PCB Substrate Materials
The foundation of any PCB is its substrate material, which provides the base upon which the conductive traces and components are placed. The choice of substrate material is crucial, as it influences the PCB’s electrical properties, thermal stability, and mechanical strength. Some of the most common PCB substrate materials include:
FR-4
FR-4 is the most widely used PCB substrate material, composed of woven fiberglass cloth impregnated with epoxy resin. It offers excellent electrical insulation, mechanical stability, and resistance to moisture and heat. FR-4 is suitable for a wide range of applications, from consumer electronics to industrial control systems.
High-Frequency Materials
For PCBs operating at high frequencies, such as those found in RF and microwave applications, specialized substrate materials are employed. These materials, such as Rogers RO4000 series and Isola IS680, have low dielectric constants and low loss tangents, minimizing signal loss and ensuring optimal high-frequency performance.
Flexible Substrates
Flexible PCBs, often made from polyimide or polyester films, offer unique advantages in applications requiring bendability or conformity to irregular shapes. These substrates enable the creation of compact, lightweight, and flexible electronic devices, such as wearables and medical implants.
Substrate Material | Dielectric Constant | Loss Tangent | Thermal Conductivity (W/mK) |
---|---|---|---|
FR-4 | 4.5 | 0.02 | 0.3 |
Rogers RO4350B | 3.48 | 0.0037 | 0.62 |
Polyimide | 3.5 | 0.002 | 0.2 |
PCB Copper Layers and Thickness
The conductive traces on a PCB are formed by etching copper layers laminated onto the substrate material. The number of copper layers and their thickness play a significant role in the PCB’s current-carrying capacity, signal integrity, and manufacturing complexity.
Number of Layers
PCBs can have varying numbers of copper layers, ranging from single-sided boards (one layer) to multi-layer boards with dozens of layers. The choice of layer count depends on the complexity of the circuit, the required signal routing density, and the need for power and ground planes. Multi-layer PCBs offer improved signal integrity, reduced electromagnetic interference (EMI), and better thermal management compared to single or double-sided boards.
Copper Thickness
The thickness of the copper layers, typically measured in ounces per square foot (oz/ft²), determines the current-carrying capacity and resistance of the traces. Common copper thicknesses include:
- 0.5 oz/ft² (17.5 μm): Suitable for low-power, high-density designs
- 1 oz/ft² (35 μm): The most commonly used thickness, offering a balance between current capacity and ease of manufacturing
- 2 oz/ft² (70 μm): Used for high-current applications or to minimize voltage drop in power distribution networks
Copper Thickness (oz/ft²) | Thickness (μm) | Current Capacity (A/mm) |
---|---|---|
0.5 | 17.5 | 1.5 |
1 | 35 | 3.0 |
2 | 70 | 6.0 |
PCB Manufacturing Process
The manufacturing process of PCBs involves several critical steps that ensure the accurate formation of conductive traces, the reliable placement of components, and the overall quality of the finished board.
Etching
Etching is the process of selectively removing unwanted copper from the laminated substrate to form the desired conductive traces. The most common etching methods are:
- Subtractive Etching: The unwanted copper is chemically removed using etchants like ferric chloride or ammonium persulfate.
- Additive Etching: Copper is selectively deposited onto the substrate through electroplating or electroless plating, forming the desired traces.
Drilling and Plating
Holes are drilled through the PCB to accommodate through-hole components and to create vias, which electrically connect different layers of the board. The drilled holes are then plated with copper to ensure reliable electrical connections.
Solder Mask Application
A solder mask, typically a green or blue polymer layer, is applied over the copper traces, leaving only the exposed pads for component soldering. The solder mask protects the traces from oxidation, prevents solder bridges, and provides electrical insulation.
Silkscreen Printing
White silkscreen legends are printed onto the PCB to indicate component designators, polarity markers, and other essential information for assembly and troubleshooting.
Surface Finishing
A surface finish is applied to the exposed copper pads to prevent oxidation and enhance solderability. Common surface finishes include:
- Hot Air Solder Leveling (HASL): A tin-lead alloy is applied to the pads and leveled using hot air.
- Organic Solderability Preservative (OSP): A thin, organic coating is applied to the pads to prevent oxidation.
- Electroless Nickel Immersion Gold (ENIG): A layer of nickel is deposited onto the pads, followed by a thin layer of gold.
