What is ODB++?
ODB++ is a file hierarchy format that contains all the necessary information required for PCB fabrication, assembly, and testing. It is an open format, meaning that it is not proprietary to any specific CAD or CAM system, allowing for seamless data exchange between different software tools.
The ODB++ Format consists of a directory structure that organizes the various files and data related to a PCB design. This structure includes:
- Job file (.job)
- Board outline
- Layer stackup
- Copper layers
- Solder mask layers
- Silkscreen layers
- Drill and route data
- Netlist
- Component placement data
- and more
By encapsulating all this information in a standardized format, ODB++ simplifies the data transfer process and reduces the chances of errors or data loss.
Benefits of Using ODB++
There are several key advantages to using the ODB++ format for PCB data exchange:
-
Standardization: ODB++ provides a consistent and standardized way of organizing and transferring PCB design data, reducing the need for manual data manipulation and minimizing the risk of errors.
-
Efficiency: By consolidating all the necessary data into a single file hierarchy, ODB++ streamlines the data transfer process, saving time and effort for both designers and manufacturers.
-
Compatibility: As an open format, ODB++ is compatible with a wide range of CAD and CAM systems, allowing for seamless integration into existing workflows.
-
Accuracy: ODB++ maintains the integrity of the original design data, ensuring that the manufactured PCB matches the designer’s intent.
-
Support for complex designs: The format is capable of handling advanced PCB features such as embedded components, HDI (High Density Interconnect), and rigid-Flex Designs.
ODB++ File Structure
The ODB++ file hierarchy consists of several key components, each serving a specific purpose in the PCB fabrication process. Here’s an overview of the main elements:
Job File (.job)
The job file is the top-level file in the ODB++ hierarchy and serves as a manifest for all the other files in the structure. It contains information about the PCB design, such as the board size, layer stackup, and general manufacturing requirements.
Board Outline
The board outline file defines the physical shape and dimensions of the PCB. It is typically in a vector format, such as Gerber or DXF, and includes any cutouts, slots, or other mechanical features.
Layer Stackup
The layer stackup file describes the arrangement of copper layers, insulating layers, and any special materials used in the PCB Construction. It includes information such as layer thicknesses, material types, and dielectric constants.
Copper Layers
Each copper layer in the PCB design is represented by a separate file in the ODB++ hierarchy. These files contain the actual trace and pad geometry for each layer, as well as any copper pour or fill areas.
Solder Mask Layers
Solder mask layers are used to protect the copper traces and pads from oxidation and prevent solder bridges during assembly. The ODB++ format includes separate files for the top and bottom solder mask layers, specifying the openings in the mask where components will be soldered.
Silkscreen Layers
Silkscreen layers are used for applying text, logos, and other markings to the PCB surface. The ODB++ hierarchy includes separate files for the top and bottom silkscreen layers, containing the artwork in a vector format.
Drill and Route Data
The drill and route data files specify the locations and sizes of holes to be drilled in the PCB, as well as any slots or cutouts that need to be routed or milled. This information is critical for the fabrication process and is typically provided in Excellon format for drills and Gerber or DXF format for routing.
Netlist
The netlist file contains the electrical connectivity information for the PCB design, specifying which components are connected to which nets. This data is used for both PCB fabrication and assembly, ensuring that the manufactured board matches the original design intent.
Component Placement Data
The component placement file provides the locations and orientations of all components on the PCB. This information is essential for automated assembly processes and is typically provided in a standard format such as IPC-D-356 or ODB++.
