Introduction to ENIG test pads
Electroless Nickel Immersion Gold (ENIG) is a popular surface finish for printed circuit boards (PCBs) due to its excellent solderability, durability, and compatibility with various components. ENIG test pads are essential for ensuring the quality and reliability of PCBs during the manufacturing process. However, a common question arises: should ENIG test pads be used with or without Solder Paste? In this article, we will explore the advantages and disadvantages of both approaches and provide guidance on when to use each method.
What are ENIG Test Pads?
ENIG test pads are small, exposed areas on a PCB that are used for testing purposes. These pads are typically located near the edge of the board and are not connected to any components or traces. The purpose of ENIG test pads is to allow manufacturers to assess the quality of the ENIG surface finish and ensure that it meets the required specifications.
The Importance of ENIG Surface Finish
ENIG is a two-layer surface finish that consists of an electroless nickel layer and a thin immersion gold layer. The nickel layer provides a barrier against copper diffusion and enhances the durability of the surface finish. The gold layer, on the other hand, protects the nickel from oxidation and ensures excellent solderability.
A high-quality ENIG surface finish is crucial for several reasons:
- Solderability: ENIG provides a flat, uniform surface that allows for reliable soldering of components to the PCB.
- Durability: The nickel layer helps prevent wear and tear, making ENIG suitable for applications that require frequent insertions or removals of components.
- Compatibility: ENIG is compatible with a wide range of components, including fine-pitch devices and Ball Grid Arrays (BGAs).
ENIG Test Pads With Solder Paste
One approach to testing ENIG surface finish is to apply solder paste to the test pads and then subject them to the same reflow process as the rest of the PCB. This method simulates the actual soldering process and can provide valuable insights into the quality of the ENIG finish.
Advantages of Using Solder Paste on ENIG Test Pads
- Realistic testing: By applying solder paste to the test pads, manufacturers can assess how well the ENIG finish will perform during the actual soldering process. This approach helps identify potential issues, such as poor wetting or dewetting of the solder.
- Detecting defects: The use of solder paste on test pads can help reveal defects in the ENIG finish, such as contamination, insufficient thickness, or uneven coverage. These defects may not be apparent when testing the pads without solder paste.
- Assessing intermetallic compound (IMC) formation: The application of solder paste allows manufacturers to evaluate the formation of IMCs between the solder and the ENIG finish. IMCs are essential for creating a strong, reliable solder joint, and their presence on test pads indicates that the ENIG finish is suitable for soldering.
Disadvantages of Using Solder Paste on ENIG Test Pads
- Additional processing: Applying solder paste to the test pads requires an extra step in the manufacturing process, which can increase production time and costs.
- Potential for false positives: If the solder paste application or reflow process is not properly controlled, it may lead to false positive results. For example, insufficient solder paste or incorrect reflow parameters can cause poor wetting on the test pads, even if the ENIG finish itself is of high quality.
- Limited coverage: Solder paste application may not cover the entire surface of the test pad, which can limit the ability to assess the uniformity of the ENIG finish.
ENIG Test Pads Without Solder Paste
Another approach to testing ENIG surface finish is to evaluate the test pads without applying solder paste. This method focuses on assessing the physical and chemical properties of the ENIG finish itself, rather than its performance during the soldering process.
Advantages of Testing ENIG Pads Without Solder Paste
- Simplicity: Testing ENIG pads without solder paste is a straightforward process that does not require additional steps or materials. This approach can save time and reduce manufacturing costs.
- Comprehensive coverage: Without solder paste, the entire surface of the test pad is exposed, allowing for a more thorough evaluation of the ENIG finish. This comprehensive coverage enables manufacturers to assess the uniformity, thickness, and overall quality of the finish.
- Isolating ENIG performance: By testing the pads without solder paste, manufacturers can isolate the performance of the ENIG finish from other variables, such as solder paste quality or reflow parameters. This approach helps identify issues specific to the ENIG process.
Disadvantages of Testing ENIG Pads Without Solder Paste
- Limited solderability assessment: Testing ENIG pads without solder paste does not provide direct information about how well the finish will perform during the actual soldering process. While the physical and chemical properties of the ENIG finish can be evaluated, its solderability cannot be fully assessed without applying solder paste.
