What is SMT Assembly and Why is it Important for PCBs?
Surface-mount technology (SMT) is a method for producing electronic circuits in which the components are mounted directly onto the surface of printed circuit boards (PCBs). An electronic device so made is called a surface-mount device (SMD). In industry, this approach has largely replaced the through-hole technology construction method of fitting components, in large part because SMT allows for increased manufacturing automation which reduces cost and improves quality. It also allows for more components to fit on a given area of substrate. Ultimately, SMT assembly is crucial in manufacturing PCBs for most modern electronics.
Key Advantages of SMT over Through-Hole PCB assembly
Advantage | Description |
---|---|
Smaller Components | SMDs are usually smaller than through-hole components, allowing for higher circuit densities. |
Faster Assembly | Pick-and-place machines can place SMDs extremely quickly, speeding up the assembly process. |
Lower Cost | The increased automation and faster assembly times lead to lower per-unit costs for high volume production. |
Double-Sided Placement | SMDs can be placed on both sides of the PCB, allowing for more compact designs. |
The 9 Key Things to Know About SMT PCB Assembly
1. Understanding the SMT Assembly Process Flow
The typical SMT assembly process follows these key steps:
1. Solder Paste Printing: Solder paste is applied to the PCB pads using a stencil.
2. Pick and Place: The SMT components are picked up and placed onto their designated locations on the PCB by pick-and-place machines.
3. Reflow Soldering: The PCB goes through a reflow oven, which melts the solder paste, permanently attaching the components to the PCB.
4. Inspection: The assembled PCB is inspected, usually via automated optical inspection (AOI), to ensure components are correctly placed and soldered.
5. Through-Hole Component Insertion (if needed): If the design includes through-hole components, these are inserted after SMT process.
6. Final Soldering: If through-hole components are used, the PCB goes through a wave soldering machine to solder these components.
7. Final Inspection and Test: The completed PCB goes through final quality checks and functional tests before being shipped.
2. Designing for SMT Manufacturability
To ensure your PCB is optimized for SMT assembly, consider these design guidelines:
– Adhere to your manufacturer’s design rules regarding minimum pitch, pad sizes, etc.
– Avoid placing components too close to the PCB edge.
– Ensure adequate spacing between components for the pick-and-place machine.
– Orient components in the same direction when possible for easier placement.
– Use standardized component sizes and footprints when possible.
3. Choosing the Right Solder Paste
The solder paste is a crucial material in SMT assembly as it forms the electrical and mechanical connection between the component and the PCB. Key considerations when choosing a solder paste include:
– Alloy type (e.g., SnPb, SAC305)
– Particle size and shape
– Flux activity
– Viscosity and printability
– Shelf life and storage requirements
4. Stencil Design for Optimal Paste Printing
The solder paste stencil determines the amount and placement of solder paste on the PCB. An optimal stencil design should:
– Have aperture sizes and shapes that match the PCB pad layout.
– Have appropriate aperture reductions for fine-pitch components.
– Use stepping or multi-level stencils for PCBs with various component heights.
– Include fiducials for alignment.
5. Pick and Place Machine Programming
Modern pick-and-place machines are highly automated but require precise programming. Key aspects include:
– Importing and aligning the PCB and component data.
– Setting up the component feeders and nozzles.
– Optimizing the placement sequence for speed and accuracy.
– Setting up vision systems for fiducial alignment and component inspection.
6. Reflow Soldering Profile Optimization
The reflow soldering process exposes the PCB to a controlled temperature profile to melt the solder and form the joints. The profile must be optimized based on:
– The solder paste specifications.
– The PCB’s thermal mass.
– The components’ heat sensitivity.
– The desired solder joint quality.
A typical reflow profile includes preheat, soak, reflow, and cooling stages.
7. Automated Optical Inspection (AOI)
AOI systems use cameras and image processing to inspect the assembled PCB for defects such as:
– Missing, misaligned, or rotated components.
– Solder bridging, voids, or insufficient solder.
– Lifted leads or tombstoning.
AOI programming involves setting up lighting, camera angles, and image processing parameters to reliably detect potential defects.
8. Rework and Repair Considerations
Despite best efforts, some PCBs may require rework or repair after assembly. Key considerations include:
– Having a rework procedure that minimizes damage to the PCB and surrounding components.
– Using appropriate tools such as hot air rework stations, soldering irons, and extraction tools.
– Cleaning the reworked area of old solder and flux residue.
– Re-inspecting the reworked PCB to ensure defect correction.
9. Quality Control and Traceability
Ensuring consistent quality and traceability is critical in SMT assembly. Key practices include:
– Implementing a robust quality management system.
