What is PCB Quality?
PCB quality refers to the overall performance, reliability, and durability of a printed circuit board (PCB). It encompasses various aspects, such as the materials used, the manufacturing process, and the adherence to industry standards and specifications. High-quality PCBs are essential for ensuring the proper functioning and longevity of electronic devices.
Factors Affecting PCB Quality
Several factors contribute to the quality of a PCB. These include:
1. Material Selection
The choice of materials used in PCB fabrication plays a crucial role in determining its quality. High-quality PCBs use superior materials that offer excellent electrical properties, thermal stability, and mechanical strength. Some commonly used materials include:
- FR-4: A flame-retardant glass-reinforced epoxy laminate, widely used for its good electrical insulation and mechanical properties.
- Polyimide: A high-temperature resistant material used in applications that require increased thermal stability.
- PTFE: Polytetrafluoroethylene, known for its low dielectric constant and low loss at high frequencies, making it suitable for high-speed and RF applications.
2. Manufacturing Process
The manufacturing process employed in PCB fabrication directly impacts the quality of the final product. Key aspects of the manufacturing process include:
- Etching: The process of removing unwanted copper from the PCB substrate to create the desired circuit pattern. Precise etching ensures accurate trace widths and spacing.
- Drilling: Creating holes in the PCB for component placement and inter-layer connections. Accurate drilling is essential for proper component fit and reliable connections.
- Plating: Applying a thin layer of metal (usually copper) to the drilled holes and exposed copper traces to improve conductivity and protect against oxidation.
- Solder Mask Application: Applying a protective coating to the PCB surface to prevent short circuits and provide insulation between components.
- Silkscreen Printing: Adding text, logos, and component identifiers to the PCB surface for easy identification and assembly.
3. Adherence to Industry Standards
High-quality PCBs are manufactured in compliance with recognized industry standards. These standards ensure consistency, reliability, and compatibility across different manufacturers and applications. Some notable standards include:
- IPC (Association Connecting Electronics Industries) Standards:
- IPC-A-600: Acceptability of Printed Boards
- IPC-6012: Qualification and Performance Specification for Rigid Printed Boards
- IPC-2221: Generic Standard on Printed Board Design
- UL (Underwriters Laboratories) Standards:
- UL 94: Standard for Safety of Flammability of Plastic Materials
- UL 796: Standard for Safety of Printed-Wiring Boards
Adherence to these standards helps maintain the quality and reliability of PCBs.
4. Quality Control and Testing
Rigorous quality control and testing procedures are essential for ensuring the quality of PCBs. These processes help identify and rectify any defects or issues before the PCBs are put into use. Common quality control and testing methods include:
- Visual Inspection: Manual or automated visual examination of the PCB for any visible defects, such as incorrect component placement, solder bridges, or damaged traces.
- Automated Optical Inspection (AOI): Using specialized cameras and software to detect surface-level defects on the PCB.
- X-Ray Inspection: Utilizing X-ray imaging to detect internal defects, such as voids in solder joints or misaligned components.
- Electrical Testing: Performing tests to verify the electrical integrity of the PCB, including continuity, insulation resistance, and high-potential (hipot) testing.
- Functional Testing: Testing the PCB under actual operating conditions to ensure it performs as intended.
PCB Quality Metrics
To assess the quality of a PCB, several key metrics are used. These metrics help quantify the performance and reliability of the PCB. Some important PCB quality metrics include:
1. Defect Rate
The defect rate is a measure of the number of defective PCBs produced per unit of production. It is typically expressed as a percentage or parts per million (PPM). A lower defect rate indicates higher PCB quality and a more reliable manufacturing process.
Defect Rate | Quality Level |
---|---|
< 100 PPM | High |
100-500 PPM | Medium |
> 500 PPM | Low |
2. First Pass Yield (FPY)
First Pass Yield (FPY) is the percentage of PCBs that pass all quality tests and inspections without requiring rework or repair. A higher FPY indicates a more efficient and reliable manufacturing process, resulting in better PCB quality.
FPY | Quality Level |
---|---|
> 95% | High |
90-95% | Medium |
< 90% | Low |
3. Mean Time Between Failures (MTBF)
Mean Time Between Failures (MTBF) is a measure of the average time a PCB operates without failure under specified conditions. It is typically expressed in hours or years. A higher MTBF indicates better PCB reliability and quality.
MTBF | Quality Level |
---|---|
> 100,000 hours | High |
50,000-100,000 hours | Medium |
< 50,000 hours | Low |
4. Solder Joint Reliability
Solder joint reliability refers to the strength and durability of the solder connections between components and the PCB. High-quality PCBs have reliable solder joints that can withstand thermal and mechanical stresses over the product’s lifetime. Solder joint reliability can be assessed through various tests, such as thermal cycling and mechanical shock tests.