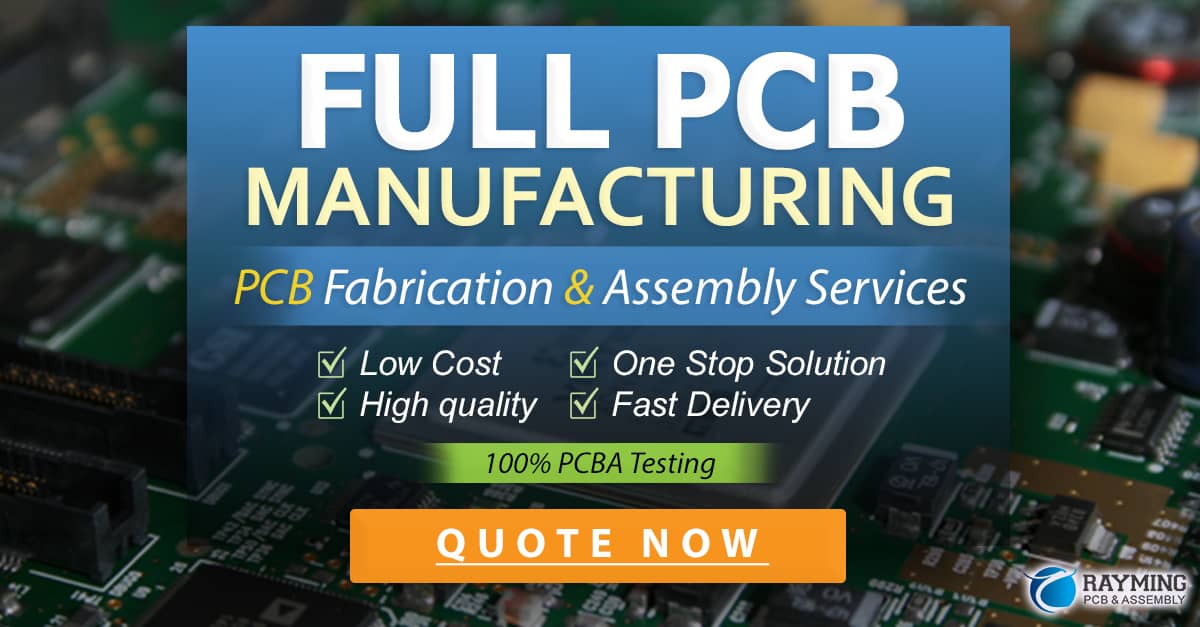
Advantages of ODB++ over Traditional Gerber Files
Traditionally, PCB design data was exchanged using Gerber files, which are a set of 2D vector files representing different layers and aspects of the PCB design. While Gerber files are still widely used, ODB++ offers several advantages:
-
Single file hierarchy: ODB++ consolidates all the design data into a single file structure, making it easier to manage and transfer compared to multiple Gerber files.
-
Intelligent data: ODB++ files contain more than just graphical data; they also include information about the logical structure of the design, such as netlist and component data, making the format more intelligent and comprehensive.
-
Improved error detection: The structured nature of ODB++ allows for better error detection and prevention during data transfer and processing.
-
Support for advanced features: ODB++ is better equipped to handle complex PCB designs with features such as embedded components, HDI, and rigid-flex constructions.
Implementing ODB++ in Your Workflow
To start using ODB++ in your PCB design and manufacturing workflow, follow these steps:
-
Verify CAD support: Check if your PCB design software supports exporting to the ODB++ format. Most modern CAD tools, such as Altium Designer, Cadence Allegro, and Mentor Graphics PADS, have built-in ODB++ export capabilities.
-
Configure export settings: Set up your CAD software to export the necessary layers and data in the ODB++ format. This may involve selecting specific layers, defining drill and route parameters, and specifying the desired output directory.
-
Generate ODB++ files: Once your export settings are configured, generate the ODB++ files from your PCB design software. This process will create the complete ODB++ file hierarchy, including the job file, layer data, and all associated files.
-
Verify and validate: Before sending the ODB++ data to your manufacturing partner, it’s essential to verify and validate the exported files. Use ODB++ viewer software to check the integrity of the data and ensure that all layers and features are correctly represented.
-
Collaborate with your manufacturer: Work closely with your PCB manufacturing partner to ensure they can process ODB++ data and to discuss any specific requirements or considerations for your design.
