Introduction to PCB Prototyping
PCB (Printed Circuit Board) prototyping is a crucial step in the development of electronic devices and systems. It involves creating a functional and testable version of the final PCB design to validate its performance, identify any issues, and make necessary improvements before mass production. In the industrial sector, PCB Prototypes play a vital role in ensuring the reliability, durability, and efficiency of electronic components used in various applications such as automotive, aerospace, manufacturing, and telecommunications.
The Importance of PCB Prototyping in Industrial Applications
Industrial PCB prototypes serve several important purposes:
-
Validation of design: Prototypes allow engineers to test the functionality and performance of the PCB design in real-world conditions, ensuring that it meets the required specifications and standards.
-
Identification of issues: During the prototyping phase, any design flaws, component incompatibilities, or manufacturing defects can be identified and addressed before proceeding to mass production, saving time and resources.
-
Optimization of performance: Prototypes enable engineers to fine-tune the PCB design, optimize component placement, and improve overall system performance based on the results of testing and evaluation.
-
Compliance with regulations: Industrial PCBs must comply with various safety, environmental, and electromagnetic compatibility (EMC) regulations. Prototyping allows manufacturers to ensure that their designs meet these requirements before final production.
The PCB Prototyping Process
Design and Schematic Creation
The first step in the PCB prototyping process is to create a detailed schematic of the electronic circuit using EDA (Electronic Design Automation) software. The schematic captures the logical connections between components, power supply requirements, and signal routing. Engineers must also consider factors such as component selection, form factor, and manufacturing constraints during the design phase.
PCB Layout and Routing
Once the schematic is finalized, the next step is to create the physical layout of the PCB using PCB design software. This involves placing components on the board, defining the layer stack-up, and routing the traces to connect the components according to the schematic. The layout must also account for factors such as signal integrity, power distribution, thermal management, and manufacturability.
Fabrication of PCB Prototype
After the PCB layout is complete, the design files are sent to a PCB fabrication house for manufacturing. The fabrication process typically involves the following steps:
-
Printing the circuit pattern: The PCB design is printed onto a photoresist layer on the copper-clad laminate using a photoplotter or direct imaging system.
-
Etching: The exposed copper areas are etched away using a chemical solution, leaving behind the desired circuit pattern.
-
Drilling: Holes are drilled through the board to accommodate through-hole components and create vias for inter-layer connections.
-
Plating: The holes are plated with copper to establish electrical connectivity between layers.
-
Solder mask application: A protective solder mask layer is applied to the board to insulate the copper traces and prevent short circuits.
-
Silkscreen printing: Text and symbols are printed onto the board for component identification and assembly guidance.
Assembly and Testing
Once the PCB prototype is fabricated, the components are soldered onto the board either manually or using automated assembly equipment. The assembled prototype is then subjected to various tests to validate its functionality, performance, and reliability. These tests may include:
-
Power-on testing: Verifying that the board powers up correctly and all voltage rails are within specified limits.
-
Functional testing: Checking that all components and subsystems operate as intended and meet the design requirements.
-
Signal integrity testing: Ensuring that the signals transmitted through the PCB are clean, stable, and free from interference or distortion.
-
Environmental testing: Exposing the prototype to various environmental conditions such as temperature, humidity, and vibration to assess its durability and reliability.
-
EMC testing: Verifying that the PCB prototype meets electromagnetic compatibility standards and does not cause or suffer from electromagnetic interference.
Advanced Techniques in Industrial PCB Prototyping
High-Density Interconnect (HDI) PCBs
HDI PCBs are characterized by their high component density, fine trace widths, and small via sizes. They enable the miniaturization of electronic devices while maintaining high performance and reliability. HDI PCB prototyping requires advanced manufacturing techniques such as microvias, blind and buried vias, and sequential lamination to achieve the required level of interconnect density.
Rigid-Flex PCBs
Rigid-flex PCBs combine rigid and flexible substrates in a single board, allowing for three-dimensional packaging and improved reliability in applications that require flexing or folding of the PCB. Prototyping rigid-flex PCBs involves special design considerations such as bend radius, stiffener placement, and adhesive selection to ensure the mechanical integrity of the board.
