Introduction
Printed Circuit Board (PCB) assembly is a complex process that involves various steps, materials, and components. Despite the advancements in technology and manufacturing processes, PCB Assembly failures can still occur, leading to costly repairs, product delays, and customer dissatisfaction. In this article, we will discuss nine common PCB assembly failures and their prevention methods to help manufacturers and designers minimize the risk of these issues.
1. Solder Bridges
What are Solder Bridges?
Solder bridges are a common PCB assembly failure that occurs when excess solder creates an unintended connection between two or more adjacent pads or traces. This can lead to short circuits, improper functioning, and potential damage to the PCB or its components.
Causes of Solder Bridges
- Excessive solder paste application
- Improper solder paste stencil design
- Incorrect reflow oven temperature profile
- Poor component placement accuracy
Prevention Methods
- Optimize solder paste stencil design to ensure proper solder paste volume and placement.
- Regularly inspect and maintain solder paste printing equipment to ensure consistent paste deposition.
- Implement a robust reflow oven temperature profiling process to achieve optimal solder joint formation.
- Utilize automated component placement systems with high accuracy to minimize the risk of misaligned components.
2. Cold Solder Joints
What are Cold Solder Joints?
Cold solder joints occur when the solder fails to melt and flow properly during the reflow process, resulting in a weak, brittle, or incomplete connection between the component and the PCB pad.
Causes of Cold Solder Joints
- Insufficient solder paste volume
- Incorrect reflow oven temperature profile
- Contaminated or oxidized component leads or PCB pads
- Poor component placement accuracy
Prevention Methods
- Ensure adequate solder paste volume through proper stencil design and regular printing equipment maintenance.
- Implement a robust reflow oven temperature profiling process to achieve optimal solder joint formation.
- Maintain a clean manufacturing environment and use appropriate cleaning methods to remove contaminants from component leads and PCB pads.
- Utilize automated component placement systems with high accuracy to minimize the risk of misaligned components.
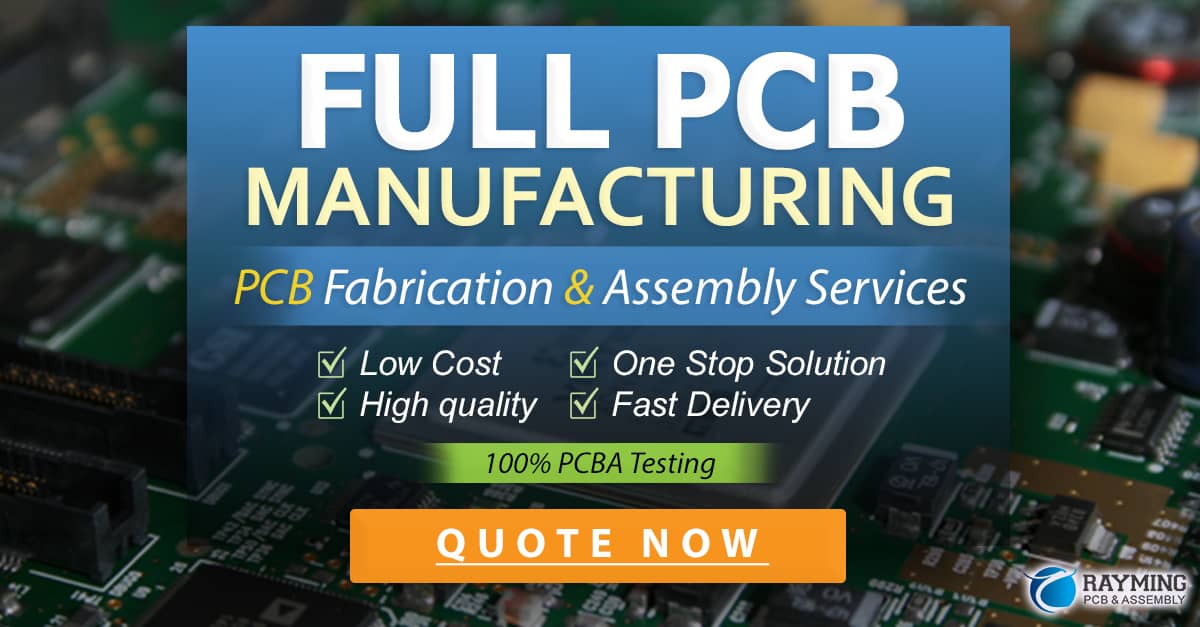
3. Tombstoning
What is Tombstoning?
