Introduction to High Tg PCBs
High Tg PCBs, or Printed Circuit Boards with a high glass transition temperature (Tg), are a type of advanced PCB designed to withstand extreme temperatures and harsh environmental conditions. These PCBs are essential for applications in industries such as aerospace, automotive, military, and telecommunications, where reliability and durability are critical factors.
The glass transition temperature (Tg) is the temperature at which a polymer substrate changes from a rigid, glassy state to a more flexible, rubbery state. In the context of PCBs, a higher Tg value indicates that the board can maintain its structural integrity and electrical properties at elevated temperatures.
Advantages of High Tg PCBs
- Enhanced thermal stability
- Improved mechanical strength
- Reduced thermal expansion
- Better signal integrity
- Increased reliability in harsh environments
Materials Used in High Tg PCBs
Substrate Materials
The most common substrate materials used in the manufacture of High Tg PCBs are:
- FR-4 High Tg: An enhanced version of the standard FR-4 laminate, with a Tg value ranging from 170°C to 180°C.
- Polyimide (PI): A high-performance polymer with excellent thermal stability and a Tg value of up to 260°C.
- PTFE (Teflon): A fluoropolymer known for its low dielectric constant, low loss tangent, and a Tg value of approximately 327°C.
- Ceramic: An inorganic, non-metallic material with high thermal conductivity and a Tg value exceeding 1,000°C.
Copper Foils
High Tg PCBs typically use copper foils with a thickness ranging from 0.5 oz to 2 oz (17.5 μm to 70 μm). The choice of copper foil thickness depends on the specific application and the required current carrying capacity.
Solder Mask and Silkscreen
High Tg solder masks and silkscreen inks are formulated to withstand the elevated temperatures experienced by the PCB during operation. These materials should have a Tg value similar to or higher than the substrate material to ensure proper adhesion and durability.
Manufacturing Process of High Tg PCBs
The manufacturing process of High Tg PCBs is similar to that of standard PCBs, with a few key differences to accommodate the specialized materials and requirements.
-
Design and Layout: The PCB design is created using EDA (Electronic Design Automation) software, taking into account the specific requirements of High Tg materials and the intended application.
-
Material Selection: The appropriate High Tg substrate material, copper foil, solder mask, and silkscreen are selected based on the design requirements and the operating environment.
-
Lamination: The substrate material is laminated with the copper foil using high temperature and pressure to create a strong bond.
-
Drilling: Holes are drilled through the laminated board to accommodate through-hole components and vias.
-
Plating: The drilled holes are plated with copper to create electrical connections between layers.
-
Etching: The unwanted copper is removed using a chemical etching process, leaving behind the desired circuit pattern.
-
Solder Mask Application: The High Tg solder mask is applied to the board to protect the copper traces and prevent solder bridging.
-
Silkscreen Printing: The silkscreen is printed onto the board to provide component labels, logos, and other identifying marks.
-
Surface Finish: A surface finish, such as ENIG (Electroless Nickel Immersion Gold) or HASL (Hot Air Solder Leveling), is applied to the exposed copper to prevent oxidation and enhance solderability.
-
Electrical Testing: The completed High Tg PCB undergoes electrical testing to ensure proper functionality and adherence to design specifications.
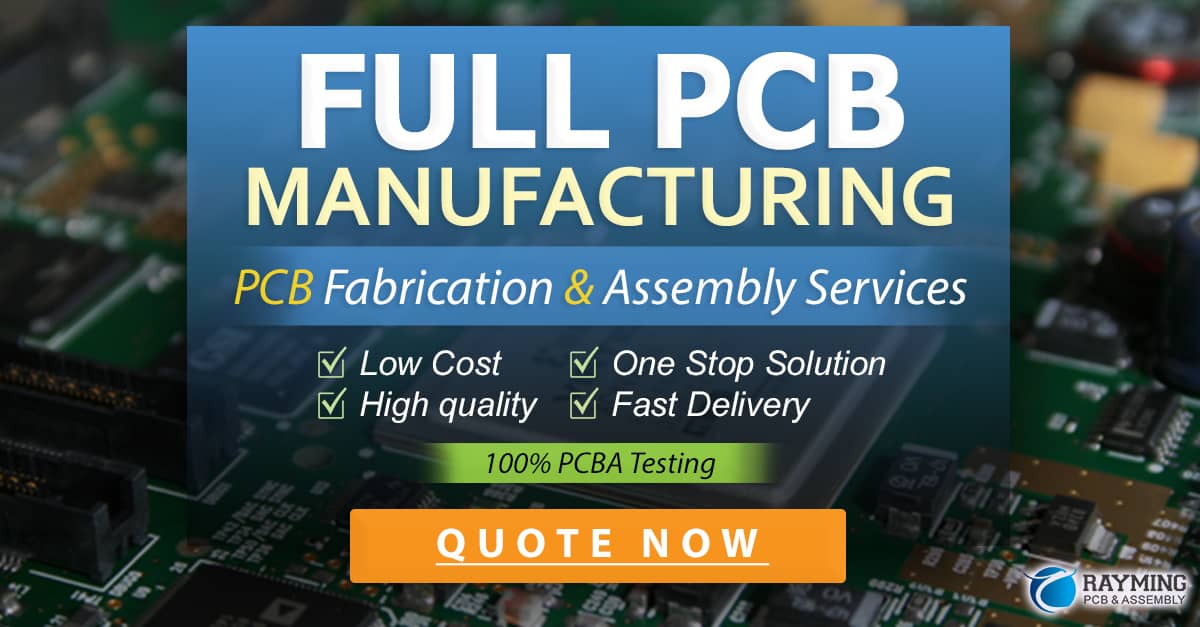
Applications of High Tg PCBs
High Tg PCBs find applications in various industries where thermal stability, reliability, and durability are essential. Some common applications include:
- Aerospace and Defense: Avionics, satellite systems, radar equipment, and military vehicles.
