Understanding PCB customization
PCB customization refers to the process of designing and manufacturing printed circuit boards that are tailored to meet specific requirements and specifications of a particular project or application. Unlike standard, off-the-shelf PCBs, customized PCBs are engineered to address unique challenges and deliver optimal performance in terms of functionality, reliability, and efficiency.
The Need for PCB Customization
The demand for PCB customization has grown significantly in recent years due to several factors:
-
Unique Application Requirements: As technology advances and new applications emerge, standard PCBs may not always meet the specific needs of these applications. Customized PCBs allow designers and manufacturers to create boards that are optimized for specific use cases, ensuring optimal performance and reliability.
-
Miniaturization and High Density: With the trend towards miniaturization and the need for more compact electronic devices, customized PCBs enable designers to create high-density layouts that maximize space utilization while maintaining signal integrity and thermal management.
-
Cost Optimization: Customized PCBs can help businesses optimize their production costs by eliminating unnecessary features, reducing material usage, and streamlining the manufacturing process. This results in more cost-effective solutions without compromising on quality or performance.
-
Intellectual Property Protection: Customized PCBs offer a level of intellectual property protection by making it more difficult for competitors to reverse engineer or replicate the design. This is particularly important for businesses operating in highly competitive markets or those with proprietary technologies.
The PCB Customization Process
The PCB customization process typically involves several key stages:
1. Design and Schematic Creation
The first step in PCB customization is the creation of a detailed design and schematic. This involves defining the board’s functional requirements, selecting components, and creating a layout that optimizes signal integrity, power distribution, and thermal management. Designers use specialized software tools such as Altium Designer, Eagle, or KiCad to create the schematic and layout files.
2. Prototype Development and Testing
Once the design is finalized, a prototype is developed to validate the functionality and performance of the customized PCB. This stage involves fabricating a small batch of boards and subjecting them to rigorous testing to ensure they meet the desired specifications. Any issues or defects identified during testing are addressed, and the design is refined accordingly.
3. Manufacturing and Assembly
After the prototype has been validated, the customized PCBs are manufactured and assembled in larger quantities. This stage involves several processes, including PCB fabrication, component placement, soldering, and quality control. Depending on the complexity of the design and the required quantities, manufacturing and assembly can be done in-house or outsourced to specialized PCB Assembly services.
Benefits of PCB Customization
PCB customization offers several key benefits for businesses and designers:
-
Enhanced Functionality and Performance: Customized PCBs are designed to meet specific requirements, resulting in enhanced functionality and performance compared to standard, off-the-shelf solutions. This can lead to improved product quality, reliability, and user experience.
-
Cost Savings: By optimizing the design and manufacturing process, PCB customization can help businesses reduce production costs and improve their bottom line. This is particularly important for high-volume production runs, where even small cost savings can add up to significant amounts over time.
-
Faster Time-to-Market: Customized PCBs can be designed and manufactured relatively quickly, allowing businesses to bring their products to market faster than if they were to rely on standard solutions. This can be a significant advantage in fast-paced, competitive markets where time-to-market is critical.
-
Improved Reliability and Durability: Customized PCBs are engineered to withstand the specific environmental conditions and stresses they will be subjected to in their intended application. This results in improved reliability and durability, reducing the risk of failures and extending the product’s lifespan.
-
Competitive Advantage: By leveraging PCB customization, businesses can differentiate their products from competitors and offer unique, value-added features that set them apart in the market. This can help them gain a competitive edge and capture a larger market share.
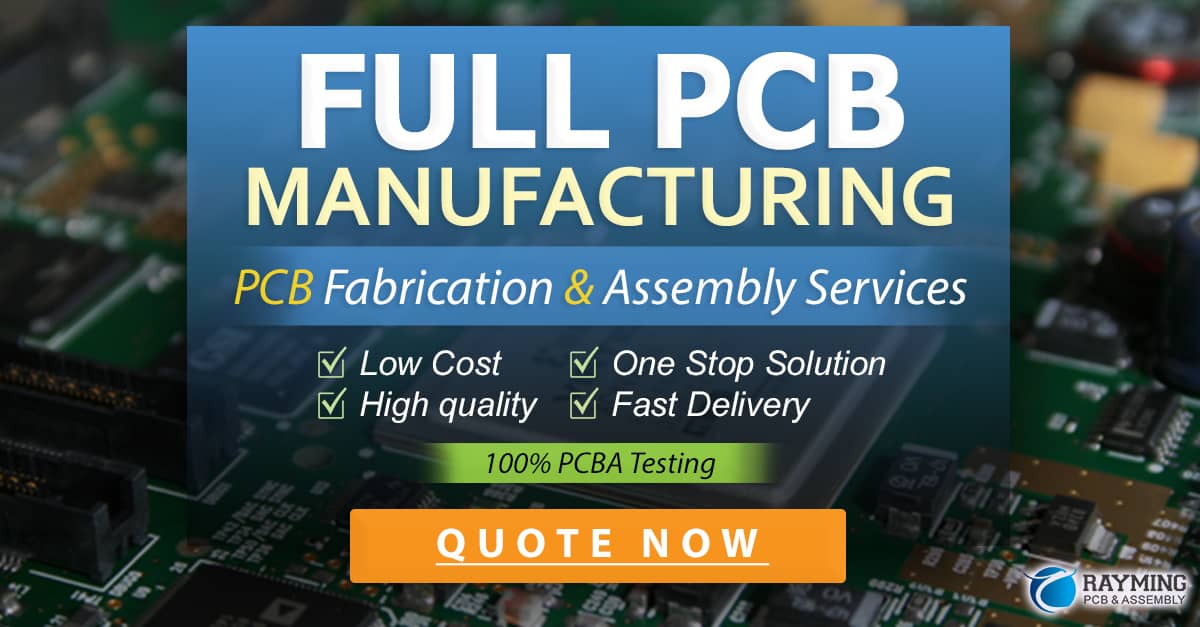
PCB Customization Trends and Technologies
The PCB customization landscape is constantly evolving, driven by advancements in materials, manufacturing processes, and design tools. Some of the key trends and technologies shaping the future of PCB customization include:
1. Advanced Materials
The development of advanced materials such as high-frequency laminates, flexible substrates, and thermally conductive materials is enabling designers to create PCBs that can operate in demanding environments and meet the requirements of cutting-edge applications. These materials offer improved electrical properties, mechanical stability, and thermal management, allowing for more compact and high-performance designs.
