What is PCB Warpage?
PCB warpage is a common issue in the manufacturing process of printed circuit boards (PCBs). It refers to the deformation or bending of the PCB, which can cause various problems in the assembly and functionality of the final product. PCB warpage can occur due to several factors, including material properties, manufacturing processes, and environmental conditions.
Causes of PCB Warpage
1. Material Properties
The choice of materials used in PCB fabrication can significantly impact the likelihood of warpage. Some of the material-related factors that contribute to PCB warpage include:
1.1. Coefficient of Thermal Expansion (CTE) Mismatch
When the CTE of the PCB substrate and the components mounted on it differ significantly, it can lead to warpage during the heating and cooling processes. The mismatch in thermal expansion rates creates stress within the PCB, causing it to bend or warp.
1.2. Moisture Absorption
Certain PCB materials, such as FR-4, are hygroscopic, meaning they tend to absorb moisture from the environment. When these materials are exposed to high temperatures during the reflow soldering process, the absorbed moisture vaporizes and expands, leading to warpage.
1.3. Glass Transition Temperature (Tg)
The glass transition temperature (Tg) is the temperature at which a material transitions from a rigid, glassy state to a more flexible, rubbery state. If the Tg of the PCB material is too low, it can soften and deform during the high-temperature processes, resulting in warpage.
2. Manufacturing Processes
The manufacturing processes involved in PCB fabrication can also contribute to warpage. Some of the process-related factors include:
2.1. Uneven Copper Distribution
If the copper traces on the PCB are not evenly distributed, it can create an imbalance in the thermal expansion and contraction of the board. This uneven distribution can lead to localized stress and warpage.
2.2. Improper Lamination
During the lamination process, multiple layers of the PCB are bonded together under high pressure and temperature. If the lamination parameters are not optimized, it can result in uneven bonding and stress distribution, causing warpage.
2.3. Rapid Cooling
After the reflow soldering process, if the PCB is cooled too quickly, it can create thermal shock and induce warpage. The rapid change in temperature causes the PCB materials to contract at different rates, leading to deformation.
3. Environmental Conditions
Environmental factors can also play a role in PCB warpage. These include:
3.1. Temperature Fluctuations
Exposure to extreme temperature fluctuations during storage, transportation, or operation can cause the PCB to expand and contract, leading to warpage.
3.2. Humidity
High humidity levels can accelerate the moisture absorption of hygroscopic PCB materials, increasing the risk of warpage during the reflow soldering process.
Effects of PCB Warpage
PCB warpage can have several negative effects on the functionality and reliability of the final product. Some of the consequences of PCB warpage include:
1. Component Misalignment
Warped PCBs can cause misalignment of surface-mounted components, leading to poor soldering and weak connections. This misalignment can result in reduced reliability and increased risk of failure.
2. Solder Joint Defects
When a PCB is warped, it can create uneven pressure on the solder joints during the reflow process. This uneven pressure can lead to solder joint defects, such as bridging, insufficient wetting, or cold joints, which can compromise the electrical and mechanical integrity of the connections.
3. Assembly Difficulties
Warped PCBs can pose challenges during the assembly process, particularly when using automated pick-and-place machines. The deformation of the PCB can cause the machine vision system to misinterpret the component placement locations, leading to misalignment and assembly errors.
4. Reduced Reliability
Warped PCBs are more susceptible to mechanical stress and vibration, which can lead to premature failure of the components and solder joints. The reduced reliability can result in increased warranty claims and customer dissatisfaction.
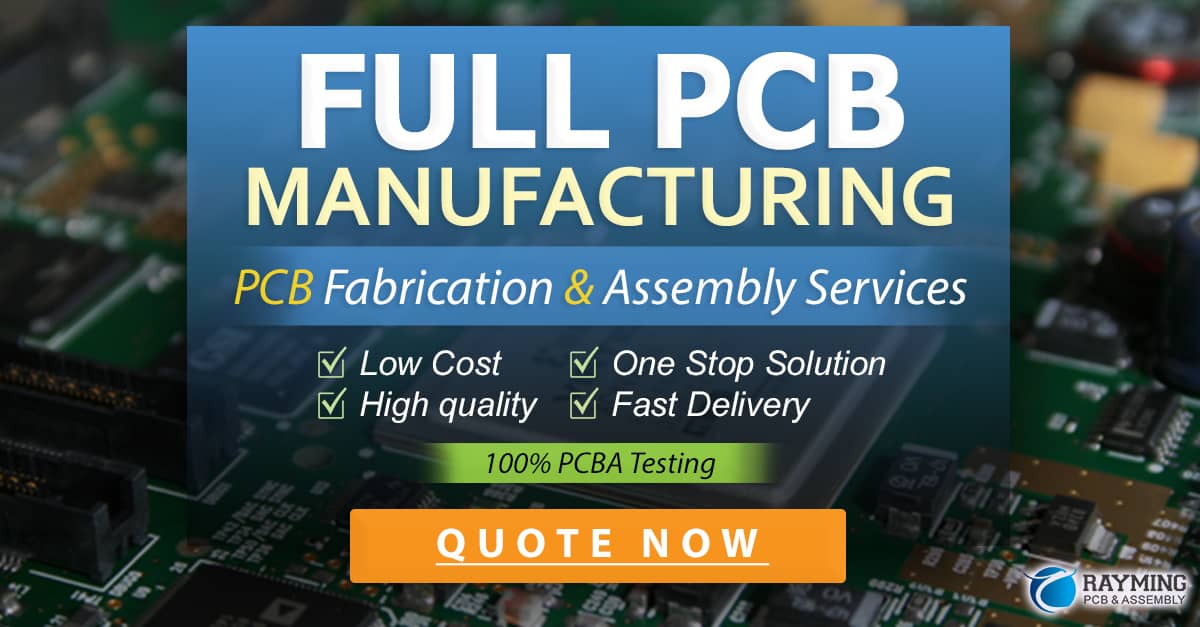
Measuring PCB Warpage
To effectively control and minimize PCB warpage, it is essential to measure and quantify the extent of deformation. Several methods can be used to measure PCB warpage, including:
1. 3D Scanning
3D scanning techniques, such as structured light scanning or laser scanning, can create a detailed digital model of the PCB surface. By comparing the scanned model to the ideal, flat surface, the warpage can be quantified and visualized.
