1. PCB Prototypes Can Be Made in Just 24 Hours
One of the most impressive facts about PCB prototypes is the speed at which they can be produced. Thanks to advancements in technology and manufacturing processes, some PCB prototype services can deliver fully functional boards in as little as 24 hours. This incredible turnaround time allows designers to quickly iterate on their designs and bring products to market faster than ever before.
2. PCB Prototypes Can Be Made with Biodegradable Materials
As concerns about environmental sustainability continue to grow, some PCB Prototype Manufacturers are exploring the use of biodegradable materials in their products. These materials, which include bioplastics and other eco-friendly alternatives to traditional PCB substrates, can help reduce the environmental impact of electronics manufacturing while still providing the same high level of performance and reliability.
3. PCB Prototypes Can Incorporate Advanced Features Like Embedded Components
PCB prototypes aren’t just simple boards with a few components attached. In fact, modern PCB prototypes can incorporate a wide range of advanced features, including embedded components that are built directly into the board itself. This allows for even greater miniaturization and functionality in a smaller package, making it possible to create highly complex and sophisticated electronic devices.
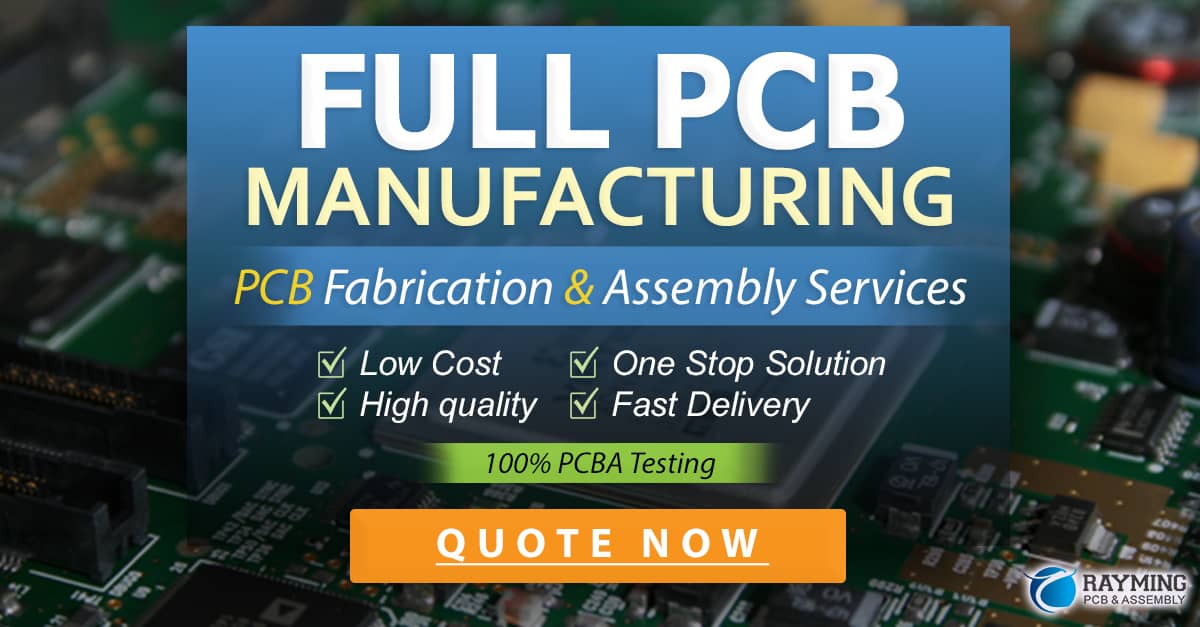
4. PCB Prototypes Can Be Used for More Than Just Electronics
While PCB prototypes are most commonly associated with electronics, they can actually be used for a wide range of applications beyond just circuits and components. For example, some designers have used PCB prototypes to create unique jewelry, art installations, and even musical instruments. The versatility of PCB technology makes it a valuable tool for creative exploration and experimentation.
5. PCB Prototypes Can Be Made with Flexible and Stretchable Materials
Not all PCB prototypes are rigid and inflexible. In fact, some manufacturers specialize in creating flexible and even stretchable PCB prototypes that can bend, twist, and conform to different shapes and surfaces. These unique properties make flexible and stretchable PCBs ideal for wearable technology, medical devices, and other applications where traditional rigid PCBs may not be suitable.
6. PCB Prototypes Can Be Manufactured with Extremely High Precision
PCB prototypes require an incredibly high level of precision to ensure that all components are properly aligned and connected. Modern PCB manufacturing equipment is capable of achieving extremely tight tolerances, with some machines able to place components with an accuracy of just a few microns. This level of precision is essential for creating reliable and high-performing electronic devices.
7. PCB Prototypes Can Be Customized with a Wide Range of Surface Finishes
The surface finish of a PCB prototype can have a significant impact on its performance, durability, and aesthetics. PCB manufacturers offer a wide range of surface finishes to choose from, including hot air solder leveling (HASL), immersion silver, immersion tin, and even gold plating for high-end applications. Each surface finish has its own unique properties and benefits, allowing designers to customize their PCB prototypes to meet specific requirements.
