Introduction to Flexible PCBs
Flexible printed circuit boards (PCBs) have gained significant popularity in recent years due to their versatility and ability to conform to various shapes and sizes. These PCBs offer numerous advantages over traditional rigid PCBs, making them ideal for a wide range of applications, including wearable devices, medical equipment, automotive electronics, and aerospace systems.
However, dealing with flexible PCBs also presents unique challenges that require careful consideration and planning. In this article, we will explore the opportunities and challenges associated with flexible PCBs and provide insights on how to effectively address them.
Advantages of Flexible PCBs
Compact and Lightweight Design
One of the primary advantages of flexible PCBs is their ability to enable compact and lightweight product designs. By replacing rigid PCBs and bulky wiring with flexible circuits, designers can significantly reduce the size and weight of electronic devices. This is particularly beneficial for applications where space is limited or where weight reduction is crucial, such as in portable devices, wearables, and aerospace systems.
Conformability and Bendability
Flexible PCBs offer excellent conformability and bendability, allowing them to adapt to various shapes and contours. This feature enables designers to create products with unique form factors and ergonomic designs. Flexible circuits can be bent, folded, or even rolled without compromising their functionality or reliability. This flexibility opens up new possibilities for product design and integration, enabling the development of innovative and user-friendly devices.
Enhanced Reliability and Durability
Compared to traditional rigid PCBs and wire harnesses, flexible PCBs offer improved reliability and durability. The absence of connectors and the reduced number of solder joints in flexible circuits minimize potential points of failure. Additionally, the ability of flexible PCBs to withstand vibrations, shocks, and thermal stresses makes them more resilient in demanding environments. This enhanced reliability translates to longer product life cycles and reduced maintenance costs.
Cost-Effectiveness
While the initial costs of flexible PCBs may be higher compared to rigid PCBs, they can offer long-term cost savings in certain applications. The compact and lightweight nature of flexible circuits can lead to reduced material usage, simplified assembly processes, and lower shipping costs. Furthermore, the improved reliability and durability of flexible PCBs can result in fewer product failures and warranty claims, ultimately reducing overall costs.
Challenges of Flexible PCBs
Design Complexity
Designing flexible PCBs involves unique considerations and challenges compared to traditional rigid PCBs. Designers must account for the mechanical properties of flexible materials, such as bend radius, flexing cycles, and material selection. They must also ensure proper signal integrity, impedance control, and electromagnetic compatibility in dynamic flexing environments. Addressing these design complexities requires specialized knowledge and expertise in Flexible Circuit Design.
Manufacturing Processes
Manufacturing flexible PCBs demands different processes and equipment compared to rigid PCBs. The choice of materials, such as flexible substrates and coverlay films, requires careful consideration to ensure compatibility and performance. Processes like coverlay lamination, stiffener attachment, and profile cutting need to be optimized for flexible circuits. Additionally, handling and packaging of flexible PCBs require special attention to prevent damage during transportation and assembly.
Testing and Validation
Testing and validating flexible PCBs presents unique challenges due to their dynamic nature. Traditional testing methods used for rigid PCBs may not be sufficient to assess the performance and reliability of flexible circuits under flexing conditions. Specialized testing equipment and techniques, such as flex testing machines and accelerated life testing, are necessary to evaluate the mechanical and electrical integrity of flexible PCBs. Thorough testing and validation are crucial to ensure the long-term reliability of flexible circuits in their intended applications.
Supply Chain Management
Managing the supply chain for flexible PCBs can be more complex compared to rigid PCBs. The availability of specific flexible materials, such as polyimide films and flexible Copper-Clad Laminates, may be limited, leading to longer lead times and potential supply disruptions. Establishing reliable supplier relationships and maintaining adequate inventory levels are essential to mitigate supply chain risks. Additionally, close collaboration with suppliers is necessary to ensure consistent quality and timely delivery of flexible PCB components.
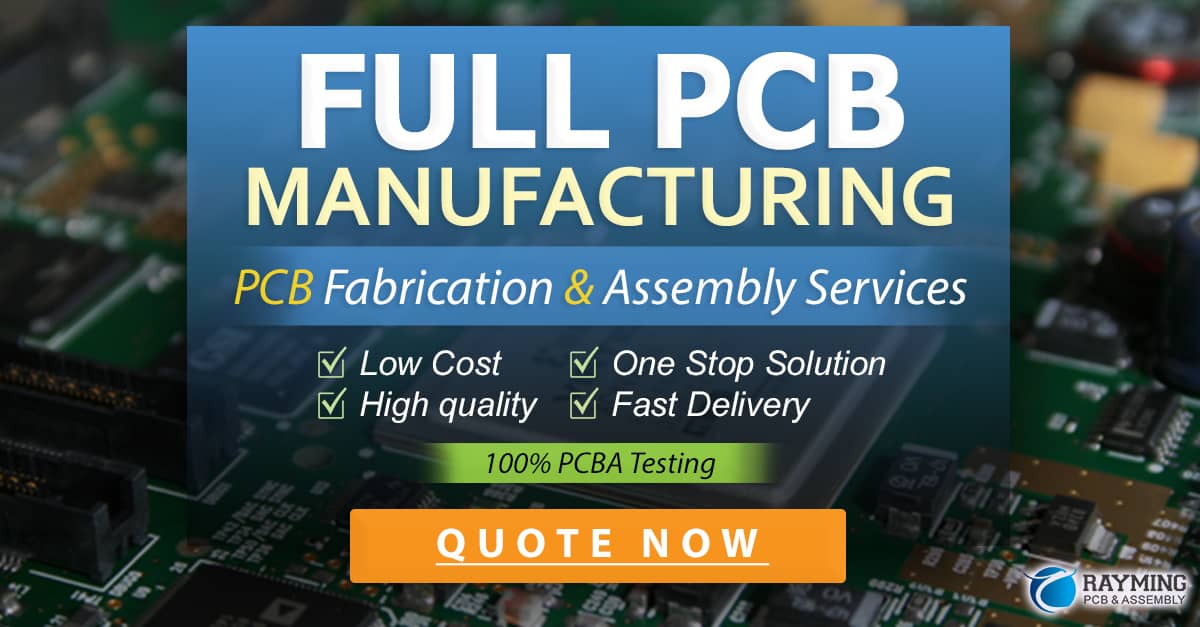
Strategies for Success
Collaborate with Experienced Partners
To effectively deal with the challenges of flexible PCBs, it is crucial to collaborate with experienced partners who have expertise in flexible circuit design, manufacturing, and testing. Partner with PCB manufacturers and assembly providers who have a proven track record in handling flexible circuits. They can provide valuable insights, guide you through the design process, and ensure the manufacturability and reliability of your flexible PCBs.