- Inability to detect certain defects: Some defects, such as poor wetting or dewetting of the solder, may not be apparent when testing ENIG pads without solder paste. These issues can only be identified during the soldering process.
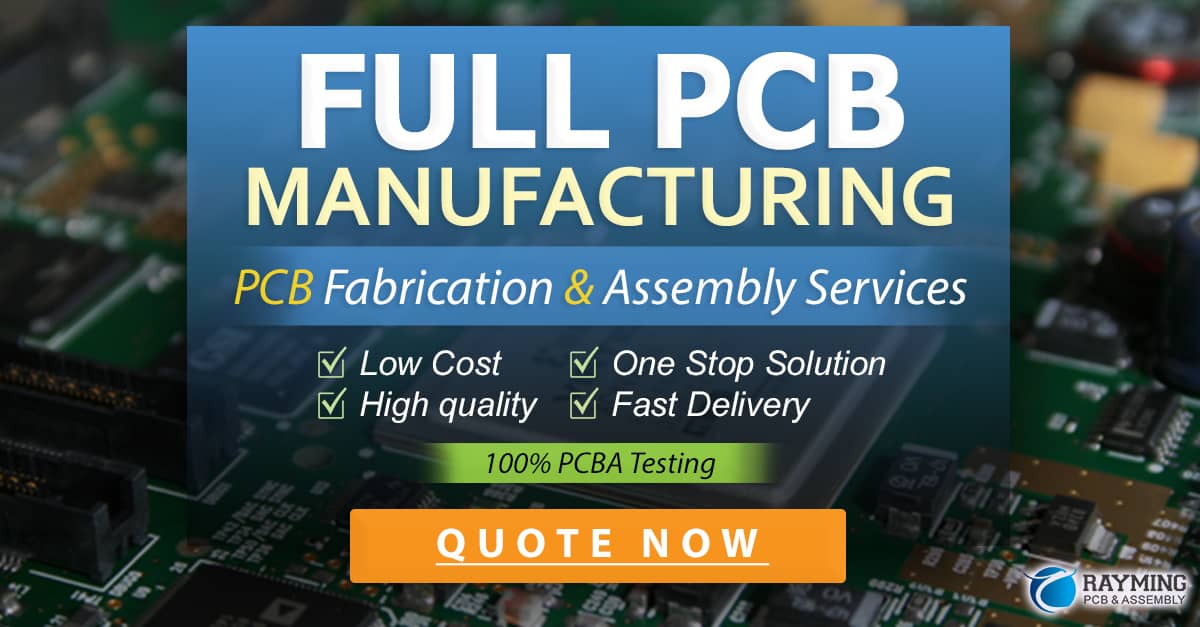
When to Use Each Method
The decision to use ENIG test pads with or without solder paste depends on the specific goals and requirements of the PCB manufacturing process.
When to Use ENIG Test Pads With Solder Paste
- Solderability verification: If the primary goal is to assess the solderability of the ENIG finish, applying solder paste to the test pads is the most appropriate approach. This method provides a realistic simulation of the soldering process and can help identify potential issues.
- Qualifying new ENIG processes: When implementing a new ENIG process or changing process parameters, using solder paste on test pads can help validate the quality and reliability of the finish. This approach ensures that the ENIG finish will perform well during the actual soldering process.
- Troubleshooting soldering issues: If a PCB is experiencing soldering problems, such as poor wetting or dewetting, applying solder paste to the test pads can help determine whether the issue is related to the ENIG finish or other factors, such as solder paste quality or reflow parameters.
When to Use ENIG Test Pads Without Solder Paste
- Routine quality control: For regular quality control checks, testing ENIG pads without solder paste is often sufficient. This approach allows manufacturers to quickly assess the physical and chemical properties of the ENIG finish and ensure that it meets the required specifications.
- Evaluating ENIG process consistency: When monitoring the consistency of an established ENIG process, testing the pads without solder paste can provide a clear picture of the finish quality over time. This method helps identify any deviations or trends in the ENIG process performance.
- Cost and time considerations: In situations where cost and time are critical factors, testing ENIG pads without solder paste may be the preferred approach. This method eliminates the need for additional processing steps and materials, reducing manufacturing costs and cycle times.
