What is PCB Troubleshooting?
PCB troubleshooting is the process of identifying, diagnosing, and resolving issues or malfunctions in printed circuit boards (PCBs). It involves a systematic approach to pinpoint the root cause of the problem and implement appropriate solutions to restore the PCB’s functionality. PCB troubleshooting is a critical skill for electronics engineers, technicians, and hobbyists to ensure the proper operation of electronic devices and systems.
Common PCB Issues
PCBs can encounter various issues during manufacturing, assembly, or operation. Some of the most common PCB problems include:
- Short circuits
- Open circuits
- Component failure
- Solder joint defects
- Incorrect component placement
- Damaged or broken traces
- Contamination or corrosion
- Overheating
- Electromagnetic interference (EMI)
- Vibration or mechanical stress
Why is PCB Troubleshooting Important?
PCB troubleshooting is essential for several reasons:
1. Ensuring Proper Functionality
The primary goal of PCB troubleshooting is to ensure that the PCB functions as intended. By identifying and resolving issues, you can restore the PCB’s performance and prevent further malfunctions.
2. Reducing Downtime
In industrial settings or critical applications, PCB Failures can lead to significant downtime and productivity losses. Effective troubleshooting minimizes the duration of downtime by quickly identifying and resolving issues.
3. Cost Savings
Unresolved PCB issues can lead to expensive repairs or replacements. By troubleshooting and fixing problems early on, you can avoid costly damage and prolong the lifespan of the PCB.
4. Quality Assurance
PCB troubleshooting is an integral part of quality assurance processes. It helps identify manufacturing defects, design flaws, or component quality issues, allowing for continuous improvement in PCB Production and assembly.
5. Skill Development
Engaging in PCB troubleshooting enhances technical skills and knowledge. It provides hands-on experience in problem-solving, circuit analysis, and component testing, which are valuable skills for electronics professionals.
PCB Troubleshooting Process
The PCB troubleshooting process typically follows these steps:
-
Visual Inspection: Begin by visually examining the PCB for any obvious defects, such as damaged components, broken traces, or solder joint issues.
-
Symptom Analysis: Identify the specific symptoms or malfunctions exhibited by the PCB. This may include power issues, signal integrity problems, or erratic behavior.
-
Schematic Review: Study the PCB schematic to understand the circuit design and identify potential areas of concern based on the observed symptoms.
-
Power Supply Check: Verify that the PCB is receiving the correct power supply voltages and currents. Check for any shorts or excessive current draw.
-
Signal Tracing: Use oscilloscopes or logic analyzers to trace signals through the PCB and identify any abnormalities or deviations from expected behavior.
-
Component Testing: Test individual components, such as resistors, capacitors, and ICs, to verify their functionality and rule out component failure.
-
Isolation Techniques: Employ isolation techniques, such as cutting traces or removing components, to narrow down the problem area and pinpoint the root cause.
-
Repair and Rework: Once the issue is identified, perform necessary repairs or rework, such as replacing faulty components or resoldering joints.
-
Verification: After repairs, thoroughly test the PCB to ensure that the issue has been resolved and the PCB functions as intended.
