Introduction to PCB Layers
Printed Circuit Boards (PCBs) are essential components in modern electronics. They provide a platform for mounting and interconnecting electronic components to create functional circuits. PCBs are made up of multiple layers, each serving a specific purpose in the overall design. The number of layers in a PCB can vary depending on the complexity and requirements of the circuit.
In this article, we will explore the different layers of PCBs and their production processes. We will discuss the materials used, the manufacturing steps involved, and the role each layer plays in the final PCB assembly.
Types of PCB Layers
PCBs can be classified based on the number of layers they contain. The most common types are:
PCB Type | Number of Layers |
---|---|
Single-sided | 1 |
Double-sided | 2 |
Multi-layer | 4, 6, 8, 10, 12 or more |
Single-sided PCBs have components and traces on only one side of the board. Double-sided PCBs utilize both sides for component placement and routing. Multi-layer PCBs consist of multiple conductive layers sandwiched between insulating layers, allowing for higher component density and more complex designs.
Production Process for Single-Sided PCBs
Step 1: Substrate Preparation
The production process begins with the preparation of the substrate material, typically FR-4 (Flame Retardant 4) laminate. FR-4 is a composite material made of woven fiberglass cloth impregnated with epoxy resin. The substrate is cut to the desired size and shape using precision cutting tools.
Step 2: Copper Cladding
A thin layer of copper foil is bonded to one side of the substrate using heat and pressure. The copper foil serves as the conductive layer for the PCB. The thickness of the copper foil can vary depending on the current carrying requirements of the circuit.
Step 3: Applying Photoresist
A photosensitive resist material is applied to the copper surface. This resist will later be used to transfer the circuit pattern onto the copper layer. The photoresist can be applied using various methods such as screen printing, spray coating, or roller coating.
Step 4: Exposure and Development
The PCB artwork, which contains the circuit pattern, is placed on top of the photoresist-coated copper layer. The artwork is typically a film or glass photomask with transparent and opaque areas representing the desired circuit pattern. The photoresist is then exposed to ultraviolet (UV) light through the artwork. The UV light hardens the exposed areas of the photoresist, while the unexposed areas remain soluble.
After exposure, the PCB is developed using a chemical solution that removes the soluble portions of the photoresist. This process reveals the copper layer in areas where the circuit pattern will be formed.
Step 5: Etching
The exposed copper areas are chemically etched away using an etchant solution, typically ferric chloride or ammonium persulfate. The etchant removes the unwanted copper, leaving behind the desired circuit pattern protected by the hardened photoresist.
Step 6: Resist Stripping
After etching, the remaining photoresist is stripped away using a chemical stripper, revealing the final copper circuit pattern on the PCB.
Step 7: Drilling
Holes are drilled through the PCB at designated locations to accommodate component leads and provide electrical connections between layers (in the case of double-sided or multi-layer PCBs). The drilling process is performed using high-speed CNC (Computer Numerical Control) drilling machines.
Step 8: Surface Finishing
To protect the exposed copper and enhance solderability, a surface finish is applied to the PCB. Common surface finishes include:
- Hot Air Solder Leveling (HASL): A thin layer of solder is applied to the copper surfaces using a hot air leveling process.
- Electroless Nickel Immersion Gold (ENIG): A layer of nickel is electrolessly plated onto the copper, followed by a thin layer of gold.
- Organic Solderability Preservative (OSP): A thin, organic coating is applied to the copper surfaces to prevent oxidation.
Step 9: Solder Mask Application
A solder mask, typically green in color, is applied to the PCB surface. The solder mask serves as an insulating layer, protecting the copper traces from accidental contact and preventing solder bridges during the component assembly process. Openings in the solder mask are created to expose the pads where components will be soldered.
Step 10: Silkscreen Printing
A silkscreen layer is printed onto the PCB surface to provide text, logos, and component identifiers. The silkscreen is typically white and helps in the assembly and troubleshooting of the PCB.
Step 11: Electrical Testing
The completed single-sided PCB undergoes electrical testing to ensure the integrity of the circuits and the absence of short circuits or open connections. Various testing methods, such as flying probe testing or bed-of-nails testing, can be employed depending on the PCB complexity and production volume.
Production Process for Double-Sided PCBs
The production process for double-sided PCBs follows similar steps to single-sided PCBs, with a few additional considerations:
Step 1-4: Substrate Preparation, Copper Cladding, Applying Photoresist, Exposure and Development
These steps are performed on both sides of the substrate, creating copper layers on the top and bottom of the PCB.
Step 5: Through-Hole Plating
Before etching, the drilled holes are plated with copper to create electrical connections between the top and bottom layers. This process involves electroless copper deposition followed by electroplating to achieve the desired thickness.
Step 6-11: Etching, Resist Stripping, Drilling, Surface Finishing, Solder Mask Application, Silkscreen Printing, Electrical Testing
These steps are carried out similarly to the single-sided PCB process, considering both sides of the PCB.
