Introduction to SMT PCB Assembly
Surface mount technology (SMT) is a method of assembling printed circuit boards (PCBs) where components are mounted directly onto the surface of the PCB rather than through holes. SMT has revolutionized electronics manufacturing by allowing for smaller, lighter, and more reliable circuit boards. This guide will provide a comprehensive overview of the SMT PCB assembly process from start to finish.
Benefits of SMT
Some key benefits of SMT include:
- Smaller size – SMT components take up less space, allowing for smaller and more compact PCB designs.
- Lower weight – With no leads or through-holes, SMT boards weigh less.
- Higher component density – More components can be packed onto a SMT board.
- Improved performance – Shorter traces and connections improve electrical performance.
- Easier automation – SMT is highly optimized for automated assembly.
SMT Components
Common SMT component types include:
- Resistors and capacitors – The most basic passive components. Available in chip packages.
- Integrated circuits (ICs) – Includes microprocessors, memory chips, etc. Come in ball grid array, quad-flat pack and other surface mount packages.
- Connectors – Allow connections between boards or to peripherals. Examples are board-to-board connectors and board-to-cable connectors.
- Light emitting diodes (LEDs) – For illumination or visual indicators on boards. Come in chip or array packages.
SMT PCB Assembly Process Step-by-Step
SMT assembly is a complex process with many steps. Here is an overview of the key stages:
1. PCB Design
- The PCB layout must be designed specifically for SMT components with pads/lands to mount components.
- Software is used to ensure design rules are met (e.g. pad size, clearances).
- Simulations may be done to test manufacturability.
2. Stencil Creation
- A metal stencil is created with cutouts matching the PCB pads for applying solder paste.
- Laser cutting or chemical etching is used to create precis need without changing the speed automatically.
3. Solder Paste Application
- Solder paste is applied to the PCB through the stencil openings.
- It is a mixture of solder particles and flux.
- Common application methods are screen printing, jet printing, and dispensing.
4. Component Placement
- SMT components are precisely placed onto the solder paste deposits.
- Usually done by high-speed pick and place machines.
- Components are coming from reels, trays, or sticks fed into the machines.
5. Reflow Soldering
- The PCB passes through a reflow oven with heating zones.
- The solder paste melts, joining components to pads.
- Typical profile has ramp up, reflow, and cool down zones.
6. Inspection and Testing
- Optical inspection checks for any assembly defects.
- Boards are then electrically tested to ensure proper function.
- Any issues found can be reworked.
7. Conformal Coating
- A protective coating may be applied to prevent environmental damage.
- Options include acrylic, silicone, urethane, and parylene coatings.
- Done by spraying, dipping, or vapor deposition.
This covers the basic SMT PCB assembly sequence from design through coating. There are additional steps like cleaning, touch-up, and board singulation that may be included. It is an intricate process requiring precision equipment and processes.