Embedded Components
Embedded component PCBs involve the integration of passive components such as resistors, capacitors, and inductors within the layers of the PCB substrate. This technique offers several advantages, including reduced board size, improved signal integrity, and enhanced thermal performance. Prototyping embedded component PCBs requires precise control over the lamination process and specialized materials to ensure reliable embedding of the components.
3D Printed Electronics
3D printing technology has recently been adapted for the fabrication of electronic circuits, allowing for the rapid prototyping of complex, three-dimensional PCB structures. Conductive and insulating materials can be deposited layer by layer to create functional electronic components and interconnects. 3D printed electronics enable the creation of customized, low-volume PCB prototypes with unique geometries and features that would be difficult or impossible to achieve with traditional manufacturing methods.
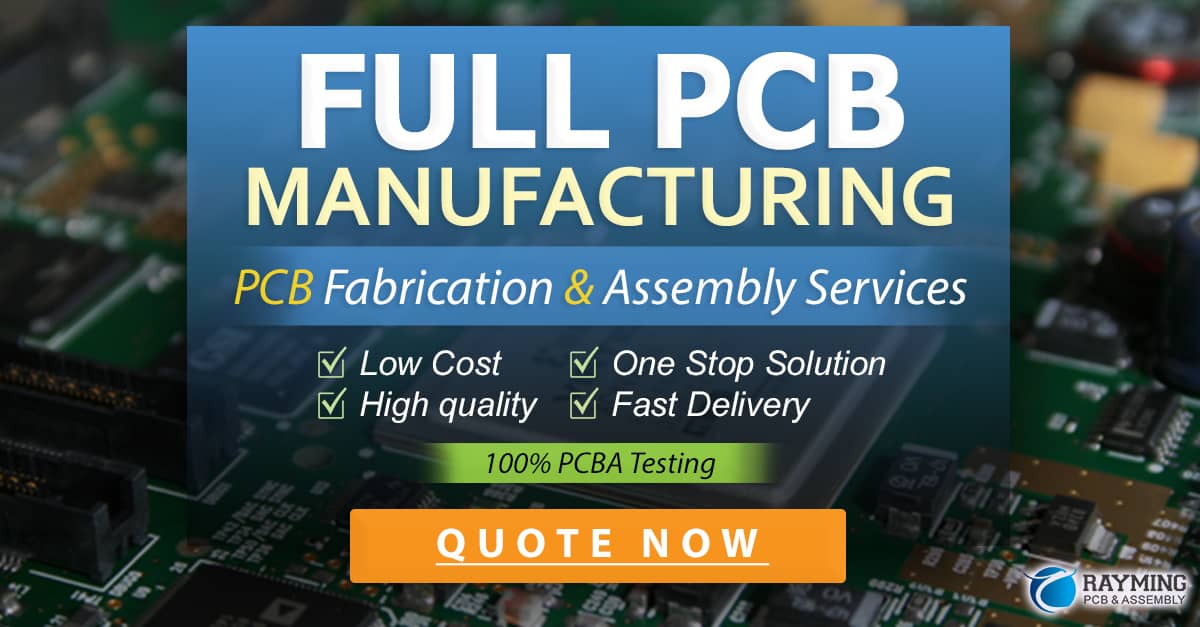
Benefits of Outsourcing Industrial PCB Prototyping
Outsourcing industrial PCB prototyping to specialized service providers offers several advantages for companies:
-
Access to expertise: PCB prototyping service providers have experienced engineers and technicians who are well-versed in the latest design and manufacturing techniques, ensuring high-quality prototypes.
-
State-of-the-art equipment: Outsourcing partners invest in advanced manufacturing equipment and software tools, enabling them to fabricate complex, high-density PCB prototypes with tight tolerances.
-
Time and cost savings: By leveraging the capabilities of a prototyping service provider, companies can reduce their in-house design and manufacturing costs and accelerate their time-to-market.
-
Scalability: Outsourcing allows companies to easily scale their prototyping needs up or down based on project requirements, without having to invest in additional resources or infrastructure.
-
Focus on core competencies: By outsourcing PCB prototyping, companies can focus their internal resources on their core competencies, such as product design, marketing, and sales.
Choosing the Right PCB Prototyping Partner
When selecting a PCB prototyping service provider, companies should consider the following factors:
-
Technical capabilities: Ensure that the provider has the necessary equipment, expertise, and experience to fabricate the required type of PCB prototype (e.g., HDI, rigid-flex, embedded components).