2. Shadow Moiré
Shadow moiré is an optical measurement method that uses a grating and a light source to project a shadow pattern onto the PCB surface. The distortion of the shadow pattern indicates the presence and extent of warpage.
3. Coordinate Measuring Machine (CMM)
A coordinate measuring machine (CMM) can be used to precisely measure the height and flatness of the PCB at various points. By comparing the measured values to the nominal dimensions, the warpage can be calculated.
Method | Advantages | Disadvantages |
---|---|---|
3D Scanning | High accuracy, detailed visualization | Expensive equipment, data processing |
Shadow Moiré | Non-contact, fast measurement | Limited resolution, sensitive to noise |
CMM | High precision, versatile | Slow measurement, contact-based |
Preventing and Treating PCB Warpage
To minimize the occurrence and impact of PCB warpage, several preventive measures and treatment techniques can be employed:
1. Material Selection
Choosing PCB materials with similar CTEs and high Tg values can help reduce the risk of warpage. Using low-CTE substrates, such as polyimide or ceramic, can provide better dimensional stability.
2. Design Optimization
Optimizing the PCB design to ensure even copper distribution and minimizing the use of large, unsupported copper areas can help prevent warpage. Incorporating balanced copper pours and using copper thieving techniques can improve the thermal and mechanical stability of the PCB.
3. Process Control
Strict control of the manufacturing processes, including lamination parameters, reflow profiles, and cooling rates, can help minimize warpage. Optimizing the reflow profile to reduce thermal stress and ensuring gradual cooling can prevent rapid dimensional changes.
4. Moisture Management
Proper storage and handling of PCBs to minimize moisture absorption can reduce the risk of warpage during the reflow process. Baking the PCBs before assembly to remove absorbed moisture can help prevent deformation.
5. Mechanical Support
Using stiffeners or support structures to reinforce the PCB can help minimize warpage, particularly for large or thin boards. Attaching the PCB to a rigid frame or using localized stiffeners in high-stress areas can improve the dimensional stability.
6. Warpage Compensation
In some cases, the PCB design can be modified to compensate for the expected warpage. By predicting the warpage pattern through simulation or empirical data, the PCB layout can be adjusted to counteract the deformation, ensuring proper component alignment after the reflow process.
Frequently Asked Questions (FAQ)
1. What is the most common cause of PCB warpage?
The most common cause of PCB warpage is the mismatch in the coefficient of thermal expansion (CTE) between the PCB substrate and the components mounted on it. This mismatch creates stress within the PCB during the heating and cooling processes, leading to deformation.
2. How can I measure the extent of PCB warpage?
Several methods can be used to measure PCB warpage, including 3D scanning, shadow moiré, and coordinate measuring machines (CMMs). These techniques provide quantitative data on the deformation of the PCB surface, allowing for accurate assessment and comparison.
3. Can PCB warpage be completely eliminated?
While it may not be possible to completely eliminate PCB warpage, it can be minimized through proper material selection, design optimization, process control, and preventive measures. By understanding the causes of warpage and implementing appropriate strategies, the impact of warpage can be significantly reduced.
4. What are the consequences of PCB warpage?
PCB warpage can lead to various problems, including component misalignment, solder joint defects, assembly difficulties, and reduced reliability. These issues can compromise the functionality and durability of the final product, resulting in increased failure rates and customer dissatisfaction.
5. How can I prevent PCB warpage during the manufacturing process?
To prevent PCB warpage during manufacturing, several measures can be taken, such as:
– Choosing PCB materials with similar CTEs and high Tg values
– Optimizing the PCB design for even copper distribution
– Controlling the lamination parameters and reflow profiles
– Managing moisture absorption through proper storage and handling
– Using mechanical supports or stiffeners to reinforce the PCB
By implementing these preventive measures, the risk of PCB warpage can be significantly reduced, ensuring better quality and reliability of the final product.
Conclusion
PCB warpage is a complex issue that can have significant implications for the quality, reliability, and functionality of electronic devices. By understanding the causes, effects, and measurement techniques of PCB warpage, manufacturers can take proactive steps to minimize its occurrence and impact.
Through careful material selection, design optimization, process control, and preventive measures, the risk of PCB warpage can be effectively managed. Implementing best practices in PCB fabrication and assembly can help ensure the production of high-quality, reliable products that meet the demands of today’s increasingly complex electronic systems.
As technology continues to advance and the demand for smaller, more intricate PCBs grows, addressing the challenge of PCB warpage will remain a critical priority for the electronics industry. By staying informed about the latest developments in materials, manufacturing processes, and quality control techniques, PCB manufacturers can stay ahead of the curve and deliver products that exceed customer expectations.
0 Comments