8. PCB Prototypes Can Be Made with High-Temperature Materials for Extreme Environments
Not all PCB prototypes are designed for use in typical office or home environments. Some applications, such as aerospace, automotive, and industrial equipment, require PCBs that can withstand extreme temperatures and other harsh conditions. To meet these demands, PCB manufacturers offer a range of high-temperature materials, such as polyimide and ceramic substrates, that can operate reliably in temperatures up to 250°C or higher.
9. PCB Prototypes Can Incorporate Wireless Connectivity
PCB prototypes aren’t just limited to wired connections. Many modern PCB designs incorporate wireless connectivity options, such as Bluetooth, Wi-Fi, and cellular networks, to enable remote monitoring, control, and data transfer. These wireless capabilities are becoming increasingly important in the era of the Internet of Things (IoT), where devices are expected to communicate and interact with each other seamlessly.
10. PCB Prototypes Can Be Manufactured with Embedded Antennas
In addition to wireless connectivity, PCB prototypes can also incorporate embedded antennas directly into the board design. This allows for even greater integration and miniaturization, as the antenna becomes an integral part of the PCB rather than a separate component. Embedded antennas can be customized to meet specific frequency and performance requirements, making them a valuable tool for wireless communication applications.
11. PCB Prototypes Can Be Simulated and Tested Virtually Before Manufacturing
Before a PCB prototype is even manufactured, designers can use advanced simulation and testing tools to verify its performance and identify potential issues. These virtual prototyping techniques allow designers to optimize their designs and catch errors early in the development process, reducing the need for costly and time-consuming physical prototypes. By simulating factors such as signal integrity, thermal performance, and mechanical stress, designers can ensure that their PCB prototypes will meet all necessary requirements.
12. PCB Prototypes Are Essential for Product Development and Innovation
Perhaps the most important thing to know about PCB prototypes is that they are absolutely essential for product development and innovation in the electronics industry. Without the ability to quickly and easily create physical prototypes of their designs, engineers and designers would be unable to test and refine their ideas, leading to slower progress and fewer breakthroughs. PCB prototypes allow for rapid iteration and experimentation, enabling the creation of new and innovative products that push the boundaries of what’s possible with electronics.
Aspect | Description |
---|---|
Speed | PCB prototypes can be produced in as little as 24 hours |
Materials | PCB prototypes can be made with biodegradable and eco-friendly materials |
Features | PCB prototypes can incorporate advanced features like embedded components |
Applications | PCB prototypes can be used for more than just electronics, including art and music |
Flexibility | PCB prototypes can be made with flexible and stretchable materials |
Precision | PCB prototypes can be manufactured with extremely high precision |
Surface Finishes | PCB prototypes can be customized with a wide range of surface finishes |
Temperature Resistance | PCB prototypes can be made with high-temperature materials for extreme environments |
Wireless Connectivity | PCB prototypes can incorporate wireless connectivity options |
Embedded Antennas | PCB prototypes can be manufactured with embedded antennas |
Virtual Testing | PCB prototypes can be simulated and tested virtually before manufacturing |
Importance | PCB prototypes are essential for product development and innovation |
Frequently Asked Questions (FAQ)
1. How long does it typically take to manufacture a PCB prototype?
Depending on the complexity of the design and the manufacturer’s capabilities, PCB prototypes can be produced in as little as 24 hours, although more complex designs may take several days or even weeks.
2. Can PCB prototypes be made with eco-friendly materials?
Yes, some PCB prototype manufacturers offer biodegradable and other eco-friendly materials as alternatives to traditional PCB substrates, helping to reduce the environmental impact of electronics manufacturing.
3. What kind of advanced features can be incorporated into PCB prototypes?
PCB prototypes can incorporate a wide range of advanced features, including embedded components, flexible and stretchable materials, wireless connectivity, and embedded antennas, among others.
4. Are PCB prototypes only used for electronics applications?
No, while PCB prototypes are most commonly associated with electronics, they can also be used for a variety of other applications, such as creating unique jewelry, art installations, and even musical instruments.
5. How important are PCB prototypes for product development and innovation?
PCB prototypes are absolutely essential for product development and innovation in the electronics industry, allowing engineers and designers to quickly and easily test and refine their ideas, leading to faster progress and more breakthroughs.
In conclusion, PCB prototypes are a fascinating and essential part of the electronics industry, with a wide range of surprising and impressive capabilities. From incredible speed and precision to advanced features and eco-friendly materials, PCB prototypes offer designers and engineers an invaluable tool for bringing their ideas to life and pushing the boundaries of what’s possible with electronics. By understanding these 12 insane but true things about PCB prototypes, professionals and enthusiasts alike can better appreciate the crucial role they play in driving innovation and progress in the world of electronics.
0 Comments