What is HDI PCB?
HDI PCB is a type of printed circuit board that features a higher density of interconnections compared to traditional PCBs. The increased density is achieved through the use of smaller vias, finer line widths, and tighter spacing between components. HDI PCBs are typically defined as having any of the following characteristics:
- Via diameter less than 150 microns
- Line width and spacing less than 100 microns
- Pad pitch less than 400 microns
The use of HDI technology enables the creation of more compact and complex electronic devices, such as smartphones, tablets, wearables, and medical devices.
HDI PCB Manufacturing Process
The manufacturing process for HDI PCBs is more complex and demanding than that of traditional PCBs. It requires advanced equipment, materials, and expertise to achieve the necessary precision and reliability. The following are the key steps involved in HDI PCB manufacturing:
1. Design and Layout
The first step in HDI PCB manufacturing is the design and layout of the circuit board. This involves creating a detailed schematic of the electronic components and their interconnections using specialized PCB design software. The layout must take into account the specific requirements of HDI technology, such as the smaller via sizes, finer line widths, and tighter component spacing.
2. Material Selection
The choice of materials is critical in HDI PCB manufacturing. The substrate, copper foil, and laminate materials must be carefully selected to ensure the required electrical, thermal, and mechanical properties. Common substrate materials for HDI PCBs include FR-4, polyimide, and Rogers materials, while the copper foil thickness is typically thinner than that used in traditional PCBs.
3. Lamination
The next step is the lamination of the substrate material with the copper foil. This is done under high pressure and temperature to ensure a strong and uniform bond between the layers. The lamination process for HDI PCBs requires precise control to maintain the integrity of the fine features and prevent distortion or delamination.
4. Drilling and Via Formation
After lamination, the vias are drilled into the PCB using high-precision drilling equipment. In HDI PCBs, the vias are typically smaller and more numerous than in traditional PCBs. There are several types of vias used in HDI PCBs, including blind vias, buried vias, and microvia. The formation of these vias requires advanced techniques such as laser drilling, plasma etching, or photovia processes.
5. Patterning and Etching
The copper foil is then patterned and etched to create the desired circuit traces and pads. This is typically done using photolithography and chemical etching processes. In HDI PCBs, the line widths and spaces are much finer than in traditional PCBs, requiring high-resolution imaging and precise control of the etching process.
6. Plating and Surface Finish
After patterning and etching, the PCB undergoes plating and surface finish processes to protect the copper traces and improve solderability. Common surface finishes for HDI PCBs include Electroless Nickel Immersion Gold (ENIG), Immersion Silver (IAg), and Organic Solderability Preservative (OSP).
7. Solder Mask and Silkscreen
The final steps in HDI PCB manufacturing involve the application of solder mask and silkscreen layers. The solder mask is a protective coating that covers the copper traces and prevents short circuits during soldering. The silkscreen layer is used to print component labels, logos, and other markings on the PCB surface.
HDI PCB Fabricators and Their Capabilities
HDI PCB fabrication requires specialized equipment, materials, and expertise that not all PCB manufacturers possess. The following table provides an overview of some leading HDI PCB fabricators and their capabilities:
Fabricator | Min. Via Diameter | Min. Line Width/Spacing | Max. Layer Count | Certifications |
---|---|---|---|---|
TTM Technologies | 50 µm | 30/30 µm | 24 | ISO 9001, AS9100, IATF 16949 |
Unimicron | 50 µm | 30/30 µm | 24 | ISO 9001, IATF 16949, ISO 14001 |
Compeq | 50 µm | 35/35 µm | 20 | ISO 9001, IATF 16949, ISO 14001 |
Tripod Technology | 75 µm | 50/50 µm | 16 | ISO 9001, IATF 16949, ISO 14001 |
Shennan Circuits | 50 µm | 30/30 µm | 24 | ISO 9001, IATF 16949, AS9100 |
These fabricators have invested in advanced manufacturing technologies and processes to meet the demanding requirements of HDI PCBs. They offer a range of HDI PCB solutions, from simple 2-layer designs to complex multi-layer boards with blind and buried vias.
