Introduction to PCB Assembly
Printed Circuit Board (PCB) assembly is a crucial process in the electronics manufacturing industry. It involves the placement and soldering of electronic components onto a printed circuit board, which forms the backbone of electronic devices. The United States is a global leader in PCB assembly services, offering state-of-the-art technology, skilled workforce, and stringent quality control measures to ensure the production of high-quality PCBs.
What is PCB Assembly?
PCB assembly is the process of attaching electronic components to a printed circuit board. The components are placed on the board according to a specific design and then soldered to create electrical connections. The process can be done manually or using automated machines, depending on the complexity of the design and the volume of production.
Types of PCB Assembly
There are three main types of PCB assembly:
- Through-hole assembly: This involves inserting component leads through holes drilled in the PCB and soldering them on the opposite side.
- Surface mount assembly: This involves placing components directly onto the surface of the PCB and soldering them in place.
- Mixed assembly: This combines both through-hole and surface mount techniques.
Benefits of PCB Assembly
PCB assembly offers several benefits, including:
- Compact design: PCBs allow for the creation of smaller and more compact electronic devices.
- Reliability: PCBs offer a more reliable and stable platform for electronic components compared to other methods.
- Cost-effective: PCB assembly is a cost-effective way to produce electronic devices in large quantities.
- Customization: PCBs can be customized to meet specific design requirements and applications.
PCB Assembly Services in the USA
The United States is home to many PCB assembly service providers, ranging from small local shops to large multinational corporations. These companies offer a wide range of services, including design, prototyping, fabrication, assembly, and testing.
Top PCB Assembly Service Providers in the USA
Company | Location | Services |
---|---|---|
Jabil | St. Petersburg, FL | Design, fabrication, assembly, testing |
Flex | San Jose, CA | Design, fabrication, assembly, testing |
Plexus | Neenah, WI | Design, fabrication, assembly, testing |
Celestica | Toronto, ON, Canada | Design, fabrication, assembly, testing |
Sanmina | San Jose, CA | Design, fabrication, assembly, testing |
These companies have a global presence and offer comprehensive PCB assembly services to customers across various industries, including aerospace, automotive, medical, telecommunications, and consumer electronics.
Advantages of Using USA PCB Assembly Services
There are several advantages to using PCB assembly services in the USA:
- Quality: USA PCB assembly service providers adhere to strict quality control standards, ensuring the production of high-quality PCBs.
- Technology: USA companies have access to the latest technology and equipment, allowing them to produce complex and advanced PCBs.
- Skilled workforce: The USA has a highly skilled and experienced workforce in the electronics manufacturing industry.
- Intellectual property protection: The USA has strong intellectual property laws that protect customers’ designs and proprietary information.
- Proximity: Using a USA-based PCB assembly service provider offers the advantage of proximity, which can lead to faster turnaround times and better communication.
PCB Assembly Process
The PCB assembly process involves several steps, each of which is critical to ensuring the quality and reliability of the final product.
PCB Design
The first step in the PCB assembly process is the design of the circuit board. This involves creating a schematic diagram that shows the electrical connections between the components and then translating that into a physical layout of the board. The design must take into account factors such as component placement, signal integrity, and manufacturing constraints.
PCB Fabrication
Once the design is complete, the next step is to fabricate the PCB. This involves creating the physical board using a variety of processes, including:
- Etching: The copper layers of the board are selectively removed to create the desired circuit pattern.
- Drilling: Holes are drilled into the board to allow for the insertion of components.
- Plating: The holes and surface of the board are plated with a conductive material to improve electrical connectivity.
- Solder mask application: A protective layer is applied to the board to prevent short circuits and protect against environmental factors.
- Silkscreen printing: Text and symbols are printed onto the board to aid in assembly and identification.
Component Placement
After the PCB is fabricated, the next step is to place the components onto the board. This can be done manually or using automated machines, depending on the complexity of the design and the volume of production. The components are typically placed using a pick-and-place machine, which uses a vacuum nozzle to pick up the components and place them onto the board with high precision.
Soldering
Once the components are placed, they must be soldered to the board to create electrical connections. This can be done using various methods, including:
- Wave soldering: The board is passed over a wave of molten solder, which flows over the components and creates a connection.