Surface Finish | Shelf Life | Solderability | Flatness |
---|---|---|---|
HASL | 12 months | Good | Fair |
OSP | 6 months | Fair | Good |
ENIG | 12+ months | Excellent | Excellent |
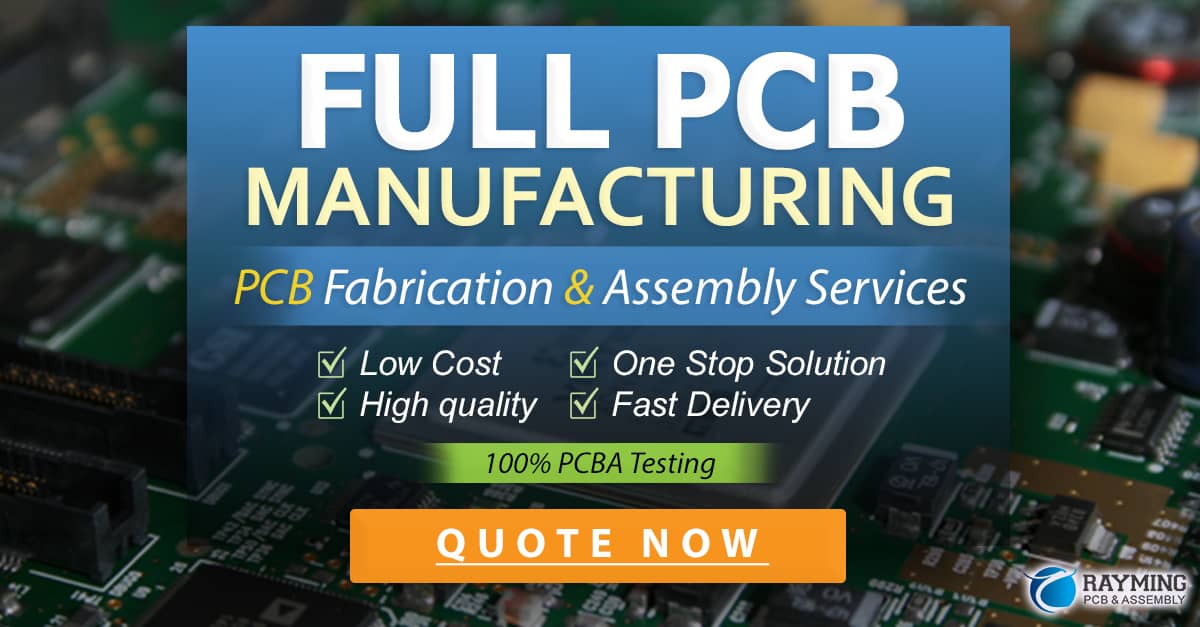
PCB Design Considerations
Effective PCB design is essential for ensuring the proper functionality, reliability, and manufacturability of the final product. Key design considerations include:
Component Placement
Components should be placed in a logical, organized manner, taking into account signal flow, thermal management, and mechanical constraints. Proper component placement minimizes signal path lengths, reduces EMI, and facilitates efficient assembly.
Signal Integrity
Maintaining signal integrity is crucial, especially in high-speed digital designs. Techniques such as controlled impedance routing, differential pair routing, and avoiding sharp trace corners help to minimize signal reflections, crosstalk, and EMI.
Power Distribution
A well-designed power distribution network is essential for providing clean, stable power to all components on the PCB. This involves the use of power and ground planes, decoupling capacitors, and proper trace sizing to minimize voltage drop and power supply noise.
Thermal Management
Effective thermal management ensures that components operate within their specified temperature ranges, preventing performance degradation and premature failure. Techniques such as the use of thermal vias, copper pours, and strategic component placement help to dissipate heat and maintain optimal operating temperatures.
Frequently Asked Questions (FAQ)
-
Q: What is the difference between a single-sided and a double-sided PCB?
A: A single-sided PCB has conductive traces on only one side of the substrate, while a double-sided PCB has traces on both sides. Double-sided PCBs offer higher component density and more design flexibility but are more complex to manufacture. -
Q: What is the purpose of vias in a PCB?
A: Vias are plated holes that electrically connect different layers of a multi-layer PCB. They allow signals to travel between layers, enabling more efficient routing and reducing the overall size of the board. -
Q: Why is a solder mask used on PCBs?
A: A solder mask serves several purposes: it protects the copper traces from oxidation, prevents solder bridges between closely spaced pads, and provides electrical insulation between components. Additionally, the solder mask gives the PCB its distinctive green or blue color. -
Q: What factors influence the choice of PCB substrate material?
A: The choice of PCB substrate material depends on several factors, including the intended application, operating frequency, environmental conditions, and budget. Factors such as the dielectric constant, loss tangent, thermal conductivity, and mechanical strength are considered when selecting the appropriate substrate material. -
Q: How does the number of copper layers affect PCB performance?
A: Increasing the number of copper layers in a PCB offers several benefits. It allows for higher component density, better signal routing, improved power distribution, and enhanced thermal management. However, adding more layers also increases the manufacturing complexity and cost of the PCB.
In conclusion, the construction of a printed circuit board involves a complex interplay of materials, manufacturing processes, and design considerations. By understanding the main factors in PCB Construction, engineers and designers can create high-quality, reliable, and efficient electronic devices that meet the ever-evolving demands of modern technology. From choosing the appropriate substrate material and copper thickness to implementing effective design techniques and selecting the right surface finish, each aspect of PCB construction contributes to the overall performance and longevity of the final product.
As technology continues to advance, the importance of well-constructed PCBs will only continue to grow. By staying informed about the latest developments in materials, manufacturing processes, and design methodologies, engineers and manufacturers can ensure that their PCBs remain at the forefront of innovation, powering the electronic devices that shape our world.
[Word count: 1656]
0 Comments