Introduction to Through Hole PCB Assembly
Through hole PCB assembly is a method of assembling printed circuit boards (PCBs) where component leads are inserted through drilled holes in the board and soldered to pads on the opposite side. This traditional assembly technique has been widely used for decades and remains a reliable choice for certain applications, despite the growing popularity of surface mount technology (SMT).
Advantages of Through Hole PCB Assembly
- Mechanical Strength: Through hole components provide stronger mechanical bonds to the PCB due to the leads being soldered through the board.
- Ease of Prototyping: Manual insertion and soldering of through hole components are easier compared to SMT, making it suitable for prototyping and low-volume production.
- High Power Handling: Through hole components can handle higher power levels than their SMT counterparts, making them ideal for power electronics applications.
- Reliability in Harsh Environments: The robust nature of through hole assembly makes it more suitable for applications exposed to vibration, shock, or extreme temperatures.
Disadvantages of Through Hole PCB Assembly
- Larger Footprint: Through hole components occupy more space on the PCB compared to SMT components, limiting the board’s density and miniaturization potential.
- Increased Drilling Costs: The need for drilled holes in through hole PCB assembly adds an additional manufacturing step and cost compared to SMT.
- Limited Component Availability: The variety of through hole components available in the market is decreasing as manufacturers focus on SMT components.
- Slower Assembly Process: Automated through hole assembly is slower than SMT assembly, leading to longer production times and higher labor costs.
Through Hole PCB Assembly Process
The through hole PCB assembly process involves several steps, from component preparation to final inspection. Here’s a detailed look at each stage:
1. PCB Fabrication
Before the assembly process begins, the PCB must be fabricated according to the design specifications. This includes creating the copper traces, solder pads, and drilled holes for through hole components.
2. Component Preparation
Through hole components are prepared for assembly by forming and trimming their leads to the appropriate length. This ensures proper insertion into the PCB holes and helps maintain consistent lead protrusion on the solder side of the board.
3. Component Insertion
The prepared components are inserted into the drilled holes on the PCB. This can be done manually for low-volume production or prototyping, or by using automated insertion machines for high-volume assembly.
Manual Insertion
In manual insertion, operators place the components into the designated holes on the PCB using hand tools or pneumatic machines. This method is suitable for low-volume production, prototyping, or when dealing with large or irregular-shaped components.
Automated Insertion
Automated insertion machines, such as axial and radial component insertion machines, are used for high-volume through hole PCB assembly. These machines can rapidly insert components into the board with high precision and consistency.
4. Soldering
After component insertion, the PCB undergoes soldering to create electrical and mechanical connections between the component leads and the solder pads.
Wave Soldering
Wave soldering is the most common method for soldering through hole components. The PCB is passed over a molten solder wave, which wets the component leads and solder pads, creating a strong bond. This process is highly automated and efficient for high-volume production.
Selective Soldering
Selective soldering is used when specific through hole components need to be soldered separately from others, often due to their heat sensitivity or to avoid solder bridging. This process involves using a localized solder fountain or mini-wave to solder only the targeted components.
Hand Soldering
For low-volume production or prototyping, hand soldering can be used to solder through hole components. This method requires skilled operators and is more time-consuming than automated soldering processes.
5. Inspection and Quality Control
After soldering, the assembled PCBs undergo inspection and quality control to ensure the integrity of the solder joints and the overall assembly.
Visual Inspection
Visual inspection is performed to check for any visible defects, such as solder bridges, cold solder joints, or damaged components. This can be done manually by trained operators or using automated optical inspection (AOI) systems.
X-Ray Inspection
X-ray inspection is used to examine the solder joints hidden under components or within multi-layer PCBs. This non-destructive testing method helps identify voids, cracks, or other defects that may not be visible through visual inspection.
Electrical Testing
Electrical testing is conducted to verify the functionality and performance of the assembled PCB. This may include in-circuit testing (ICT), functional testing, or boundary scan testing, depending on the complexity and requirements of the board.
