Introduction to PCB Layout Topology
Printed Circuit Board (PCB) layout topology plays a crucial role in the performance and reliability of high-speed electronic systems. As signal speeds continue to increase, the layout of the PCB becomes increasingly important to ensure signal integrity, minimize electromagnetic interference (EMI), and maintain overall system stability. This article will delve into the key aspects of high-speed PCB layout topology, providing insights and best practices for designing robust and efficient high-speed circuits.
Understanding Signal Integrity in High-Speed PCBs
Signal integrity is a critical consideration in high-speed PCB design. As signal frequencies increase, the PCB Traces begin to behave like transmission lines, leading to various signal integrity issues such as reflections, crosstalk, and signal distortion. To mitigate these problems, designers must carefully consider factors such as trace geometry, impedance matching, and termination techniques.
Impedance Matching and Controlled Impedance
One of the fundamental principles of high-speed PCB layout is impedance matching. When a signal travels along a trace, it encounters a Characteristic Impedance determined by the trace geometry and the dielectric properties of the PCB material. To minimize reflections and ensure efficient power transfer, the impedance of the trace must match the impedance of the source and load devices.
Controlled impedance is a technique used to maintain consistent impedance throughout the signal path. By carefully designing the trace width, thickness, and spacing, as well as selecting appropriate dielectric materials, designers can achieve a desired characteristic impedance. Common controlled impedance values include 50 ohms for single-ended signals and 100 ohms for differential pairs.
Termination Techniques
Proper termination is essential to prevent signal reflections and maintain signal integrity in high-speed PCBs. There are several termination techniques commonly used, including:
-
Series Termination: A resistor is placed in series with the signal source to match the impedance of the trace. This technique is effective for point-to-point connections.
-
Parallel Termination: A resistor is placed at the end of the trace, in parallel with the load device. This technique is suitable for multi-drop bus configurations.
-
AC Termination: Capacitors and resistors are used to provide high-frequency termination while allowing DC bias levels to pass through. This technique is often used in high-speed memory interfaces.
The choice of termination technique depends on the specific requirements of the system, such as signal speed, topology, and power consumption.
PCB Layer Stackup and Signal Routing
The PCB layer stackup and signal routing strategies play a significant role in high-speed PCB layout topology. A well-designed layer stackup helps minimize crosstalk, reduces EMI, and provides a stable reference plane for high-speed signals.
Layer Stackup Considerations
A typical high-speed PCB layer stackup consists of multiple layers, including signal layers, ground planes, and power planes. The arrangement of these layers is crucial for maintaining signal integrity and minimizing interference. Some key considerations for layer stackup design include:
-
Signal Layer Adjacency: High-speed signals should be routed on layers adjacent to a solid ground or power plane to provide a consistent reference and minimize crosstalk.
-
Ground and Power Plane Placement: Ground and power planes should be placed close to the signal layers to reduce loop area and minimize inductance.
-
Dielectric Thickness: The thickness of the dielectric material between layers affects the characteristic impedance and propagation delay of signals. Thinner dielectrics are preferred for high-speed designs.
-
Symmetry: A symmetric layer stackup helps balance copper distribution and minimizes warpage during the manufacturing process.
Signal Routing Techniques
Proper signal routing is critical for maintaining signal integrity and minimizing crosstalk in high-speed PCBs. Some important signal routing techniques include:
-
Trace Geometry: High-speed traces should be as short and direct as possible to minimize propagation delay and signal distortion. Avoid sharp corners and use smooth curves or 45-degree angles for trace routing.
-
Trace Spacing: Adequate spacing between traces helps reduce crosstalk. The spacing should be based on the signal speed, trace geometry, and layer stackup.
-
Differential Pair Routing: Differential signals should be routed as closely coupled pairs with controlled spacing and matched lengths to maintain signal integrity and common-mode noise rejection.
-
Via Placement: Vias should be placed strategically to minimize signal discontinuities and reduce capacitive loading. Avoid placing vias in critical signal paths or near sensitive components.
