What is Medical PCB Assembly?
Medical PCB (printed circuit board) assembly refers to the process of assembling and manufacturing printed circuit boards specifically designed for use in medical devices and equipment. These PCBs must meet stringent quality, reliability, and regulatory standards to ensure the safety and effectiveness of the medical devices they are used in.
Medical PCBs are found in a wide range of medical applications, including:
- Diagnostic equipment (e.g., MRI machines, X-ray machines, ultrasound devices)
- Monitoring devices (e.g., patient monitors, ECG machines, pulse oximeters)
- Treatment equipment (e.g., pacemakers, defibrillators, infusion pumps)
- Surgical instruments (e.g., electrosurgical units, surgical robots)
- Laboratory equipment (e.g., blood analyzers, DNA sequencers, centrifuges)
The assembly process for medical PCBs is similar to that of other PCBs, but with added emphasis on cleanliness, precision, and traceability to meet the stringent requirements of the medical industry.
Key Differences Between Medical PCBs and Standard PCBs
Medical PCBs differ from standard PCBs in several key aspects:
-
Regulatory compliance: Medical PCBs must comply with various regulations and standards, such as the FDA’s Quality System Regulation (QSR) and ISO 13485, to ensure their safety and effectiveness.
-
Higher reliability requirements: Medical devices often perform critical functions, and their failure can have serious consequences. Therefore, medical PCBs must have higher reliability and longer lifespans compared to standard PCBs.
-
Cleanliness and contamination control: Medical PCBs must be manufactured in clean environments to minimize the risk of contamination, which could compromise the safety and performance of the medical device.
-
Traceability: Medical PCB Assembly requires extensive documentation and traceability to ensure that each component and process can be tracked throughout the product lifecycle.
-
Specialized components: Medical PCBs often use specialized components, such as high-precision sensors, miniaturized connectors, and biocompatible materials, to meet the unique requirements of medical applications.
The Medical PCB Assembly Process
The medical PCB assembly process typically involves the following steps:
1. Design and Prototyping
The first step in medical PCB assembly is designing the circuit board based on the specific requirements of the medical device. This involves creating schematic diagrams, selecting components, and laying out the board to optimize performance and manufacturability. Once the design is finalized, prototypes are built and tested to verify functionality and compliance with relevant standards.
2. Component Sourcing and Inspection
Components for medical PCBs must be sourced from reliable suppliers and undergo rigorous inspection to ensure their quality and authenticity. This includes verifying the components’ specifications, performing visual inspections, and conducting electrical tests. Counterfeit or substandard components can compromise the performance and safety of the medical device.
3. PCB Fabrication
The PCB fabrication process involves creating the bare circuit board based on the approved design. This typically involves the following steps:
- Printing the circuit pattern onto a copper-clad substrate using photoresist and etching techniques
- Drilling holes for through-hole components and vias
- Applying solder mask and silkscreen layers for insulation and labeling
- Performing electrical tests to verify the board’s integrity
4. Surface Mount Assembly (SMT)
Surface mount assembly involves attaching surface mount components to the PCB using automated pick-and-place machines and reflow soldering. The process typically follows these steps:
- Applying solder paste to the PCB pads using a stencil or screen printing
- Placing surface mount components onto the solder paste using pick-and-place machines
- Passing the board through a reflow oven to melt the solder and form electrical connections
- Inspecting the assembled board using automated optical inspection (AOI) to detect any defects or misalignments
5. Through-Hole Assembly (THT)
Through-hole assembly involves inserting and soldering through-hole components into the drilled holes on the PCB. This process can be done manually or using automated insertion machines. The assembled board is then passed through a wave soldering machine to form electrical connections on the underside of the board.