Tombstoning, also known as “drawbridging,” is a PCB assembly failure that occurs when a surface-mounted component (SMD) lifts up on one end during the reflow process, resulting in an open circuit or poor connection.
Causes of Tombstoning
- Uneven solder paste deposition
- Incorrect component placement
- Imbalanced solder joint surface tension
- Rapid heating or cooling during the reflow process
Prevention Methods
- Optimize solder paste stencil design to ensure even solder paste deposition on component pads.
- Utilize automated component placement systems with high accuracy to minimize the risk of misaligned components.
- Design component pads with balanced copper distribution to promote even solder joint formation.
- Implement a controlled reflow oven temperature profile with appropriate ramp rates and dwell times.
4. Insufficient Solder
What is Insufficient Solder?
Insufficient solder is a PCB assembly failure that occurs when there is not enough solder to create a strong, reliable connection between the component and the PCB pad, leading to weak joints and potential open circuits.
Causes of Insufficient Solder
- Inadequate solder paste volume
- Incorrect solder paste stencil design
- Poor solder paste printing process control
- Contaminated or oxidized component leads or PCB pads
Prevention Methods
- Optimize solder paste stencil design to ensure proper solder paste volume and placement.
- Regularly inspect and maintain solder paste printing equipment to ensure consistent paste deposition.
- Implement a robust quality control process to monitor solder paste volume and printing consistency.
- Maintain a clean manufacturing environment and use appropriate cleaning methods to remove contaminants from component leads and PCB pads.
5. Solder Balls
What are Solder Balls?
Solder balls are small, spherical balls of solder that can form on the PCB surface during the reflow process. They can cause short circuits, interfere with the proper functioning of the PCB, and lead to reliability issues.
Causes of Solder Balls
- Excessive solder paste volume
- Incorrect reflow oven temperature profile
- Contamination or impurities in the solder paste
- Poor solder mask design or application
Prevention Methods
- Optimize solder paste stencil design to ensure proper solder paste volume and placement.
- Implement a robust reflow oven temperature profiling process to achieve optimal solder joint formation and minimize solder splatter.
- Use high-quality solder paste with minimal impurities and contaminants.
- Ensure proper solder mask design and application to prevent solder from spreading beyond the desired areas.
6. Lifted Pads
What are Lifted Pads?
Lifted pads occur when the copper pad on the PCB separates from the substrate material during the assembly process, often due to excessive mechanical stress or improper bonding between the pad and the substrate.
Causes of Lifted Pads
- Excessive mechanical stress during component placement or soldering
- Poor adhesion between the copper pad and the PCB substrate
- Incorrect reflow oven temperature profile
- Contamination or moisture on the PCB surface
Prevention Methods
- Ensure proper PCB design with adequate pad size and copper thickness to withstand mechanical stress.
- Implement a controlled component placement process to minimize mechanical stress on the pads.
- Maintain a clean and dry manufacturing environment to prevent contamination and moisture-related issues.
- Utilize a robust reflow oven temperature profiling process to achieve optimal solder joint formation without excessive heat stress.
7. Component Shifting
What is Component Shifting?
Component shifting is a PCB assembly failure that occurs when components move from their intended position during the reflow process, leading to misalignment, poor connections, and potential short circuits.
Causes of Component Shifting
- Incorrect solder paste volume or placement
- Improper component placement
- Excessive vibration or movement during the reflow process
- Incorrect reflow oven temperature profile
Prevention Methods
- Optimize solder paste stencil design to ensure proper solder paste volume and placement.
- Utilize automated component placement systems with high accuracy to minimize the risk of misaligned components.
- Implement a stable and vibration-free reflow oven system to prevent component movement during the soldering process.
- Ensure a well-designed reflow oven temperature profile to achieve optimal solder joint formation without excessive heat or cooling rates.
8. Electrostatic Discharge (ESD) Damage
What is ESD Damage?
ESD damage occurs when static electricity discharges through sensitive electronic components, causing permanent damage or latent defects that can lead to premature failure.
Causes of ESD Damage
- Improper handling of sensitive components
- Inadequate ESD protection measures in the manufacturing environment
- Insufficient grounding of personnel and equipment
- Use of non-ESD-safe materials and tools
Prevention Methods
- Implement a comprehensive ESD protection program, including ESD-safe workstations, flooring, and storage solutions.
