What is PCB Warpage?
PCB warpage is a common issue in the electronics manufacturing industry where a printed circuit board (PCB) experiences an unintended alteration of its shape, resulting in a non-flat or distorted board. This deformation can occur during various stages of the PCB manufacturing process, such as lamination, solder mask application, or soldering of components. PCB warpage can lead to several problems, including difficulties in component assembly, reduced reliability, and even complete failure of the electronic device.
Types of PCB Warpage
There are two main types of PCB warpage:
-
Concave Warpage: In this type of warpage, the edges of the PCB curve upwards, while the center of the board remains flat or slightly depressed. This is also known as “dish” or “smile” warpage.
-
Convex Warpage: Convex warpage is the opposite of concave warpage, where the edges of the PCB curve downwards, and the center of the board is raised. This type of warpage is also referred to as “dome” or “frown” warpage.
Type of Warpage | Description |
---|---|
Concave | Edges curve upwards, center remains flat or slightly depressed |
Convex | Edges curve downwards, center is raised |
Causes of PCB Warpage
Several factors can contribute to PCB warpage, including:
1. Material Selection
The choice of materials used in the construction of a PCB can significantly impact its susceptibility to warpage. The most common materials used in PCBs are:
- FR-4: A glass-reinforced epoxy laminate, which is the most widely used material for PCBs due to its excellent electrical and mechanical properties.
- Polyimide: A high-temperature resistant material used in applications that require enhanced thermal stability.
- Ceramic: Used in high-frequency and high-power applications due to its excellent electrical and thermal properties.
Each material has different thermal expansion coefficients (CTE), which can lead to warpage when subjected to temperature changes during the manufacturing process or in the final application.
2. Copper Distribution
The distribution of copper on a PCB can also contribute to warpage. When copper is unevenly distributed across the board, it can cause unbalanced stresses, leading to deformation. This is particularly common in boards with high-density layouts or those with large copper pour areas.
3. Lamination Process
The lamination process, which involves bonding the layers of a PCB together under high pressure and temperature, can also cause warpage. If the pressure or temperature is not uniform across the board, or if there are variations in the thickness of the layers, it can result in uneven stresses and subsequent warpage.
4. Soldering Process
During the soldering process, the PCB is subjected to high temperatures, which can cause the board to expand and contract. If the soldering temperature is too high or if there are uneven heating or cooling rates, it can lead to warpage.
Effects of PCB Warpage
PCB warpage can have several detrimental effects on the performance and reliability of electronic devices:
1. Component Placement Difficulties
Warped PCBs can make it challenging to place components accurately on the board. Surface-mount components, in particular, require a flat surface for proper placement and soldering. If the board is warped, components may not sit flush against the surface, leading to poor solder joints or even complete failure to attach.
2. Solder Joint Reliability
Even if components are successfully placed on a warped PCB, the solder joints may be compromised. Warpage can cause uneven solder distribution or insufficient solder contact, resulting in weak or unreliable joints. This can lead to intermittent connections, increased resistance, or even complete joint failure.
3. Mechanical Stress
A warped PCB can experience increased mechanical stress, particularly when subjected to vibration or thermal cycling. This stress can cause solder joints to crack or components to detach from the board, leading to device failure.
4. Reduced Thermal Dissipation
When a PCB is warped, it may not make proper contact with heatsinks or other thermal management solutions. This can result in reduced heat dissipation, leading to increased operating temperatures and potential thermal damage to components.
