Introduction to PCB Manufacturing in China
China has emerged as a global leader in the production of printed circuit boards (PCBs), with a thriving industry that offers high-quality products at competitive prices. PCB manufacturing in China has experienced remarkable growth over the past few decades, thanks to the country’s vast resources, skilled workforce, and favorable government policies. In this article, we will explore the various aspects of PCB manufacturing in China, including its history, current state, and future prospects.
The Rise of PCB Manufacturing in China
The PCB industry in China has its roots in the 1980s, when the country began to open up its economy and attract foreign investment. Initially, the industry was small and focused mainly on low-end products. However, as China’s economy grew and its manufacturing capabilities improved, the PCB industry began to expand rapidly.
In the 1990s, the Chinese government implemented a series of policies to support the development of the electronics industry, including tax incentives and subsidies for manufacturers. This helped to attract more foreign investment and encouraged the growth of the PCB industry.
By the early 2000s, China had become a major player in the global PCB market, with a large number of manufacturers located in the Pearl River Delta region of Guangdong Province. Today, China is the world’s largest producer of PCBs, accounting for over 50% of global production.
Advantages of PCB Manufacturing in China
There are several reasons why China has become such a popular destination for PCB manufacturing:
-
Lower Costs: Labor costs in China are significantly lower than in many other countries, which allows manufacturers to offer competitive prices for their products.
-
Skilled Workforce: China has a large pool of skilled workers with experience in electronics manufacturing, which helps to ensure high-quality production.
-
Advanced Technology: Chinese PCB Manufacturers have invested heavily in advanced manufacturing technologies, such as high-density interconnect (HDI) and flexible printed circuits (FPCs), which allows them to produce complex, high-performance products.
-
Extensive Supply Chain: China has a well-developed supply chain for electronics manufacturing, with a wide range of suppliers for raw materials, components, and equipment.
-
Government Support: The Chinese government has implemented policies to support the development of the electronics industry, including tax incentives and subsidies for manufacturers.
Types of PCBs Manufactured in China
Chinese PCB manufacturers offer a wide range of products to meet the needs of different industries and applications. Some of the most common types of PCBs manufactured in China include:
Single-sided PCBs
Single-sided PCBs have conductive traces on only one side of the board. They are the simplest and most cost-effective type of PCB, and are often used in low-complexity applications such as toys and simple electronics.
Double-sided PCBs
Double-sided PCBs have conductive traces on both sides of the board, which allows for higher circuit density and more complex designs. They are commonly used in consumer electronics, automotive electronics, and industrial control systems.
Multi-layer PCBs
Multi-layer PCBs have multiple layers of conductive traces separated by insulating layers. They offer the highest circuit density and performance, and are used in high-end applications such as smartphones, computers, and aerospace systems. Chinese manufacturers have the capability to produce multi-layer PCBs with up to 60 layers.
Flexible PCBs
Flexible PCBs are made from flexible materials such as polyimide or polyester, which allows them to bend and fold without damaging the circuits. They are commonly used in applications where space is limited or where the PCB needs to conform to a curved surface, such as in wearable devices and medical equipment.
Rigid-flex PCBs
Rigid-Flex PCBs combine the benefits of both rigid and flexible PCBs, with rigid sections for mounting components and flexible sections for connecting them. They offer improved reliability and design flexibility compared to traditional PCBs, and are often used in aerospace, military, and medical applications.
PCB Manufacturing Process in China
The PCB manufacturing process in China typically involves the following steps:
-
Design: The PCB design is created using computer-aided design (CAD) software, which generates the necessary files for manufacturing.
-
Material Selection: The appropriate materials for the PCB, such as the substrate, copper foil, and solder mask, are selected based on the specific requirements of the application.
-
Patterning: The desired circuit pattern is transferred onto the PCB substrate using a photolithographic process, which involves applying a photoresist coating, exposing it to UV light through a patterned mask, and developing the exposed areas.
-
Etching: The unwanted copper is removed from the PCB using a chemical etching process, leaving only the desired circuit pattern.
-
Drilling: Holes are drilled in the PCB to allow for the mounting of components and the creation of vias (connections between layers).
-
Plating: The holes and exposed copper areas are plated with a conductive material, such as copper or gold, to improve conductivity and protect against corrosion.
-
Solder Mask Application: A layer of solder mask is applied to the PCB to protect the copper traces and prevent solder bridges during assembly.
-
Silkscreen Printing: Labels and other markings are printed onto the PCB using a silkscreen printing process.
-
Surface Finishing: A surface finish, such as HASL (hot air solder leveling) or ENIG (electroless nickel immersion gold), is applied to the exposed copper areas to improve solderability and protect against oxidation.
-
Electrical Testing: The completed PCB is tested for electrical continuity and functionality to ensure that it meets the required specifications.
