What is a PCB prototype?
A PCB (Printed Circuit Board) prototype is a preliminary version of a printed circuit board that is used for testing and validation before mass production. It allows designers and engineers to physically test the functionality, performance, and reliability of their designed circuit. PCB prototypes are essential in the electronic product development process as they help identify and rectify any issues or defects before the final product is manufactured.
The Importance of PCB Prototyping
PCB prototyping is a crucial step in the development of electronic devices for several reasons:
-
Design Validation: PCB prototypes allow designers to validate their circuit design and ensure that it functions as intended. It helps identify any design flaws, component incompatibilities, or layout issues that may affect the performance of the final product.
-
Testing and Debugging: With a physical prototype, engineers can perform various tests, such as signal integrity analysis, power consumption measurements, and thermal stress tests. This helps identify and debug any issues that may arise during the operation of the device.
-
Cost Savings: Identifying and rectifying design issues during the prototyping stage can save significant costs compared to discovering problems after mass production has begun. It is much cheaper to modify a prototype than to recall or rework a large batch of faulty products.
-
Time-to-Market: PCB prototyping allows for parallel development processes, such as firmware development and mechanical design, to occur simultaneously. This can significantly reduce the overall development time and help bring the product to market faster.
PCB Prototype Manufacturing Process
The PCB prototype manufacturing process typically involves the following steps:
1. Design Creation
The first step in PCB prototyping is to create the circuit design using Electronic Design Automation (EDA) software. The designer creates a schematic diagram that represents the electrical connections between components and then converts it into a PCB layout. The layout determines the physical placement of components and routing of traces on the board.
2. Design Review and Verification
Once the design is complete, it undergoes a thorough review process to ensure that it meets all the required specifications and standards. This includes checking for design rule violations, ensuring proper component placement, and verifying the signal integrity of the layout.
3. Fabrication
After the design is finalized, the PCB prototype is fabricated using various methods, such as:
- Subtractive Methods: This involves removing unwanted copper from a pre-laminated PCB substrate using chemical etching or mechanical milling.
- Additive Methods: This involves adding conductive traces onto a non-conductive substrate using techniques like ink-jet printing or 3D printing.
The choice of fabrication method depends on factors such as the complexity of the design, the required precision, and the production volume.
4. Assembly
Once the PCB is fabricated, the components are assembled onto the board using either through-hole or surface-mount technology (SMT). Through-hole components have long leads that are inserted into drilled holes on the PCB, while SMT components are placed directly onto the surface of the board.
5. Testing and Inspection
After assembly, the PCB prototype undergoes various tests to ensure its functionality and reliability. This includes:
- Visual Inspection: The assembled PCB is visually inspected for any defects, such as solder bridges, component misalignment, or damaged traces.
- Electrical Testing: The PCB is powered on, and its electrical characteristics, such as voltage levels, current consumption, and signal integrity, are measured and compared against the design specifications.
- Functional Testing: The PCB is tested in its intended operating environment to ensure that it performs as expected under real-world conditions.
6. Rework and Modification
If any issues are identified during the testing and inspection phase, the PCB prototype is reworked or modified to rectify the problems. This may involve replacing faulty components, modifying the circuit design, or adjusting the layout.
7. Final Verification
Once all the necessary modifications are made, the PCB prototype undergoes a final round of testing and verification to ensure that it meets all the required specifications and standards. If the prototype passes all the tests, it is ready for mass production.
PCB Prototype Manufacturing Methods
There are several methods for manufacturing PCB prototypes, each with its own advantages and limitations. The choice of method depends on factors such as the complexity of the design, the required precision, and the production volume.
1. CNC Milling
CNC (Computer Numerical Control) milling is a subtractive manufacturing method that uses a computer-controlled milling machine to remove unwanted copper from a pre-laminated PCB substrate. This method is suitable for low-volume prototyping and can produce high-precision PCBs with fine features.
Advantages | Limitations |
---|---|
High precision | Slow process |
Suitable for complex designs | Limited material options |
Ideal for low-volume production | Higher cost for high-volume production |
2. Laser Etching
Laser etching is another subtractive manufacturing method that uses a high-powered laser to remove unwanted copper from the PCB substrate. This method is faster than CNC milling and can produce very fine features, making it suitable for high-density PCB designs.
Advantages | Limitations |
---|---|
High speed | Higher equipment cost |
Very fine feature resolution | Limited material options |
Suitable for high-density designs | Not suitable for thick copper layers |
3. Ink-Jet Printing
Ink-jet printing is an additive manufacturing method that uses a specialized ink-jet printer to deposit conductive ink onto a non-conductive substrate. This method is suitable for low-volume prototyping and can produce flexible and stretchable PCBs.
Advantages | Limitations |
---|---|
Fast prototyping | Lower conductivity compared to copper |
Suitable for flexible and stretchable PCBs | Limited material options |
Low cost for low-volume production | Not suitable for high-current applications |
4. 3D Printing
3D printing is an additive manufacturing method that uses a specialized 3D printer to deposit conductive and non-conductive materials layer by layer to form a complete PCB. This method is suitable for complex, multi-layer PCB designs and can produce embedded components and unique form factors.