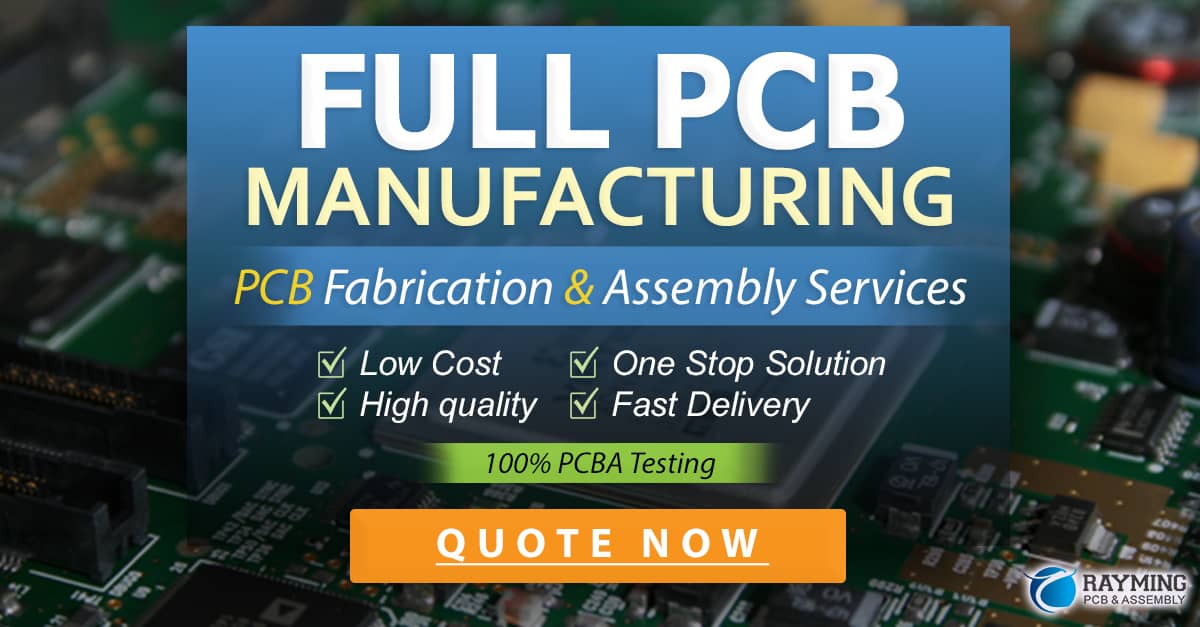
Production Process for Multi-Layer PCBs
Multi-layer PCBs involve a more complex production process due to the presence of multiple conductive layers and insulating layers.
Step 1: Inner Layer Fabrication
The inner layers of the multi-layer PCB are fabricated using a process similar to the single-sided PCB production. Each inner layer is patterned, etched, and inspected individually.
Step 2: Lamination
The inner layers are aligned and stacked with insulating prepreg (pre-impregnated) layers between them. Copper foils are placed on the top and bottom of the stack to form the outer layers. The entire stack is then laminated under high pressure and temperature to fuse the layers together.
Step 3: Drilling
Holes are drilled through the laminated board to create vias that connect the different layers. The drilling process is critical in multi-layer PCBs as it ensures proper alignment and connectivity between layers.
Step 4: Through-Hole Plating
The drilled holes are plated with copper to create electrical connections between the layers. This process involves electroless copper deposition followed by electroplating.
Step 5: Outer Layer Processing
The outer layers of the multi-layer PCB are processed using steps similar to the double-sided PCB production, including patterning, etching, and surface finishing.
Step 6: Solder Mask Application and Silkscreen Printing
A solder mask is applied to the outer layers, and silkscreen printing is performed to add text, logos, and component identifiers.
Step 7: Electrical Testing
Rigorous electrical testing is conducted on the multi-layer PCB to ensure the integrity of the circuits and the proper functioning of the interconnections between layers.
Advantages of Different PCB Layers
PCB Type | Advantages |
---|---|
Single-sided | – Simple design and low cost – Suitable for basic circuits and low-density layouts |
Double-sided | – Increased component density compared to single-sided PCBs – Allows for more complex routing and signal paths |
Multi-layer | – High component density and routing complexity – Improved signal integrity and reduced electromagnetic interference – Enables advanced circuitry and high-speed applications |
FAQ
1. What is the most common base material used for PCBs?
The most common base material used for PCBs is FR-4 (Flame Retardant 4) laminate. FR-4 is a composite material made of woven fiberglass cloth impregnated with epoxy resin. It offers good mechanical strength, electrical insulation, and thermal stability.
2. How does the number of layers affect the cost of a PCB?
The cost of a PCB generally increases with the number of layers. Single-sided PCBs are the most economical, followed by double-sided PCBs. Multi-layer PCBs are the most expensive due to the complexity of the fabrication process and the additional materials required, such as prepreg and copper foils for each layer.
3. What is the purpose of the solder mask on a PCB?
The solder mask is an insulating layer applied to the PCB surface. It serves several purposes:
- Protects the copper traces from oxidation and environmental damage
- Prevents accidental short circuits during soldering
- Provides electrical insulation between adjacent traces and components
- Improves the aesthetic appearance of the PCB
4. Can multi-layer PCBs have different copper thicknesses for each layer?
Yes, multi-layer PCBs can have different copper thicknesses for each layer. The copper thickness can be adjusted based on the current carrying requirements and signal integrity needs of each layer. Inner layers often have thinner copper compared to outer layers, as they typically carry lower currents and have shorter trace lengths.
5. What is the role of vias in multi-layer PCBs?
Vias are conductive pathways that connect different layers in a multi-layer PCB. They are created by drilling holes through the PCB and plating them with copper. Vias allow signals and power to be routed between layers, enabling more complex routing and higher component density. There are different types of vias, such as through-hole vias, blind vias, and buried vias, each serving specific purposes in the PCB design.
Conclusion
The production process for different layers of PCBs involves a series of precise steps to create reliable and functional circuit boards. Single-sided, double-sided, and multi-layer PCBs each have their own manufacturing processes, materials, and advantages.
Understanding the role of each layer and the fabrication techniques employed helps in designing and manufacturing PCBs that meet the specific requirements of electronic devices. As technology advances, the demand for high-density, high-performance PCBs continues to grow, driving innovation in PCB design and production processes.
By carefully selecting the appropriate number of layers and optimizing the design, PCB manufacturers can create boards that offer the best balance of functionality, reliability, and cost-effectiveness for a wide range of applications.
0 Comments