Introduction to Surface Mount Devices
Surface Mount Devices (SMDs) have revolutionized the electronics industry by enabling the production of smaller, lighter, and more efficient electronic components and circuits. SMDs are electronic components that are designed to be mounted directly onto the surface of a printed circuit board (PCB) rather than through holes, as with traditional through-hole components. This innovative mounting technique has allowed for significant advancements in electronic device design and manufacturing.
In this comprehensive article, we will explore the world of Surface Mount Devices, discussing their history, advantages, types, and applications. We will also delve into the manufacturing process, design considerations, and the future of SMD technology.
History of Surface Mount Devices
The concept of surface mounting electronic components dates back to the 1960s when the first surface mount transistors were introduced. However, it wasn’t until the 1980s that SMD technology began to gain widespread adoption in the electronics industry.
Early Development
In the early days of electronics, components were primarily mounted on PCBs using through-hole technology. This involved inserting component leads through holes drilled in the PCB and soldering them on the opposite side. While effective, this method had limitations in terms of component density, manufacturing efficiency, and device size.
The Rise of SMD Technology
The introduction of Surface Mount Devices in the 1980s marked a significant turning point in the electronics industry. As electronic devices became increasingly smaller and more complex, the need for a more efficient and space-saving mounting technique became apparent. SMDs offered several advantages over through-hole components, including:
- Reduced component size
- Increased component density on PCBs
- Improved manufacturing efficiency
- Enhanced device performance
As a result, SMD technology quickly gained popularity, and by the 1990s, it had become the dominant mounting method in the electronics industry.
Advantages of Surface Mount Devices
Surface Mount Devices offer numerous benefits over traditional through-hole components. These advantages have contributed to their widespread adoption and have enabled the development of increasingly sophisticated electronic devices.
Space Savings
One of the most significant advantages of SMDs is their small size. SMDs are typically much smaller than their through-hole counterparts, allowing for greater component density on PCBs. This space-saving characteristic is crucial in the design of compact electronic devices, such as smartphones, wearables, and IoT devices.
Improved Performance
SMDs offer improved electrical performance compared to through-hole components. The shorter lead lengths and reduced parasitic capacitance and inductance of SMDs contribute to better signal integrity and higher-frequency operation. This makes SMDs particularly well-suited for high-speed digital circuits and RF applications.
Manufacturing Efficiency
The use of SMDs streamlines the manufacturing process, resulting in increased efficiency and reduced costs. SMDs are well-suited for automated assembly processes, such as pick-and-place machines and Reflow Soldering. This automation allows for faster production times, fewer assembly errors, and higher throughput compared to manual through-hole assembly.
Design Flexibility
SMDs provide greater design flexibility, enabling the creation of more complex and innovative electronic devices. The small size and various package options of SMDs allow for more efficient PCB layouts and the integration of advanced features in limited space.
