Introduction to Solder Paste
Solder paste is a crucial component in the PCB SMT (Surface Mount Technology) assembly process. It is a mixture of tiny solder particles suspended in a flux medium, which is applied to the PCB pads before placing the surface mount components. The solder paste plays a significant role in creating reliable electrical and mechanical connections between the components and the PCB.
Composition of Solder Paste
Solder paste typically consists of the following components:
- Solder alloy particles (e.g., tin-lead, lead-free)
- Flux medium (e.g., rosin-based, water-soluble, no-clean)
- Additives (e.g., rheological modifiers, tackifiers)
The solder alloy particles make up 50-95% of the paste by weight, while the flux medium and additives account for the remaining 5-50%.
Types of Solder Paste
There are various types of solder paste available, depending on the specific requirements of the PCB assembly process. Some common types include:
- Lead-based solder paste (e.g., Sn63Pb37)
- Lead-free solder paste (e.g., SAC305, SN100C)
- Water-soluble solder paste
- No-clean solder paste
The choice of solder paste depends on factors such as the PCB design, component types, environmental regulations, and manufacturing process.
Roles of Solder Paste in PCB SMT Assembly
1. Creating Electrical Connections
The primary role of solder paste in PCB SMT assembly is to create reliable electrical connections between the surface mount components and the PCB pads. During the reflow soldering process, the solder particles in the paste melt and form a strong metallic bond with the component leads and PCB pads. This ensures proper electrical conductivity and signal integrity in the assembled PCB.
2. Providing Mechanical Strength
In addition to electrical connections, solder paste also provides mechanical strength to the assembled components. The solidified solder joint holds the components securely in place, preventing them from moving or detaching during normal use or under mechanical stress. A well-formed solder joint can withstand vibrations, shocks, and thermal cycles, ensuring the long-term reliability of the PCB.
3. Facilitating Component Placement
Solder paste plays a crucial role in facilitating the placement of surface mount components on the PCB. The tacky nature of the flux medium in the solder paste helps to temporarily hold the components in place during the assembly process. This is especially important for small and lightweight components that can easily shift or fall off the PCB before the reflow soldering process.
4. Protecting Against Oxidation
The flux medium in the solder paste serves as a protective layer against oxidation during the reflow soldering process. It removes any oxide films on the component leads and PCB pads, ensuring a clean and wettable surface for the molten solder to bond with. Without the flux, the solder may not wet properly, leading to poor or non-existent solder joints.
5. Enhancing Solder Joint Quality
The quality of the solder paste directly affects the quality of the resulting solder joints. Factors such as particle size distribution, flux activity, and rheological properties play a crucial role in determining the final solder joint characteristics. A well-formulated solder paste ensures good wetting, minimal voiding, and uniform solder joint formation across the PCB.
Solder Paste Application Process
Solder Paste Printing
The most common method of applying solder paste to a PCB is through stencil printing. A stencil is a thin metal sheet with laser-cut apertures that correspond to the PCB pad locations. The solder paste is deposited onto the PCB through these apertures using a squeegee or automated printer. The stencil thickness, aperture size, and printing parameters (e.g., squeegee pressure, speed, angle) determine the volume and consistency of the solder paste deposit.
Solder Paste Inspection (SPI)
After printing, the solder paste deposits are typically inspected using a solder paste inspection (SPI) system. SPI systems use 2D or 3D imaging technology to measure the volume, height, area, and alignment of the solder paste deposits. This inspection process helps to identify any printing defects, such as insufficient paste, bridging, or misalignment, which can be corrected before component placement.
Solder Paste Storage and Handling
Solder paste is a perishable material that requires proper storage and handling to maintain its quality and performance. Some key considerations include:
-
Shelf life: Solder paste has a limited shelf life, typically ranging from 3 to 12 months, depending on the formulation and storage conditions. Expired solder paste may have reduced flux activity, poor printability, and compromised solder joint quality.
-
Storage temperature: Solder paste should be stored at a controlled temperature, usually between 0-10°C (32-50°F), to prevent premature flux activation and solder particle oxidation. Prolonged exposure to high temperatures can degrade the solder paste performance.
-
Handling: Solder paste should be handled with care to avoid contamination and air entrapment. The paste should be thoroughly mixed before use to ensure a homogeneous distribution of solder particles and flux. Proper handling techniques, such as using clean spatulas and avoiding excessive stirring, can help maintain the solder paste quality.