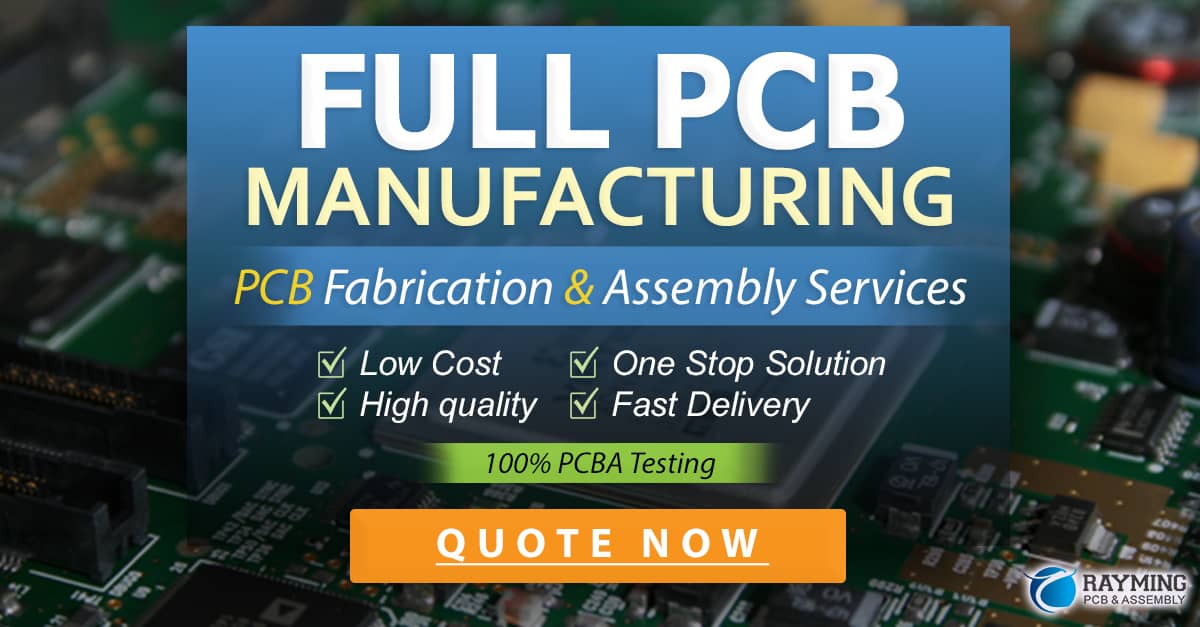
Power Distribution Network (PDN) Design
The power distribution network (PDN) is responsible for delivering clean and stable power to the components on a high-speed PCB. A well-designed PDN is essential for maintaining signal integrity and preventing power-related issues such as voltage drops, ground bounce, and electromagnetic interference (EMI).
PDN Components
The PDN consists of several key components, including:
-
Power Planes: Dedicated copper layers that distribute power to various parts of the PCB.
-
Ground Planes: Continuous copper layers that provide a low-impedance return path for signals and help minimize EMI.
-
Decoupling Capacitors: Capacitors placed close to power pins of ICs to provide local energy storage and reduce high-frequency noise.
-
Voltage Regulators: Components that regulate and stabilize the voltage supplied to different parts of the PCB.
PDN Design Considerations
When designing the PDN for a high-speed PCB, several factors should be considered:
-
Impedance Control: The PDN should have low impedance across the frequency range of interest to minimize voltage fluctuations and ensure stable power delivery.
-
Decoupling Strategy: Proper placement and selection of decoupling capacitors are critical for effective high-frequency noise suppression. Use a combination of bulk, ceramic, and low-ESL capacitors to cover different frequency ranges.
-
Plane Splitting: In some cases, it may be necessary to split power planes to accommodate different voltage levels or to isolate sensitive circuits. Carefully consider the placement of split planes to minimize noise coupling.
-
Via Placement: Power and ground vias should be placed close to the power pins of ICs to minimize inductance and ensure effective decoupling.
Signal Integrity Simulation and Analysis
To ensure the reliability and performance of high-speed PCBs, signal integrity simulation and analysis are essential steps in the design process. These tools help designers identify and mitigate potential signal integrity issues before the PCB is manufactured.