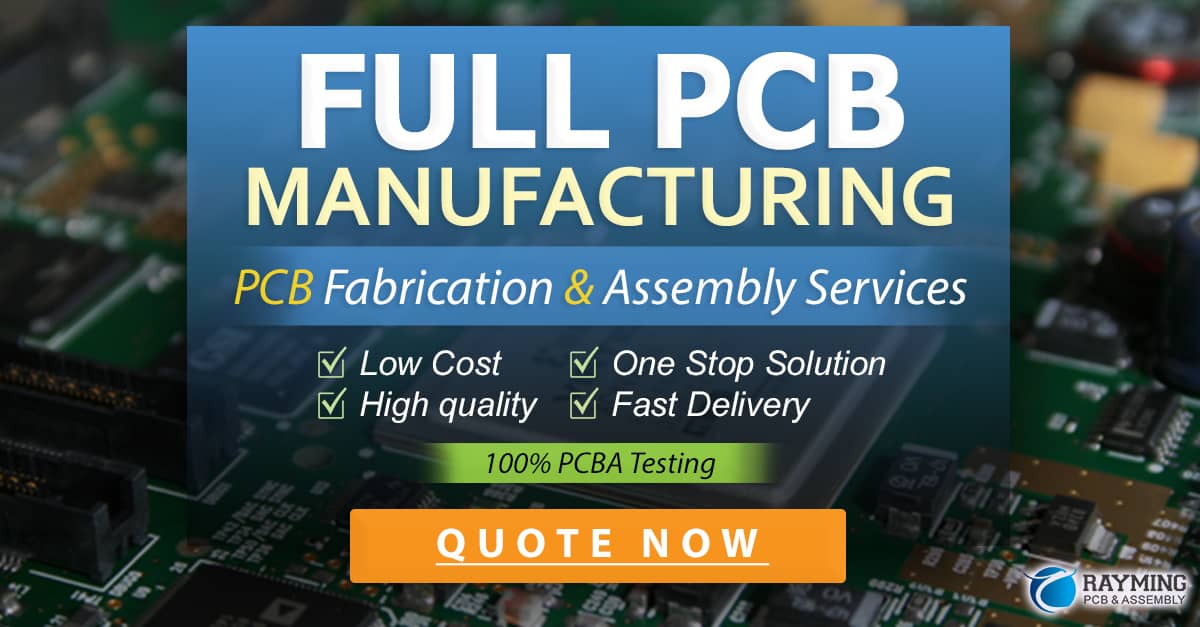
Types of Surface Mount Devices
Surface Mount Devices come in a wide variety of packages and sizes to suit different applications and design requirements. Some of the most common types of SMDs include:
Chip Components
Chip components, such as resistors, capacitors, and inductors, are among the most basic and widely used SMDs. These components are typically rectangular in shape and have metallized terminals on either end for soldering to the PCB.
Component | Package Size (mm) | Description |
---|---|---|
Resistor | 0201 (0.6 x 0.3) | High-precision, low-power |
Capacitor | 0402 (1.0 x 0.5) | High-capacity, low-ESR |
Inductor | 0603 (1.6 x 0.8) | High-Q, low-DCR |
Transistors and Diodes
SMD transistors and diodes are available in various package styles, such as SOT (Small Outline Transistor), TSOP (Thin Small Outline Package), and DFN (Dual Flat No-lead). These packages are designed to provide efficient heat dissipation and minimize parasitic effects.
Integrated Circuits
Integrated circuits (ICs) are complex semiconductor devices that incorporate multiple electronic components on a single chip. SMD ICs come in a variety of package styles, including:
- SOIC (Small Outline Integrated Circuit)
- QFP (Quad Flat Package)
- BGA (Ball Grid Array)
- CSP (Chip Scale Package)
Each package style has its own characteristics and is chosen based on factors such as pin count, power dissipation, and signal integrity requirements.
Surface Mount Device Manufacturing Process
The manufacturing process for Surface Mount Devices involves several key steps to ensure the production of high-quality components.
Wafer Fabrication
The first step in the SMD manufacturing process is wafer fabrication. This involves creating a semiconductor wafer, typically made of silicon, which serves as the substrate for the electronic components. The wafer undergoes a series of photolithography, etching, and deposition processes to create the desired electronic structures.
Die Singulation
Once the wafer has been fabricated, it is cut into individual semiconductor dies using a process called singulation. This is typically done using a high-precision saw or laser cutting tool.
Packaging
The singulated dies are then packaged into their final SMD form factor. This involves attaching the die to a lead frame or substrate, Wire Bonding or flip-chip bonding the die to the package terminals, and encapsulating the assembly in a protective molding compound.
Testing and Inspection
Before being shipped to customers, SMDs undergo rigorous testing and inspection to ensure they meet the required specifications and quality standards. This may include electrical testing, visual inspection, and environmental stress testing.