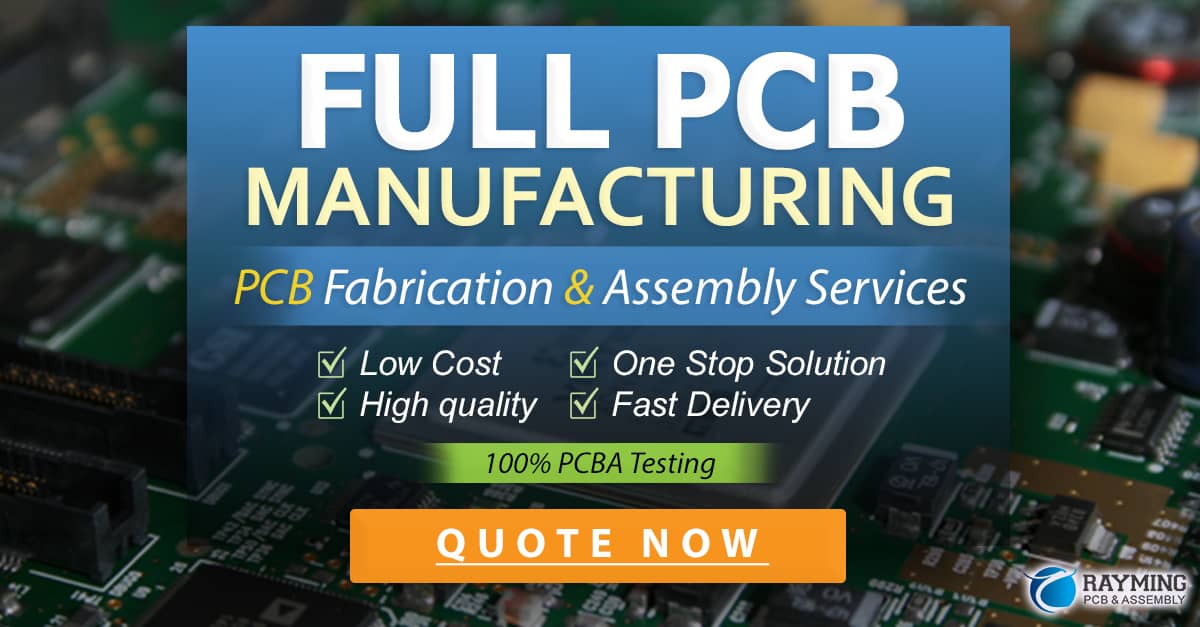
Quality Control in Chinese PCB Manufacturing
Quality control is a critical aspect of PCB manufacturing, and Chinese manufacturers have implemented strict quality control measures to ensure that their products meet the highest standards. Some of the key quality control measures used in Chinese PCB manufacturing include:
Incoming Material Inspection
All incoming materials, such as substrates, copper foil, and solder masks, are carefully inspected to ensure that they meet the required specifications and are free from defects.
In-Process Inspection
During the manufacturing process, various in-process inspections are carried out to ensure that each step is completed correctly and that the PCB meets the required quality standards.
Automated Optical Inspection (AOI)
AOI systems are used to automatically inspect the PCB for defects such as shorts, opens, and misalignments. This helps to catch defects early in the manufacturing process and reduce the risk of costly rework or scrap.
Electrical Testing
As mentioned earlier, the completed PCB is subjected to electrical testing to ensure that it functions correctly and meets the required specifications. This includes continuity testing, insulation resistance testing, and functional testing.
Certification and Compliance
Many Chinese PCB manufacturers are certified to international quality standards such as ISO 9001, ISO 14001, and UL. They also comply with various environmental and safety regulations, such as RoHS (Restriction of Hazardous Substances) and REACH (Registration, Evaluation, Authorization, and Restriction of Chemicals).
Choosing a PCB Manufacturer in China
With so many PCB manufacturers to choose from in China, it can be challenging to find the right one for your needs. Here are some factors to consider when choosing a PCB manufacturer in China:
Experience and Expertise
Look for a manufacturer with a proven track record of producing high-quality PCBs for a variety of applications. They should have experience in manufacturing the specific type of PCB you require, whether it’s a single-sided, double-sided, multi-layer, or flexible PCB.
Manufacturing Capabilities
Make sure the manufacturer has the necessary equipment and technology to produce your PCBs to the required specifications. This includes advanced manufacturing processes such as HDI and FPC, as well as the ability to handle complex designs and high-volume production.
Quality Control
As mentioned earlier, quality control is critical in PCB manufacturing. Look for a manufacturer with a robust quality control system in place, including incoming material inspection, in-process inspection, AOI, and electrical testing.
Certifications and Compliance
Choose a manufacturer that is certified to international quality standards and complies with relevant environmental and safety regulations. This will help to ensure that your PCBs meet the necessary requirements for your target market.