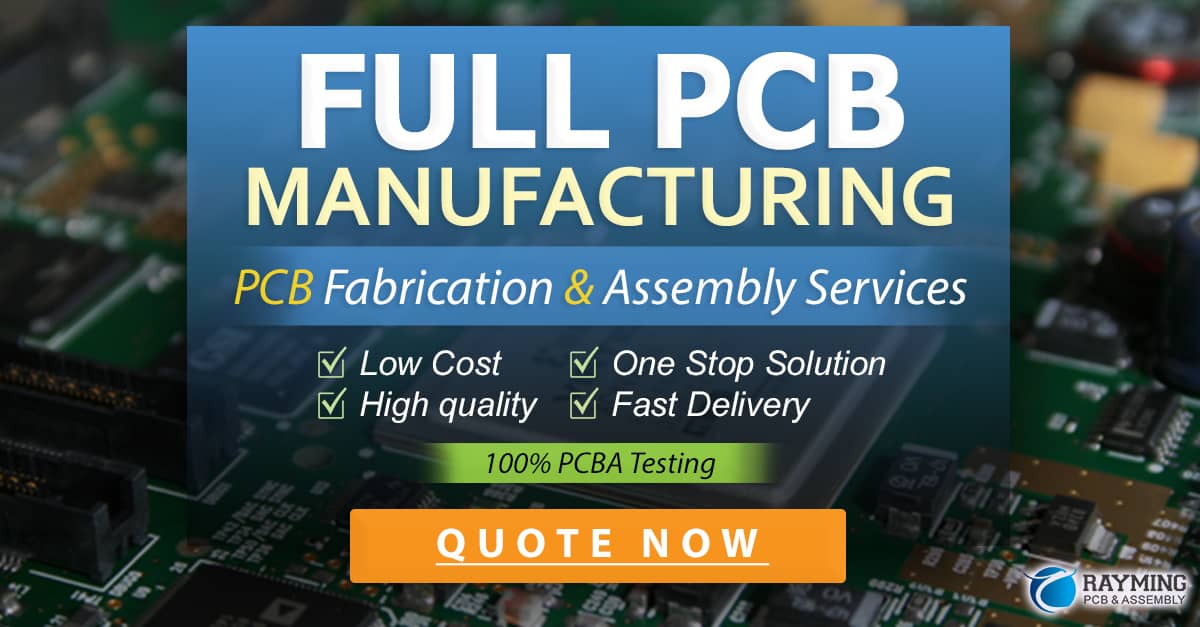
Best Practices for Ensuring PCB Quality
To ensure the highest level of PCB quality, consider the following best practices:
- Choose a reputable PCB manufacturer with a proven track record of producing high-quality boards.
- Provide clear and detailed design specifications to the manufacturer, including material requirements, layer stack-up, and tolerances.
- Use design for manufacturability (DFM) principles to optimize your PCB design for ease of manufacturing and assembly.
- Specify appropriate testing and inspection requirements to the manufacturer, such as AOI, X-ray inspection, and electrical testing.
- Request comprehensive quality control documentation from the manufacturer, including test reports and certificates of conformance.
- Conduct thorough incoming inspections and testing on received PCBs to verify their quality and functionality.
- Establish a robust supply chain management system to ensure the quality and traceability of components used in PCB Assembly.
Frequently Asked Questions (FAQs)
1. What is the difference between PCB quality and reliability?
PCB quality refers to the overall performance and adherence to specifications of a PCB at the time of manufacture. Reliability, on the other hand, is a measure of how well the PCB performs over its intended lifetime under specified operating conditions. High-quality PCBs are more likely to have better reliability.
2. How can I determine the quality of a PCB?
You can determine the quality of a PCB by considering factors such as the materials used, manufacturing process, adherence to industry standards, and quality control measures employed by the manufacturer. Additionally, you can assess PCB quality using metrics like defect rate, first pass yield, and mean time between failures.
3. What are the consequences of using low-quality PCBs?
Using low-quality PCBs can lead to various problems, such as:
– Reduced reliability and shorter product lifespan
– Increased risk of failures and malfunctions
– Potential safety hazards, especially in critical applications
– Increased maintenance and repair costs
– Damage to the reputation of the product or company
4. How can I ensure consistent PCB quality across different production runs?
To ensure consistent PCB quality across different production runs, consider the following:
– Use the same PCB manufacturer and materials for each run
– Provide clear and detailed specifications to the manufacturer
– Implement strict quality control and testing procedures
– Conduct regular audits of the manufacturing process
– Monitor and track quality metrics over time to identify any trends or issues
5. What should I do if I receive low-quality PCBs from a manufacturer?
If you receive low-quality PCBs from a manufacturer, take the following steps:
1. Document the defects or issues with the PCBs, including photos and test results.
2. Notify the manufacturer of the problem and request a root cause analysis and corrective action plan.
3. Negotiate a resolution, such as a refund, replacement, or rework of the affected PCBs.
4. Consider switching to a different manufacturer if the issue persists or is not adequately addressed.
Conclusion
PCB quality is a critical factor in ensuring the reliable performance and longevity of electronic devices. By understanding the factors that influence PCB quality, such as material selection, manufacturing process, and adherence to industry standards, you can make informed decisions when designing and sourcing PCBs.
Implementing best practices for PCB quality, such as using reputable manufacturers, providing clear specifications, and conducting thorough testing and inspection, can help you achieve the highest level of PCB quality for your applications.
Remember, investing in high-quality PCBs may have a higher upfront cost, but it can ultimately save you time, money, and reputation in the long run by reducing the risk of failures, malfunctions, and customer dissatisfaction.
0 Comments