Designing with Surface Mount Devices
Designing electronic circuits using Surface Mount Devices requires careful consideration of various factors to ensure optimal performance, reliability, and manufacturability.
PCB Layout Considerations
When designing PCBs for SMDs, it is essential to follow best practices for component placement, trace routing, and soldermask design. Key considerations include:
- Providing adequate clearance between components for automated assembly
- Minimizing trace lengths and impedance mismatches to improve signal integrity
- Ensuring proper soldermask coverage to prevent shorts and improve solderability
Thermal Management
SMDs can generate significant amounts of heat during operation, which must be effectively dissipated to prevent performance degradation and reliability issues. Thermal management strategies for SMDs include:
- Selecting packages with good thermal conductivity
- Providing adequate copper pours and thermal vias for heat dissipation
- Using thermal interface materials and heatsinks where necessary
Assembly and Soldering
Proper assembly and soldering techniques are critical for ensuring the reliability and longevity of SMD-based circuits. Key considerations include:
- Using appropriate Solder Paste and stencil design for automated assembly
- Controlling reflow soldering temperature profiles to prevent component damage
- Implementing proper cleaning and inspection processes to ensure high-quality solder joints
Future of Surface Mount Device Technology
As electronic devices continue to evolve and become more sophisticated, Surface Mount Device technology is poised for further advancements and innovations.
Miniaturization trends
The trend towards miniaturization in electronic devices is expected to drive the development of even smaller and more compact SMDs. This may include the adoption of newer packaging technologies, such as Wafer-Level Packaging (WLP) and 3D packaging, which enable higher component density and improved performance.
Advanced Materials
The use of advanced materials, such as gallium nitride (GaN) and silicon carbide (SiC), is expected to gain traction in SMD technology. These materials offer superior electrical and thermal properties compared to traditional silicon, enabling the development of high-performance and energy-efficient power electronics and RF devices.
Flexible and Wearable Electronics
The growing demand for flexible and wearable electronic devices is likely to drive the development of SMDs that can be integrated into flexible and stretchable substrates. This may involve the use of novel packaging techniques, such as chip-on-flex and chip-on-glass, as well as the development of SMDs with improved mechanical flexibility.
Frequently Asked Questions (FAQ)
- What is the difference between Surface Mount Devices and through-hole components?
-
Surface Mount Devices are designed to be mounted directly onto the surface of a PCB, while through-hole components have leads that are inserted through holes in the PCB and soldered on the opposite side.
-
What are the advantages of using Surface Mount Devices?
-
SMDs offer several advantages, including smaller size, improved performance, increased manufacturing efficiency, and greater design flexibility compared to through-hole components.
-
What are some common types of Surface Mount Devices?
-
Common types of SMDs include chip components (resistors, capacitors, inductors), transistors and diodes, and various integrated circuit packages such as SOIC, QFP, BGA, and CSP.
-
What is the manufacturing process for Surface Mount Devices?
-
The manufacturing process for SMDs involves wafer fabrication, die singulation, packaging, and testing and inspection to ensure high-quality components.
-
What are some key considerations when designing with Surface Mount Devices?
- When designing with SMDs, key considerations include PCB layout best practices, thermal management strategies, and proper assembly and soldering techniques to ensure optimal performance, reliability, and manufacturability.
Conclusion
Surface Mount Devices have transformed the electronics industry, enabling the development of smaller, faster, and more efficient electronic devices. By offering numerous advantages over traditional through-hole components, SMDs have become the dominant mounting technology in modern electronics manufacturing.
As electronic devices continue to evolve and push the boundaries of performance and functionality, SMD technology is expected to advance in tandem. From ongoing miniaturization efforts to the adoption of advanced materials and packaging techniques, the future of Surface Mount Devices is bright and full of exciting possibilities.
By understanding the fundamentals of SMDs, their manufacturing process, and design considerations, engineers and manufacturers can harness the full potential of this innovative technology to create the next generation of cutting-edge electronic devices.
0 Comments