What is PCB Tenting?
PCB tenting, also known as via tenting or Tented Vias, is a process in printed circuit board (PCB) manufacturing where the small holes (vias) that connect different layers of the board are covered with a thin layer of solder mask material. This technique is used to protect the vias from contamination, improve the PCB’s mechanical strength, and enhance its overall aesthetics.
Benefits of PCB Tenting
-
Protection from contamination: By covering the vias with solder mask, PCB tenting prevents dust, debris, and other contaminants from entering the holes and causing short circuits or other issues.
-
Improved mechanical strength: Tented vias provide additional support to the PCB, making it more resistant to bending, twisting, and other physical stresses.
-
Enhanced aesthetics: PCB tenting creates a cleaner, more uniform appearance by hiding the vias beneath the solder mask layer.
-
Reduced solder bridging: When vias are left exposed, there is a risk of solder bridging during the assembly process. PCB tenting minimizes this risk by covering the vias.
-
Better signal integrity: Tented vias can help maintain signal integrity by reducing the potential for unwanted signal reflections and crosstalk.
The PCB Manufacturing Process
To understand the importance of PCB tenting, it’s essential to have a basic understanding of the PCB manufacturing process. The main steps involved in creating a PCB are:
-
Design: The PCB layout is designed using specialized software, taking into account factors such as component placement, signal routing, and manufacturing constraints.
-
Fabrication: The physical PCB is created by layering and bonding Copper-Clad Laminates, drilling holes for vias and component leads, and applying solder mask and silkscreen layers.
-
Assembly: Electronic components are soldered onto the PCB using various techniques, such as through-hole or surface-mount assembly.
-
Testing and inspection: The assembled PCB undergoes rigorous testing and inspection to ensure proper functionality and adherence to quality standards.
PCB tenting is performed during the fabrication stage, after the vias have been drilled but before the solder mask is applied.
Types of Vias in PCBs
There are several types of vias used in PCB design, each with its own characteristics and applications:
Via Type | Description | Application |
---|---|---|
Through-hole via | A hole drilled through the entire PCB, connecting all layers | Used for through-hole components and in simpler PCB designs |
Blind via | A hole drilled from the surface of the PCB to an inner layer, but not through the entire board | Used to connect surface layers to inner layers in multi-layer PCBs |
Buried via | A hole connecting two or more inner layers, but not extending to the surface of the PCB | Used to interconnect inner layers in complex, high-density PCB designs |
Microvias | A small-diameter via (typically less than 0.15mm) used for high-density interconnects | Used in advanced packaging technologies, such as HDI (High-Density Interconnect) PCBs |
PCB tenting can be applied to all types of vias, depending on the specific design requirements and manufacturing capabilities.
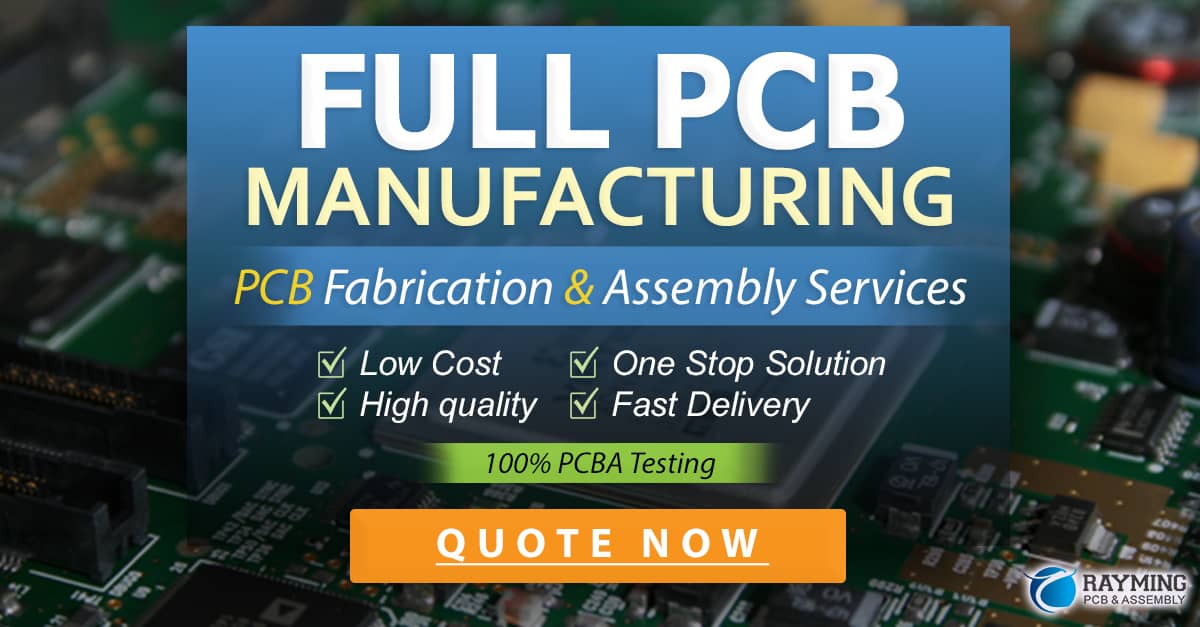
Designing for PCB Tenting
When designing a PCB with tented vias, there are several key considerations to keep in mind:
-
Via size and spacing: Ensure that the vias are sized and spaced appropriately to allow for proper solder mask coverage. Consult with your PCB manufacturer for their specific guidelines.