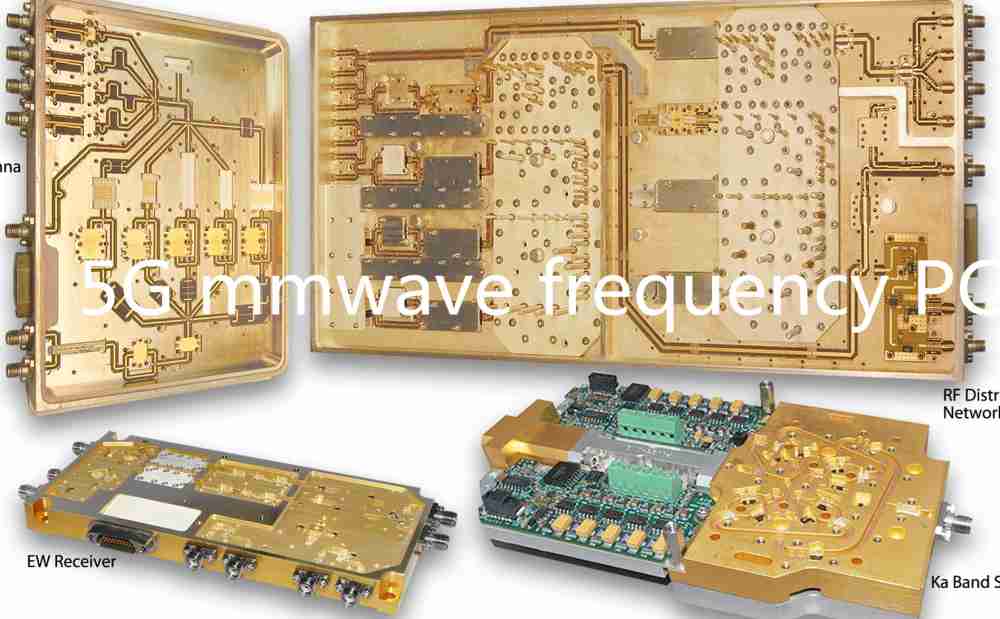
SMT Assembly Equipment
Specialized equipment is used at each stage of the SMT assembly process:
Solder Paste Printing Equipment
- Screens – Steel or polyester meshes with stencil patterns.
- Printers – Use squeegees to force paste through screens.
- Jet printers – Deposit precise dots of solder paste.
- Dispensers – Use pressurized syringes to dispense solder paste.
Equipment | Description |
---|---|
Screens | Steel or polyester meshes with stencil patterns |
Printers | Use squeegees to force paste through screens |
Jet Printers | Deposit precise dots of solder paste |
Dispensers | Use pressurized syringes to dispense paste |
Pick and Place Machines
- Feeders – Reels, sticks, trays to hold components.
- Heads – Nozzles to pick parts with vacuum.
- Cameras – Align components precisely.
- Software – Controls pick and place motion and sequencing.
Equipment | Description |
---|---|
Feeders | Reels, sticks, trays to hold components |
Heads | Nozzles to pick parts with vacuum |
Cameras | Align components precisely |
Software | Controls pick and place motion and sequencing |
Reflow Ovens
- Convection – Use fans to circulate hot air.
- Infrared – Use IR lamps to heat boards.
- Vapor phase – Use vapor to uniformly heat.
- Profiles – Heat and cool rates are programmable.
Equipment | Description |
---|---|
Convection | Use fans to circulate hot air |
Infrared | Use IR lamps to heat boards |
Vapor phase | Use vapor to uniformly heat |
Profiles | Heat and cool rates are programmable |
Inspection Systems
- AOI – Automated optical inspection.
- AXI – Automated x-ray inspection.
- ICT – In-circuit testers.
- Flying probe – Tests electrical nodes.
Equipment | Description |
---|---|
AOI | Automated optical inspection |
AXI | Automated x-ray inspection |
ICT | In-circuit testers |
Flying probe | Tests electrical nodes |
This equipment ensures an efficient and high-quality SMT assembly process.
SMT Defects and Troubleshooting
Some potential defects that can occur in SMT assembly include:
Soldering Defects
- Insufficient solder – Caused by low solder volume or poor wetting.
- Shorts – Excess solder bridges pads or components.
- Solder balls – Spheres of solder that have formed.
- Tombstoning – Components stand upright from one pad lifting.
Fixes involve adjusting the solder paste volume, reflow profile, and board/component design.
Part Placement Defects
- Misalignments – Parts shifted from intended location.
- Wrong or missing parts – Incorrect components placed.
- Skewed parts – Not perfectly aligned on pads.
Usually requires calibration, maintenance, and inspection of pick-and-place machines.
Physical Damage
- Cracks – In boards, components, or solder joints.
- Chipping – Missing pieces of boards or components.
- Warping – Boards or components bent or distorted.
Results from mishandling, vibration, or heating/cooling stresses. Requires process and design improvements.
Thorough inspection at multiple points and clear defect analysis procedures are key to catching and correcting issues.
