Introduction to PCB Surface Finish
When it comes to designing and manufacturing Printed Circuit Boards (PCBs), selecting the appropriate surface finish is a crucial decision. The surface finish not only protects the copper traces and pads from oxidation and corrosion but also ensures reliable solderability and enhances the overall performance of the PCB. With a variety of surface finish options available, it’s essential to understand their characteristics, advantages, and limitations to make an informed choice based on your specific project requirements.
In this comprehensive article, we’ll dive deep into the world of PCB surface finishes, exploring the most common types, their properties, and their suitability for different applications. By the end of this article, you’ll have a solid understanding of how to select the right surface finish for your PCB, ensuring optimal performance and reliability.
The Importance of PCB Surface Finish
Protection against Oxidation and Corrosion
One of the primary functions of a PCB surface finish is to protect the exposed copper traces and pads from oxidation and corrosion. Copper, being a highly reactive metal, tends to oxidize quickly when exposed to air and moisture. This oxidation process can lead to the formation of a non-conductive layer on the surface of the copper, which can hinder solderability and cause reliability issues.
A properly applied surface finish acts as a barrier between the copper and the environment, preventing oxidation and corrosion. This protection is crucial for maintaining the integrity of the PCB and ensuring long-term reliability, especially in harsh environmental conditions.
Enhancing Solderability
Another key role of PCB surface finish is to enhance the solderability of the copper pads and traces. Solderability refers to the ability of a surface to be wetted by molten solder and form a reliable solder joint. A good surface finish should provide a clean, flat, and uniform surface that promotes optimal solder wetting and minimizes the formation of defects such as solder bridges, voids, or poor adhesion.
Different surface finishes have varying levels of solderability, depending on their composition, thickness, and compatibility with the solder alloy used. Choosing a surface finish with excellent solderability characteristics ensures reliable and consistent solder joints, reducing the risk of manufacturing defects and improving the overall quality of the PCB Assembly.
Compatibility with Assembly Processes
The choice of PCB surface finish also depends on the specific assembly processes and requirements of your project. Different surface finishes have varying levels of compatibility with different soldering techniques, such as reflow soldering, Wave Soldering, or hand soldering. Some surface finishes may require additional processing steps or have specific handling requirements to ensure optimal results.
For example, some surface finishes, such as Immersion Silver (IAg) or Electroless Nickel Immersion Gold (ENIG), are more suitable for fine-pitch components and high-density layouts due to their flat and uniform surface. Others, like Hot Air Solder Leveling (HASL), may be more suitable for through-hole components and larger pitch sizes.
Considering the compatibility of the surface finish with your assembly processes and components is essential to avoid potential issues during manufacturing and ensure a smooth and efficient assembly process.
Common Types of PCB Surface Finish
Now that we understand the importance of PCB surface finish let’s explore some of the most common types available in the industry.
1. Hot Air Solder Leveling (HASL)
HASL is one of the most widely used PCB surface finishes, known for its cost-effectiveness and excellent solderability. In this process, the PCB is dipped into a molten solder bath, typically consisting of a tin-lead alloy (SnPb) or a lead-free alternative (SN100C or SAC305). The excess solder is then blown off using hot air knives, leaving a thin, uniform layer of solder on the copper pads and through-holes.
Advantages:
– Cost-effective and widely available
– Excellent solderability and wetting properties
– Suitable for both through-hole and surface mount components
– Good shelf life and resistance to oxidation
Disadvantages:
– Uneven surface due to solder buildup on pads and through-holes
– Potential for solder bridges or shorts in fine-pitch designs
– Limited compatibility with lead-free assembly processes
– Thermal shock during the HASL process may cause PCB Warpage
2. Electroless Nickel Immersion Gold (ENIG)
ENIG is a popular choice for high-reliability applications and fine-pitch designs. This two-layer surface finish consists of an electroless nickel plating followed by a thin immersion gold coating. The nickel layer provides a barrier against copper diffusion and enhances the durability of the surface, while the gold layer protects the nickel from oxidation and ensures excellent solderability.