6. Cleaning and Finishing
After inspection, the assembled PCBs are cleaned to remove any flux residue or contaminants from the soldering process. This can be done using various cleaning methods, such as ultrasonic cleaning, aqueous cleaning, or no-clean flux systems.
Finally, the PCBs may undergo additional finishing processes, such as conformal coating, potting, or labeling, depending on the application requirements and customer specifications.
Choosing Between Through Hole and Surface Mount Technology
When deciding between through hole and surface mount technology for PCB assembly, consider the following factors:
-
Component Availability: Through hole components are becoming less common as the industry shifts towards SMT. Ensure that the required through hole components are readily available for your project.
-
Board Density and Size: SMT allows for higher component density and smaller board sizes compared to through hole assembly. If miniaturization is a priority, SMT may be the better choice.
-
Power Handling: Through hole components generally have higher power handling capabilities than SMT components. If your application involves high power levels, through hole assembly may be more suitable.
-
Environmental Factors: Through hole assembly offers better mechanical strength and reliability in harsh environments, such as those exposed to vibration, shock, or extreme temperatures.
-
Production Volume and Cost: SMT is more cost-effective for high-volume production due to faster assembly processes and lower labor costs. Through hole assembly may be more economical for low-volume production or prototyping.
-
Design Complexity: SMT allows for more complex designs with finer pitch components and higher routing density. Through hole assembly may be more suitable for simpler designs or those requiring larger components.
-
Manufacturing Capabilities: Consider the capabilities of your PCB assembly partner. Some manufacturers may specialize in SMT, while others have expertise in through hole assembly.
Factor | Through Hole Assembly | Surface Mount Technology |
---|---|---|
Component Availability | Decreasing | Widely available |
Board Density and Size | Lower density, larger | Higher density, smaller |
Power Handling | Higher power handling | Lower power handling |
Environmental Factors | More reliable | Less reliable |
Production Volume & Cost | Economical for low volume | Cost-effective for high volume |
Design Complexity | Simpler designs | More complex designs possible |
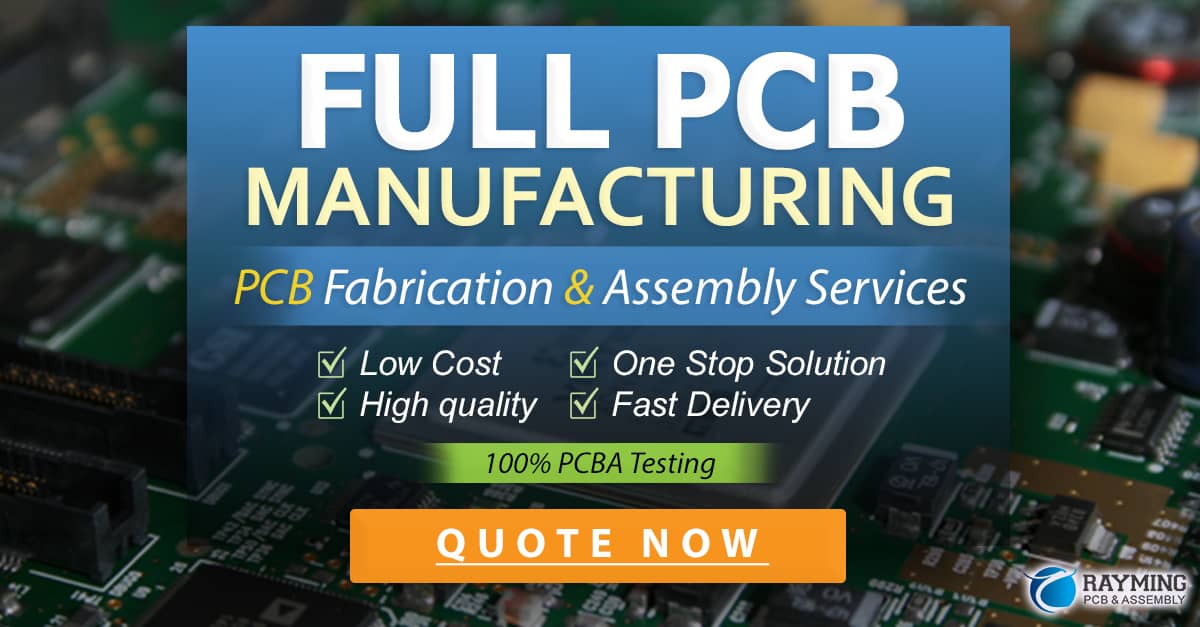
Best Practices for Through Hole PCB Assembly
To ensure the success of your through hole PCB assembly project, consider the following best practices:
-
Design for Manufacturability (DFM): Collaborate with your PCB assembly partner to ensure your design is optimized for through hole assembly. This includes considering component placement, hole sizes, and lead protrusion.