Customer Service and Support
Look for a manufacturer with responsive and knowledgeable customer service and support. They should be able to answer your questions, provide technical assistance, and help you troubleshoot any issues that may arise during the manufacturing process.
Price and Lead Time
While price is an important consideration, it should not be the only factor in your decision. Look for a manufacturer that offers competitive prices without compromising on quality or lead time. Make sure they can deliver your PCBs within the required timeframe and have the capacity to handle your order volume.
The Future of PCB Manufacturing in China
Despite the challenges posed by the COVID-19 pandemic and global economic uncertainty, the outlook for PCB manufacturing in China remains positive. The country’s strong manufacturing capabilities, extensive supply chain, and supportive government policies are expected to continue driving growth in the industry.
One of the key trends in Chinese PCB manufacturing is the increasing adoption of advanced technologies such as 5G, artificial intelligence (AI), and the Internet of Things (IoT). These technologies are driving demand for high-performance, high-density PCBs that can support faster data transmission and processing speeds.
Another trend is the growing focus on sustainability and environmental protection. Chinese PCB manufacturers are investing in eco-friendly materials and processes, such as halogen-free substrates and lead-free solders, to reduce their environmental impact and comply with increasingly stringent regulations.
Finally, the Chinese government’s “Made in China 2025” initiative, which aims to upgrade the country’s manufacturing capabilities and promote the development of high-tech industries, is expected to provide further support for the PCB industry. This includes investments in research and development, infrastructure, and talent development to help Chinese manufacturers stay at the forefront of technological innovation.
Frequently Asked Questions (FAQ)
-
What is the minimum order quantity (MOQ) for PCBs from Chinese manufacturers?
The minimum order quantity varies depending on the manufacturer and the specific type of PCB. Some manufacturers may have an MOQ as low as 50 pieces, while others may require a minimum of 500 or more pieces. -
How long does it take to receive PCBs from a Chinese manufacturer?
Lead times vary depending on the complexity of the PCB and the manufacturer’s production schedule. Typical lead times range from 1-2 weeks for standard PCBs to 4-6 weeks for more complex designs. -
Can Chinese PCB manufacturers handle small-volume, high-mix orders?
Yes, many Chinese PCB manufacturers have the flexibility to handle small-volume, high-mix orders. However, the price per unit may be higher for smaller orders due to the higher setup costs. -
What file formats are required for PCB manufacturing in China?
Most Chinese PCB manufacturers accept Gerber files, which are the industry standard for PCB design. Other common file formats include ODB++, IPC-2581, and DXF. -
How can I ensure the quality of PCBs from a Chinese manufacturer?
To ensure the quality of PCBs from a Chinese manufacturer, look for a manufacturer with a robust quality control system in place, including incoming material inspection, in-process inspection, AOI, and electrical testing. Choose a manufacturer that is certified to international quality standards and complies with relevant environmental and safety regulations. It’s also a good idea to request samples before placing a large order to verify the quality of the PCBs.
Conclusion
PCB manufacturing in China has come a long way in recent decades, and the country has established itself as a global leader in the industry. With its vast resources, skilled workforce, and advanced manufacturing capabilities, China offers a compelling value proposition for companies looking to source high-quality PCBs at competitive prices.
When choosing a PCB manufacturer in China, it’s important to consider factors such as experience and expertise, manufacturing capabilities, quality control, certifications and compliance, customer service and support, and price and lead time. By carefully evaluating these factors and selecting a reputable manufacturer, companies can ensure that they receive the highest quality PCBs for their needs.
Looking to the future, PCB manufacturing in China is well-positioned to continue its growth and innovation, driven by the increasing adoption of advanced technologies, the growing focus on sustainability and environmental protection, and the supportive policies of the Chinese government. As the industry evolves and adapts to new challenges and opportunities, Chinese PCB manufacturers will undoubtedly play a key role in shaping the future of electronics manufacturing.
Type of PCB | Layers | Applications |
---|---|---|
Single-sided | 1 | Low-complexity applications (e.g. toys, simple electronics) |
Double-sided | 2 | Consumer electronics, automotive, industrial control systems |
Multi-layer | 4-60 | High-end applications (e.g. smartphones, computers, aerospace) |
Flexible | 1-2 | Wearable devices, medical equipment, space-constrained applications |
Rigid-Flex | Varies | Aerospace, military, medical applications |
Table 1: Common Types of PCBs Manufactured in China
Quality Control Measure | Description |
---|---|
Incoming Material Inspection | Inspection of incoming materials for defects and specifications |
In-Process Inspection | Inspection of each manufacturing step for quality and accuracy |
Automated Optical Inspection (AOI) | Automated inspection for defects such as shorts, opens, and misalignments |
Electrical Testing | Testing for electrical continuity, insulation resistance, and functionality |
Certification and Compliance | Compliance with international quality standards and regulations |
Table 2: Quality Control Measures in Chinese PCB Manufacturing
0 Comments