- Train personnel on proper ESD-safe handling techniques and best practices.
- Use ESD-safe materials, tools, and packaging throughout the manufacturing process.
- Regularly audit and maintain ESD protection measures to ensure ongoing effectiveness.
9. Flux Residue
What is Flux Residue?
Flux residue is the remaining contaminants left on the PCB surface after the soldering process. If not properly cleaned, flux residue can lead to corrosion, electrical leakage, and long-term reliability issues.
Causes of Flux Residue
- Incomplete cleaning process after soldering
- Use of inappropriate cleaning agents or methods
- Insufficient cleaning time or agitation
- Improper selection of flux or solder paste
Prevention Methods
- Select appropriate flux and solder paste for the specific application and cleaning process.
- Implement a thorough cleaning process using suitable cleaning agents and equipment.
- Ensure adequate cleaning time and agitation to effectively remove all flux residues.
- Regularly monitor the cleaning process effectiveness and make adjustments as necessary.
PCB Assembly Failure Prevention Summary
Failure Mode | Key Prevention Methods |
---|---|
Solder Bridges | – Optimize solder paste stencil design – Regularly maintain printing equipment – Implement robust reflow oven temperature profiling – Utilize high-accuracy component placement systems |
Cold Solder Joints | – Ensure adequate solder paste volume – Implement robust reflow oven temperature profiling – Maintain a clean manufacturing environment – Utilize high-accuracy component placement systems |
Tombstoning | – Optimize solder paste stencil design – Utilize high-accuracy component placement systems – Design balanced component pad copper distribution – Implement controlled reflow oven temperature profile |
Insufficient Solder | – Optimize solder paste stencil design – Regularly maintain printing equipment – Implement robust quality control process – Maintain a clean manufacturing environment |
Solder Balls | – Optimize solder paste stencil design – Implement robust reflow oven temperature profiling – Use high-quality solder paste – Ensure proper solder mask design and application |
Lifted Pads | – Ensure proper PCB design – Implement controlled component placement process – Maintain a clean and dry manufacturing environment – Utilize robust reflow oven temperature profiling |
Component Shifting | – Optimize solder paste stencil design – Utilize high-accuracy component placement systems – Implement stable and vibration-free reflow oven system – Ensure well-designed reflow oven temperature profile |
ESD Damage | – Implement comprehensive ESD protection program – Train personnel on ESD-safe handling techniques – Use ESD-safe materials, tools, and packaging – Regularly audit and maintain ESD protection measures |
Flux Residue | – Select appropriate flux and solder paste – Implement thorough cleaning process – Ensure adequate cleaning time and agitation – Regularly monitor cleaning process effectiveness |
Frequently Asked Questions (FAQ)
-
Q: What is the most common PCB assembly failure?
A: Solder bridges are one of the most common PCB assembly failures, often caused by excessive solder paste application, improper stencil design, or incorrect reflow oven temperature profiles. -
Q: How can I prevent tombstoning during the PCB assembly process?
A: To prevent tombstoning, optimize your solder paste stencil design for even paste deposition, use high-accuracy component placement systems, design component pads with balanced copper distribution, and implement a controlled reflow oven temperature profile. -
Q: What causes solder balls to form on PCBs during assembly?
A: Solder balls can form due to excessive solder paste volume, incorrect reflow oven temperature profiles, contamination or impurities in the solder paste, or poor solder mask design and application. -
Q: How can I minimize the risk of ESD damage during PCB assembly?
A: To minimize ESD damage, implement a comprehensive ESD protection program, train personnel on ESD-safe handling techniques, use ESD-safe materials and tools, and regularly audit and maintain your ESD protection measures. -
Q: What steps can I take to ensure proper removal of flux residue after soldering?
A: To ensure proper removal of flux residue, select an appropriate flux and solder paste for your application and cleaning process, implement a thorough cleaning process using suitable cleaning agents and equipment, ensure adequate cleaning time and agitation, and regularly monitor the effectiveness of your cleaning process.
Conclusion
Understanding common PCB assembly failures and their prevention methods is essential for manufacturers and designers to ensure the production of high-quality, reliable electronic products. By implementing the prevention methods discussed in this article, such as optimizing solder paste stencil design, utilizing high-accuracy component placement systems, implementing robust reflow oven temperature profiling, and maintaining a clean manufacturing environment, you can significantly reduce the risk of PCB assembly failures and improve the overall quality of your products.
0 Comments