- Reflow soldering: The board is heated in an oven, causing the solder paste applied to the components to melt and create a connection.
- Hand soldering: For low-volume or complex designs, components may be soldered by hand using a soldering iron.
Inspection and Testing
After the components are soldered, the board undergoes a series of inspections and tests to ensure that it meets the required specifications and functions properly. This may include:
- Visual inspection: The board is visually inspected for defects such as missing components, solder bridges, or damaged components.
- Automated optical inspection (AOI): An automated system uses cameras to inspect the board for defects.
- X-ray inspection: X-rays are used to inspect the internal structure of the board and ensure that the solder joints are properly formed.
- Functional testing: The board is powered on and tested to ensure that it functions as intended.
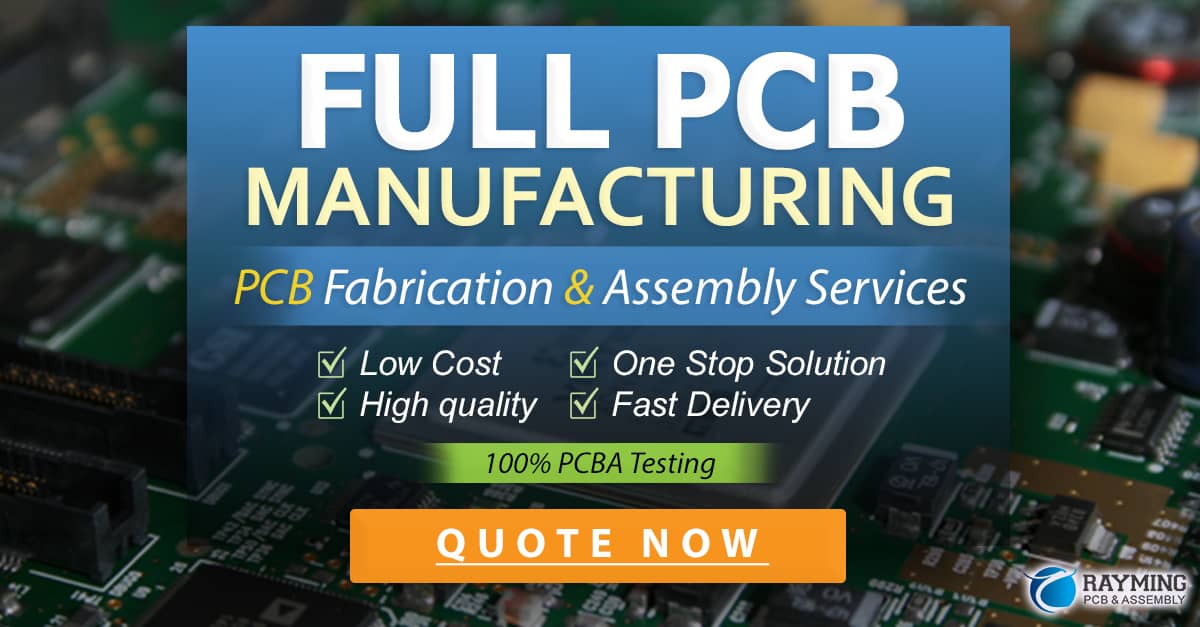
Quality Control in PCB Assembly
Quality control is a critical aspect of PCB assembly, as even minor defects can lead to failures in the final product. USA PCB assembly service providers adhere to strict quality control standards to ensure the production of high-quality PCBs.
Quality Control Standards
There are several quality control standards that are commonly used in the PCB assembly industry, including:
- IPC standards: The IPC (Association Connecting Electronics Industries) publishes a set of standards for PCB design, fabrication, and assembly. These standards are widely used in the industry and provide guidelines for ensuring the quality and reliability of PCBs.
- ISO standards: The International Organization for Standardization (ISO) publishes a set of quality management standards that are applicable to the PCB assembly industry. These standards provide guidelines for establishing and maintaining a quality management system.
- MIL-SPEC standards: The United States Department of Defense publishes a set of standards for PCB assembly that are used in military and aerospace applications. These standards are more stringent than commercial standards and require additional testing and documentation.