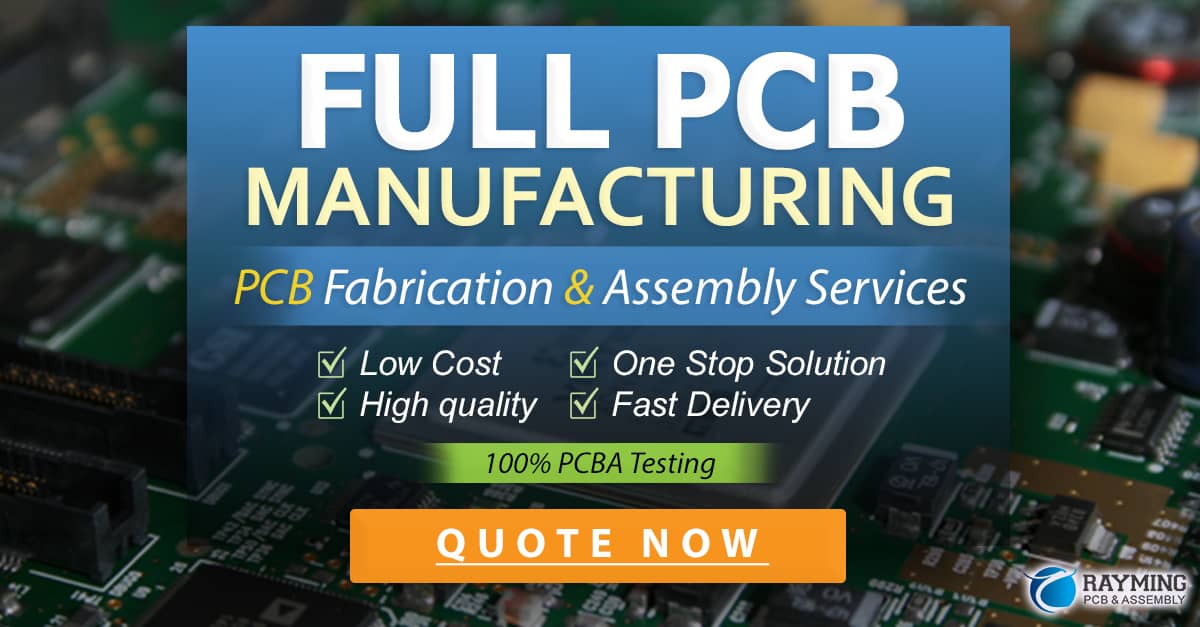
Prevention and Mitigation of PCB Warpage
To minimize the risk of PCB warpage, several strategies can be employed during the design and manufacturing process:
1. Material Selection
Choosing materials with similar CTEs can help reduce the likelihood of warpage. When using dissimilar materials, it is essential to consider their thermal properties and design the board accordingly. For example, using a low-CTE core material with high-CTE outer layers can help balance the stresses and minimize warpage.
2. Symmetrical Copper Distribution
Designing the PCB with a symmetrical copper distribution can help balance the stresses across the board. This can be achieved by using similar copper pour areas on both sides of the board and avoiding large, isolated copper regions.
3. Optimized Lamination Process
Ensuring that the lamination process is well-controlled and consistent can help reduce warpage. This involves maintaining uniform pressure and temperature across the board and using press pads or cushions to distribute the pressure evenly.
4. Controlled Soldering Process
To minimize warpage during soldering, it is essential to control the temperature profile and ensure even heating and cooling rates. Using a gradual ramp-up and ramp-down of temperature can help reduce thermal shock and minimize stress on the board.
5. Design for Manufacturability
Incorporating design for manufacturability (DFM) principles can help reduce the risk of warpage. This includes using standard board sizes and thicknesses, avoiding abrupt changes in copper density, and providing adequate support for large components.
Frequently Asked Questions (FAQ)
-
What is the difference between concave and convex PCB warpage?
Concave warpage, also known as “dish” or “smile” warpage, occurs when the edges of the PCB curve upwards, while the center remains flat or slightly depressed. Convex warpage, also referred to as “dome” or “frown” warpage, is the opposite, with the edges curving downwards and the center of the board raised. -
Can PCB warpage be completely eliminated?
While it may not be possible to eliminate PCB warpage completely, it can be minimized through careful design, material selection, and process control. Employing strategies such as symmetrical copper distribution, optimized lamination, and controlled soldering can significantly reduce the risk of warpage. -
How does PCB warpage affect component placement?
Warped PCBs can make it difficult to place components accurately, particularly surface-mount components that require a flat surface for proper placement and soldering. If the board is warped, components may not sit flush against the surface, leading to poor solder joints or even complete failure to attach. -
What role does material selection play in PCB warpage?
The choice of materials used in the construction of a PCB can significantly impact its susceptibility to warpage. Different materials have varying thermal expansion coefficients (CTE), which can lead to warpage when subjected to temperature changes. Choosing materials with similar CTEs or using a combination of low-CTE core materials and high-CTE outer layers can help minimize warpage. -
How can PCB designers mitigate the risk of warpage?
PCB designers can mitigate the risk of warpage by incorporating design for manufacturability (DFM) principles, such as using standard board sizes and thicknesses, avoiding abrupt changes in copper density, and providing adequate support for large components. Additionally, designing the board with symmetrical copper distribution and considering the thermal properties of materials can help reduce the likelihood of warpage.
0 Comments