What is a Single Layer PCB?
A single layer PCB, also known as a single-sided PCB, has one layer of conductive copper traces on a insulating substrate material like FR-4. All the components and circuits are placed on one side of the board. Single layer PCBs are the simplest and most economical type of PCB.
Advantages of single layer PCBs include:
- Low cost due to simple manufacturing process
- Quick fabrication turnaround time
- Easier to design layout
- Suitable for low complexity circuits
- Ideal for high volume production
However, single layer PCBs also have some limitations:
- Restricted routing space for circuits
- Not suitable for complex or dense designs
- Can have poor EMI performance
- Through hole components can only be placed on one side
Single layer PCBs are commonly used in simple electronics like toys, calculators, flashlights, LED strips, passive filters, and other low density applications. Their low cost makes them ideal for prototyping and high volume manufacturing of simple devices.
What is a Double Layer PCB?
A double layer PCB, also called a double-sided PCB, has two layers of conductive copper, one on each side of the insulating substrate. The two copper layers are connected using conductive vias. Components can be mounted on both sides of the board. Double layer PCBs provide more routing space and design flexibility compared to single layer.
Key advantages of double layer PCBs are:
- Twice the routing area vs single layer
- Supports higher component density
- Better EMI performance with proper grounding plane
- Allows for more complex circuits
- Enables shorter traces between components
- Vias can act as heat dissipation channels
The main trade-offs of double layer PCBs are:
- Higher cost than single layer boards
- More complex manufacturing process
- Longer fabrication time
- More challenging layout and routing
- Requires vias for layer interconnections
Double layer PCBs are used in a wide range of electronic devices that require higher circuit density and performance than single layer boards can provide. Common applications include smartphones, computers, industrial controls, automotive electronics, medical devices, and IoT products.
Factors to Consider When Choosing PCB Layers
So how do you decide between single layer vs double layer for your PCB project? Here are the key factors to evaluate:
Circuit Complexity
The first consideration is the complexity of your circuit design. If your device has a relatively simple circuit with a low number of components, a single layer PCB may be sufficient. However, if your design includes a microcontroller, multiple ICs, or a large number of components, a double layer PCB will likely be necessary to accommodate all the routing traces.
As a general rule of thumb, designs with more than 50 components or ICs with 100+ pins will usually require a double layer PCB. However, this depends on the size of the components and the overall board dimensions.
Size Constraints
The available space for your PCB is another important factor. If you have tight size constraints, a double layer PCB allows you to pack more components and traces into a smaller area by utilizing both sides of the board. With a single layer board, you are limited to placing components on one side only.
However, if space is not a concern and you have a relatively simple circuit, a single layer PCB may be the most cost-effective option. Single layer boards also tend to be thinner than double layer ones.
Cost Considerations
Cost is often a primary driver in choosing between single layer and double layer PCBs. Single layer boards are almost always cheaper than double layer ones due to the simpler manufacturing process.
According to PCBCart, a PCB Prototype manufacturer, the price difference between single and double layer PCBs can be 30-50% or more depending on the specifications. For example, a 10x10cm single layer PCB may cost around $20 while a double layer board of the same size could be $30 or more.
However, it’s important to consider the total cost of your project, not just the PCB fabrication cost. If using a single layer PCB requires a larger board size or additional wiring to make the routing work, it may end up being more expensive overall than using a double layer board in a smaller form factor. The cost of rework and troubleshooting problems in a sub-optimal single layer design can also add up.
For high volume production, the cost difference between single and double layer boards becomes much smaller. It may be worth using double layer boards even for simpler designs if the marginally higher fabrication cost is outweighed by the benefits in reliability, performance or size.
Signal Integrity
For designs with high speed digital signals or sensitive analog circuits, maintaining good signal integrity is critical. Factors like crosstalk, EMI, and ground bounce can degrade signals and cause errors.
Double layer PCBs have an advantage for signal integrity because the second copper layer can be used as a ground plane. Proper grounding is essential for mitigating EMI and ensuring clean power delivery. Having a continuous ground plane on the bottom layer allows return currents to flow unimpeded and minimizes loop areas that can act as antennas.
With a single layer board, the ground connections have to be routed along with the signal traces. This can lead to longer return current paths and greater risk of crosstalk or EMI issues, especially at high frequencies.
The exception is very simple, low frequency analog circuits where a ground plane may not be necessary. In those cases, a single layer board may be acceptable and even preferable to minimize capacitive coupling.
Power and Heat Management
If your design includes high power components like voltage regulators, MOSFETs, or power LEDs, using a double layer PCB can help with power delivery and heat dissipation. The bottom copper layer can be used as a power plane to minimize voltage drop and provide low impedance current paths.
Having conductive vias also allows heat to be conducted from the top to bottom layer and dissipated through the bottom copper pour. This can help prevent hotspots and improve reliability, especially if the bottom layer is exposed to air or attached to a heatsink.
With a single layer board, the copper area for power routing and heatsinking is more limited. This can be an issue for designs with high current draw or tight thermal limits.
Manufacturing Considerations
The capabilities of your PCB fabricator may also influence the choice of layers. Some manufacturers may have higher prices or longer lead times for double layer boards, while others may be well optimized for double layer designs.
It’s worth getting quotes from multiple PCB shops and understanding their design rules and manufacturing limitations. Some fabs may have restrictions on minimum hole size, trace/space width, or via types that could affect your design decisions.