- Automotive: Engine control units, power electronics, and sensors exposed to high temperatures.
- Industrial: High-temperature sensors, motor drives, and power supplies in industrial equipment.
- Telecommunications: High-power RF and microwave circuits, base stations, and satellite communication systems.
- Medical: Sterilizable medical devices, implantable electronics, and diagnostic equipment.
- Oil and Gas: Downhole drilling equipment, seismic sensors, and wellhead control systems.
Choosing the Right High Tg PCB Manufacturer
When selecting a High Tg PCB manufacturer, consider the following factors to ensure the best quality and service:
- Experience: Look for a manufacturer with a proven track record in producing High Tg PCBs for your specific industry and application.
- Capabilities: Ensure that the manufacturer has the necessary equipment, expertise, and processes to handle High Tg materials and meet your design requirements.
- Quality Control: Inquire about the manufacturer’s quality control processes, certifications (e.g., ISO 9001, AS9100, IATF 16949), and testing capabilities.
- Technical Support: Choose a manufacturer that offers comprehensive technical support, from design assistance to troubleshooting and after-sales service.
- Lead Time and Pricing: Consider the manufacturer’s lead times and pricing structure to ensure they align with your project timeline and budget.
Top High Tg PCB Manufacturers
Manufacturer | Location | Certifications | Specialties |
---|---|---|---|
Avanti Circuits | USA | ISO 9001, AS9100, IATF 16949 | Aerospace, Defense, Automotive |
Sanmina | USA | ISO 9001, AS9100, IATF 16949, ISO 13485 | Medical, Aerospace, Automotive |
Tripod Technology | Taiwan | ISO 9001, AS9100, IATF 16949 | Automotive, Telecommunications |
NCAB Group | Sweden | ISO 9001, AS9100, IATF 16949, ISO 14001 | Aerospace, Automotive, Industrial |
Unimicron | Taiwan | ISO 9001, AS9100, IATF 16949, ISO 14001 | Telecommunications, Automotive, Industrial |
Best Practices for Designing High Tg PCBs
When designing High Tg PCBs, follow these best practices to ensure optimal performance and reliability:
- Material Selection: Choose the appropriate High Tg substrate material based on the operating temperature range, environmental conditions, and electrical requirements of your application.
- Thermal Management: Incorporate thermal management techniques, such as using heatsinks, thermal vias, and proper component placement, to dissipate heat effectively and prevent hot spots.
- Signal Integrity: Consider the impact of high temperatures on signal integrity, and design your PCB layout accordingly. Use appropriate trace widths, spacing, and impedance control measures to minimize signal distortion and crosstalk.
- Mechanical Strength: Ensure that your High Tg PCB design has adequate mechanical strength to withstand vibrations, shocks, and thermal stresses in the intended operating environment.
- Manufacturing Considerations: Collaborate closely with your High Tg PCB manufacturer to ensure that your design is optimized for manufacturability, taking into account factors such as minimum trace widths, hole sizes, and copper weights.
Frequently Asked Questions (FAQ)
-
What is the difference between High Tg PCBs and standard PCBs?
High Tg PCBs are designed to withstand higher operating temperatures and harsher environmental conditions compared to standard PCBs. They use specialized substrate materials, such as FR-4 High Tg, Polyimide, or PTFE, which have a higher glass transition temperature (Tg) than the materials used in standard PCBs. -
How do I select the right High Tg substrate material for my application?
The choice of High Tg substrate material depends on factors such as the operating temperature range, environmental conditions, electrical requirements, and budget. Work closely with your PCB manufacturer to evaluate the available options and select the most suitable material for your specific application. -
Can High Tg PCBs be used in multilayer designs?
Yes, High Tg PCBs can be manufactured in multilayer configurations, allowing for more complex designs and higher component densities. However, the manufacturing process for multilayer High Tg PCBs requires specialized equipment and expertise, so it is essential to choose a manufacturer with experience in producing these boards. -
Are High Tg PCBs more expensive than standard PCBs?
Yes, High Tg PCBs are generally more expensive than standard PCBs due to the specialized materials and manufacturing processes involved. However, the added cost is justified by the enhanced thermal stability, reliability, and durability provided by High Tg PCBs in demanding applications. -
What certifications should I look for when choosing a High Tg PCB manufacturer?
When selecting a High Tg PCB manufacturer, look for certifications relevant to your industry and application, such as: - ISO 9001 for general quality management
- AS9100 for aerospace and defense
- IATF 16949 for automotive
- ISO 13485 for medical devices
- ISO 14001 for environmental management
These certifications demonstrate the manufacturer’s commitment to quality, reliability, and adherence to industry standards.
Conclusion
High Tg PCBs are essential for applications that demand exceptional thermal stability, reliability, and durability in harsh operating environments. By understanding the materials, manufacturing processes, and best practices involved in High Tg PCB design and fabrication, engineers can create robust and high-performance electronic systems for industries such as aerospace, automotive, industrial, and telecommunications.
When selecting a High Tg PCB manufacturer, prioritize experience, capabilities, quality control, technical support, and alignment with your project requirements. By partnering with a reputable manufacturer and following best design practices, you can ensure the success of your High Tg PCB projects and deliver reliable, long-lasting electronic solutions for your customers.
0 Comments