6. Final Inspection and Testing
After the assembly process is complete, the medical PCB undergoes a series of inspections and tests to verify its functionality, quality, and compliance with relevant standards. This may include:
- Visual inspection for defects, cleanliness, and proper labeling
- Automated optical inspection (AOI) to detect solder defects, component placement issues, and other anomalies
- X-ray inspection to verify the integrity of hidden connections, such as ball grid arrays (BGAs) and hidden vias
- In-circuit testing (ICT) to verify the electrical performance of individual components and circuits
- Functional testing to ensure that the PCB performs as intended within the medical device
7. Conformal Coating and Potting
To protect the medical PCB from moisture, dust, and other environmental factors, a conformal coating or potting compound may be applied. Conformal coating involves applying a thin layer of protective material, such as acrylic, silicone, or urethane, over the assembled PCB. Potting involves encapsulating the PCB in a protective resin or epoxy.
8. Packaging and Shipping
Once the medical PCB has passed all inspections and tests, it is packaged in ESD-safe and moisture-resistant packaging materials to protect it during storage and transportation. The packaged PCBs are then shipped to the medical device manufacturer for integration into the final product.
Quality Control and Regulatory Compliance in Medical PCB Assembly
Quality control and regulatory compliance are critical aspects of medical PCB assembly, as they ensure the safety, reliability, and effectiveness of the medical devices in which the PCBs are used.
Quality Management Systems (QMS)
Medical PCB assembly companies must have a robust quality management system (QMS) in place to ensure consistent quality and compliance with relevant standards and regulations. The most widely recognized QMS standards for medical devices are:
- ISO 13485: This standard specifies requirements for a quality management system specific to the medical device industry. It is based on the ISO 9001 standard but includes additional requirements for risk management, cleanliness, traceability, and regulatory compliance.
- FDA Quality System Regulation (QSR): Also known as 21 CFR Part 820, this regulation sets forth the quality system requirements for medical devices sold in the United States. It covers various aspects of design, manufacturing, packaging, labeling, storage, installation, and servicing of medical devices.
Risk Management
Risk management is a critical component of medical PCB assembly, as it helps identify, assess, and mitigate potential risks associated with the PCB and its use in the medical device. The most widely recognized risk management standard for medical devices is ISO 14971, which provides a framework for identifying, evaluating, and controlling risks throughout the product lifecycle.
Traceability
Traceability is essential in medical PCB assembly, as it allows manufacturers to track the origin, history, and location of each component and process step throughout the product lifecycle. This is achieved through the use of unique identifiers, such as serial numbers, lot numbers, and date codes, which are recorded and linked to specific production records.
Traceability helps manufacturers to:
- Identify and isolate defective components or processes
- Facilitate product recalls and field actions
- Investigate and resolve customer complaints
- Demonstrate compliance with regulatory requirements
Cleanliness and Contamination Control
Medical PCBs must be manufactured in clean environments to minimize the risk of contamination, which could compromise the safety and performance of the medical device. This is typically achieved through the use of cleanroom facilities, which are designed to control airborne particles, temperature, humidity, and other environmental factors.
Cleanroom classification is based on the number and size of particles allowed per cubic meter of air, as defined by the ISO 14644-1 standard. For example, an ISO Class 7 cleanroom allows a maximum of 352,000 particles (0.5 microns or larger) per cubic meter of air.
