1. Understanding the PCB Assembly Process
Before diving into the specifics, it is essential to understand the overall PCB assembly process. The process typically involves the following steps:
- Solder Paste Application
- Component Placement
- Reflow Soldering
- Inspection and Testing
- Cleaning and Finishing
1.1 Solder Paste Application
Solder paste, a mixture of tiny solder particles and flux, is applied to the PCB pads using a stencil or screen printing process. The solder paste helps in the attachment of components to the board during the reflow soldering process.
1.2 Component Placement
Surface Mount Devices (SMDs) and through-hole components are placed onto the PCB using pick-and-place machines or manual placement techniques. Proper component orientation and alignment are crucial for successful assembly.
1.3 Reflow Soldering
The PCB with placed components is passed through a reflow oven, where the solder paste melts and forms a permanent connection between the components and the PCB pads. The reflow process follows a specific temperature profile to ensure optimal solder joint formation.
1.4 Inspection and Testing
After the reflow soldering process, the assembled PCB undergoes visual inspection and various testing procedures to identify any defects or malfunctions. Common inspection methods include:
- Automated Optical Inspection (AOI)
- X-ray Inspection
- In-Circuit Testing (ICT)
- Functional Testing
1.5 Cleaning and Finishing
Once the PCB passes the inspection and testing phase, it is cleaned to remove any flux residue or contaminants. Additional finishing processes, such as conformal coating or potting, may be applied depending on the application requirements.
2. Choosing the Right Components
Selecting the appropriate components for your PCB assembly is crucial for ensuring the desired functionality and reliability of the final product. Consider the following factors when choosing components:
- Functionality: Ensure that the selected components meet the required specifications and perform the intended functions.
- Quality: Opt for high-quality components from reputable manufacturers to minimize the risk of failures and defects.
- Compatibility: Verify that the chosen components are compatible with each other and the PCB design.
- Availability: Consider the lead time and availability of components to avoid delays in the assembly process.
- Cost: Strike a balance between cost and quality to optimize the overall production budget.
3. Designing for Manufacturability (DFM)
Designing a PCB with manufacturability in mind can significantly improve the efficiency and success of the assembly process. Follow these DFM guidelines:
- Adhere to the minimum trace width and spacing requirements based on the PCB fabrication capabilities.
- Ensure adequate clearance between components to facilitate proper placement and soldering.
- Use standard component packages and footprints to simplify the assembly process and reduce the risk of errors.
- Minimize the use of fine-pitch components, as they require precise placement and soldering techniques.
- Incorporate fiducial markers on the PCB to assist in component alignment during the assembly process.
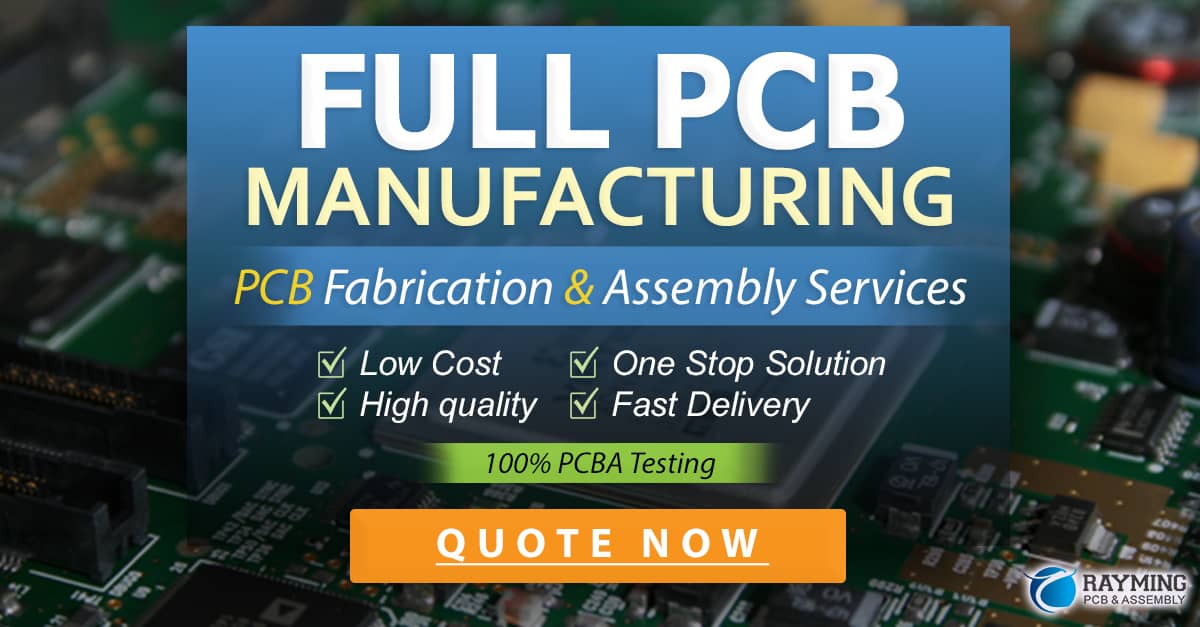
4. Solder Paste Stencil Design
The solder paste stencil plays a vital role in the accurate application of solder paste onto the PCB pads. Consider the following factors when designing the solder paste stencil:
- Aperture size and shape: Ensure that the aperture dimensions match the pad sizes on the PCB and provide adequate solder paste coverage.
- Stencil thickness: Select an appropriate stencil thickness based on the component sizes and solder paste requirements. Typically, stencil thicknesses range from 0.1 mm to 0.2 mm.
- Stencil material: Choose a suitable stencil material, such as stainless steel or nickel-plated stainless steel, for durability and compatibility with the solder paste.
- Stencil registration: Incorporate registration marks or fiducials on the stencil to ensure accurate alignment with the PCB during the solder paste application process.
5. Reflow Soldering Profile Optimization
Optimizing the reflow soldering profile is essential for achieving reliable solder joints and preventing component damage. Consider the following factors when setting up the reflow profile:
- Solder paste specifications: Refer to the solder paste manufacturer’s recommended temperature profile and adjust it according to the specific PCB assembly requirements.
- Component thermal limitations: Ensure that the reflow temperature does not exceed the maximum temperature ratings of the components to prevent thermal damage.
- Ramp rates: Control the ramp rates (heating and cooling rates) to allow for even heat distribution and minimize thermal stress on the components.
- Peak temperature and time above liquidus (TAL): Achieve the desired peak temperature and maintain it for an appropriate duration to ensure complete solder melting and wetting.
6. Inspection and Testing Techniques
Implementing effective inspection and testing techniques is crucial for identifying and resolving any issues in the assembled PCBs. Consider the following techniques:
- Automated Optical Inspection (AOI): Use AOI systems to detect component placement errors, solder joint defects, and other visual anomalies.
- X-ray Inspection: Employ X-ray inspection for evaluating solder joint quality, particularly for components with hidden or obscured solder joints.
- In-Circuit Testing (ICT): Perform electrical tests using ICT fixtures to verify the connectivity and functionality of individual components and circuits.
- Functional Testing: Conduct functional tests to assess the overall performance and functionality of the assembled PCB under real-world operating conditions.
7. Cleaning and Contamination Control
Proper cleaning and contamination control are essential for ensuring the long-term reliability and performance of the assembled PCBs. Consider the following practices:
- Flux residue removal: Use appropriate cleaning agents and methods to remove flux residue from the PCB surface after the soldering process.
- Contamination prevention: Implement measures to prevent contamination during the assembly process, such as using clean room environments, wearing gloves, and using ESD (Electrostatic Discharge) protection.
- Cleanliness testing: Perform cleanliness tests, such as ROSE (Resistivity of Solvent Extract) or ion chromatography, to verify the effectiveness of the cleaning process.
8. Documentation and Traceability
Maintaining proper documentation and traceability throughout the PCB assembly process is essential for quality control and troubleshooting purposes. Consider the following practices:
- Bill of Materials (BOM): Create and maintain an accurate BOM that lists all the components used in the PCB assembly, including their part numbers, quantities, and specifications.