-
Solder mask clearance: Provide adequate clearance around the vias for the solder mask to adhere properly. Again, follow your manufacturer’s recommendations.
-
Via location: Place vias in areas that are easily accessible for tenting during the manufacturing process. Avoid placing vias too close to component pads or other features that may interfere with the tenting process.
-
Material selection: Choose a solder mask material that is compatible with the PCB substrate and provides good coverage and adhesion.
-
Design for manufacturability: Collaborate with your PCB manufacturer to ensure that your design is optimized for their specific tenting process and capabilities.
PCB Tenting Techniques
There are two primary methods for applying solder mask to tent vias:
-
Liquid photoimageable solder mask (LPISM): In this process, a liquid solder mask is applied to the PCB surface, then exposed to UV light through a photomask. The exposed areas harden, while the unexposed areas are washed away, leaving the vias tented.
-
Dry film solder mask (DFSM): This method involves laminating a dry film solder mask onto the PCB surface, then exposing it to UV light through a photomask. The exposed areas remain intact, while the unexposed areas are removed during development, resulting in tented vias.
Both techniques have their advantages and limitations, and the choice often depends on the specific PCB design, material requirements, and the manufacturer’s capabilities.
Challenges and Limitations of PCB Tenting
While PCB tenting offers numerous benefits, there are some challenges and limitations to consider:
-
Incomplete tenting: If the solder mask does not fully cover the via, it can leave a small opening that allows contaminants to enter or solder to escape during assembly.
-
Thin solder mask coverage: In some cases, the solder mask over the tented vias may be thinner than the surrounding areas, making it more susceptible to damage or wear over time.
-
Reduced thermal conductivity: Tented vias can limit the PCB’s ability to dissipate heat, as the solder mask material has lower thermal conductivity than the copper used in the vias.
-
Increased manufacturing complexity: Tenting Vias adds an extra step to the PCB fabrication process, which can increase production time and costs.
Despite these challenges, the benefits of PCB tenting often outweigh the drawbacks for many applications.
Best Practices for PCB Tenting
To ensure successful PCB tenting, follow these best practices:
-
Communicate with your manufacturer: Work closely with your PCB manufacturer to understand their tenting capabilities, guidelines, and recommendations.
-
Follow design rules: Adhere to the manufacturer’s design rules for via size, spacing, and solder mask clearance to ensure optimal tenting results.
-
Consider the application: Evaluate whether PCB tenting is necessary or beneficial for your specific application, taking into account factors such as the operating environment, reliability requirements, and cost constraints.
-
Test and validate: Perform thorough testing and validation of your tented PCB design to ensure that it meets all performance and reliability requirements.
-
Monitor the manufacturing process: Regularly monitor and audit the PCB fabrication process to maintain consistent tenting quality and identify any potential issues early on.
FAQ
-
Is PCB tenting necessary for all PCB designs?
No, PCB tenting is not always necessary. The decision to use tented vias depends on factors such as the operating environment, reliability requirements, and design complexity. In some cases, leaving vias untented may be sufficient or even preferable. -
Can PCB tenting be applied selectively to certain vias?
Yes, selective tenting is possible. In some designs, only specific vias may require tenting, while others are left untented. This can be useful for optimizing the balance between protection, thermal management, and manufacturing efficiency. -
How does PCB tenting affect signal integrity?
Tented vias can help improve signal integrity by reducing the potential for unwanted signal reflections and crosstalk. The solder mask material acts as an insulator, minimizing the interaction between signals passing through adjacent vias. -
What is the impact of PCB tenting on manufacturing costs?
PCB tenting can slightly increase manufacturing costs due to the additional processing step and materials required. However, the cost impact is often outweighed by the benefits of improved reliability, protection, and aesthetics. -
Can PCB tenting be used with high-density interconnect (HDI) PCBs?
Yes, PCB tenting is commonly used in HDI PCB designs, particularly with microvias. Tenting helps protect the small, delicate vias and maintains the high-density layout’s integrity. However, the tenting process must be carefully controlled to ensure proper solder mask coverage and adhesion.
Conclusion
PCB tenting is a valuable technique in PCB manufacturing that offers numerous benefits, including protection from contamination, improved mechanical strength, enhanced aesthetics, reduced solder bridging, and better signal integrity. By understanding the importance of PCB tenting and following best practices for design and manufacturing, you can create high-quality, reliable PCBs that meet the demands of today’s complex electronic systems.
Effective communication with your PCB manufacturer, adherence to design guidelines, and thorough testing and validation are essential for successful PCB tenting implementation. As PCB technology continues to evolve, the role of tenting via will remain crucial in ensuring the performance, reliability, and longevity of advanced electronic devices.
0 Comments