Introduction to PCB Stencils
In the world of printed circuit board (PCB) manufacturing, PCB stencils play a crucial role in ensuring precise and efficient application of solder paste onto the board. The stencil acts as a template, allowing solder paste to be deposited onto specific areas of the PCB, where components will be placed. This article will delve into the PCB screen printing stencil making process, exploring the various steps involved and the importance of each stage.
What is a PCB Stencil?
A PCB stencil is a thin sheet of material, typically stainless steel, with laser-cut openings that correspond to the pads on a PCB. The stencil is placed over the PCB, and solder paste is applied using a squeegee, forcing the paste through the openings and onto the pads. This process ensures that the correct amount of solder paste is deposited in the right locations, which is essential for proper component placement and soldering.
Benefits of Using PCB Stencils
Using PCB stencils in the screen printing process offers several advantages:
- Precision: Stencils ensure accurate solder paste deposition, minimizing the risk of bridging or insufficient solder on pads.
- Consistency: With a stencil, the amount of solder paste applied remains consistent across the entire PCB, leading to uniform solder joints.
- Efficiency: Screen printing with stencils is a fast and efficient process, allowing for high-volume production of PCBs.
- Cost-effective: Stencils are relatively inexpensive and can be reused multiple times, reducing overall production costs.
PCB Stencil Making Process
The PCB stencil making process involves several key steps, each of which contributes to the quality and accuracy of the final stencil.
Step 1: Design and Artwork Preparation
The first step in creating a PCB stencil is to prepare the design and artwork. This involves the following:
- PCB Design: The PCB design is created using electronic design automation (EDA) software, such as Altium Designer, Eagle, or KiCad. The design includes the placement of components, traces, and pads.
- Gerber File Generation: Once the PCB design is complete, Gerber files are generated. These files contain the necessary information for manufacturing the PCB and the stencil, including the locations and dimensions of the pads.
- Stencil Artwork: The Gerber files are then used to create the stencil artwork. This artwork is essentially a negative image of the PCB, with openings corresponding to the pads where solder paste will be applied.
Step 2: Material Selection
The next step is to select the appropriate material for the stencil. The most common materials used for PCB stencils are:
- Stainless Steel: Stainless steel is the most widely used material for PCB stencils due to its durability, stability, and resistance to wear and corrosion. It is available in various thicknesses, typically ranging from 0.1 mm to 0.2 mm.
- Nickel: Nickel stencils are sometimes used for their enhanced durability and longer lifespan compared to stainless steel. However, they are more expensive and less common.
- Polyester: Polyester stencils are used for low-volume or prototype production. They are less durable than metal stencils but are cheaper and easier to produce.
Step 3: Laser Cutting
Once the material is selected, the stencil artwork is used to guide the laser cutting process. Laser cutting involves using a high-powered laser to precisely cut the openings in the stencil material according to the artwork. This process ensures accurate and clean cuts, resulting in a high-quality stencil.
Laser cutting offers several advantages over other methods, such as chemical etching:
- Precision: Laser cutting provides excellent dimensional accuracy, with minimal deviation from the artwork.
- Speed: The laser cutting process is fast, allowing for quick turnaround times.
- Clean Edges: Laser-cut stencils have clean, burr-free edges, which is essential for proper solder paste release.
Step 4: Inspection and Quality Control
After the stencil is cut, it undergoes a thorough inspection and quality control process to ensure that it meets the required specifications. This involves:
- Visual Inspection: The stencil is visually inspected for any defects, such as incomplete cuts, burrs, or damage.
- Dimensional Verification: The dimensions of the openings are measured using specialized equipment, such as a coordinate measuring machine (CMM) or a vision system, to ensure they match the artwork within the specified tolerances.
- Thickness Measurement: The thickness of the stencil is measured to ensure it is consistent and within the specified range.
Any stencils that do not meet the quality standards are rejected and remanufactured.
Step 5: Cleaning and Packaging
Once the stencil passes the quality control checks, it is cleaned to remove any debris or contaminants that may have accumulated during the manufacturing process. This is typically done using an ultrasonic cleaner with a suitable cleaning solution.
After cleaning, the stencil is packaged for shipping. It is important to package the stencil securely to prevent damage during transit. Common packaging materials include foam, bubble wrap, and protective cardboard or plastic sheets.
Stencil Design Considerations
When designing a PCB stencil, several factors must be considered to ensure optimal performance during the screen printing process.
Aperture Size and Shape
The aperture size and shape are critical factors in determining the amount of solder paste deposited on the pads. The aperture size should be slightly larger than the pad size to allow for proper solder paste release. The shape of the aperture can also affect the solder paste deposit, with common shapes being square, circular, and home plate.
Stencil Thickness
The thickness of the stencil influences the volume of solder paste deposited. Thicker stencils deposit more solder paste, while thinner stencils deposit less. The optimal thickness depends on the size and pitch of the components being used. Common stencil thicknesses range from 0.1 mm to 0.2 mm.
Aperture Wall Angle
The aperture wall angle, also known as the aspect ratio, is the ratio of the aperture width to the stencil thickness. A higher aspect ratio results in better solder paste release, as it allows for easier flow of the paste through the aperture. A minimum aspect ratio of 1.5 is generally recommended for optimal results.