- Assembly instructions: Develop clear and detailed assembly instructions that outline the step-by-step process for component placement, soldering, and testing.
- Traceability: Implement a traceability system that tracks the components, materials, and processes used in each PCB assembly. This can help in identifying the root cause of any issues and facilitating corrective actions.
Frequently Asked Questions (FAQ)
1. What is the difference between Surface Mount Technology (SMT) and Through-Hole Technology (THT) in PCB assembly?
Surface Mount Technology (SMT) involves placing components directly onto the surface of the PCB, while Through-Hole Technology (THT) involves inserting component leads through holes in the PCB and soldering them on the opposite side. SMT allows for smaller component sizes and higher component density, while THT provides stronger mechanical connections and is suitable for larger components or high-power applications.
2. What are the common defects that can occur during PCB assembly?
Common defects in PCB assembly include:
– Solder bridges: Unintended connections between adjacent pads or traces due to excessive solder.
– Solder voids: Gaps or holes in the solder joint, reducing the strength and reliability of the connection.
– Component misalignment: Improper placement or orientation of components on the PCB.
– Tombstoning: When a component stands up on one end due to uneven heating or solder paste application.
– Cold solder joints: Weak or brittle solder joints resulting from insufficient heat or poor solder wetting.
3. How can I prevent electrostatic discharge (ESD) damage during PCB assembly?
To prevent ESD damage during PCB assembly, follow these practices:
– Use ESD-safe workstations, including grounded mats, wrist straps, and conductive flooring.
– Handle PCBs and components using ESD-safe tools and packaging materials.
– Ensure proper grounding of personnel and equipment.
– Maintain a humidity level of 30-50% in the assembly environment to reduce static buildup.
– Provide ESD training to personnel involved in the assembly process.
4. What are the benefits of using automated optical inspection (AOI) in PCB assembly?
Automated optical inspection (AOI) offers several benefits in PCB assembly:
– Rapid and consistent inspection: AOI systems can quickly scan the entire PCB surface and identify defects with high accuracy and repeatability.
– Early defect detection: AOI enables the identification of defects early in the assembly process, allowing for timely corrections and reducing rework costs.
– Improved quality control: AOI helps in maintaining consistent quality standards by detecting and documenting defects that may be missed by manual inspection.
– Increased productivity: Automated inspection reduces the time and labor required for manual inspection, improving overall production efficiency.
5. How do I select the appropriate solder paste for my PCB assembly?
When selecting solder paste for your PCB assembly, consider the following factors:
– Alloy composition: Choose a solder alloy that meets the required melting temperature, strength, and compatibility with the components and PCB materials.
– Particle size: Select a solder paste with an appropriate particle size distribution for the component pitch and pad sizes on your PCB.
– Flux type: Consider the flux type (e.g., rosin, no-clean, water-soluble) based on the cleaning requirements and the desired level of residue after soldering.
– Viscosity: Ensure that the solder paste viscosity is suitable for the intended application method (e.g., stencil printing, dispensing).
– Compatibility: Verify that the solder paste is compatible with the reflow soldering process and the selected components.
Factor | Description |
---|---|
Alloy Composition | Choose a solder alloy based on melting temperature, strength, and compatibility |
Particle Size | Select a solder paste with appropriate particle size for component pitch and pad sizes |
Flux Type | Consider flux type (rosin, no-clean, water-soluble) based on cleaning requirements and desired residue level |
Viscosity | Ensure solder paste viscosity is suitable for the intended application method |
Compatibility | Verify compatibility with the reflow soldering process and selected components |
In conclusion, understanding and implementing these eight key aspects of PCB assembly can significantly enhance the quality, reliability, and efficiency of your electronic products. By selecting the right components, designing for manufacturability, optimizing the assembly processes, and ensuring proper inspection and documentation, you can minimize defects, reduce costs, and improve overall production outcomes. Stay informed about the latest advancements in PCB assembly technologies and best practices to stay ahead in the competitive electronics industry.
0 Comments