Best Practices for ENIG Test Pad Evaluation
Regardless of whether ENIG test pads are used with or without solder paste, several best practices should be followed to ensure reliable and consistent results:
- Establish clear acceptance criteria: Define specific acceptance criteria for ENIG test pad evaluation, such as minimum thickness, uniformity, and solderability requirements. These criteria should be based on industry standards and customer specifications.
- Use appropriate test methods: Select test methods that are suitable for evaluating the desired properties of the ENIG finish. Common test methods include visual inspection, thickness measurement, X-ray fluorescence (XRF) analysis, and Wetting Balance tests.
- Maintain consistent process conditions: Ensure that the ENIG process parameters, such as plating times, temperatures, and chemical concentrations, are consistently maintained within the specified ranges. Variations in process conditions can affect the quality and performance of the ENIG finish.
- Implement statistical process control (SPC): Use SPC techniques to monitor and control the ENIG process over time. Collecting and analyzing data from test pad evaluations can help identify trends, detect process shifts, and implement corrective actions when necessary.
- Regularly calibrate and maintain equipment: Ensure that all equipment used for ENIG processing and test pad evaluation is regularly calibrated and maintained according to the manufacturer’s recommendations. Proper equipment maintenance helps ensure accurate and reliable results.
FAQs
-
Q: What is the purpose of ENIG test pads on a PCB?
A: ENIG test pads are used to assess the quality and reliability of the ENIG surface finish during the PCB manufacturing process. They help ensure that the ENIG finish meets the required specifications and will perform well during the soldering process. -
Q: Can ENIG test pads be used without applying solder paste?
A: Yes, ENIG test pads can be evaluated without applying solder paste. This approach focuses on assessing the physical and chemical properties of the ENIG finish itself, rather than its performance during the soldering process. -
Q: What are the advantages of using solder paste on ENIG test pads?
A: Applying solder paste to ENIG test pads allows for realistic testing of the solderability of the finish. It can help detect defects, assess intermetallic compound formation, and identify potential issues that may arise during the actual soldering process. -
Q: When should ENIG test pads be used without solder paste?
A: ENIG test pads can be used without solder paste for routine quality control checks, evaluating the consistency of an established ENIG process, or when cost and time considerations are critical. This approach provides a quick assessment of the physical and chemical properties of the ENIG finish. -
Q: What are some best practices for ENIG test pad evaluation?
A: Best practices for ENIG test pad evaluation include establishing clear acceptance criteria, using appropriate test methods, maintaining consistent process conditions, implementing statistical process control, and regularly calibrating and maintaining equipment. These practices help ensure reliable and consistent results.
Conclusion
The decision to use ENIG test pads with or without solder paste depends on the specific goals and requirements of the PCB manufacturing process. Using solder paste on test pads provides a realistic assessment of solderability and can help detect defects and potential issues during the soldering process. On the other hand, testing ENIG pads without solder paste allows for a quick evaluation of the physical and chemical properties of the finish and is suitable for routine quality control and process consistency monitoring.
By understanding the advantages and disadvantages of each approach and following best practices for ENIG test pad evaluation, manufacturers can ensure the quality and reliability of their PCBs. Implementing a comprehensive testing strategy that combines both methods, as appropriate, can provide a complete picture of the ENIG finish performance and help optimize the manufacturing process.
As the electronics industry continues to evolve and demand higher-quality and more reliable PCBs, the use of ENIG test pads will remain an essential tool for manufacturers. By staying informed about the latest testing methods and best practices, PCB Manufacturers can stay ahead of the curve and deliver products that meet the ever-increasing expectations of their customers.
Method | Advantages | Disadvantages |
---|---|---|
ENIG Test Pads With Solder Paste | – Realistic testing of solderability – Detection of defects – Assessment of intermetallic compound formation |
– Additional processing steps and costs – Potential for false positives – Limited coverage of the test pad surface |
ENIG Test Pads Without Solder Paste | – Simplicity and reduced costs – Comprehensive coverage of the test pad surface – Isolation of ENIG performance |
– Limited assessment of solderability – Inability to detect certain defects related to soldering |
0 Comments