Introduction to PCB Stencils
PCB stencils are essential tools in the manufacturing process of printed circuit boards (PCBs). They are used to apply solder paste onto the PCB pads, ensuring precise and consistent solder paste deposition. The use of PCB stencils has revolutionized the PCB Assembly process, enabling high-volume production and improved quality control.
What is a PCB Stencil?
A PCB stencil is a thin metal sheet with apertures that correspond to the solder pads on a PCB. The stencil is placed over the PCB, and solder paste is applied using a squeegee. The solder paste is forced through the apertures, depositing it onto the PCB pads. The stencil is then removed, leaving a precise amount of solder paste on each pad.
Benefits of Using PCB Stencils
Using PCB stencils offers several benefits in the PCB assembly process:
- Precision: PCB stencils ensure accurate and consistent solder paste deposition, resulting in higher quality solder joints.
- Efficiency: Stencils allow for rapid solder paste application, reducing assembly time and increasing production throughput.
- Cost-effectiveness: The use of stencils minimizes solder paste waste and reduces the need for manual touch-ups, leading to cost savings.
- Repeatability: Stencils ensure consistent solder paste deposition across multiple PCBs, enabling high-volume production with minimal variations.
Types of PCB Stencils
There are several types of PCB stencils available, each with its own characteristics and applications. The choice of stencil type depends on factors such as the PCB design, component pitch, and manufacturing requirements. Let’s explore the different types of PCB stencils in detail.
1. Laser-Cut Stencils
Laser-cut stencils are the most common type of PCB stencils. They are created using a high-precision laser cutting machine that cuts apertures into a thin metal sheet, typically stainless steel. The laser cutting process allows for precise and intricate aperture designs, making laser-cut stencils suitable for a wide range of PCB designs.
Advantages of Laser-Cut Stencils
- High precision and accuracy
- Suitable for fine-pitch components
- Durable and long-lasting
- Quick turnaround time
Disadvantages of Laser-Cut Stencils
- Higher cost compared to other stencil types
- Limited aperture size and shape options
2. Electroformed Stencils
Electroformed stencils, also known as E-FAB stencils, are created using an electroforming process. A photoresist pattern is applied to a conductive substrate, and metal is electroplated onto the exposed areas. The photoresist is then removed, leaving a thin metal stencil with precise apertures.
Advantages of Electroformed Stencils
- Extremely precise and accurate
- Suitable for ultra-fine pitch components
- Smooth aperture walls for improved paste release
- Ability to create complex aperture shapes
Disadvantages of Electroformed Stencils
- Higher cost compared to laser-cut stencils
- Longer lead times due to the electroforming process
- Limited thickness options
3. Chemical Etched Stencils
Chemical etched stencils are manufactured using a chemical etching process. A photoresist pattern is applied to a metal sheet, and the exposed areas are chemically etched away, creating the desired apertures. Chemical etched stencils are commonly used for prototyping and low-volume production.
Advantages of Chemical Etched Stencils
- Lower cost compared to laser-cut and electroformed stencils
- Suitable for prototyping and low-volume production
- Ability to create complex aperture shapes
Disadvantages of Chemical Etched Stencils
- Lower precision compared to laser-cut and electroformed stencils
- Longer lead times due to the chemical etching process
- Limited thickness options
4. Hybrid Stencils
Hybrid stencils combine different manufacturing techniques to achieve specific requirements. For example, a hybrid stencil may have laser-cut apertures for fine-pitch components and chemically etched apertures for larger components. Hybrid stencils offer the benefits of multiple stencil types in a single stencil.
Advantages of Hybrid Stencils
- Combines the strengths of different stencil types
- Suitable for complex PCB designs with varying component sizes
- Offers flexibility in aperture design and placement
Disadvantages of Hybrid Stencils
- Higher cost due to the combination of manufacturing techniques
- Longer lead times compared to single-process stencils
Stencil Materials
PCB stencils can be made from various materials, each with its own properties and benefits. The choice of stencil material depends on factors such as durability, cost, and compatibility with the solder paste.