By implementing ODB++ in your workflow, you can streamline the data exchange process, reduce the risk of errors, and improve the overall efficiency of your PCB design and manufacturing pipeline.
Best Practices for Working with ODB++
To get the most out of the ODB++ format and ensure smooth data exchange and manufacturing processes, consider the following best practices:
-
Use a consistent naming convention: Establish a clear and consistent naming convention for your ODB++ files and directories to avoid confusion and ensure easy identification of the data.
-
Include all necessary data: Make sure to include all the required data in your ODB++ export, such as the complete layer stackup, drill and route information, and component placement data.
-
Communicate with your manufacturer: Maintain open communication with your PCB manufacturing partner to discuss any specific requirements, constraints, or preferences they may have regarding ODB++ data.
-
Perform thorough verification: Always verify and validate your ODB++ files before sending them to your manufacturer. Use ODB++ viewer software to check for any errors, inconsistencies, or missing data.
-
Keep your CAD software updated: Ensure that you are using the latest version of your PCB design software and any relevant ODB++ export plugins to take advantage of the most recent features and improvements.
-
Backup and archive: Regularly backup and archive your ODB++ data to protect against data loss and to maintain a historical record of your designs.
By following these best practices, you can ensure a smooth and efficient transition from PCB design to manufacturing using the ODB++ format.
FAQ
1. Is ODB++ compatible with all PCB design software?
Most modern PCB design software, such as Altium Designer, Cadence Allegro, and Mentor Graphics PADS, support exporting to the ODB++ format. However, it’s essential to verify the specific capabilities of your CAD tool and ensure that it can generate the necessary ODB++ files.
2. Can ODB++ handle complex PCB designs with advanced features?
Yes, ODB++ is designed to support complex PCB designs, including features such as embedded components, HDI (High Density Interconnect), and rigid-flex constructions. The format’s intelligent data structure and comprehensive file hierarchy enable it to capture and convey the intricacies of advanced PCB designs.
3. Is ODB++ an open format, or is it proprietary to specific software?
ODB++ is an open format, meaning that it is not proprietary to any specific CAD or CAM system. This openness allows for seamless data exchange between different software tools and ensures compatibility across various design and manufacturing environments.
4. How does ODB++ compare to traditional Gerber files?
ODB++ offers several advantages over traditional Gerber files, including a single file hierarchy, intelligent data structure, improved error detection, and support for advanced PCB features. While Gerber files are still widely used, ODB++ provides a more comprehensive and efficient solution for PCB data exchange.
5. What steps can I take to ensure successful data exchange with my PCB manufacturer using ODB++?
To ensure successful data exchange using ODB++, follow these key steps:
1. Verify that your CAD software supports ODB++ export and configure the export settings accordingly.
2. Generate the complete ODB++ file hierarchy, including all necessary layers and data.
3. Thoroughly verify and validate the exported ODB++ files using viewer software.
4. Communicate closely with your PCB manufacturer to discuss any specific requirements or considerations for your design.
5. Maintain consistent naming conventions, backup your data, and keep your CAD software updated to the latest version.
By adhering to these practices and leveraging the capabilities of the ODB++ format, you can streamline your PCB design and manufacturing process, reduce errors, and achieve high-quality results.
Conclusion
ODB++ has emerged as a vital standard for PCB data exchange, offering a comprehensive, efficient, and reliable solution for transferring design data from CAD to CAM systems. By adopting the ODB++ format in your PCB design and manufacturing workflow, you can:
- Streamline data exchange
- Reduce the risk of errors
- Support complex PCB designs
- Ensure compatibility between different software tools
- Improve overall efficiency and quality
As the electronics industry continues to evolve and PCB designs become increasingly complex, the importance of robust data exchange formats like ODB++ will only continue to grow. By understanding the capabilities and best practices associated with ODB++, PCB designers and manufacturers can position themselves for success in this dynamic and demanding field.
0 Comments