Surface mount technology (SMT) revolutionized the electronics assembly industry by enabling the manufacture of smaller, lighter, and more reliable products. SMT production lines feature state-of-the-art equipment for high-speed component placement and soldering. However, without proper planning and optimization, even the most advanced SMT lines will underperform. This article examines key strategies for optimizing every stage of the SMT production process.
Component Storage and Feeding
SMT components must be stored and presented to pick-and-place machines in an orderly fashion to prevent jams and minimize changeover time.
Tape and Reel
The most common format is tape and reel. Components are packed in paper or plastic embossed tapes that are wound onto reels. Tape and reel provides:
- Protection from mechanical shock and contamination
- Controlled presentation of components to pick-and-place nozzles
- Flexibility to accommodate different component sizes
Stick Magazines
Some larger components like connectors and ICs are delivered in stick magazines. These long tubes have compartments lined up in a row. Stick mags also protect components and enable reliable feeding.
Tray Storage
Trays are used to store and transport medium-sized parts like quad flat packs (QFP) and small outline ICs (SOIC). Trays provide organization but usually require additional processing to singulate components.
Storage Racks and Towers
Tapes, sticks, and trays are housed in storage racks and towers located close to pick-and-place machines. Proper storage avoids:
- Component jams
- Nozzle crashes
- Feeder calibration issues
PCB Handling Systems
The PCB handling system transports boards between processes and holds them securely during assembly. Key elements include:
Conveyors
Overhead conveyors move boards between machines. They should provide:
- Adjustable speed
- Minimal vibration
- ESD-safe transport
Rail Guides
Guide rails keep PCBs aligned and prevent skewing. Different board sizes require rail adjustments.
Clamps
Board clamps securely hold PCBs in place during component placement and soldering. Different clamping mechanisms suit various board sizes and types.
Buffers
First-in-first-out (FIFO) buffers help absorb variations in line throughput. Buffer capacity should match production demand. Overflow buffers prevent bottlenecks.
Pick-and-Place Optimization
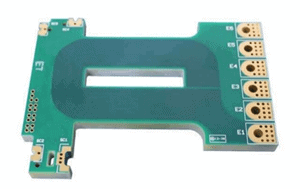
Pick-and-place machines position and mount components onto PCBs. They consist of:
- Feeders to supply components
- Nozzles to pick parts
- Gantry system to move components
- Vision systems to align parts
- Software to orchestrate operations
Key Factors
The following factors influence pick-and-place productivity and quality:
- Nozzle selection – The right nozzles avoid lifting and placement errors
- Feeder setup – Efficient feeder layout minimizes nozzle changes
- Component sequencing – Logical part chaining prevents excessive nozzle changes
- Pick-and-place algorithms – Optimization algorithms maximize machine performance
- Maintenance – Regular maintenance and calibration sustains accuracy
Proper nozzle selection, feeder setup, pick sequences, algorithms, and maintenance boosts machine throughput, uptime, and placement accuracy.
Reflow Oven Optimization
After component placement, boards pass through reflow ovens to solder parts. Reflow optimization focuses on:
Thermal Profiling
Each assembly requires a custom thermal profile that heats boards to form high-quality solder joints without damaging sensitive components. Profiling involves:
- Defining heating stages and target temperatures
- Selecting zones to achieve the thermal profile
- Adjusting conveyor speed to match heating needs
- Monitoring temperatures with thermocouples
- Tweaking settings until optimal results are achieved
Airflow and Exhaust
Reflow ovens contain a controlled atmosphere to prevent oxidation during soldering. Parameters include:
- Air exchange rate
- Laminar airflow to remove fumes
- Nitrogen levels to prevent oxidation
- Ventilation rate for proper exhaust
Settings must balance air quality with energy efficiency.
Maintenance
Regular maintenance preserves soldering performance. Tasks include:
- Cleaning heaters and fans
- Replacing worn conveyor belts
- Checking thermocouples and gas sensors
- Updating heating element coils
- Calibrating temperature uniformity
Effective maintenance sustain performance and product quality.
Inspection and Testing
Post-reflow inspection and testing verifies assembly quality:
AOI Inspection
Automated optical inspection (AOI) checks for defects like missing or misaligned components. Algorithms detect and classify errors for repair.
X-Ray Inspection
X-ray imaging finds hidden defects like poor solder joints, voids, or foreign objects. Operators analyze images to identify problems.