For complex double layer designs, it’s also important to communicate clearly with your fab and assembly partners to ensure the design is manufacturable and avoid issues like drill misregistration or soldermask problems.
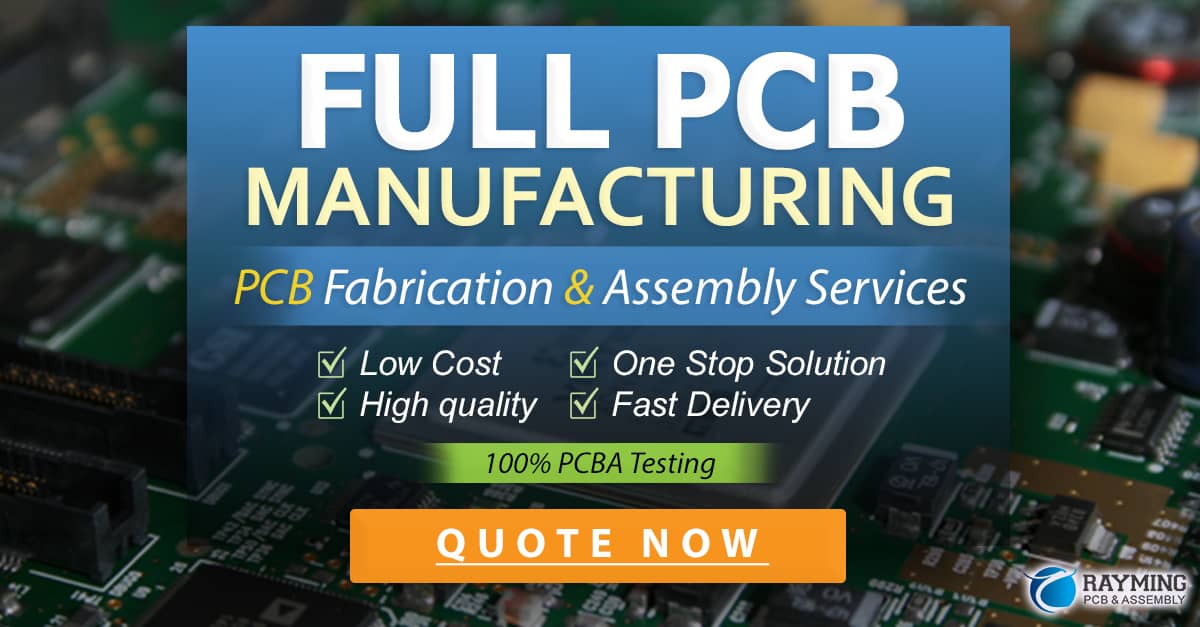
Single Layer vs Double Layer PCB Comparison Table
Here is a summary comparison of single layer and double layer PCBs:
Factor | Single Layer PCB | Double Layer PCB |
---|---|---|
Layers | 1 copper layer | 2 copper layers |
Cost | Lower | Higher |
Complexity | Simpler | More complex |
Density | Lower | Higher |
Routing area | Less | More |
EMI/signal integrity | Worse | Better |
Power/heat management | Limited | Better |
Manufacturing | Simpler | More complex |
Applications | Simple, low density circuits | Complex, high density circuits |
PCB Layers FAQs
1. Can I mix SMT and through-hole components on a single layer PCB?
Yes, you can mix surface mount (SMT) and through-hole components on a single layer board. However, the through-hole component leads will be exposed on the opposite side which may require insulation. Wave soldering through-hole parts can also be more challenging with surface mount parts on the same side.
2. Are there any disadvantages to using double layer PCBs?
The main disadvantages of double layer PCBs are the higher cost and more complex manufacturing process compared to single layer boards. Proper layer alignment and via drilling also requires tighter tolerances. For very simple circuits, a double layer board may be overkill.
3. What is the maximum size possible for a single layer PCB?
In theory, there is no hard limit on the maximum size of a single layer PCB. Some manufacturers can fabricate single layer boards up to 550 x 1500 mm or more. However, very large boards may be more prone to warping and are uncommon for most applications. Yield and handling issues also get worse with increasing size.
4. How do I choose the right copper weight for my PCB?
The copper weight or thickness affects the current carrying capacity and impedance of the traces. Thicker copper allows higher currents and lower resistive losses but adds cost. 1oz (35µm) copper is the most common choice for low power circuits. 2oz (70µm) or more may be used for power electronics. High frequency RF circuits may use 0.5oz or less for controlled impedance.
5. Are there any alternatives to single or double layer PCBs?
For very simple circuits, alternatives like perf board, stripboard, or wire-wrap may be sufficient and lower cost than a custom PCB. At the other end of the spectrum, complex designs may require Multilayer PCBs with 4, 6, 8 or more layers to achieve the necessary density and signal integrity. Rigid-flex circuits are another option for unique packaging requirements.
Conclusion
Choosing between a single layer and double layer PCB is an important design decision that affects cost, complexity, performance, and manufacturability. Single layer PCBs offer simplicity and lower cost but have limitations in terms of routing density and signal integrity. Double layer PCBs provide more flexibility and better EMI performance but come with higher cost and manufacturing complexity.
To make the right choice, consider key factors like your circuit complexity, size constraints, cost targets, signal integrity requirements, and power/thermal needs. When in doubt, consult with your PCB manufacturing partner for their recommendations and capabilities.
By understanding the trade-offs and choosing the appropriate number of PCB layers for your project, you can optimize your design for cost, reliability, and performance. At the end of the day, the right choice depends on your specific application and requirements.
0 Comments