Invest in Design Tools and Training
Invest in specialized design tools and software that cater to the unique requirements of flexible PCBs. These tools should support features such as 3D modeling, mechanical simulation, and signal integrity analysis to optimize flexible circuit designs. Additionally, provide training and education to your design teams to enhance their knowledge and skills in flexible PCB design. Encourage them to stay updated with the latest industry trends, best practices, and emerging technologies in flexible electronics.
Implement Robust Testing and Validation
Develop a comprehensive testing and validation plan specific to flexible PCBs. Collaborate with testing service providers who have experience in evaluating the performance and reliability of flexible circuits. Implement a combination of mechanical, electrical, and environmental tests to assess the robustness of your flexible PCBs under various operating conditions. Utilize accelerated life testing methods to predict the long-term reliability of your products and identify potential failure modes early in the development cycle.
Foster Supply Chain Partnerships
Establish strong partnerships with suppliers and manufacturers who specialize in flexible PCB materials and components. Develop long-term relationships based on trust, transparency, and mutual benefits. Collaborate closely with your suppliers to ensure timely availability of materials, consistent quality, and responsive support. Regularly review and assess your supply chain to identify potential risks and implement contingency plans to mitigate disruptions.
Conclusion
Flexible PCBs offer numerous opportunities for product innovation, miniaturization, and enhanced reliability. However, dealing with flexible PCBs also presents unique challenges that require careful consideration and strategic approaches. By collaborating with experienced partners, investing in design tools and training, implementing robust testing and validation, and fostering supply chain partnerships, you can effectively address these challenges and capitalize on the benefits of flexible PCBs.
As the demand for flexible electronics continues to grow, staying ahead of the curve in flexible PCB technology is essential for companies aiming to remain competitive in their respective industries. By embracing the opportunities and proactively addressing the challenges associated with flexible PCBs, you can unlock new possibilities for your products and deliver innovative solutions to your customers.
Frequently Asked Questions (FAQ)
1. What are the key advantages of using flexible PCBs over traditional rigid PCBs?
Flexible PCBs offer several advantages over rigid PCBs, including:
– Compact and lightweight design
– Conformability and bendability
– Enhanced reliability and durability
– Cost-effectiveness in certain applications
2. What are the main challenges in designing flexible PCBs?
Designing flexible PCBs involves unique challenges such as:
– Accounting for mechanical properties of flexible materials
– Ensuring signal integrity and electromagnetic compatibility in dynamic flexing environments
– Optimizing material selection and stack-up for flexibility and performance
– Addressing bend radius, flexing cycles, and other mechanical considerations
3. How do manufacturing processes differ for flexible PCBs compared to rigid PCBs?
Manufacturing flexible PCBs requires different processes and equipment compared to rigid PCBs. Key differences include:
– Material selection, such as flexible substrates and coverlay films
– Coverlay lamination and stiffener attachment processes
– Profile cutting and handling techniques specific to flexible circuits
– Specialized packaging to prevent damage during transportation and assembly
4. What testing methods are used to validate the performance and reliability of flexible PCBs?
Testing and validating flexible PCBs involve specialized methods such as:
– Flex testing machines to evaluate mechanical integrity under repeated flexing
– Accelerated life testing to assess long-term reliability
– Electrical testing under dynamic flexing conditions
– Environmental testing to simulate real-world operating conditions
5. How can companies effectively manage the supply chain for flexible PCBs?
To effectively manage the supply chain for flexible PCBs, companies can:
– Establish reliable supplier relationships with expertise in flexible materials and components
– Maintain adequate inventory levels to mitigate supply disruptions
– Collaborate closely with suppliers to ensure consistent quality and timely delivery
– Regularly review and assess supply chain risks and implement contingency plans
Aspect | Flexible PCBs | Rigid PCBs |
---|---|---|
Design | Conformable and bendable | Fixed and rigid |
Weight | Lightweight | Heavier compared to flexible PCBs |
Reliability | Enhanced reliability due to fewer connections | More prone to failures at connection points |
Durability | Withstands vibrations, shocks, and thermal stresses | Less resilient to mechanical stresses |
Manufacturing Processes | Requires specialized processes and equipment | Established and standardized processes |
Cost | Higher initial costs, potential long-term savings | Lower initial costs, higher assembly costs |
0 Comments