Introduction to Soldermask Expansion
Soldermask expansion, also known as soldermask clearance or solder resist clearance, is a crucial parameter in the design and manufacturing of printed circuit boards (PCBs). It refers to the additional space around the copper pads on a PCB, which is not covered by the soldermask layer. This expansion allows for proper soldering of surface mount devices (SMDs) to the pads, ensuring a reliable electrical connection.
What is Soldermask?
Soldermask, or solder resist, is a thin protective layer applied to the copper traces of a PCB. Its primary purpose is to prevent solder from bridging between adjacent pads or traces during the soldering process. Soldermask also provides insulation and protection against oxidation and contamination of the copper traces.
The Importance of Soldermask Expansion
Soldermask expansion plays a vital role in the successful assembly of SMD components on a PCB. Without adequate soldermask clearance around the pads, several issues may arise:
- Insufficient solder joint formation
- Difficulty in component placement
- Increased risk of solder bridging
- Reduced reliability of the electrical connection
By providing the appropriate soldermask expansion, designers can ensure that the SMD components are properly soldered to the pads, resulting in a more reliable and robust PCB assembly.
Factors Affecting Soldermask Expansion
Several factors influence the determination of the optimal soldermask expansion value for a given PCB design. These include:
PCB Manufacturing Capabilities
The soldermask expansion value depends on the capabilities of the PCB manufacturer. Different manufacturers may have varying limitations on the minimum soldermask expansion they can achieve consistently. It is essential to consult with the manufacturer and understand their capabilities before finalizing the design.
SMD Component Package Type
The package type of the SMD component being used also affects the soldermask expansion value. Different package types, such as chip resistors, QFPs, BGAs, and QFNs, have varying pad sizes and pitch requirements. The soldermask expansion should be adjusted accordingly to ensure proper soldering and prevent solder bridging.
PCB Assembly Process
The PCB assembly process, particularly the soldering method employed, influences the soldermask expansion value. Different soldering techniques, such as wave soldering, reflow soldering, and hand soldering, have different requirements for soldermask clearance. The expansion value should be optimized based on the specific assembly process being used.
PCB Material and Thickness
The material and thickness of the PCB substrate can also impact the soldermask expansion value. Different materials, such as FR-4, Rogers, or polyimide, have varying thermal expansion coefficients and dimensional stability. Thicker PCBs may require larger soldermask expansion values to accommodate potential warpage during the soldering process.
Calculating Soldermask Expansion
Calculating the appropriate soldermask expansion value involves considering the pad size, Soldermask Thickness, and the desired clearance between the pad and the soldermask opening. The general formula for calculating soldermask expansion is:
Soldermask Expansion = (Soldermask Opening – Pad Size) / 2
For example, if a pad has a size of 0.5mm x 0.5mm and the desired soldermask opening is 0.7mm x 0.7mm, the soldermask expansion would be:
Soldermask Expansion = (0.7mm – 0.5mm) / 2 = 0.1mm
This means that the soldermask opening would extend 0.1mm beyond each side of the pad.
Recommended Soldermask Expansion Values
The recommended soldermask expansion values vary depending on the SMD component package type and the PCB manufacturing capabilities. The following table provides general guidelines for soldermask expansion based on common SMD package types:
SMD Package Type | Recommended Soldermask Expansion |
---|---|
Chip Resistor | 0.05mm – 0.1mm |
SOT-23 | 0.1mm – 0.15mm |
SOIC | 0.1mm – 0.2mm |
QFP | 0.15mm – 0.25mm |
BGA | 0.2mm – 0.3mm |
It is important to note that these values are general recommendations and may vary based on specific manufacturer guidelines and PCB design requirements.