Advantages:
– Flat and uniform surface, suitable for fine-pitch components
– Excellent solderability and wetting properties
– Good shelf life and resistance to oxidation
– Compatible with both lead-free and leaded assembly processes
– Suitable for Wire Bonding and press-fit connections
Disadvantages:
– Higher cost compared to HASL
– Potential for “black pad” issue due to improper plating processes
– Thicker nickel layer may cause stress on the PCB substrate
– Gold Embrittlement may occur if the gold layer is too thick
3. Immersion Silver (IAg)
Immersion Silver is a cost-effective alternative to ENIG, offering excellent solderability and a flat surface finish. In this process, a thin layer of silver is chemically deposited onto the copper surface through an immersion plating process. The silver layer provides protection against oxidation and ensures good solderability.
Advantages:
– Cost-effective compared to ENIG
– Flat and uniform surface, suitable for fine-pitch components
– Excellent solderability and wetting properties
– Compatible with both lead-free and leaded assembly processes
– Suitable for press-fit connections
Disadvantages:
– Limited shelf life due to silver tarnishing over time
– Potential for silver migration in high-humidity environments
– May require additional handling and packaging precautions
– Not suitable for wire bonding applications
4. Organic Solderability Preservative (OSP)
OSP is a chemical coating that is applied to the copper surface to protect it from oxidation and enhance solderability. The organic compounds in OSP form a thin, transparent layer on the copper, which is activated during the soldering process, allowing the solder to wet the surface effectively.
Advantages:
– Cost-effective and simple process
– Flat and uniform surface, suitable for fine-pitch components
– Good solderability and wetting properties
– Compatible with both lead-free and leaded assembly processes
– Environmentally friendly and RoHS compliant
Disadvantages:
– Limited shelf life due to the gradual degradation of the OSP coating
– Potential for poor solderability if the OSP coating is too thin or unevenly applied
– May require additional cleaning steps before assembly
– Not suitable for multiple reflow cycles or rework processes
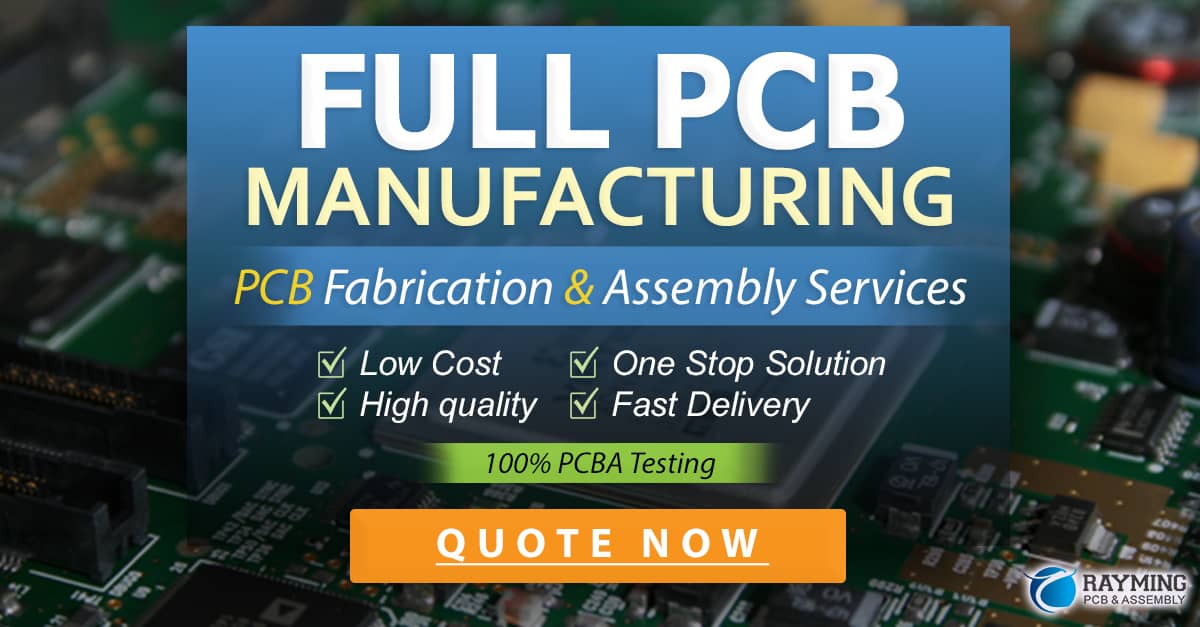
Factors to Consider When Selecting a PCB Surface Finish
Choosing the right PCB surface finish depends on several factors, including the specific requirements of your project, the assembly processes involved, and the environmental conditions the PCB will be exposed to. Here are some key factors to consider when making your decision:
- Application and Environment
- Consider the end-use application of the PCB and the environmental conditions it will be subjected to.