Stainless Steel
Stainless steel is the most commonly used material for PCB stencils. It offers excellent durability, stability, and compatibility with most solder pastes. Stainless steel stencils are available in different grades and thicknesses to suit various applications.
Nickel
Nickel stencils are known for their smooth surface finish and excellent paste release properties. They are often used for fine-pitch applications and high-volume production. Nickel stencils are more expensive than stainless steel stencils but offer superior performance in certain scenarios.
Polyimide
Polyimide stencils, also known as polymer stencils, are made from a flexible polymer material. They are commonly used for applications that require a conformable stencil, such as PCBs with irregular surfaces or flexible substrates. Polyimide stencils offer good durability and are compatible with most solder pastes.
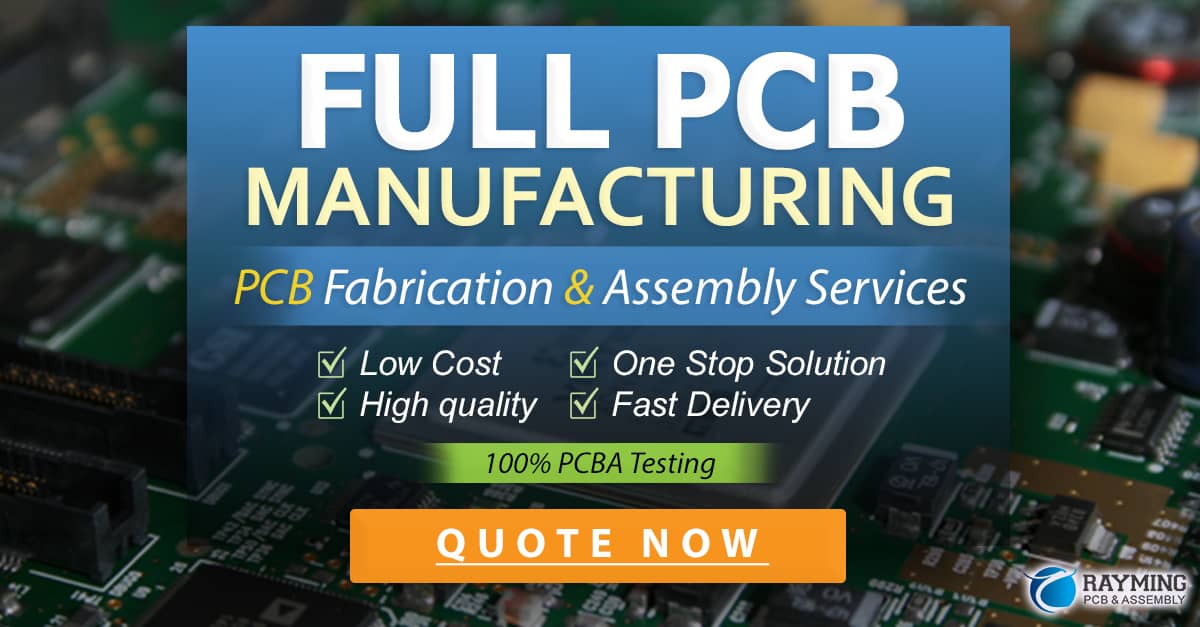
Stencil Thickness
The thickness of a PCB stencil plays a crucial role in determining the amount of solder paste deposited on the PCB pads. The choice of stencil thickness depends on factors such as the component pitch, pad size, and desired solder joint profile.
Stencil Thickness | Typical Applications |
---|---|
100-150 μm | Standard SMD components |
150-200 μm | Large SMD components, through-hole components |
50-100 μm | Fine-pitch SMD components |
25-50 μm | Ultra-fine pitch SMD components |
It’s essential to choose the appropriate stencil thickness to ensure optimal solder paste deposition and solder joint formation.
Stencil Aperture Design
The design of stencil apertures is critical for achieving accurate and consistent solder paste deposition. Aperture design considerations include:
Aperture Size and Shape
The size and shape of the apertures should match the size and shape of the corresponding PCB pads. Apertures that are too small may result in insufficient solder paste deposition, while oversized apertures may lead to solder bridging.