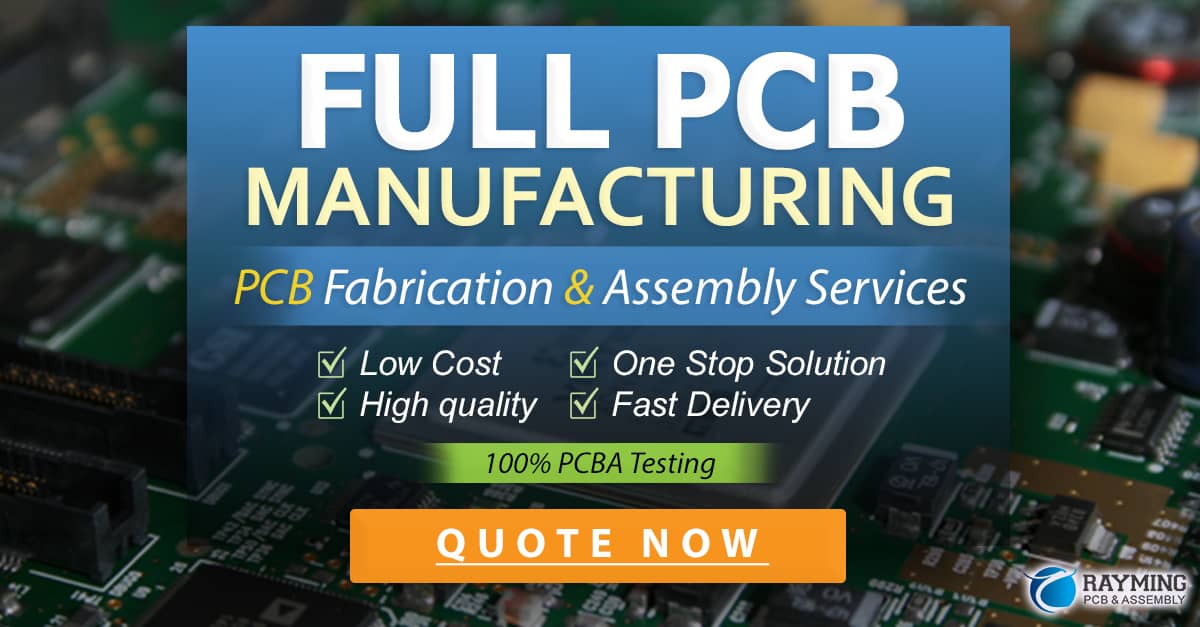
Best Practices for Soldermask Expansion
To ensure optimal soldermask expansion and achieve reliable PCB assembly, consider the following best practices:
-
Consult with the PCB manufacturer and assembly provider to understand their capabilities and limitations regarding soldermask expansion.
-
Use the recommended soldermask expansion values for the specific SMD component package types being used in the design.
-
Maintain consistent soldermask expansion values throughout the PCB design to ensure uniform soldering results.
-
Consider the thermal expansion characteristics of the PCB material and adjust the soldermask expansion accordingly to minimize warpage during soldering.
-
Conduct thorough design reviews and use design for manufacturability (DFM) tools to identify and address any soldermask expansion issues before finalizing the PCB layout.
Common Issues Related to Soldermask Expansion
Improper soldermask expansion can lead to several manufacturing and reliability issues, such as:
Solder Bridging
Insufficient soldermask expansion can result in solder bridging between adjacent pads during the soldering process. This can cause short circuits and lead to PCB malfunction.
Poor Solder Joint Formation
Excessive soldermask expansion can hinder proper solder joint formation between the SMD component and the pad. This can result in weak or unreliable electrical connections, potentially leading to intermittent failures or reduced product lifespan.
Difficulty in Component Placement
Inaccurate soldermask expansion can make it challenging to place SMD components accurately on the pads. Misaligned components can cause assembly issues and affect the overall quality of the PCB.
Reduced Manufacturing Yield
Inconsistent or improper soldermask expansion values can lead to increased manufacturing defects and lower production yields. This can result in higher costs and longer lead times for PCB fabrication and assembly.
Frequently Asked Questions (FAQ)
-
What is soldermask expansion, and why is it important?
Soldermask expansion refers to the additional space around the copper pads on a PCB that is not covered by the soldermask layer. It is important because it allows for proper soldering of SMD components to the pads, ensuring a reliable electrical connection. -
How does soldermask expansion affect the PCB assembly process?
Soldermask expansion affects the PCB assembly process by providing adequate clearance for solder to form a proper joint between the SMD component and the pad. Insufficient expansion can lead to solder bridging, while excessive expansion can hinder proper solder joint formation. -
What factors should be considered when determining the soldermask expansion value?
Factors to consider when determining the soldermask expansion value include PCB manufacturing capabilities, SMD component package type, PCB assembly process, and PCB material and thickness. -
How can I calculate the appropriate soldermask expansion value for my PCB design?
The soldermask expansion value can be calculated using the formula: Soldermask Expansion = (Soldermask Opening – Pad Size) / 2. It is important to consult with the PCB manufacturer and consider the specific requirements of the SMD components being used. -
What are some best practices for ensuring optimal soldermask expansion in PCB design?
Best practices for ensuring optimal soldermask expansion include consulting with the PCB manufacturer and assembly provider, using recommended expansion values for specific SMD package types, maintaining consistent expansion values throughout the design, considering thermal expansion characteristics of the PCB material, and conducting thorough design reviews using DFM tools.
Conclusion
Soldermask expansion is a critical parameter in the design and manufacturing of PCBs. It ensures proper soldering of SMD components to the copper pads, resulting in reliable electrical connections and overall PCB functionality. By understanding the factors that influence soldermask expansion and following best practices, designers can optimize their PCB layouts for manufacturability and reliability.
Consulting with PCB manufacturers, using recommended expansion values, and conducting thorough design reviews are essential steps in achieving optimal soldermask expansion. By addressing this critical aspect of PCB design, designers can minimize manufacturing issues, improve production yields, and ultimately deliver high-quality, reliable electronic products to the market.
0 Comments