The Role of PCB Stencils in Electronics Manufacturing
PCB stencils play a crucial role in the electronics manufacturing process, particularly in the surface mount assembly (SMA) stage. The main functions of a PCB stencil include:
- Applying solder paste: The stencil helps deposit the right amount of solder paste onto the PCB pads.
- Ensuring consistency: Stencils provide a uniform application of solder paste across the entire PCB, reducing the risk of defects.
- Increasing efficiency: Using a stencil is much faster and more accurate than applying solder paste manually.
How PCB Stencils are Made
PCB stencils are typically made using one of two methods:
-
Laser cutting: A high-precision laser is used to cut the openings in the stencil material according to the PCB design. This method is more accurate and efficient for complex designs and fine-pitch components.
-
Chemical etching: The stencil material is coated with a photoresist, exposed to UV light through a film with the PCB pattern, and then etched using chemicals. This method is less expensive but not as precise as laser cutting.
Method | Advantages | Disadvantages |
---|---|---|
Laser cutting | High precision, efficient for complex designs | More expensive |
Chemical etching | Lower cost | Less precise, not suitable for fine-pitch components |
Stencil Materials
PCB stencils can be made from various materials, each with its own advantages and disadvantages. The most common materials are:
Stainless Steel
Stainless steel is the most widely used material for PCB stencils due to its durability, stability, and compatibility with most solder pastes. It offers excellent performance for fine-pitch applications and is available in various thicknesses.
Advantages:
– Durable and long-lasting
– Stable and resistant to warping
– Compatible with most solder pastes
– Suitable for fine-pitch applications
Disadvantages:
– More expensive than polyimide stencils
– Can be prone to damage if mishandled
Polyimide
Polyimide, also known as Kapton, is a flexible, lightweight material that is gaining popularity for PCB stencils. It is less expensive than stainless steel and offers some unique advantages.
Advantages:
– Lower cost compared to stainless steel
– Lightweight and flexible
– Reduces the risk of damaging the PCB during stencil placement
Disadvantages:
– Less durable than stainless steel
– Not suitable for very fine-pitch applications
– May require more frequent cleaning and replacement
Stencil Thickness
The thickness of a PCB stencil is a critical factor in determining the amount of solder paste deposited on the PCB pads. The optimal stencil thickness depends on several factors, including the size and pitch of the components, the desired solder joint height, and the type of solder paste used.
Common stencil thicknesses range from 0.100 mm to 0.250 mm (4 to 10 mils), with the most frequently used thicknesses being:
- 0.100 mm (4 mils)
- 0.125 mm (5 mils)
- 0.150 mm (6 mils)
- 0.200 mm (8 mils)
To determine the appropriate stencil thickness, consider the following guidelines:
Component Pitch | Recommended Stencil Thickness |
---|---|
> 0.65 mm | 0.150 mm – 0.200 mm |
0.5 mm – 0.65 mm | 0.125 mm – 0.150 mm |
< 0.5 mm | 0.100 mm – 0.125 mm |
Keep in mind that these are general recommendations, and the optimal stencil thickness may vary depending on the specific requirements of your PCB design and assembly process.
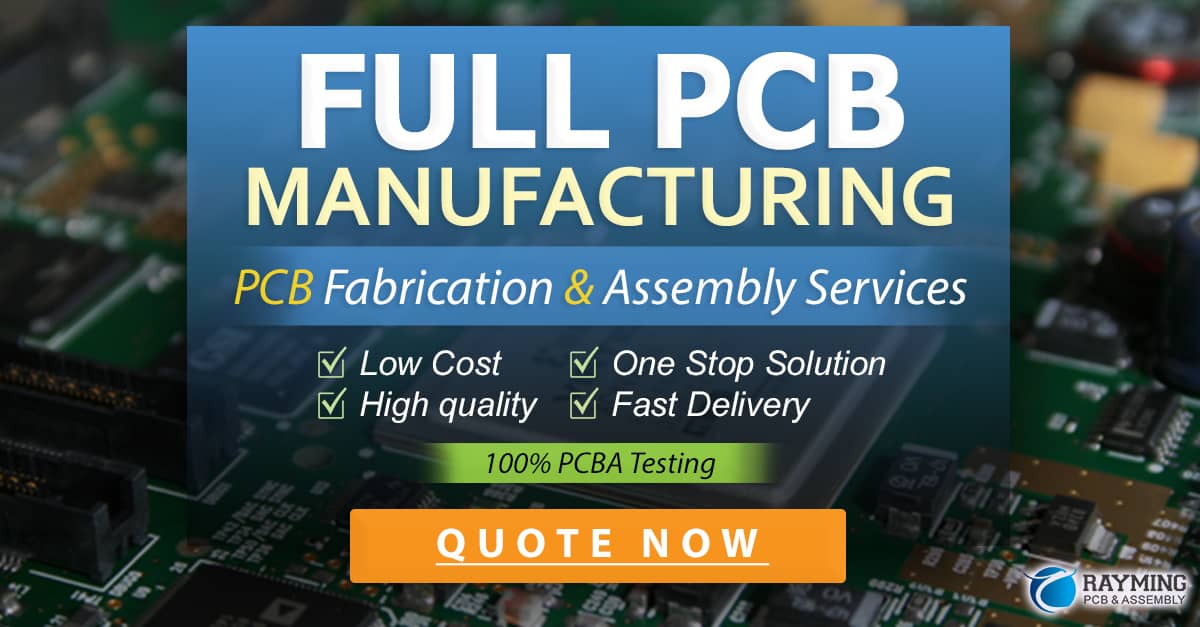
Stencil Aperture Design
The aperture design of a PCB stencil refers to the size, shape, and layout of the openings that allow solder paste to be deposited on the PCB pads. Proper aperture design is essential for achieving the desired solder paste volume and ensuring a reliable soldering process.