Quality Control Techniques
There are several quality control techniques that are used in PCB assembly to ensure the production of high-quality boards, including:
- Statistical process control (SPC): SPC is a method of monitoring the manufacturing process to identify and correct issues before they lead to defects. This involves collecting data on key process parameters and using statistical analysis to identify trends and variations.
- Failure mode and effects analysis (FMEA): FMEA is a systematic method of identifying potential failure modes in a product or process and assessing their impact on the final product. This allows for the identification and mitigation of potential issues before they occur.
- Continuous improvement: Continuous improvement is a philosophy of constantly seeking ways to improve the manufacturing process and product quality. This involves regularly reviewing processes and procedures and implementing changes to improve efficiency and reduce defects.
Choosing a PCB Assembly Service Provider
Choosing the right PCB assembly service provider is critical to ensuring the success of your project. There are several factors to consider when selecting a provider, including:
Technical Capabilities
The first factor to consider is the technical capabilities of the provider. This includes their experience with the specific type of PCB you require, their manufacturing capabilities, and their ability to meet your design requirements. It is important to choose a provider that has experience with the technology and processes required for your project.
Quality Control
Quality control is another critical factor to consider when choosing a PCB assembly service provider. You should look for a provider that has a robust quality management system in place and adheres to industry standards such as IPC and ISO. It is also important to consider their track record of producing high-quality PCBs and their ability to meet your quality requirements.
Capacity and Lead Time
The capacity and lead time of the provider are also important factors to consider. You should choose a provider that has the capacity to meet your volume requirements and can deliver your PCBs within your required timeframe. It is important to discuss your requirements upfront and ensure that the provider can meet your needs.
Cost
Cost is always a consideration when choosing a PCB assembly service provider. However, it is important to balance cost with quality and reliability. Choosing the lowest cost provider may result in lower quality PCBs that do not meet your requirements. It is important to get quotes from multiple providers and compare not only the cost but also the value they provide in terms of quality, reliability, and service.
Communication and Support
Finally, communication and support are critical factors to consider when choosing a PCB assembly service provider. You should look for a provider that is responsive and easy to communicate with throughout the manufacturing process. They should also provide support and assistance with any issues or questions that arise during the project.
Frequently Asked Questions (FAQs)
- What is the difference between through-hole and surface mount assembly?
-
Through-hole assembly involves inserting component leads through holes drilled in the PCB and soldering them on the opposite side, while surface mount assembly involves placing components directly onto the surface of the PCB and soldering them in place.
-
What quality control standards are commonly used in PCB assembly?
-
IPC standards, ISO standards, and MIL-SPEC standards are commonly used in PCB assembly to ensure the quality and reliability of PCBs.
-
How do I choose the right PCB assembly service provider for my project?
-
When choosing a PCB assembly service provider, consider their technical capabilities, quality control processes, capacity and lead time, cost, and communication and support. It is important to choose a provider that can meet your specific requirements and provide high-quality PCBs within your timeframe and budget.
-
What is the typical lead time for PCB assembly?
-
The lead time for PCB assembly can vary depending on the complexity of the design, the volume of production, and the provider’s capacity. Typical lead times can range from a few days to several weeks, so it is important to discuss your requirements upfront and ensure that the provider can meet your needs.
-
What should I do if I encounter issues with my PCB assembly?
- If you encounter issues with your PCB assembly, the first step is to contact your PCB assembly service provider. They should provide support and assistance to help resolve any issues or questions that arise during the project. It is important to work closely with your provider throughout the manufacturing process to ensure that any issues are identified and addressed quickly.
Conclusion
PCB assembly is a critical process in the electronics manufacturing industry, and the United States is a global leader in providing high-quality PCB assembly services. From design to fabrication, component placement, soldering, and testing, each step of the PCB assembly process is crucial to ensuring the quality and reliability of the final product.
When choosing a PCB assembly service provider in the USA, it is important to consider factors such as technical capabilities, quality control processes, capacity and lead time, cost, and communication and support. By selecting the right provider and working closely with them throughout the manufacturing process, you can ensure the success of your project and the production of high-quality PCBs that meet your specific requirements.
As the electronics industry continues to evolve and grow, the demand for high-quality PCB assembly services will only increase. By leveraging the expertise and capabilities of USA PCB assembly service providers, businesses can stay competitive and deliver innovative products to market quickly and efficiently.
0 Comments