What are PCB CNC Machines?
PCB CNC machines are computer-controlled devices designed specifically for the manufacturing of printed circuit boards. These machines utilize precise and automated processes to drill holes, route traces, and perform other essential tasks in the PCB Fabrication process. CNC machines have revolutionized the way PCBs are manufactured, offering high precision, speed, and consistency compared to traditional manual methods.
Types of PCB CNC Machines
There are several types of PCB CNC machines, each designed for specific tasks in the PCB manufacturing process. Some of the most common types include:
-
Drilling Machines: These machines are used to drill holes in PCBs for component placement and interconnections. They can drill hundreds or even thousands of holes per minute with exceptional accuracy.
-
Routing Machines: PCB routing machines are used to create the intricate traces and paths that connect components on the board. They use high-speed spindles and specialized cutting tools to remove unwanted copper from the PCB substrate.
-
V-Scoring Machines: V-scoring machines create precise V-shaped grooves on the PCB, allowing for easy separation of individual boards from a larger panel.
-
Depaneling Machines: After the PCBs are fabricated, depaneling machines are used to separate the individual boards from the larger panel. These machines ensure clean and precise cuts without damaging the components or traces.
Advantages of PCB CNC Machines
The use of CNC machines in PCB manufacturing offers several significant advantages over traditional manual methods. Some of the key benefits include:
-
Precision and Accuracy: CNC machines are capable of producing PCBs with extremely high precision and accuracy. They can drill holes and route traces with tolerances as small as a few microns, ensuring the proper functioning of the final product.
-
Increased Efficiency: CNC machines can work continuously without breaks, significantly reducing the time required for PCB fabrication. They can handle complex designs and large-scale production with ease, improving overall manufacturing efficiency.
-
Consistency and Repeatability: With CNC machines, every PCB produced is identical to the previous one. This consistency and repeatability are crucial in electronics manufacturing, where even minor variations can lead to device malfunctions.
-
Cost-Effectiveness: Although the initial investment in PCB CNC machines may be higher compared to manual methods, the long-term cost savings are significant. CNC machines reduce labor costs, minimize material waste, and increase production speed, resulting in a more cost-effective manufacturing process.
High-Tech Features of Modern PCB CNC Machines
As technology advances, PCB CNC machines are becoming more sophisticated and feature-rich. Some of the cutting-edge technologies and features found in modern PCB CNC machines include:
-
Multi-Spindle Drilling: Advanced drilling machines now come equipped with multiple spindles, allowing for simultaneous drilling of multiple holes. This feature greatly enhances the speed and efficiency of the drilling process.
-
Automatic Tool Changers: CNC machines with automatic tool changers can switch between different drilling bits or routing tools without manual intervention. This feature reduces setup time and increases overall productivity.
-
Vision Systems: Some PCB CNC machines incorporate vision systems that can inspect the board for defects, align the board accurately, and even perform quality control checks in real-time. These systems ensure the highest level of precision and minimize human error.
-
Dust Collection Systems: To maintain a clean and safe work environment, modern PCB CNC machines often include built-in dust collection systems. These systems effectively remove debris and dust generated during the drilling and routing processes, preventing contamination and ensuring the longevity of the machine.
-
Integration with CAD/CAM Software: CNC machines can be seamlessly integrated with Computer-Aided Design (CAD) and Computer-Aided Manufacturing (CAM) software. This integration allows for the direct transfer of design files to the machine, streamlining the manufacturing process and reducing the chances of errors.
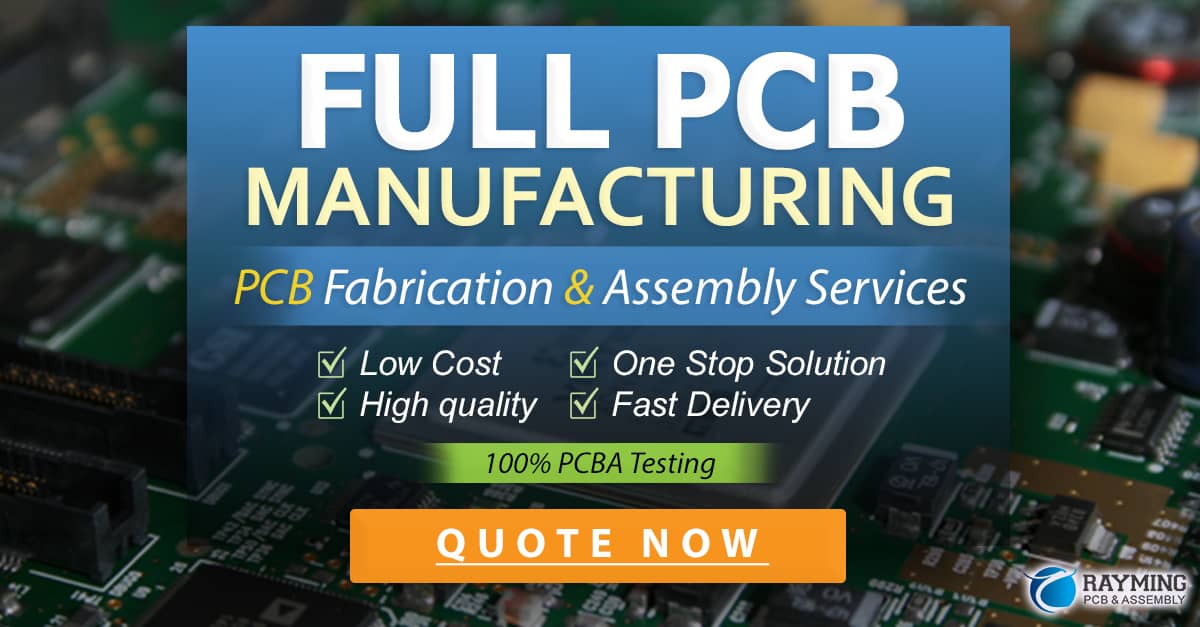
Applications of PCB CNC Machines
PCB CNC machines find applications across various industries and sectors where electronic devices are manufactured. Some of the key areas where these machines are extensively used include:
-
Consumer Electronics: From smartphones and laptops to smart home devices and wearables, PCB CNC machines play a vital role in the production of consumer electronics. The high precision and speed offered by these machines enable the mass production of complex PCBs for these devices.
