Printed circuit boards (PCBs) are essential components in nearly all modern electronic devices. Prototype PCBs allow engineers to test new circuit designs and functionality before finalizing a design for mass production. This article provides an overview of considerations and best practices for assembling prototype PCBs.
Design File Preparation
Before assembly can begin, the PCB design files must be finalized and validated. This includes:
Schematics
- Ensure the schematic is complete with all required components for the design.
- Run an electrical rules check to catch any errors.
- Have the schematic reviewed by a second engineer.
PCB Layout
- Confirm the PCB layout matches the schematic.
- Verify clearances and spacings meet requirements.
- Run a design rule check to catch any errors.
- Have the board layout reviewed by a second engineer.
Gerber Files
- Export the Gerber design files needed for PCB fabrication and assembly.
- Carefully check all layers against the design.
- Ensure the Gerber files meet fabrication requirements.
Prototype PCB Fabrication
There are several options for obtaining prototype PCBs:
- In-house fabrication for fast turnaround but requires capital equipment investment
- Outsourcing to a PCB prototype shop for lower volumes
- Batching multiple designs to take advantage of PCB assembly services
Factors to consider when choosing a PCB fabrication method:
- Lead time
- Cost per board
- Minimum order quantity
- Maximum board size
- Available materials and layers
- Impedance control requirements
- Other special fabrication needs
Component Selection
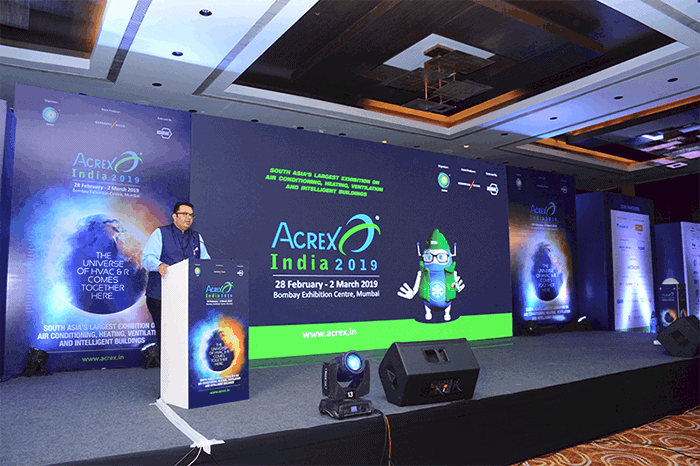
Selecting the right components is critical for a successful prototype build.
Component Sources
- Preferred part numbers – choose parts already proven and readily available
- Manufacturer inventory – leverage existing stock
- Digikey, Mouser, Avnet, Arrow – major electronics distributors
- Find “equivalent” substitutes – match key parameters if preferred parts not available
Bill of Materials
- Create detailed bill of materials with part numbers, descriptions, quantities
- Include component specifications – tolerance, rating, packaging etc.
- Assign reference designators matching schematic
Managing Inventory
- Order sufficient quantities to support builds and potential rework
- Consider long lead time parts – order early or find substitutes
- Store components properly for moisture sensitivity, electrostatic discharge etc.
PCB Assembly Process
Assembly of the PCB involves soldering components onto the fabricated board.
Equipment
- Soldering iron – for manual soldering or rework
- Reflow oven – for solder paste and SMT components
- Inspection microscope – confirms quality solder joints
- Multimeter – verifies connections between points
Materials
- Solder paste – for SMT components
- Solder wire – for leaded components
- Flux – promotes solder flow and wetting
- Isopropyl alcohol – cleans flux residue
Assembly Steps
- Start with larger components first – sockets, connectors
- Install sensitive components next – ICs, any shielding
- Add remaining smaller components
- Reflow solder paste connections
- Hand solder any through-hole components
- Clean assemble board of flux residue
- Comprehensive visual inspection at multiple magnifications
Testing and Verification
Thoroughly testing a prototype PCB is crucial to identify any issues and confirm the design functions as intended before committing to production.
Pre-Power Checks
- Inspect for correct components placements and polarity
- Verify quality solder joints and no shorts
- Check for loose wires or debris
- Confirm programmed firmware/software
Power-On Testing
- Apply power incrementally, monitoring current draw
- Check outputs and functionality at each stage
- Troubleshoot any issues found
- Verify performance across operating conditions
Repeat Builds
- Reproduce additional boards for comprehensive testing
- Check consistency across multiple boards
- Confirm the process yields a robust, working design
Documentation
Maintaining detailed documentation is key for reproducing quality results.
- BOM, schematics, assembly drawings, and test procedures
- Photographs at each assembly stage
- Notes for any rework or modifications
- Test data logs and reports
- Issues encountered and solutions
Thorough design, assembly, and testing documentation reduces errors and speeds up future iterations.
Prototype to Production
If the prototype evaluation is successful, the following tasks help transition the design from prototype to production release.
- Design for Manufacturing analysis – identify any needed changes to support volume production
- Apply for certifications – FCC, UL, CE, etc.
- Complete qualification and reliability testing – meets standards and environment needs
- Finalize test specifications – for both incoming component inspection and finished product
- Determine packaging and labeling requirements
- Initiate sourcing for production components, PCBs, and enclosures
With careful planning, a quality prototype build paves the way for moving into full scale production.
Frequently Asked Questions
What are some key considerations for assembling a prototype PCB?
Some of the most important considerations are:
- Ensure the design files are complete and validated before starting assembly
- Select components carefully to match the BOM and availability
- Use the right PCB fabrication source to meet cost, speed and capability needs
- Follow a step-by-step assembly and soldering process for consistency
- Execute comprehensive testing to verify the design works as intended
- Document details at each step to aid future debugging and replication
What equipment is typically required?
At minimum, assembling prototype boards requires the following equipment:
- Soldering iron and accessories for hand soldering
- Inspection microscope for verifying solder joint quality
- Multimeter for basic connectivity and voltage testing
- Reflow oven for soldering SMT components
- Applicable programming and debugging tools
For more complex designs, additional test equipment like oscilloscopes, function generators, and spectrum analyzers may be necessary.
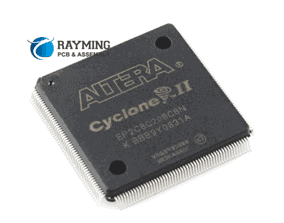
What defects should be looked for when inspecting solder joints?
Common solder joint defects to look for include:
- Insufficient solder – causing intermittent connections
- Cold solder joints – exhibiting a dull gray, porous appearance
- Cracked solder joints – gaps in the solder indicate a poor bond
- Solder bridges – solder overflowing and shorting adjacent joints
- Solder balls – spheres of solder indicating dripping
- PCB delamination or burn marks – from overheating during soldering
How many boards should be built for prototype testing?
As budgets allow, building 3-5 boards is recommended to provide enough samples for robust testing. This allows engineers to check for consistency across boards and have spare boards for experiments. Building a single prototype board risks being left with no working board if it gets damaged during handling or testing.
When does it make sense to outsource PCB assembly?
For low-to-medium complexity boards, assembling in-house provides maximum control and flexibility for prototyping. Outsourcing assembly services can save time for engineers and makes more economic sense at higher volumes or for highly dense, complex boards requiring specialized equipment.
0 Comments