PCB Troubleshooting Tools
To effectively troubleshoot PCBs, you’ll need a set of essential tools:
Tool | Purpose |
---|---|
Multimeter | Measure voltage, current, resistance, and continuity |
Oscilloscope | Analyze waveforms and signal integrity |
Logic Analyzer | Capture and analyze digital signals |
Soldering Iron | Perform soldering and desoldering tasks |
Desoldering Tools | Remove components or solder for rework |
Magnifying Lens | Visually inspect small components and solder joints |
ESD-safe Workstation | Protect sensitive components from electrostatic discharge |
Thermal Imaging Camera | Identify overheating components or thermal issues |
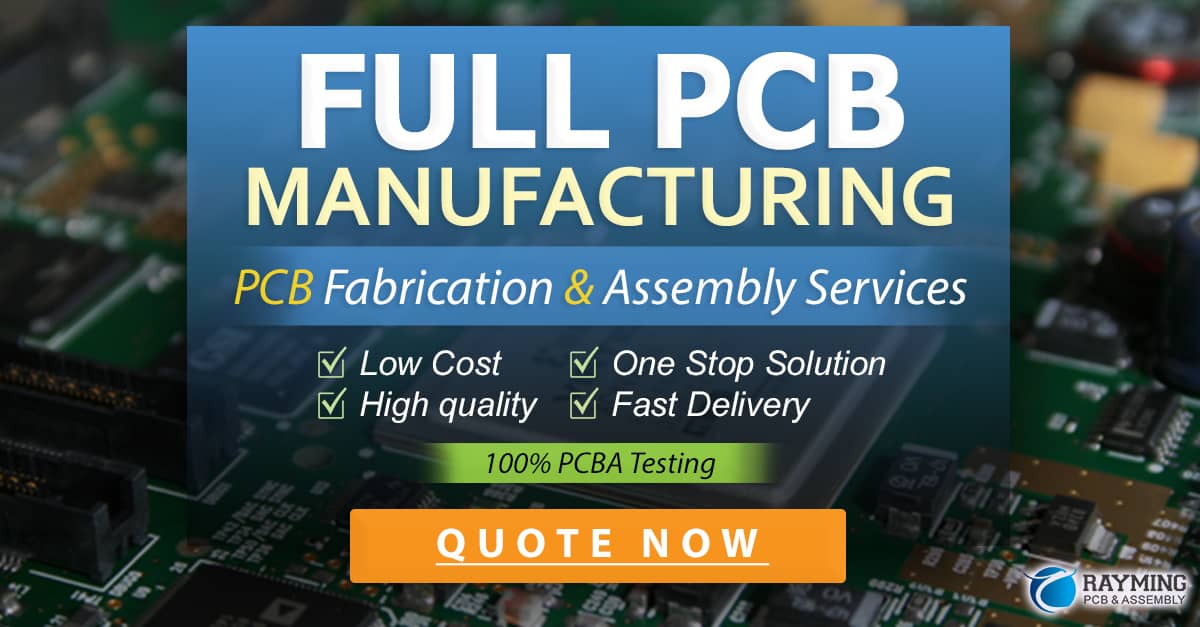
Common PCB Troubleshooting Techniques
Here are some common techniques used in PCB troubleshooting:
1. Continuity Testing
Continuity testing involves checking for electrical connectivity between two points on the PCB. It helps identify short circuits, open circuits, or poor connections. Use a multimeter set to continuity mode to perform this test.
2. Voltage Measurement
Voltage measurement is crucial for verifying the proper functioning of power supply rails and signal levels. Use a multimeter or oscilloscope to measure voltages at various test points on the PCB and compare them with the expected values.
3. Current Measurement
Current measurement helps identify excessive current draw or short circuits. Use a current probe or a multimeter with a current-sensing capability to measure the current flowing through specific components or traces.
4. Signal Tracing
Signal tracing involves following the path of a signal through the PCB to identify any distortions, reflections, or noise. Use an oscilloscope to capture and analyze waveforms at different test points along the signal path.
5. Thermal Analysis
Thermal analysis helps identify overheating components or areas on the PCB. Use a thermal imaging camera or temperature probe to measure the temperature of components and compare it with their specified operating range.
6. X-ray Inspection
X-ray inspection is useful for examining hidden or obscured solder joints, such as those in ball grid array (BGA) packages. It allows you to detect solder joint defects, voids, or bridging that may not be visible through visual inspection.
PCB Troubleshooting Case Studies
Let’s explore a few real-world examples of PCB troubleshooting:
Case Study 1: Power Supply Failure
Problem: A PCB-based power supply unit fails to provide the expected output voltage.