ICT Testing
In-circuit testing (ICT) validates board functionality by probing testpoints and verifying circuit continuity. Failed tests pinpoint faults.
Flying Probe Testing
Flying probe testers perform electrical testing without fixtures. They are flexible and suitable for low-volume runs.
Inspection and testing provides vital feedback for optimizing the production line and improving yields.
Data Analysis and Control
Modern SMT lines feature sophisticated software to collect, analyze, and apply production data. Key capabilities include:
Traceability
Barcodes and data collection tracks boards and components through each process step. Genealogy data aids root cause analysis.
Data Mining
Statistical tools find trends and correlations in production data to guide optimization. Data mining helps identify issues and improvement opportunities.
Closed-Loop Control
Measurements and metrics are fed back to adjust feeders, pick-and-place parameters, reflow profiles, and inspection criteria. This creates a self-correcting system.
Change Management
Software controls updates to programs, bill of materials, and procedures. Change management prevents unauthorized modifications and enforces version control.
Overall Line Optimization
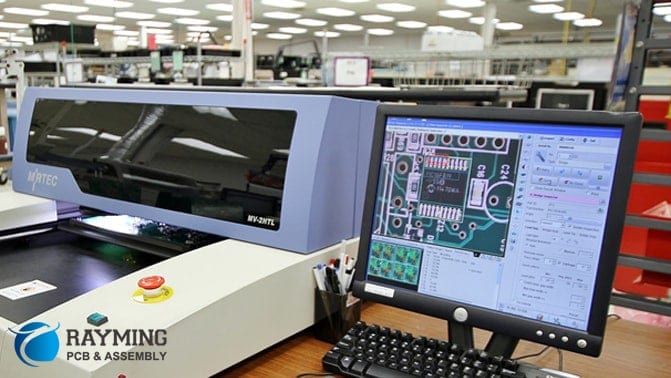
In addition to optimizing individual machines, overall line balancing helps maximize productivity. Steps include:
Takt Time Analysis
Takt time, the pace of production, sets the tempo for line operations. Processes should align with takt requirements.
Line Balancing
Work content and cycle times are balanced across machines to avoid bottlenecks. Buffer capacity provides flexibility.
Total Productive Maintenance (TPM)
TPM initiatives engage staff to maintain equipment, improve uptime, and meet cycle time targets. TPM fosters ownership.
Continuous Improvement
Regular kaizen events tap worker insights to enhance processes. Improvement goals connect to business objectives.
Optimized SMT lines achieve high throughput, uptime, quality, and yield to deliver maximum value and competitive advantage. A holistic systems view connects all elements into an efficient, high-performance production system.
Frequently Asked Questions
What are some challenges with optimizing SMT production lines?
Some common challenges include:
- Long changeover times between product variants
- Frequent pick-and-place nozzle crashes and jams
- High rework rates after soldering
- Difficulty balancing line throughput and inventory
- Lack of standardized procedures and settings
How can software analytics help optimize SMT lines?
Software analytics provides data-driven insights to guide SMT optimization:
- Traceability identifies high-failure processes or components
- Data mining reveals issues and correlations
- Closed-loop control applies metrics to automatically improve processes
- Statistical tools find optimization opportunities
Software gives the visibility needed for smart decision making.
What maintenance is required on SMT lines?
Regular maintenance activities on SMT lines include:
- Cleaning conveyors, nozzles, and filters
- Lubricating moving parts
- Replacing worn clamp belts and conveyor belts
- Checking calibration of pick-and-place accuracy
- Updating heating elements and thermocouples
- Testing power supplies and servos
Maintenance sustains performance, prevents breakdowns, and reduces unplanned downtime.
How can staff training help optimize SMT lines?
Proper training enables staff to:
- Set up machines correctly
- Identify potential issues
- Perform preventive maintenance
- Analyze data and root causes
- Continuously improve processes
Skilled teams are essential for optimizing processes and sharing best practices.
What are some key soldering defects to monitor?
Typical soldering defects requiring monitoring include:
- Insufficient solder and cold joints
- Solder blobs and bridges
- Solder voids or porosity
- Solder balls or splatter
- Charred or burnt flux residue
- Delamination or cracked joints
Inspection and testing finds defects before they impact reliability or yields.
0 Comments