects found in inspection?
Some of the most common PCB defects include opens and shorts in circuits, incorrect hole sizes, laminate material flaws, solder mask and silkscreen errors, component misalignment or damage, insufficient solder joints, and contamination. The specific defects vary based on the type of PCB and its manufacturing process.
How much does PCB inspection equipment cost?
The cost of PCB inspection equipment varies widely based on the type and capabilities. Simple magnification lenses and lighting may only cost a few hundred dollars. Automated optical inspection (AOI) machines and Flying probe testers can range from tens of thousands to hundreds of thousands of dollars. High-end X-ray and acoustic microscopy systems can cost over a million dollars. The cost must be justified based on the value of the PCBs being inspected and the risk of defects.
0 Comments