– Documenting and reviewing process parameters for each assembly run.
– Marking PCBs with unique identifiers for traceability.
– Regularly calibrating and maintaining assembly equipment.
– Conducting ongoing reliability testing and failure analysis.
Frequently Asked Questions (FAQ)
1. What is the difference between SMT and through-hole assembly?
SMT components are mounted directly onto the surface of the PCB, while through-hole components have leads that are inserted into holes drilled in the PCB and soldered on the opposite side. SMT allows for smaller components, higher component density, and faster automated assembly compared to through-hole.
2. Can SMT and through-hole components be used on the same PCB?
Yes, it’s possible to have a mixed assembly with both SMT and through-hole components on the same PCB. In this case, the SMT components are typically assembled first, followed by the insertion and soldering of the through-hole components.
3. What is a BGA component and how is it assembled?
BGA (Ball Grid Array) is a type of SMT package where the component has an array of solder balls on its underside instead of leads. During assembly, the BGA is placed directly onto the corresponding pad array on the PCB and reflowed. Proper alignment and reflow profile control are critical for BGA Assembly success.
4. What is the role of nitrogen in reflow soldering?
Nitrogen is sometimes used in reflow ovens to create an inert atmosphere. This reduces oxidation on the solder joints during the reflow process, which can improve solder joint quality and appearance. Nitrogen can be especially beneficial for lead-free solder processes.
5. How do I select an SMT assembly partner?
When choosing an SMT assembly partner, consider factors such as:
– Their experience with similar projects and PCB complexity.
– Their quality control and traceability processes.
– Their capacity and lead times.
– Their ability to handle your expected volumes.
– Their location and logistics capabilities.
– Their customer service and communication.
It’s also advisable to review their certifications, audit their facilities, and request references from existing customers.
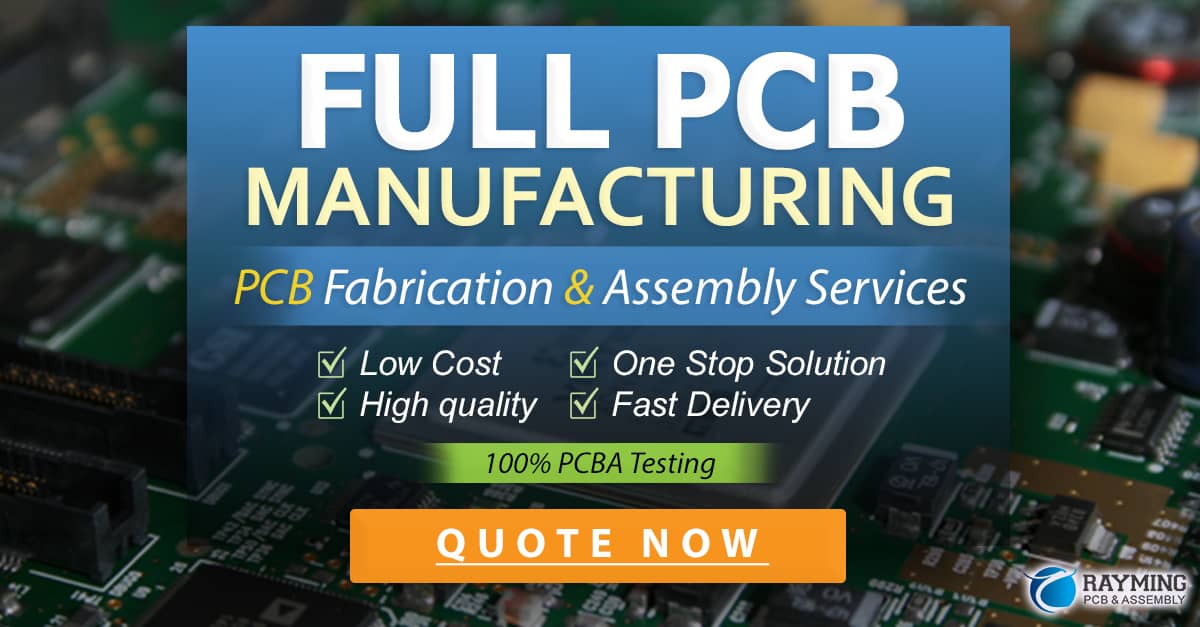
Conclusion
SMT assembly is a complex process with many critical factors to consider, from PCB design to final inspection. By understanding these key aspects, working closely with your assembly partner, and continuously optimizing your process, you can achieve high-quality, reliable PCB assemblies for your products.
0 Comments