What is a PCB Trace Width Calculator?
A PCB trace width calculator is a tool used to determine the appropriate width of copper traces on a printed circuit board (PCB) based on various electrical and environmental factors. The width of PCB traces plays a crucial role in ensuring proper current carrying capacity, signal integrity, and overall reliability of the circuit.
Key Factors Affecting Trace Width
Several factors influence the calculation of trace width:
- Current: The amount of current flowing through the trace
- Temperature Rise: The acceptable temperature rise above ambient
- Copper Thickness: The thickness of the copper layer on the PCB
- Trace Length: The length of the trace on the PCB
Why is Trace Width Important?
Properly sized PCB traces are essential for several reasons:
Current Carrying Capacity
The width of a trace determines its cross-sectional area, which directly affects its current carrying capacity. If a trace is too narrow, it may not be able to handle the required current, leading to excessive heating and potential damage to the PCB.
Signal Integrity
Trace width also impacts signal integrity. High-speed signals are sensitive to trace impedance, which is influenced by the trace width and the distance between the trace and the reference plane (e.g., ground or power plane). Mismatched impedances can lead to signal reflections and distortions.
EMI and Crosstalk
Properly designed trace widths can help minimize electromagnetic interference (EMI) and crosstalk between adjacent traces. Wider traces have lower resistance and inductance, which can reduce EMI emissions. Additionally, maintaining appropriate spacing between traces can minimize crosstalk.
How to Use a PCB Trace Width Calculator
Using a PCB trace width calculator involves inputting the relevant parameters and interpreting the results. Here’s a step-by-step guide:
Step 1: Determine the Required Current
Identify the maximum current that will flow through the trace. This information can be obtained from the circuit design or component datasheets.
Step 2: Set the Acceptable Temperature Rise
Decide on the maximum acceptable temperature rise above the ambient temperature. This value depends on the PCB material, component ratings, and operating environment. A common value is 10°C to 20°C.
Step 3: Specify the Copper Thickness
Enter the thickness of the copper layer on the PCB. Standard copper thicknesses are 0.5 oz/ft², 1 oz/ft², and 2 oz/ft², which correspond to 17.5 μm, 35 μm, and 70 μm, respectively.
Step 4: Input the Trace Length (Optional)
Some calculators may require the trace length to account for voltage drop along the trace. If this parameter is available, enter the estimated or actual length of the trace.
Step 5: Calculate the Trace Width
After inputting the required parameters, the calculator will display the recommended trace width. The result may be given in mils (thousandths of an inch) or millimeters.
Step 6: Interpret the Results
Compare the calculated trace width with the PCB manufacturing capabilities and design constraints. If the calculated width is too narrow for reliable manufacturing or if it exceeds the available space, consider adjusting the design or using wider traces in critical areas.
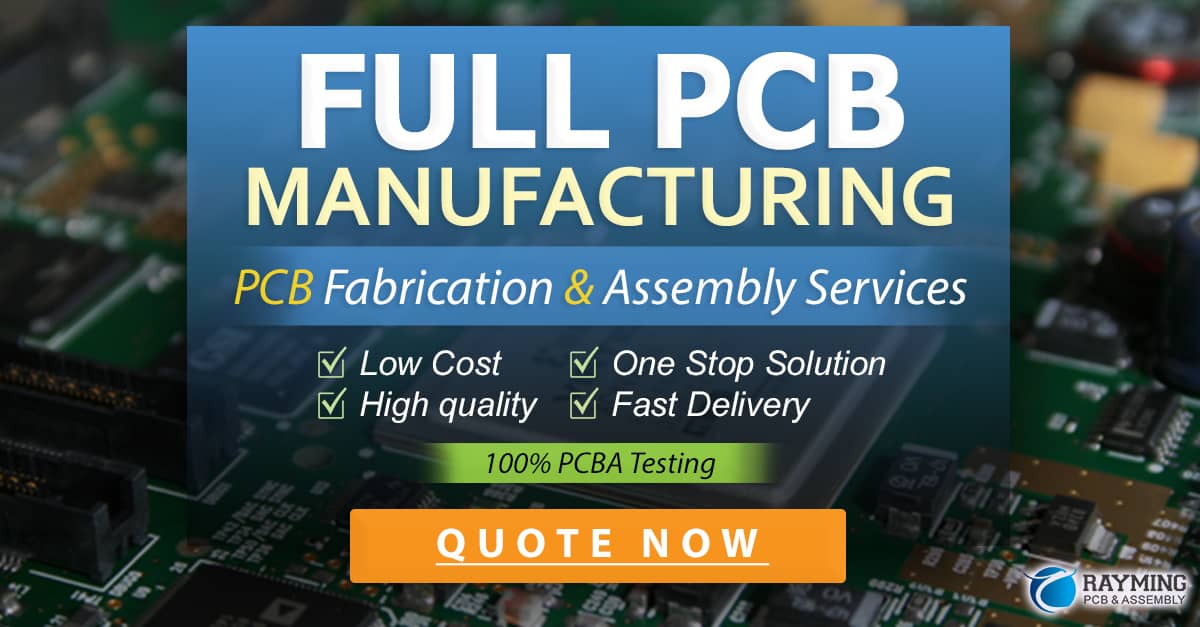
PCB Trace Width Calculation Example
Let’s walk through an example to illustrate the process of calculating trace width.