Fiducial Marks
Fiducial marks are reference points on the stencil that help align it with the PCB during the screen printing process. These marks are typically located in the corners of the stencil and should be compatible with the vision system used in the assembly line.
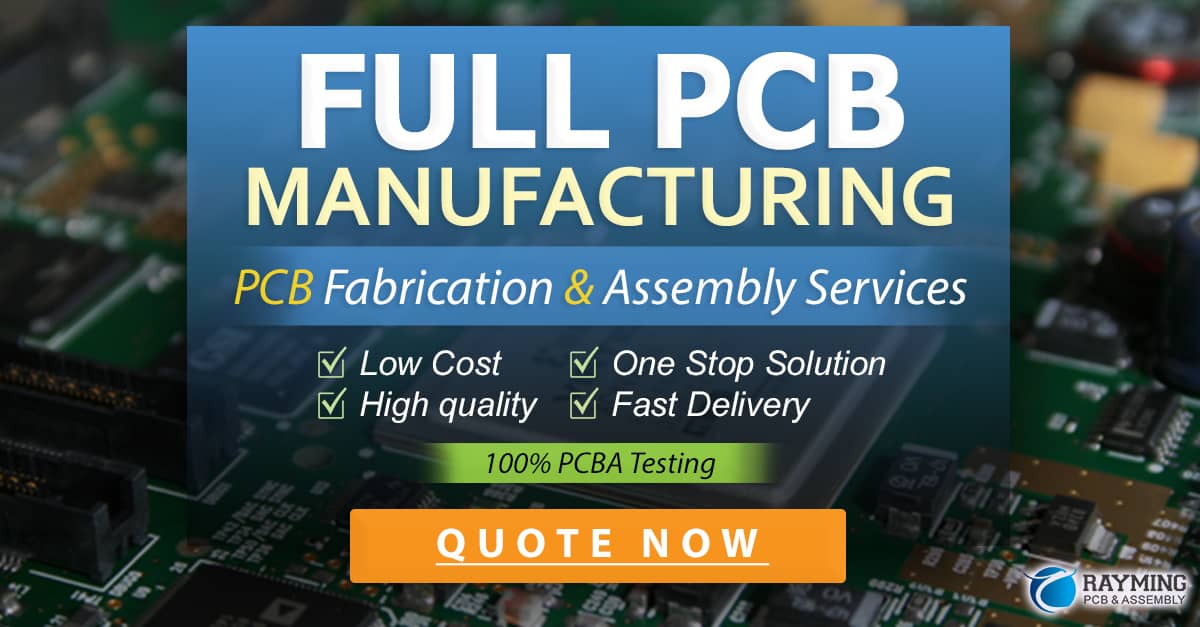
Stencil Maintenance and Care
Proper maintenance and care of PCB stencils are essential for ensuring consistent performance and longevity. Some key aspects of stencil maintenance include:
- Cleaning: Stencils should be cleaned regularly to remove any residual solder paste or contaminants. This can be done using a stencil cleaner or an ultrasonic cleaner with an appropriate cleaning solution.
- Storage: When not in use, stencils should be stored in a clean, dry environment to prevent corrosion or damage. They should be kept in protective packaging or hung vertically to minimize the risk of warping.
- Inspection: Stencils should be inspected periodically for signs of wear, damage, or clogging of apertures. Any issues should be addressed promptly to maintain print quality.
- Repair: In some cases, minor damage to a stencil can be repaired using laser welding or chemical etching. However, if the damage is extensive, it may be more cost-effective to replace the stencil.
Conclusion
The PCB screen printing stencil making process is a critical aspect of PCB manufacturing, ensuring precise and consistent solder paste deposition. By understanding the various steps involved, from design and material selection to laser cutting and quality control, manufacturers can produce high-quality stencils that meet the demands of modern electronics production.
As PCB designs continue to evolve, with smaller components and tighter tolerances, the importance of accurate and reliable stencils will only continue to grow. By staying up-to-date with the latest stencil making technologies and best practices, manufacturers can remain competitive and deliver the highest quality products to their customers.
Frequently Asked Questions (FAQ)
1. What is the most common material used for PCB stencils?
The most common material used for PCB stencils is stainless steel. Stainless steel stencils offer excellent durability, stability, and resistance to wear and corrosion, making them suitable for high-volume production.
2. What is the typical thickness of a PCB stencil?
The typical thickness of a PCB stencil ranges from 0.1 mm to 0.2 mm. The optimal thickness depends on the size and pitch of the components being used, with thicker stencils depositing more solder paste and thinner stencils depositing less.
3. What is the purpose of fiducial marks on a PCB stencil?
Fiducial marks on a PCB stencil serve as reference points to help align the stencil with the PCB during the screen printing process. These marks are typically located in the corners of the stencil and should be compatible with the vision system used in the assembly line.
4. How often should PCB stencils be cleaned?
PCB stencils should be cleaned regularly to remove any residual solder paste or contaminants. The frequency of cleaning depends on the usage and the type of solder paste being used. As a general rule, stencils should be cleaned after every shift or every 1,000 prints, whichever comes first.
5. Can damaged PCB stencils be repaired?
In some cases, minor damage to a PCB stencil can be repaired using laser welding or chemical etching. However, if the damage is extensive, it may be more cost-effective to replace the stencil entirely. Regular inspection and maintenance can help prevent damage and extend the life of the stencil.
0 Comments