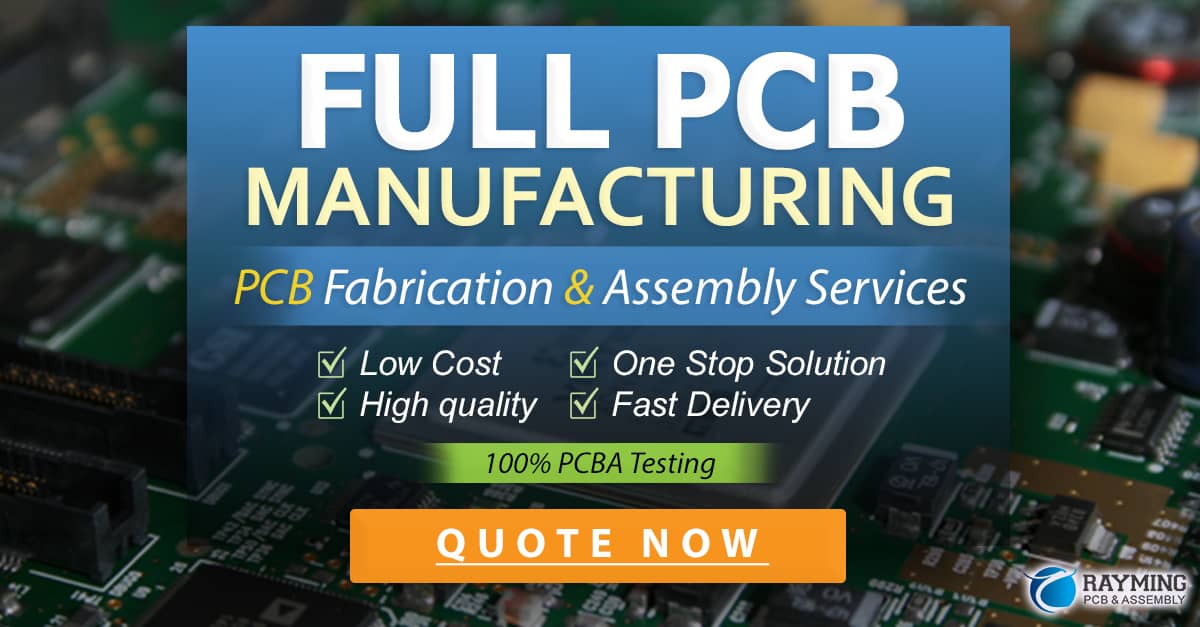
Challenges in HDI PCB Manufacturing
Despite the advances in HDI PCB technology, there are still several challenges that manufacturers and fabricators face:
1. Miniaturization
As electronic devices continue to shrink in size, the demand for even smaller and denser HDI PCBs grows. This requires continual investment in new manufacturing technologies and processes to achieve finer line widths, smaller vias, and tighter tolerances.
2. Signal Integrity
The high density of interconnections in HDI PCBs can lead to signal integrity issues, such as crosstalk, impedance mismatch, and signal loss. Manufacturers must employ advanced design techniques, such as impedance control, differential pair routing, and shielding, to mitigate these issues.
3. Thermal Management
The increased density of components in HDI PCBs can also result in higher heat generation and thermal management challenges. Manufacturers must incorporate effective thermal management solutions, such as thermal vias, heat sinks, and advanced substrate materials, to ensure reliable operation.
4. Cost
The complexity of HDI PCB manufacturing and the need for advanced equipment and materials can result in higher costs compared to traditional PCBs. Manufacturers must continuously optimize their processes and supply chains to minimize costs while maintaining the required quality and reliability.
Frequently Asked Questions (FAQ)
-
What is the difference between HDI PCBs and traditional PCBs?
HDI PCBs have a higher density of interconnections, finer line widths, and smaller via diameters compared to traditional PCBs. This allows for the creation of more compact and complex electronic devices. -
What are the advantages of using HDI PCBs?
The main advantages of HDI PCBs include reduced board size, improved electrical performance, increased functionality, and better signal integrity. HDI technology enables the miniaturization of electronic devices and the integration of more features into smaller form factors. -
What are the different types of vias used in HDI PCBs?
The common types of vias used in HDI PCBs are blind vias, buried vias, and microvias. Blind vias connect an outer layer to an inner layer, buried vias connect two or more inner layers, and microvias are small vias with diameters less than 150 microns. -
What materials are used in HDI PCB manufacturing?
Common substrate materials for HDI PCBs include FR-4, polyimide, and Rogers materials. The copper foil used in HDI PCBs is typically thinner than that used in traditional PCBs. Other materials include laminate, solder mask, and surface finish coatings. -
How can I choose the right HDI PCB fabricator for my project?
When selecting an HDI PCB fabricator, consider factors such as their manufacturing capabilities, quality certifications, experience with similar projects, and customer support. Review their minimum feature sizes, layer count limits, and available surface finishes to ensure they can meet your specific requirements. Request samples and references to assess their quality and reliability.
Conclusion
HDI PCBs have become essential components in the rapidly evolving world of electronic devices. Their ability to enable miniaturization, improved performance, and increased functionality has made them indispensable in a wide range of applications, from consumer electronics to aerospace and defense. HDI PCB manufacturers and fabricators play a crucial role in bringing these advanced circuit boards to life, leveraging cutting-edge technologies and processes to meet the ever-increasing demands of the industry.
As we look to the future, the importance of HDI PCBs will only continue to grow. With the advent of 5G networks, the Internet of Things (IoT), and artificial intelligence (AI), the need for smaller, faster, and more powerful electronic devices will drive further innovation in HDI PCB technology. Manufacturers and fabricators that can stay at the forefront of these developments, while addressing the challenges of miniaturization, signal integrity, thermal management, and cost, will be well-positioned to succeed in this dynamic and exciting industry.
0 Comments