Example Scenario
- Current: 1 A
- Temperature Rise: 15°C
- Copper Thickness: 1 oz/ft² (35 μm)
- Trace Length: 50 mm
Using an online PCB trace width calculator, we input these parameters and obtain the following result:
Current (A) | Temperature Rise (°C) | Copper Thickness (oz/ft²) | Trace Length (mm) | Recommended Trace Width (mm) |
---|---|---|---|---|
1 | 15 | 1 | 50 | 0.8 |
The calculator recommends a trace width of 0.8 mm (approx. 31 mils) for the given parameters.
PCB Trace Width Rules of Thumb
While calculators provide accurate results, some general rules of thumb can be used for quick estimates:
- For low-current signals (< 100 mA), a trace width of 0.2 mm to 0.3 mm is usually sufficient.
- For moderate currents (100 mA to 500 mA), use trace widths between 0.3 mm and 0.8 mm.
- For high-current traces (> 500 mA), use wider traces (> 0.8 mm) or consider using multiple traces in parallel.
Remember, these are rough guidelines, and it’s always best to use a calculator for more precise results.
Advanced Considerations
High-Speed Signals
When dealing with high-speed signals, additional factors come into play:
- Impedance matching: Ensure that the trace impedance matches the source and load impedances to minimize reflections.
- Length matching: Match the lengths of signal traces to maintain signal integrity and avoid timing issues.
- Differential pairs: Use tightly coupled differential pairs for high-speed differential signals to minimize crosstalk and EMI.
Power Traces
Power traces often carry significant currents and require special consideration:
- Voltage drop: Ensure that the voltage drop along the power trace is within acceptable limits.
- Copper pour: Use copper pours or planes to distribute power and provide low-impedance paths.
- Via placement: Place vias strategically to minimize voltage drop and improve current distribution.
Frequently Asked Questions (FAQ)
1. What happens if I use a trace that is too narrow?
If a trace is too narrow for the current it carries, it may overheat and cause damage to the PCB. Excessive heating can lead to trace degradation, delamination of the PCB Layers, or even complete trace failure.
2. Can I use different trace widths for different sections of the same trace?
Yes, you can use different trace widths for different sections of the same trace. This is often done to optimize space usage on the PCB. However, ensure that the narrowest section can still handle the required current and that any width transitions are gradual to avoid impedance discontinuities.
3. How do I calculate trace width for traces on inner layers of a multi-layer PCB?
The process for calculating trace width on inner layers is similar to that for outer layers. However, you should consider the thickness of the inner layer copper, which may be different from the outer layers. Additionally, the temperature rise may be affected by the proximity to other layers and the overall thermal characteristics of the PCB Stackup.
4. What is the minimum trace width that can be reliably manufactured?
The minimum trace width depends on the PCB manufacturing process and the capabilities of the manufacturer. Typical minimum trace widths range from 0.1 mm to 0.15 mm for standard PCB fabrication. However, advanced processes can achieve even narrower traces. Always consult with your PCB manufacturer for their specific capabilities and guidelines.
5. Can I use a trace width calculator for flexible PCBs?
Yes, you can use a trace width calculator for flexible PCBs. However, keep in mind that flexible PCBs may have different copper thicknesses and thermal characteristics compared to rigid PCBs. Additionally, the mechanical stresses experienced by flexible PCBs during use may necessitate wider traces to ensure reliability.
Conclusion
PCB trace width calculators are essential tools for designing reliable and efficient printed circuit boards. By considering factors such as current, temperature rise, copper thickness, and trace length, designers can determine the appropriate trace widths for their specific applications. Proper trace sizing ensures adequate current carrying capacity, signal integrity, and minimizes issues such as EMI and crosstalk.
When using a trace width calculator, it’s important to input accurate parameters and interpret the results in the context of the overall PCB design and manufacturing constraints. Additionally, designers should be aware of advanced considerations for high-speed signals and power traces.
By following best practices and leveraging the power of trace width calculators, PCB designers can create robust and reliable circuits that meet the demands of modern electronic devices.
0 Comments