Advantages | Limitations |
---|---|
Suitable for complex, multi-layer designs | Slow process |
Can produce embedded components | Limited material options |
Enables unique form factors | Higher cost compared to traditional methods |
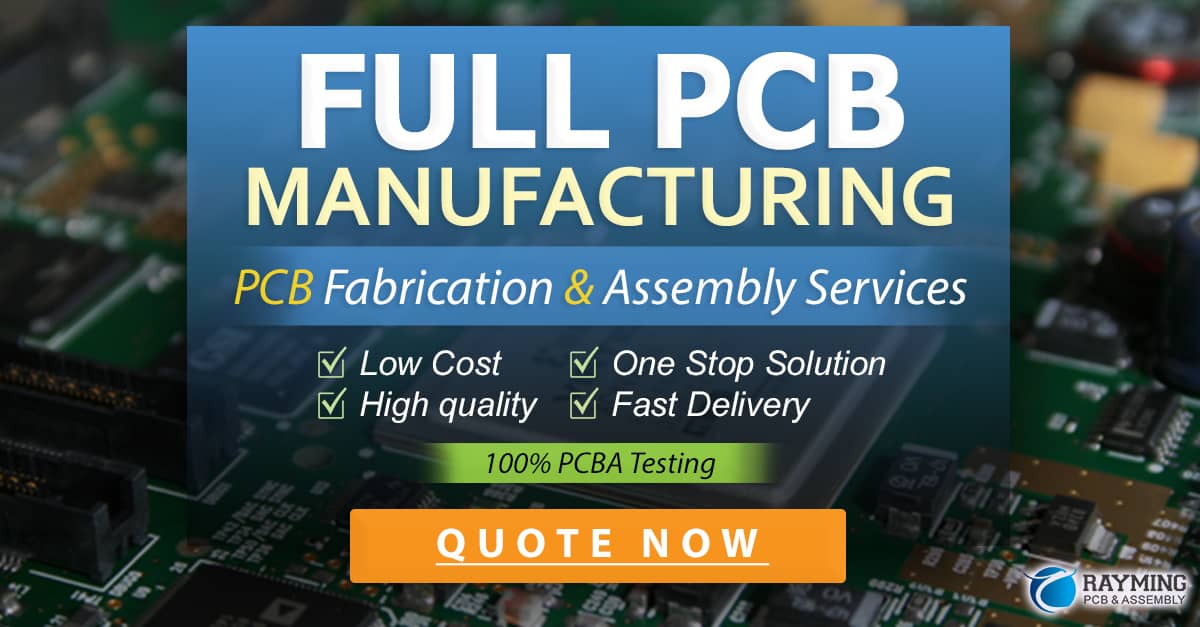
Choosing the Right PCB Prototype Manufacturer
Choosing the right PCB prototype manufacturer is crucial for ensuring the success of your project. Here are some factors to consider when selecting a manufacturer:
1. Experience and Expertise
Look for a manufacturer with experience in producing PCB prototypes similar to your design. They should have the necessary expertise and knowledge to guide you through the prototyping process and provide valuable insights and recommendations.
2. Manufacturing Capabilities
Ensure that the manufacturer has the necessary equipment and capabilities to produce your PCB prototype. Consider factors such as the minimum feature size, layer count, material options, and manufacturing methods available.
3. Quality Control
Quality control is critical in PCB prototyping. Look for a manufacturer that has a robust quality control process in place, including visual inspection, electrical testing, and functional testing. They should also have the necessary certifications and standards compliance, such as ISO 9001 and IPC Class 2 or 3.
4. Turnaround Time
PCB prototyping is often a time-sensitive process, so choose a manufacturer that can deliver your prototypes within your required timeframe. Many manufacturers offer expedited services for faster turnaround times, but this may come at an additional cost.
5. Cost
Cost is always a consideration in any project. Look for a manufacturer that offers competitive pricing without compromising on quality. Be cautious of manufacturers that offer prices that seem too good to be true, as they may cut corners on quality or use subpar materials.
6. Customer Support
Good customer support is essential in PCB prototyping. Look for a manufacturer that is responsive, communicative, and willing to work closely with you throughout the prototyping process. They should be able to provide timely updates, answer your questions, and address any issues that may arise.
Frequently Asked Questions (FAQ)
1. What is the typical turnaround time for PCB prototypes?
The turnaround time for PCB prototypes varies depending on the complexity of the design, the manufacturing method used, and the manufacturer’s workload. Typical turnaround times range from 24 hours to 2 weeks, but some manufacturers offer expedited services for faster delivery.
2. How much does it cost to manufacture a PCB prototype?
The cost of manufacturing a PCB prototype depends on several factors, such as the size of the board, the number of layers, the materials used, and the manufacturing method employed. Simple, single-layer PCB prototypes can cost as little as $10, while complex, multi-layer designs can cost several hundred dollars.
3. What are the minimum feature sizes for PCB prototypes?
The minimum feature sizes for PCB prototypes depend on the manufacturing method used. CNC milling and laser etching can typically achieve minimum trace widths and spacings of around 0.1mm, while ink-jet printing and 3D printing can achieve even smaller features, down to 0.05mm or less.
4. Can I manufacture PCB prototypes in-house?
Yes, it is possible to manufacture PCB prototypes in-house using desktop PCB milling machines or 3D printers. However, in-house manufacturing may be limited by the available equipment, materials, and expertise. It may also be more cost-effective to outsource PCB prototyping to a professional manufacturer for complex or high-volume projects.
5. What file formats are required for PCB prototyping?
The file formats required for PCB prototyping depend on the manufacturer and the design software used. Most manufacturers accept standard file formats such as Gerber files (RS-274X), ODB++ files, and Excellon drill files. Some manufacturers may also accept native design files from popular EDA software such as Altium Designer, Eagle, or KiCad.
Conclusion
PCB prototyping is a critical step in the electronic product development process, allowing designers and engineers to validate their designs, identify and rectify issues, and ensure the functionality and reliability of their products. With the various manufacturing methods and manufacturers available, it is important to choose the right approach and partner for your specific project requirements.
By considering factors such as experience, capabilities, quality control, turnaround time, cost, and customer support, you can select a PCB prototype manufacturer that can help bring your ideas to life and support the success of your project.
0 Comments