-
Component Selection: Choose through hole components that are readily available and comply with industry standards. Avoid using obsolete or hard-to-find components that may delay your project or increase costs.
-
Lead Preparation: Ensure that component leads are properly formed and trimmed before insertion. This helps maintain consistent lead protrusion and prevents issues during soldering.
-
Solder Joint Quality: Monitor the quality of solder joints throughout the assembly process. Implement appropriate soldering techniques, such as controlling solder temperature and dwell time, to achieve reliable and strong solder connections.
-
Inspection and Testing: Conduct thorough inspections and testing at various stages of the assembly process to identify and address any defects or issues early on. This includes visual inspection, X-ray inspection, and electrical testing.
-
Cleaning and Protection: Clean the assembled PCBs to remove any flux residue or contaminants that may impact the board’s long-term reliability. Apply necessary protective measures, such as conformal coating or potting, to ensure the board can withstand its intended operating environment.
-
Documentation and Traceability: Maintain accurate documentation throughout the assembly process, including assembly drawings, bill of materials (BOM), and production records. Implement a traceability system to track components, materials, and processes used in each assembly.
By following these best practices, you can improve the quality, reliability, and efficiency of your through hole PCB assembly process.
Frequently Asked Questions (FAQ)
-
Q: What is through hole PCB assembly?
A: Through hole PCB assembly is a method of assembling printed circuit boards where component leads are inserted through drilled holes in the board and soldered to pads on the opposite side. -
Q: What are the advantages of through hole PCB assembly?
A: The advantages of through hole PCB assembly include stronger mechanical bonds, ease of prototyping, high power handling capabilities, and reliability in harsh environments. -
Q: What are the disadvantages of through hole PCB assembly?
A: The disadvantages of through hole PCB assembly include larger component footprints, increased drilling costs, limited component availability, and slower assembly processes compared to surface mount technology (SMT). -
Q: What are the key steps in the through hole PCB assembly process?
A: The key steps in the through hole PCB assembly process include PCB fabrication, component preparation, component insertion, soldering, inspection and quality control, cleaning, and finishing. -
Q: How do I choose between through hole and surface mount technology for my PCB assembly project?
A: When choosing between through hole and surface mount technology, consider factors such as component availability, board density and size, power handling requirements, environmental factors, production volume and cost, design complexity, and the manufacturing capabilities of your PCB assembly partner.
Conclusion
Through hole PCB assembly remains a viable and reliable method for assembling printed circuit boards, particularly for applications that require strong mechanical bonds, high power handling, or reliability in harsh environments. By understanding the advantages, disadvantages, and best practices associated with through hole assembly, you can make informed decisions when designing and manufacturing your PCBs.
As the electronics industry continues to evolve, it’s essential to stay up-to-date with the latest technologies and trends in PCB assembly. Whether you choose through hole or surface mount technology, working closely with an experienced PCB assembly partner can help ensure the success of your project.
0 Comments