Factors to consider when designing stencil apertures include:
-
Aperture size: The size of the aperture should be slightly larger than the PCB pad to allow for proper solder paste release. A common rule of thumb is to add 10-20% to the pad dimensions.
-
Aperture shape: The shape of the aperture should match the shape of the PCB pad. Common shapes include rectangles, circles, and ovals. For fine-pitch components, more complex shapes like home plates or D-shapes may be used to improve paste release.
-
Aspect ratio: The aspect ratio is the relationship between the aperture width and the stencil thickness. A higher aspect ratio (smaller aperture, thicker stencil) can lead to poor paste release, while a lower aspect ratio (larger aperture, thinner stencil) may result in excessive solder paste deposition.
-
Area ratio: The area ratio is the relationship between the area of the aperture opening and the area of the aperture walls. A higher area ratio (larger opening, smaller walls) promotes better paste release.
To optimize the stencil aperture design, consider the following guidelines:
- Aperture size: 10-20% larger than the pad size
- Aspect ratio: 1.5 to 2.0 for most applications
- Area ratio: 0.66 or higher for good paste release
Stencil Frame and Mounting
PCB stencils are typically mounted in a metal frame to ensure stability and facilitate handling during the solder paste printing process. The frame also helps to maintain the stencil’s flatness and prevents warping or damage.
Common stencil frame types include:
-
Tensioned frame: The stencil is stretched and secured in a reusable frame using a tensioning system. This ensures a flat and stable surface for printing.
-
Glue-mounted frame: The stencil is glued to a disposable aluminum frame. This method is less expensive but may result in less consistent tension across the stencil.
When mounting the stencil in the frame, it is essential to ensure proper alignment with the PCB and the solder paste printer. Misalignment can lead to inaccurate solder paste deposition and assembly defects.
Stencil Cleaning and Maintenance
Regular cleaning and maintenance of PCB stencils are crucial for ensuring consistent solder paste printing quality and extending the stencil’s life. Solder paste residue, dust, and debris can accumulate on the stencil over time, leading to printing defects and reduced paste release.
To clean and maintain your PCB stencils:
-
Clean the stencil after each use: Use a lint-free cloth or wipe moistened with isopropyl alcohol (IPA) to remove solder paste residue from the stencil surface and apertures.
-
Perform periodic deep cleaning: For more thorough cleaning, use a stencil cleaning solution or ultrasonic cleaner to remove stubborn residue and debris.
-
Inspect the stencil for damage: Regularly check the stencil for signs of wear, such as bent or damaged apertures, and replace the stencil if necessary.
-
Store the stencil properly: When not in use, store the stencil in a clean, dry environment to prevent contamination and damage.
By following these cleaning and maintenance practices, you can ensure optimal performance and longevity of your PCB stencils.
Frequently Asked Questions (FAQ)
1. What is the difference between a PCB stencil and a solder paste screen?
A PCB stencil and a solder paste screen are essentially the same things, both referring to a thin sheet of material with openings that correspond to the solder pads on a PCB. The term “stencil” is more commonly used in the industry.
2. Can I reuse a PCB stencil?
Yes, PCB stencils can be reused multiple times if they are properly cleaned and maintained. However, the stencil should be replaced if it shows signs of wear or damage that could affect the solder paste printing quality.
3. How do I choose the right stencil thickness for my PCB?
The optimal stencil thickness depends on factors such as the component pitch, desired solder joint height, and solder paste type. As a general guideline, use thicker stencils (0.150 mm – 0.200 mm) for larger component pitches (> 0.65 mm) and thinner stencils (0.100 mm – 0.125 mm) for finer pitches (< 0.5 mm).
4. What is the best way to clean a PCB stencil?
To clean a PCB stencil, use a lint-free cloth or wipe moistened with isopropyl alcohol (IPA) to remove solder paste residue after each use. For deeper cleaning, use a stencil cleaning solution or ultrasonic cleaner periodically to remove stubborn residue and debris.
5. How often should I replace my PCB stencil?
The lifespan of a PCB stencil depends on factors such as usage frequency, cleaning and maintenance practices, and the complexity of the PCB design. As a general rule, replace the stencil when it shows signs of wear or damage that could affect the solder paste printing quality, such as bent or damaged apertures, or when the printing quality becomes inconsistent.
0 Comments