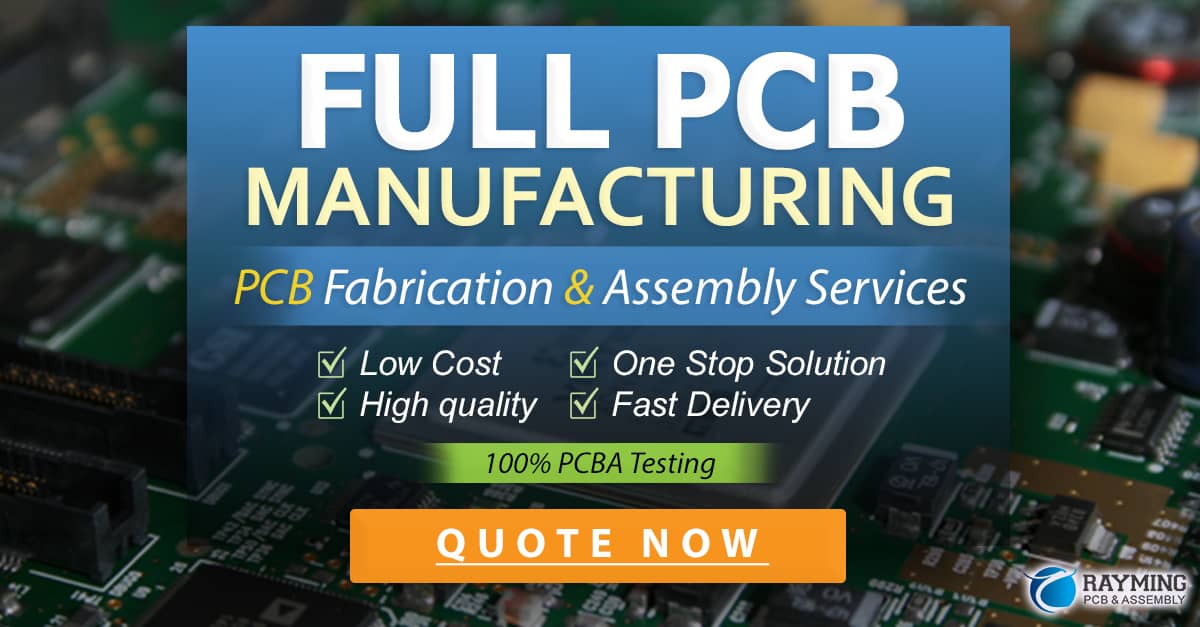
Solder Paste Characteristics
Particle Size Distribution
The size distribution of the solder particles in the paste is a critical factor in determining the printing and reflow performance. Solder paste is classified into different types based on the particle size, such as Type 3 (25-45 µm), Type 4 (20-38 µm), and Type 5 (15-25 µm). Smaller particle sizes allow for finer pitch printing and better solder joint formation, but may also be more prone to oxidation and have shorter shelf life.
Flux Activity
The flux activity of the solder paste refers to its ability to remove oxides and other contaminants from the component leads and PCB pads during the reflow soldering process. The flux activity level is classified as Low (L), Medium (M), or High (H), depending on the flux chemistry and activation temperature. Higher flux activity provides better wetting and solder joint formation but may also require more stringent cleaning processes.
Rheological Properties
The rheological properties of solder paste, such as viscosity, thixotropy, and slump resistance, determine its printing and dispensing characteristics. A well-balanced solder paste should have a consistent viscosity, good shear thinning behavior (thixotropy), and minimal slumping after printing. These properties ensure accurate and repeatable solder paste deposition, as well as good component placement and reflow soldering results.
Property | Description | Importance |
---|---|---|
Viscosity | Resistance to flow under stress | Affects printing quality and deposit consistency |
Thixotropy | Shear thinning behavior, viscosity decrease under shear stress | Enables smooth printing and prevents paste slumping |
Slump Resistance | Ability to maintain shape after printing | Prevents bridging and short circuits between pads |
Solder Paste Quality Control
Solder Paste Testing
Regular testing of solder paste is essential to ensure consistent quality and performance. Some common tests include:
-
Viscosity: Measures the flow resistance of the solder paste using a viscometer or rheometer. The viscosity should be within the specified range and stable over time.
-
Slump: Evaluates the ability of the printed solder paste to maintain its shape without slumping or spreading. Slump tests are typically performed on test patterns with varying pad sizes and spacings.