- For harsh environments, such as high humidity, extreme temperatures, or corrosive atmospheres, choose a surface finish with robust protection against oxidation and corrosion, like ENIG or IAg.
-
For general-purpose applications in controlled environments, cost-effective options like HASL or OSP may be sufficient.
-
Component Types and Pitch
- Take into account the types of components used in your design and their pitch (spacing between leads).
- For fine-pitch components, such as Ball Grid Arrays (BGAs) or Quad Flat Packages (QFPs), a flat and uniform surface finish like ENIG or IAg is recommended to ensure proper solder joint formation.
-
For through-hole components and larger pitch sizes, HASL can be a suitable and cost-effective option.
-
Assembly Processes
- Consider the assembly processes involved, such as reflow soldering, wave soldering, or hand soldering.
- Some surface finishes, like ENIG or IAg, are compatible with a wide range of assembly processes, including lead-free and leaded soldering.
-
Others, like OSP, may have limitations in terms of multiple reflow cycles or rework processes.
-
Shelf Life and Storage
- Evaluate the expected shelf life of your PCB and the storage conditions it will be subjected to.
- Surface finishes like ENIG and HASL have longer shelf life and are less sensitive to storage conditions.
-
IAg and OSP have limited shelf life due to tarnishing or degradation over time and may require additional handling and packaging precautions.
-
Cost and Availability
- Consider the cost implications of different surface finishes and their availability from your PCB manufacturer.
- HASL and OSP are generally more cost-effective options, while ENIG and IAg may have higher costs associated with the additional processing steps involved.
- Discuss the availability and lead times of different surface finishes with your PCB manufacturer to ensure they align with your project timeline and budget.
Comparison of PCB Surface Finishes
To help you make an informed decision, here’s a comparison table summarizing the key characteristics of the common PCB surface finishes:
Surface Finish | Solderability | Flatness | Shelf Life | Cost | Compatibility |
---|---|---|---|---|---|
HASL | Excellent | Poor | Long | Low | Leaded and lead-free |
ENIG | Excellent | Excellent | Long | High | Leaded and lead-free |
IAg | Excellent | Excellent | Limited | Medium | Leaded and lead-free |
OSP | Good | Excellent | Limited | Low | Leaded and lead-free |
FAQ
- What is the most cost-effective PCB surface finish?
-
HASL and OSP are generally the most cost-effective PCB surface finishes, as they involve fewer processing steps and materials compared to ENIG or IAg.
-
Which surface finish is best for fine-pitch components?
-
ENIG and IAg are recommended for fine-pitch components due to their flat and uniform surface, which ensures proper solder joint formation and minimizes the risk of solder bridges or shorts.
-
Can I use HASL for lead-free assembly processes?
-
While HASL can be used for lead-free assembly processes, it may require additional process control and optimization to ensure compatibility and reliability. Lead-free HASL alternatives, such as SN100C or SAC305, are available for lead-free assembly processes.
-
How long can I store PCBs with IAg or OSP surface finish?
-
The shelf life of PCBs with IAg or OSP surface finish is limited due to the potential for tarnishing or degradation over time. It is recommended to use these PCBs within 6 to 12 months of manufacture and store them in a controlled environment with low humidity and temperature.
-
Is ENIG suitable for wire bonding applications?
- Yes, ENIG is suitable for wire bonding applications due to its flat surface and good bondability. The gold layer provides a suitable surface for wire bonding, ensuring reliable and stable connections.
Conclusion
Selecting the right surface finish for your PCB is a critical decision that impacts the reliability, solderability, and overall performance of your electronic device. By understanding the characteristics, advantages, and limitations of common surface finishes like HASL, ENIG, IAg, and OSP, you can make an informed choice based on your specific project requirements and constraints.
Consider factors such as the application environment, component types and pitch, assembly processes, shelf life, and cost when evaluating different surface finish options. Engage with your PCB manufacturer to discuss your requirements and seek their expertise in recommending the most suitable surface finish for your project.
By carefully selecting the appropriate PCB surface finish, you can ensure optimal protection against oxidation and corrosion, enhance solderability, and achieve reliable and high-quality PCB assembly. This, in turn, contributes to the overall success and longevity of your electronic product.
0 Comments