In addition to cleanroom facilities, medical PCB assembly companies must also implement contamination control procedures, such as:
- Personnel gowning and hygiene protocols
- Material handling and storage procedures
- Equipment cleaning and maintenance schedules
- Environmental monitoring and testing
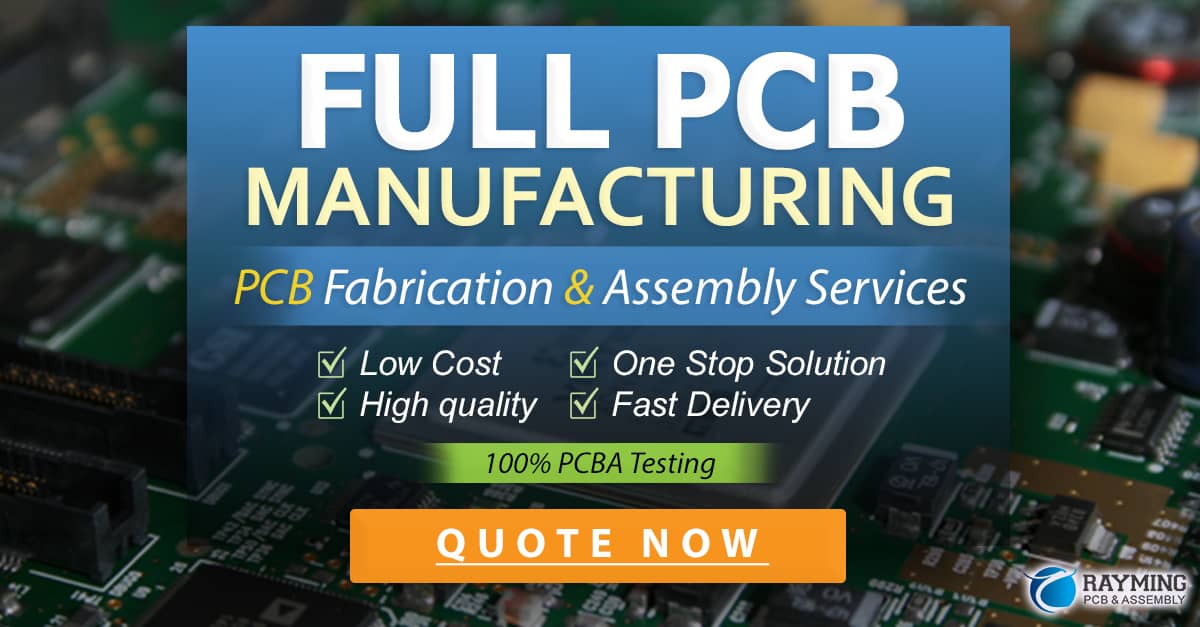
Challenges in Medical PCB Assembly
Medical PCB assembly presents several unique challenges compared to standard PCB assembly, including:
Miniaturization
Many medical devices, such as implantable devices and wearable monitors, require miniaturized PCBs to fit within the device’s small form factor. This can be challenging, as it requires the use of smaller components, tighter tolerances, and more precise assembly techniques.
High-Density Interconnect (HDI) PCBs
High-density interconnect (HDI) PCBs are increasingly common in medical devices, as they allow for more complex circuitry and higher component density in a smaller form factor. HDI PCBs present additional challenges in terms of design, fabrication, and assembly, such as:
- Smaller via sizes and pad pitches
- Tighter tolerances for trace widths and spacings
- More complex layer stackups and lamination processes
- Higher risk of thermal and mechanical stress during assembly
Biocompatibility
Medical PCBs that come into contact with the patient’s body or bodily fluids must be made from biocompatible materials to minimize the risk of adverse reactions or toxicity. This requires careful selection of PCB substrates, solder masks, and other materials based on their biocompatibility testing results.
Electromagnetic Compatibility (EMC)
Medical devices must be designed to minimize electromagnetic interference (EMI) and ensure electromagnetic compatibility (EMC) with other devices in the healthcare environment. This requires careful design of the PCB layout, selection of components with low EMI characteristics, and the use of shielding and filtering techniques to reduce emissions and susceptibility.
Supply Chain Management
Medical PCB assembly companies must have a robust supply chain management system in place to ensure the quality, availability, and traceability of components used in medical PCBs. This includes:
- Qualifying and monitoring suppliers based on their quality, delivery, and regulatory compliance
- Maintaining adequate inventory levels to avoid shortages and production delays
- Implementing counterfeit prevention and detection measures, such as component authentication and testing
- Ensuring proper handling, storage, and packaging of components to maintain their integrity and traceability
Conclusion
Medical PCB assembly is a complex and highly regulated process that requires specialized knowledge, equipment, and processes to ensure the safety, reliability, and effectiveness of the medical devices in which the PCBs are used.
