Introduction to PCB Surface Finishes
Printed Circuit Boards (PCBs) are essential components in modern electronic devices. They provide a reliable and efficient means of connecting electronic components and ensuring proper functionality. One crucial aspect of PCB manufacturing is the surface finish, which plays a vital role in protecting the copper traces, enhancing solderability, and improving the overall performance and longevity of the PCB.
In this comprehensive article, we will explore the various types of PCB Prototype surface finishes, their characteristics, advantages, and applications. We will also discuss the factors to consider when selecting the appropriate surface finish for your PCB project.
What is a PCB Surface Finish?
A PCB surface finish is a coating applied to the exposed copper traces and pads on a printed circuit board. Its primary purpose is to prevent oxidation and corrosion of the copper, which can degrade the electrical conductivity and solderability of the PCB. Additionally, surface finishes provide a suitable surface for component assembly and enhance the aesthetic appeal of the PCB.
Importance of Choosing the Right Surface Finish
Selecting the appropriate surface finish for your PCB prototype is crucial for several reasons:
-
Protection: Surface finishes protect the copper traces from oxidation and corrosion, ensuring the long-term reliability of the PCB.
-
Solderability: Different surface finishes have varying levels of solderability, which affects the ease and quality of component assembly.
-
Compatibility: The choice of surface finish should be compatible with the components, soldering process, and operating environment of the PCB.
-
Cost: Surface finishes vary in cost, and choosing the right one can help optimize the overall cost of PCB manufacturing.
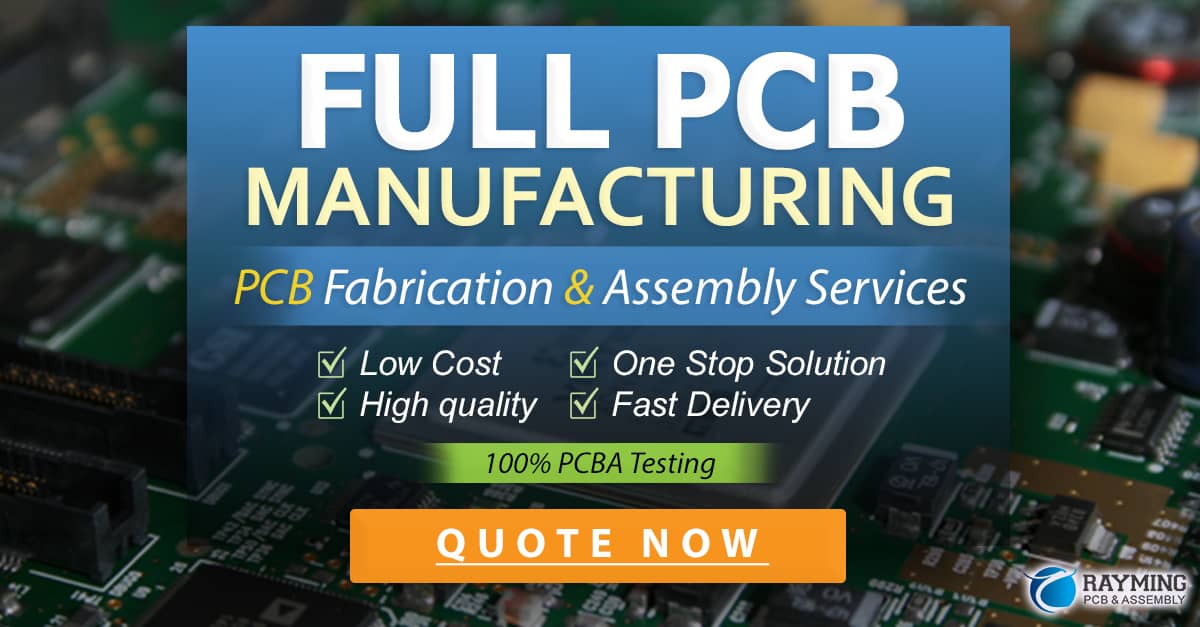
Types of PCB Surface Finishes
There are several types of PCB surface finishes available, each with its own characteristics, advantages, and limitations. Let’s explore the most common ones:
1. Hot Air Solder Leveling (HASL)
HASL is one of the most widely used surface finishes in the PCB industry. It involves dipping the PCB into a molten solder bath and then using hot air to level the solder on the surface. The resulting finish provides excellent solderability and protection against oxidation.
Advantages of HASL:
- Cost-effective
- Good solderability
- Suitable for through-hole and surface mount components
- Widely available and well-established process
Disadvantages of HASL:
- Uneven surface due to solder dipping process
- Not suitable for fine-pitch components
- Potential for Solder Bridging and shorts
- Limited shelf life due to solder oxidation
2. Electroless Nickel Immersion Gold (ENIG)
ENIG is a popular choice for high-reliability applications. It consists of an electroless nickel layer deposited on the copper, followed by a thin immersion gold layer. The nickel provides excellent corrosion resistance, while the gold offers superior solderability and protection against oxidation.