Troubleshooting Steps:
1. Check the input voltage to ensure it is within the specified range.
2. Verify the continuity of the power supply’s input and output connections.
3. Measure the voltages at key points in the power supply circuit, such as the Voltage Regulator input and output.
4. Inspect the voltage regulator and associated components for any signs of damage or overheating.
5. Replace any faulty components and retest the power supply.
Resolution: The voltage regulator was found to be damaged due to a voltage spike. Replacing the voltage regulator restored the power supply’s functionality.
Case Study 2: Intermittent Signal Issues
Problem: A PCB experiences intermittent signal integrity issues, resulting in erratic behavior.
Troubleshooting Steps:
1. Visually inspect the PCB for any damaged or loose connections.
2. Use an oscilloscope to capture the problematic signal waveforms.
3. Analyze the waveforms for any abnormalities, such as ringing, overshoot, or reflections.
4. Check the PCB layout for any potential signal integrity issues, such as improper termination or crosstalk.
5. Rework the affected traces or add necessary termination components.
Resolution: The issue was traced to a poorly terminated high-speed signal line. Adding proper termination resistors resolved the intermittent signal problems.
Case Study 3: Component Failure
Problem: A specific component on the PCB consistently fails after a short period of operation.
Troubleshooting Steps:
1. Identify the failing component and its characteristics.
2. Check the component’s datasheet for any specific operating requirements or limitations.
3. Measure the voltage, current, and temperature of the component during operation.
4. Analyze the PCB layout and component placement for any potential stress factors.
5. Consider alternative components with better specifications or higher reliability.
Resolution: The failing component was found to be operating beyond its rated temperature range due to inadequate heat dissipation. Replacing the component with a higher-rated alternative and improving the PCB’s thermal management resolved the issue.
Frequently Asked Questions (FAQ)
-
What are the most common causes of PCB failures?
Some of the most common causes of PCB failures include component defects, manufacturing issues, improper handling, environmental factors (such as moisture or temperature extremes), and design flaws. -
How can I prevent PCB failures?
To prevent PCB failures, follow best practices in PCB design, manufacturing, and assembly. This includes using high-quality components, adhering to design guidelines, implementing proper handling and storage procedures, and conducting thorough testing and quality control. -
What should I do if I suspect a component failure on a PCB?
If you suspect a component failure, start by visually inspecting the component for any signs of damage or abnormalities. Use a multimeter to test the component’s functionality and compare it with the expected values. If the component is confirmed to be faulty, replace it with a known good component and retest the PCB. -
How can I troubleshoot PCB issues related to electromagnetic interference (EMI)?
To troubleshoot EMI issues, use an oscilloscope or spectrum analyzer to identify the frequency and source of the interference. Check for proper grounding, shielding, and decoupling techniques in the PCB design. Consider adding EMI filters, ferrite beads, or shielding materials to mitigate the interference. -
What safety precautions should I take when troubleshooting PCBs?
When troubleshooting PCBs, always prioritize safety. Wear protective gear, such as ESD-safe gloves and wrist straps, to prevent electrostatic discharge damage. Be cautious when handling high-voltage or high-current circuits. Follow proper handling procedures for hazardous materials, such as lead-based solder. Ensure adequate ventilation when working with solvents or fumes.
Conclusion
PCB troubleshooting is a critical skill for anyone involved in electronics design, manufacturing, or maintenance. By understanding the common issues, employing systematic troubleshooting techniques, and utilizing the right tools, you can effectively identify and resolve PCB problems. Regular training, practice, and staying updated with the latest technologies will enhance your PCB troubleshooting abilities.
Remember, prevention is always better than cure. Investing in robust PCB design, quality components, and thorough testing can minimize the occurrence of PCB issues in the first place. However, when problems do arise, a structured troubleshooting approach and a keen eye for detail will be your greatest assets in restoring the functionality of your PCBs.
0 Comments