-
Tack: Measures the adhesive strength of the solder paste to hold components in place before reflow soldering. Tack tests are conducted using a tack tester or by placing components on printed solder paste deposits.
-
Wetting: Assesses the ability of the molten solder to wet and spread on the component leads and PCB pads during reflow soldering. Wetting tests are performed using wetting balance or by evaluating the solder joint formation on test coupons.
Solder Paste Defects and Troubleshooting
Despite careful solder paste selection and process control, defects can still occur during PCB assembly. Some common solder paste-related defects include:
-
Insufficient solder: Occurs when the solder paste deposit is too small or has poor wetting, resulting in weak or open solder joints.
-
Solder bridging: Happens when the solder paste spreads and connects adjacent pads, causing short circuits.
-
Solder balls: Small spheres of solder that form on the PCB surface due to excessive solder paste, poor wetting, or contamination.
-
Voiding: Gaps or voids within the solder joint caused by trapped flux, moisture, or other volatile substances.
Troubleshooting solder paste defects involves a systematic approach that considers various factors, such as stencil design, printing parameters, reflow profile, and component placement accuracy. Regular process monitoring, SPI, and post-reflow inspection can help identify and correct solder paste-related issues in a timely manner.
FAQ
1. What is the shelf life of solder paste, and how should it be stored?
The shelf life of solder paste typically ranges from 3 to 12 months, depending on the formulation and storage conditions. Solder paste should be stored at a controlled temperature between 0-10°C (32-50°F) to prevent premature flux activation and solder particle oxidation. Expired or improperly stored solder paste may have reduced performance and solder joint quality.
2. How does the particle size of solder paste affect the printing and reflow process?
The particle size of solder paste determines its printing resolution and reflow performance. Smaller particle sizes, such as Type 4 (20-38 µm) and Type 5 (15-25 µm), allow for finer pitch printing and better solder joint formation on small components and pads. However, smaller particles are also more prone to oxidation and may have shorter shelf life compared to larger particle sizes like Type 3 (25-45 µm).
3. What are the main types of flux in solder paste, and how do they differ?
The main types of flux in solder paste are rosin-based, water-soluble, and no-clean. Rosin-based flux provides good wetting and solder joint formation but requires cleaning after reflow soldering. Water-soluble flux is more aggressive in removing oxides but also needs thorough cleaning. No-clean flux has lower activity and leaves minimal residue, eliminating the need for post-reflow cleaning.
4. How can solder paste defects, such as insufficient solder or bridging, be prevented?
Preventing solder paste defects involves a combination of proper stencil design, printing parameters, and process control. Some key factors include:
- Optimizing stencil aperture size and shape for the specific component and pad sizes
- Controlling printing parameters, such as squeegee pressure, speed, and separation speed
- Conducting regular solder paste inspections (SPI) to detect and correct printing defects
- Maintaining a clean and controlled printing environment to prevent contamination
- Using a compatible reflow profile that ensures proper solder melting and wetting
5. What are the consequences of using expired or contaminated solder paste in PCB assembly?
Using expired or contaminated solder paste can lead to various issues in PCB assembly, such as:
- Poor printability and inconsistent solder paste deposits
- Reduced flux activity and poor wetting during reflow soldering
- Solder joint defects, such as insufficient solder, bridging, or voiding
- Decreased solder joint strength and reliability
- Potential long-term reliability issues, such as premature component failure or intermittent connections
To avoid these issues, it is crucial to use fresh, high-quality solder paste and follow proper storage and handling guidelines. Regular solder paste testing and process monitoring can also help identify and address any quality or performance issues before they impact the final PCB assembly.
Conclusion
Solder paste plays a critical role in PCB SMT assembly, serving as the medium that creates reliable electrical and mechanical connections between surface mount components and the PCB. The quality and performance of solder paste directly impact the integrity and reliability of the assembled PCB.
Proper selection, storage, handling, and application of solder paste are essential for achieving high-quality solder joints and minimizing defects. Regular solder paste testing, process monitoring, and continuous improvement initiatives can help optimize the PCB assembly process and ensure consistent product quality.
As PCB designs continue to evolve with smaller components, finer pitches, and more complex layouts, the importance of solder paste in SMT assembly will only continue to grow. Staying up-to-date with the latest solder paste technologies, best practices, and quality control methods will be crucial for electronics manufacturers to remain competitive in the ever-advancing electronics industry.
0 Comments