By understanding the key differences between medical PCBs and standard PCBs, the steps involved in the assembly process, and the quality control and regulatory requirements, medical device manufacturers can ensure that their PCBs meet the highest standards of performance and patient safety.
As medical technology continues to advance, the demand for more complex, miniaturized, and reliable PCBs will only increase. Medical PCB assembly companies that can adapt to these challenges and maintain a focus on quality, innovation, and regulatory compliance will be well-positioned to support the growth and development of the medical device industry.
FAQ
1. What are the key standards and regulations that apply to medical PCB assembly?
The key standards and regulations that apply to medical PCB assembly include:
- ISO 13485: Quality management system standard for medical devices
- FDA Quality System Regulation (QSR) or 21 CFR Part 820: Quality system requirements for medical devices sold in the United States
- ISO 14971: Risk management standard for medical devices
- IPC-A-610: Acceptability standard for electronic assemblies
- IPC-6012: Qualification and performance specification for rigid printed boards
2. What are the cleanroom requirements for medical PCB assembly?
The cleanroom requirements for medical PCB assembly depend on the specific needs of the medical device and the level of cleanliness required. Typically, medical PCB assembly is performed in ISO Class 7 (10,000) or ISO Class 8 (100,000) cleanrooms, as defined by the ISO 14644-1 standard. These cleanrooms control airborne particles, temperature, humidity, and other environmental factors to minimize the risk of contamination.
3. What is the difference between conformal coating and potting in medical PCB assembly?
Conformal coating and potting are both methods used to protect medical PCBs from environmental factors, but they differ in their application and level of protection:
- Conformal coating involves applying a thin layer of protective material, such as acrylic, silicone, or urethane, over the assembled PCB. This provides a barrier against moisture, dust, and other contaminants, while still allowing access to the components for repair or rework.
- Potting involves encapsulating the PCB in a protective resin or epoxy, which completely seals the board and its components. This provides a higher level of protection against moisture, shock, and vibration, but makes it difficult or impossible to access the components for repair or rework.
4. How do medical PCB assembly companies ensure traceability throughout the product lifecycle?
Medical PCB assembly companies ensure traceability throughout the product lifecycle by using unique identifiers, such as serial numbers, lot numbers, and date codes, to track the origin, history, and location of each component and process step. This information is recorded and linked to specific production records, allowing manufacturers to:
- Identify and isolate defective components or processes
- Facilitate product recalls and field actions
- Investigate and resolve customer complaints
- Demonstrate compliance with regulatory requirements
Traceability is maintained through the use of barcode scanning, RFID tagging, and other automated data capture technologies, as well as through the implementation of robust documentation and record-keeping systems.
5. What are the challenges associated with miniaturization and high-density interconnect (HDI) PCBs in medical devices?
Miniaturization and high-density interconnect (HDI) PCBs present several challenges in medical device design and assembly, including:
- Smaller component sizes and tighter tolerances, which require more precise assembly techniques and equipment
- Increased heat generation and thermal management issues due to higher component density
- Greater susceptibility to mechanical stress and vibration due to the use of finer pitch components and thinner PCB substrates
- Higher risk of signal integrity issues, such as crosstalk and electromagnetic interference (EMI), due to closer trace spacing and higher signal frequencies
- More complex design and layout requirements to ensure manufacturability and reliability
To overcome these challenges, medical PCB assembly companies must invest in advanced equipment, processes, and expertise, such as high-precision pick-and-place machines, micro-via drilling and filling techniques, and 3D modeling and simulation tools. Close collaboration between the design, manufacturing, and quality teams is also essential to ensure that the PCBs meet the required performance, reliability, and regulatory standards.
0 Comments