Aperture Wall Angle
The aperture wall angle affects the release of solder paste from the stencil. A wall angle of 5-7 degrees is commonly used to ensure proper paste release and prevent clogging.
Aperture Aspect Ratio
The aspect ratio of an aperture refers to the ratio of its width to its thickness. A higher aspect ratio (larger width compared to thickness) may result in improved paste release and more consistent deposition.
Aperture Orientation
The orientation of apertures should be optimized to ensure proper paste release and minimize the risk of solder bridging. Apertures should be oriented in a way that promotes smooth paste flow and reduces the chances of paste smearing.
Stencil Maintenance and Cleaning
Proper maintenance and cleaning of PCB stencils are essential for ensuring consistent performance and prolonging their lifespan. Regular cleaning helps prevent solder paste buildup, clogging of apertures, and contamination.
Cleaning Methods
- Manual cleaning: Using solvents and wiping materials to manually clean the stencil.
- Ultrasonic cleaning: Immersing the stencil in an ultrasonic cleaning bath with appropriate cleaning solutions.
- Automated cleaning: Using specialized stencil cleaning machines that automate the cleaning process.
Cleaning Frequency
The frequency of stencil cleaning depends on factors such as the type of solder paste used, the volume of production, and the environmental conditions. It’s recommended to establish a regular cleaning schedule based on these factors to maintain optimal stencil performance.
Storage and Handling
Proper storage and handling of PCB stencils are crucial to prevent damage and contamination. Stencils should be stored in a clean, dry environment and protected from physical damage. When handling stencils, it’s important to use clean gloves to avoid introducing contaminants.
Frequently Asked Questions (FAQ)
-
What is the difference between a PCB stencil and a solder paste screen?
A PCB stencil and a solder paste screen serve the same purpose of applying solder paste onto PCB pads. However, a stencil is typically made from a thin metal sheet, while a screen is made from a mesh material with a patterned emulsion. Stencils offer higher precision and are more commonly used in modern PCB assembly processes. -
How do I choose the right stencil thickness for my PCB?
The choice of stencil thickness depends on factors such as the component pitch, pad size, and desired solder joint profile. As a general guideline, use thinner stencils (50-100 μm) for fine-pitch components and thicker stencils (150-200 μm) for larger components and through-hole components. It’s recommended to consult with your stencil manufacturer or assembly provider for specific recommendations based on your PCB design. -
Can I reuse a PCB stencil?
Yes, PCB stencils can be reused multiple times with proper cleaning and maintenance. Regular cleaning helps remove solder paste residue and prevents clogging of apertures. However, the lifespan of a stencil depends on factors such as the frequency of use, cleaning practices, and storage conditions. It’s important to inspect the stencil regularly for signs of wear or damage and replace it when necessary. -
How do I store PCB stencils when not in use?
PCB stencils should be stored in a clean, dry environment to prevent contamination and damage. It’s recommended to store stencils in a vertical position to minimize the risk of warping or bending. Stencils can be stored in protective containers or bags to shield them from dust and debris. Avoid storing stencils in areas with high humidity or extreme temperatures, as this can affect their integrity and performance. -
Can I use the same stencil for different PCB designs?
No, each PCB design requires a specific stencil that matches its pad layout and component placement. Using a stencil designed for a different PCB can result in incorrect solder paste deposition, leading to assembly defects and reliability issues. It’s crucial to use a dedicated stencil for each PCB design to ensure accurate and consistent solder paste application.
Conclusion
PCB stencils are indispensable tools in the PCB assembly process, enabling precise and consistent solder paste deposition. Understanding the different types of PCB stencils, their materials, thicknesses, and aperture designs is essential for achieving optimal results. Proper stencil maintenance, cleaning, and storage practices are equally important to ensure consistent performance and longevity.
When selecting a PCB stencil, consider factors such as the PCB design complexity, component pitch, production volume, and budget. Consult with stencil manufacturers or assembly providers to determine the most suitable stencil type and specifications for your specific requirements.
By leveraging the appropriate PCB stencil and following best practices in stencil usage and maintenance, you can enhance the quality, efficiency, and reliability of your PCB assembly process.
0 Comments