Pre-Layout Simulation
Pre-layout simulation involves modeling the PCB Stackup, material properties, and component characteristics to predict signal behavior. Some common pre-layout simulation techniques include:
-
Impedance Calculation: Calculating the characteristic impedance of traces based on the PCB stackup and material properties.
-
Signal Integrity Analysis: Simulating signal propagation, reflections, and crosstalk to identify potential issues and optimize trace geometry and termination strategies.
-
Power Integrity Analysis: Analyzing the PDN to ensure stable power delivery and identify potential resonances or voltage drop issues.
Post-Layout Simulation
Post-layout simulation takes into account the actual PCB layout, including trace routing, via placement, and component placement. It provides a more accurate assessment of signal integrity and helps identify layout-related issues. Some common post-layout simulation techniques include:
-
Time-Domain Reflectometry (TDR): Analyzing the impedance profile of traces to identify discontinuities and reflections.
-
Eye Diagram Analysis: Evaluating the quality of high-speed signals by analyzing eye openings, jitter, and noise margins.
-
Electromagnetic Compatibility (EMC) Analysis: Simulating the electromagnetic behavior of the PCB to identify potential EMI issues and ensure compliance with EMC regulations.
Best Practices for High-Speed PCB Layout
To ensure the successful design and performance of high-speed PCBs, consider the following best practices:
-
Collaborate with the system architect and component engineers to understand the specific requirements and constraints of the design.
-
Use a well-defined design process that includes schematic review, layout guidelines, signal integrity simulation, and Design Rule Checks (DRC).
-
Follow industry-standard guidelines for high-speed PCB layout, such as IPC-2221 and IPC-2251.
-
Use a consistent and well-documented naming convention for components, nets, and layers to facilitate communication and ensure clarity.
-
Regularly review and update the design based on simulation results and feedback from manufacturers and assembly houses.
-
Conduct thorough testing and validation of the manufactured PCB to verify signal integrity, power integrity, and EMC performance.
Conclusion
High-speed PCB layout topology is a critical aspect of designing reliable and performant electronic systems. By understanding the principles of signal integrity, impedance control, power distribution, and simulation techniques, designers can create robust PCBs that meet the demanding requirements of modern high-speed applications.
As signal speeds continue to increase, staying up-to-date with the latest techniques and best practices in high-speed PCB layout becomes increasingly important. By following the guidelines and recommendations presented in this article, designers can navigate the complexities of high-speed PCB design and ensure the success of their projects.
FAQs
-
Q: What is the importance of controlled impedance in high-speed PCB layout?
A: Controlled impedance is crucial for maintaining signal integrity in high-speed PCBs. By carefully designing trace geometry and selecting appropriate dielectric materials, designers can achieve a desired characteristic impedance that matches the impedance of source and load devices. This minimizes signal reflections and ensures efficient power transfer. -
Q: What are the benefits of using a symmetric layer stackup in high-speed PCB design?
A: A symmetric layer stackup helps balance copper distribution and minimizes warpage during the manufacturing process. It also provides a consistent reference plane for high-speed signals and reduces crosstalk between adjacent layers. -
Q: Why is proper decoupling important in power distribution network (PDN) design?
A: Proper decoupling is essential for maintaining stable power delivery and reducing high-frequency noise in high-speed PCBs. Decoupling capacitors placed close to power pins of ICs provide local energy storage and suppress noise across different frequency ranges. Effective decoupling ensures signal integrity and prevents power-related issues such as voltage drops and ground bounce. -
Q: What are the common signal routing techniques used in high-speed PCB layout?
A: Common signal routing techniques in high-speed PCB layout include keeping traces as short and direct as possible, maintaining adequate spacing between traces to reduce crosstalk, routing differential pairs with controlled spacing and matched lengths, and strategically placing vias to minimize signal discontinuities and capacitive loading. -
Q: How can signal integrity simulation and analysis help in high-speed PCB design?
A: Signal integrity simulation and analysis are essential tools for identifying and mitigating potential signal integrity issues before the PCB is manufactured. Pre-layout simulation helps predict signal behavior, optimize trace geometry and termination strategies, and ensure stable power delivery. Post-layout simulation takes into account the actual PCB layout and provides a more accurate assessment of signal integrity, helping identify layout-related issues such as reflections, crosstalk, and EMI.
0 Comments