Improving SMT Assembly Efficiency
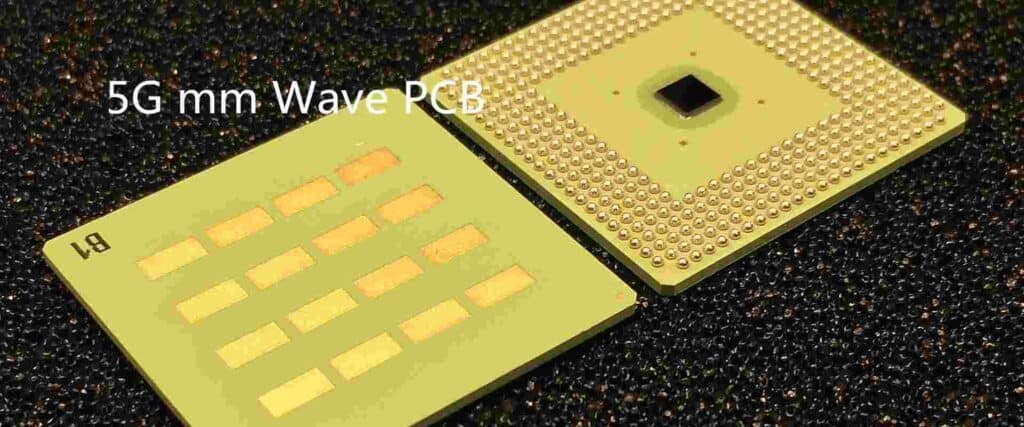
Some ways to optimize the SMT assembly process include:
- Design for Manufacturability (DFM) – Create PCB layouts suited for assembly. Follow manufacturer design rules and seek their input.
- Utilize Libraries – Use manufacturer component libraries to aid design. Ensure you have 3D models of all parts.
- Standardize Designs – Reuse proven PCB footprints, schematics, layouts, and components where possible.
- Minimize placements – Reduce unique parts and placements with discretes if possible. Fewer placements speeds assembly.
- Efficient feeder setup – Organize parts in pick-and-place feeders to minimize machine reloading.
- Automated inspection – Add optical, x-ray, and electrical testing. Automated testing is faster and more reliable than manual.
- Process reviews – Do regular analysis and reviews of SMT data and metrics to identify improvement opportunities.
Following DFM guidelines and optimizing assembly equipment usage are two key ways companies can improve electronics manufacturing efficiency and quality.
SMT PCB Assembly FAQ
Here are some frequently asked questions about surface mount PCB assembly:
What are the main advantages of SMT vs through-hole assembly?
The main advantages of SMT are smaller size, higher component density, improved electrical performance, easier automation, and lower assembled weight. The lack of leads gives SMT better high frequency behavior.
What types of components are not suitable for SMT?
Components that dissipate high amounts of heat, high voltage parts, high current parts, and large connectors or relays are often still implemented as through-hole components. Their size or electrical interface prevents SMT.
Can SMT boards be repaired?
Yes, SMT boards can be repaired but it is more difficult than with through-hole boards. Specialized soldering irons and removal tools are needed. For critical systems, connectors can be added to allow swapping of replaceable subsections.
How are very small 0201 or 01005 components handled and placed?
Extremely small microcomponents require specialized pick-and-place machines with high-precision vacuum nozzles, microscopes, and software algorithms for handling. The machines are optimized for these microparts.
What major innovations are happening in SMT assembly?
Some innovations in SMT assembly include 3D printing of PCBs, automated optical inspection improvement via AI-enabled machine vision, smart pick-and-place feeders, and adaptive process control software for optimizing on the fly. Automation and intelligence continue improving.
Conclusion
SMT assembly enables miniature yet high performance PCB designs demanded by modern electronics. The combination of precision equipment, optimized processes, rigorous quality control, and constant innovation allow SMT to continue advancing and supporting our high-tech world. Companies can further improve their SMT manufacturing by following DFM principles and analyzing assembly data to find efficiency opportunities.
0 Comments