Advantages of ENIG:
- Flat and uniform surface finish
- Excellent solderability and wettability
- Suitable for fine-pitch components
- Long shelf life and storage stability
- Good corrosion resistance
Disadvantages of ENIG:
- Higher cost compared to HASL
- Potential for “black pad” defect due to nickel corrosion
- Gold can dissolve into solder during assembly, affecting joint reliability
3. Immersion Silver (IAg)
Immersion silver is a cost-effective alternative to ENIG. It involves the deposition of a thin layer of silver directly onto the copper surface. Silver provides excellent solderability and conductivity while offering protection against oxidation.
Advantages of IAg:
- Cost-effective compared to ENIG
- Good solderability and wettability
- Flat and uniform surface finish
- Suitable for fine-pitch components
- Faster deposition process compared to ENIG
Disadvantages of IAg:
- Limited shelf life due to silver tarnishing
- Potential for silver migration and dendrite growth
- Not suitable for high-temperature applications
4. Immersion Tin (ISn)
Immersion tin is another cost-effective surface finish option. It involves the deposition of a thin layer of tin directly onto the copper surface. Tin provides good solderability and protection against oxidation.
Advantages of ISn:
- Cost-effective
- Good solderability and wettability
- Flat and uniform surface finish
- Suitable for fine-pitch components
- Faster deposition process compared to ENIG
Disadvantages of ISn:
- Limited shelf life due to tin oxidation
- Potential for Tin Whiskers, which can cause short circuits
- Not suitable for high-temperature applications
5. Organic Solderability Preservative (OSP)
OSP is a chemical coating applied to the copper surface to prevent oxidation and enhance solderability. It is a thin, transparent layer that does not significantly affect the dimensions of the PCB.
Advantages of OSP:
- Cost-effective
- Flat and uniform surface finish
- Suitable for fine-pitch components
- Environmentally friendly (no heavy metals)
- Easily removable during soldering
Disadvantages of OSP:
- Limited shelf life due to coating degradation
- Potential for poor solderability if not stored properly
- Not suitable for multiple soldering cycles
- Requires careful handling to avoid contamination
Factors to Consider When Choosing a Surface Finish
When selecting a surface finish for your PCB prototype, consider the following factors:
-
Application requirements: Consider the specific requirements of your application, such as operating environment, temperature range, and reliability expectations.
-
Component compatibility: Ensure that the chosen surface finish is compatible with the components and assembly process used in your PCB.
-
Cost: Evaluate the cost implications of different surface finishes and select one that balances performance and budget constraints.
-
Shelf life: Consider the expected shelf life of your PCB and choose a surface finish that provides adequate protection and stability over the desired period.
-
Solderability: Assess the solderability requirements of your PCB and select a surface finish that offers good wettability and solder joint reliability.
-
Manufacturing capabilities: Ensure that your chosen PCB Manufacturer has the capability and expertise to apply the desired surface finish consistently and reliably.
Comparison Table of PCB Surface Finishes
Surface Finish | Solderability | Shelf Life | Cost | Suitable for Fine-Pitch | RoHS Compliant |
---|---|---|---|---|---|
HASL | Good | Limited | Low | No | Yes |
ENIG | Excellent | Long | High | Yes | Yes |
IAg | Good | Limited | Moderate | Yes | Yes |
ISn | Good | Limited | Low | Yes | Yes |
OSP | Good | Limited | Low | Yes | Yes |
Frequently Asked Questions (FAQ)
-
Q: What is the most cost-effective PCB surface finish?
A: Hot Air Solder Leveling (HASL) and Organic Solderability Preservative (OSP) are generally the most cost-effective surface finishes for PCBs. -
Q: Which surface finish is best for high-reliability applications?
A: Electroless Nickel Immersion Gold (ENIG) is often preferred for high-reliability applications due to its excellent corrosion resistance and long shelf life. -
Q: Can I use immersion silver for high-temperature applications?
A: Immersion silver is not recommended for high-temperature applications as it has limitations in terms of temperature stability and potential for silver migration. -
Q: How long does the OSP surface finish last?
A: The shelf life of OSP is limited and typically ranges from 6 to 12 months, depending on storage conditions and handling. -
Q: Is HASL suitable for fine-pitch components?
A: HASL is not ideal for fine-pitch components due to its uneven surface finish resulting from the solder dipping process. ENIG, IAg, or ISn are better choices for fine-pitch applications.
Conclusion
Selecting the appropriate surface finish for your PCB prototype is crucial for ensuring the reliability, solderability, and longevity of your electronic device. Each surface finish has its own advantages and limitations, and the choice depends on various factors such as application requirements, component compatibility, cost, and manufacturing capabilities.
By understanding the characteristics of different surface finishes and considering the specific needs of your project, you can make an informed decision that optimizes the performance and cost-effectiveness of your PCB prototype.
At RAYPCB, we offer a wide range of PCB surface finishes to cater to diverse customer requirements. Our experienced team can guide you in selecting the most suitable surface finish for your project and ensure the highest quality standards in PCB manufacturing. Contact us today to discuss your PCB prototype needs and leverage our expertise in delivering reliable and cost-effective solutions.
0 Comments