2. 3D Printing
3D printing technology is increasingly being used in PCB customization to create complex geometries and integrate mechanical features directly into the board. This allows for greater design flexibility, reduced assembly time, and improved mechanical stability. 3D printing also enables rapid prototyping and low-volume production, making it an attractive option for businesses with specialized requirements.
3. Embedded Components
Embedded component technology involves integrating passive components such as resistors, capacitors, and inductors directly into the PCB substrate. This approach offers several benefits, including reduced board size, improved signal integrity, and enhanced reliability. Embedded components also simplify the assembly process and reduce the risk of component failures due to mechanical stress or vibration.
4. High-Density Interconnect (HDI)
HDI technology enables the creation of PCBs with high-density layouts and fine-pitch components. This is achieved through the use of micro-vias, blind and buried vias, and thin dielectric layers. HDI PCBs offer improved signal integrity, reduced crosstalk, and better power distribution, making them well-suited for applications that require high-speed data transmission and compact form factors.
5. Intelligent PCBs
The integration of sensors, microcontrollers, and other intelligent components into PCBs is becoming increasingly common in customized designs. These intelligent PCBs can monitor their own performance, adapt to changing conditions, and communicate with other devices, enabling advanced functionality such as predictive maintenance, self-calibration, and remote monitoring.
Choosing the Right PCB Assembly Service
When it comes to PCB customization, choosing the right assembly service is crucial to ensure the success of your project. Here are some key factors to consider:
-
Experience and Expertise: Look for a PCB assembly service with a proven track record in handling customized designs and a deep understanding of the latest technologies and manufacturing processes. They should have the necessary expertise to guide you through the customization process and provide valuable insights and recommendations.
-
Manufacturing Capabilities: Ensure that the assembly service has the necessary equipment, facilities, and processes in place to handle your specific requirements. This includes the ability to work with advanced materials, high-density layouts, and specialized components.
-
Quality Control and Testing: A reputable PCB assembly service should have strict quality control measures in place to ensure that your customized PCBs meet the highest standards of reliability and performance. They should also offer comprehensive testing services to validate the functionality and integrity of your boards before they are shipped.
-
Turnaround Time and Flexibility: Consider the assembly service’s turnaround time and their ability to accommodate your schedule and delivery requirements. They should be flexible enough to handle both small-volume prototyping and large-scale production runs, depending on your needs.
-
Customer Support and Communication: Choose a PCB assembly service that values clear communication and provides excellent customer support throughout the customization process. They should be responsive to your inquiries, keep you informed of progress, and be willing to work closely with you to address any issues or concerns that may arise.
Frequently Asked Questions (FAQ)
-
Q: What is the minimum order quantity for customized PCBs?
A: The minimum order quantity for customized PCBs varies depending on the assembly service and the complexity of the design. Some services offer low-volume prototyping options with minimum quantities as low as one or two boards, while others may require higher minimum quantities for production runs. -
Q: How long does the PCB customization process typically take?
A: The duration of the PCB customization process depends on several factors, including the complexity of the design, the availability of components, and the manufacturing and assembly processes required. Simple designs can be completed in a matter of days, while more complex projects may take several weeks or even months. -
Q: Can I provide my own components for a customized PCB?
A: Many PCB assembly services offer the option to use customer-supplied components in customized designs. However, it is important to ensure that the components meet the necessary specifications and are compatible with the manufacturing processes used by the assembly service. It is also essential to provide accurate and complete documentation, including component datasheets and any special handling requirements. -
Q: What file formats are typically required for PCB customization?
A: The most common file formats used in PCB customization include Gerber files (for PCB fabrication), ODB++ files (for component placement and assembly), and IPC-2581 files (for design data exchange). Other formats such as DXF, STEP, and IGES may also be used for mechanical design and integration. -
Q: How can I ensure the security and confidentiality of my customized PCB design?
A: To protect your intellectual property and maintain the confidentiality of your customized PCB design, it is important to choose a reputable PCB assembly service that has robust security measures in place. This includes secure data storage and transfer protocols, non-disclosure agreements (NDAs), and strict access controls. It is also advisable to discuss your security requirements upfront and ensure that the assembly service can meet your specific needs.
Conclusion
PCB customization has emerged as a powerful approach to deliver state-of-the-art electronic design and manufacturing solutions. By tailoring PCBs to meet specific requirements and leveraging advanced technologies and materials, businesses can achieve enhanced functionality, improved performance, and cost savings. As the demand for customized solutions continues to grow, partnering with a reliable and experienced PCB assembly service is crucial to ensure the success of your projects.
When considering PCB customization for your next project, take the time to carefully evaluate your requirements, explore the latest trends and technologies, and choose an assembly service that can provide the expertise, capabilities, and support you need. With the right approach and partnership, PCB customization can help you stay ahead of the curve and deliver cutting-edge electronic solutions to your customers.
0 Comments