-
Automotive Industry: Modern vehicles are equipped with numerous electronic systems, such as infotainment systems, sensors, and control units. PCB CNC machines are used to manufacture the PCBs that form the backbone of these electronic components, ensuring reliable and efficient performance.
-
Medical Devices: Medical devices, including diagnostic equipment, monitoring systems, and implantable devices, rely on high-quality PCBs for their functionality. PCB CNC machines are essential in producing the intricate and reliable PCBs required for these life-critical applications.
-
Aerospace and Defense: The aerospace and defense industries demand PCBs that can withstand extreme conditions and meet stringent reliability standards. PCB CNC machines are used to fabricate high-performance PCBs for avionics, communication systems, and other critical applications in these sectors.
-
Industrial Automation: As industries move towards automation and the Internet of Things (IoT), PCBs play a crucial role in connecting sensors, actuators, and control systems. PCB CNC machines are employed to manufacture the PCBs that enable seamless communication and control in industrial automation setups.
Industry | Applications |
---|---|
Consumer Electronics | Smartphones, laptops, smart home devices, wearables |
Automotive | Infotainment systems, sensors, control units |
Medical Devices | Diagnostic equipment, monitoring systems, implantable devices |
Aerospace and Defense | Avionics, communication systems, critical applications |
Industrial Automation | Sensors, actuators, control systems, IoT devices |
Frequently Asked Questions (FAQ)
-
What is the difference between a PCB CNC machine and a regular CNC machine?
A PCB CNC machine is specifically designed for the manufacturing of printed circuit boards. It is equipped with features and tools optimized for PCB fabrication, such as high-speed spindles, automatic tool changers, and vision systems. Regular CNC machines, on the other hand, are more versatile and can be used for machining various materials, including metals, plastics, and wood. -
How long does it take to manufacture a PCB using a CNC machine?
The time required to manufacture a PCB using a CNC machine depends on several factors, such as the complexity of the design, the size of the board, and the capabilities of the machine. On average, a simple PCB can be produced in a matter of minutes, while more complex designs may take several hours. However, CNC machines significantly reduce the overall manufacturing time compared to manual methods. -
Can PCB CNC machines handle Multilayer PCBs?
Yes, modern PCB CNC machines are capable of handling multilayer PCBs. These machines can drill through multiple layers of the PCB stack and create precise interconnections between the layers. The advanced features and tools of PCB CNC machines enable the fabrication of complex multilayer boards with high accuracy and reliability. -
What is the typical accuracy of a PCB CNC machine?
The accuracy of a PCB CNC machine depends on the specific model and its capabilities. High-end machines can achieve accuracies in the range of a few microns (typically ±10 microns or better). This level of accuracy is essential for manufacturing high-density PCBs with fine pitch components and intricate trace patterns. -
How often do PCB CNC machines require maintenance?
Regular maintenance is crucial to ensure the optimal performance and longevity of PCB CNC machines. The frequency of maintenance depends on factors such as the machine’s usage, the type of materials being processed, and the operating environment. Generally, PCB CNC machines require daily cleaning and lubrication, along with periodic checks and calibration. Manufacturers typically provide detailed maintenance schedules and guidelines to keep the machines running smoothly and minimize downtime.
Conclusion
PCB CNC machines have revolutionized the electronics manufacturing industry, offering high precision, speed, and consistency in the production of printed circuit boards. These machines have become indispensable tools for fabricating PCBs across various industries, from consumer electronics and automotive to medical devices and aerospace.
As technology continues to advance, PCB CNC machines are becoming more sophisticated, incorporating features like multi-spindle drilling, automatic tool changers, vision systems, and seamless integration with CAD/CAM software. These advancements further enhance the capabilities and efficiency of PCB manufacturing, enabling the production of increasingly complex and high-performance electronic devices.
Investing in PCB CNC machines not only improves the quality and reliability of PCBs but also offers significant cost savings and increased productivity in the long run. As the demand for electronic devices continues to grow, the role of PCB CNC machines in shaping the future of electronics manufacturing becomes ever more crucial.
By embracing the latest advancements in PCB CNC technology, manufacturers can stay ahead of the curve, meet the evolving needs of various industries, and contribute to the development of cutting-edge electronic solutions that shape our world.
0 Comments