-
Quality control: Look for a provider with a robust quality management system and a track record of delivering high-quality prototypes consistently.
-
Turnaround time: Consider the provider’s standard lead times and their ability to accommodate expedited orders if needed.
-
Communication and support: Choose a provider that offers clear communication channels, responsive customer support, and a willingness to collaborate closely with your design team.
-
Cost: Obtain quotes from multiple providers and compare their pricing, taking into account factors such as prototype complexity, quantity, and turnaround time.
Future Trends in Industrial PCB Prototyping
As the demand for smaller, faster, and more sophisticated electronic devices continues to grow, industrial PCB prototyping technologies and practices must evolve to keep pace. Some of the key trends shaping the future of PCB prototyping include:
-
Miniaturization: The push for miniaturization will drive the adoption of advanced packaging techniques such as system-in-package (SiP), wafer-level packaging (WLP), and 3D integrated circuits (3D ICs).
-
High-speed design: With the increasing prevalence of high-speed interfaces and protocols, PCB prototyping will need to focus on signal integrity, power integrity, and EMC to ensure reliable performance at higher frequencies.
-
Additive manufacturing: 3D printing and other additive manufacturing technologies will play a growing role in PCB prototyping, enabling the creation of complex, non-planar structures and the integration of electronics with mechanical components.
-
Sustainable materials: There will be a greater emphasis on the use of environmentally friendly, recyclable, and biodegradable materials in PCB fabrication to reduce electronic waste and minimize the environmental impact of electronics manufacturing.
-
Intelligent automation: The integration of artificial intelligence (AI), machine learning, and robotics in PCB prototyping processes will enable faster, more efficient, and more accurate fabrication and testing of prototypes.
Conclusion
Industrial PCB prototyping is a critical step in the development of reliable, high-performance electronic systems. By leveraging advanced manufacturing techniques, specialized service providers, and innovative technologies, companies can create functional, testable prototypes that validate their designs and pave the way for successful mass production. As the electronics industry continues to evolve, staying abreast of the latest trends and best practices in PCB prototyping will be essential for companies seeking to maintain their competitive edge in the market.
Frequently Asked Questions (FAQ)
-
What is the typical turnaround time for industrial PCB prototypes?
The turnaround time for industrial PCB prototypes varies depending on the complexity of the design, the manufacturing processes involved, and the service provider. Standard lead times can range from a few days to several weeks, but many providers offer expedited services for time-critical projects. -
How much does it cost to prototype an industrial PCB?
The cost of prototyping an industrial PCB depends on factors such as the size of the board, the number of layers, the components used, and the quantity of prototypes required. Prices can range from a few hundred to several thousand dollars per prototype, depending on the specific requirements of the project. -
What are the main advantages of outsourcing industrial PCB prototyping?
Outsourcing industrial PCB prototyping offers several advantages, including access to specialized expertise and advanced manufacturing equipment, time and cost savings, scalability, and the ability to focus on core competencies while leaving the prototyping process to experienced professionals. -
How do I choose the right PCB prototyping partner for my project?
When choosing a PCB prototyping partner, consider factors such as their technical capabilities, quality control processes, turnaround times, communication and support, and cost. Look for a provider with experience in fabricating the specific type of PCB prototype you require and a track record of delivering high-quality results. -
What are some of the key trends shaping the future of industrial PCB prototyping?
Some of the key trends shaping the future of industrial PCB prototyping include miniaturization, high-speed design, additive manufacturing, sustainable materials, and intelligent automation. Staying informed about these trends and adapting to new technologies and practices will be essential for companies looking to remain competitive in the rapidly evolving electronics industry.
Prototype Type | Typical Turnaround Time | Approximate Cost Range |
---|---|---|
Standard PCB | 1-2 weeks | $100 – $1,000 |
HDI PCB | 2-4 weeks | $500 – $5,000 |
Rigid-Flex PCB | 3-6 weeks | $1,000 – $10,000 |
Embedded Component PCB | 4-8 weeks | $2,000 – $20,000 |
3D Printed Electronics | 1-2 weeks | $500 – $5,000 |
Note: The turnaround times and cost ranges provided in the table are rough estimates and may vary significantly based on the specific requirements of each project and the capabilities of the chosen service provider.
0 Comments