Introduction to PCB Assembly
Printed Circuit Board (PCB) assembly is a crucial process in the manufacturing of electronic devices. It involves the placement and soldering of electronic components onto a printed circuit board. PCB assembly companies play a vital role in the electronics industry by providing high-quality, reliable, and cost-effective PCB assembly services.
Double sided PCB assembly is a type of PCB assembly where electronic components are placed and soldered on both sides of the printed circuit board. This allows for a higher density of components and more complex circuits compared to single sided PCB assembly.
Benefits of Double Sided PCB Assembly
Double sided PCB assembly offers several benefits over single sided PCB assembly:
-
Increased component density: Double sided PCB assembly allows for a higher density of components to be placed on the PCB, resulting in smaller and more compact electronic devices.
-
Improved circuit complexity: With components placed on both sides of the PCB, more complex circuits can be designed and manufactured.
-
Better signal integrity: Double sided PCB assembly can improve signal integrity by reducing the distance between components and minimizing signal interference.
-
Cost-effective: Despite the added complexity, double sided PCB assembly can be more cost-effective than single sided PCB assembly for certain applications due to the reduced PCB size and improved functionality.
Choosing a Double Sided PCB Assembly Company
When selecting a double sided PCB assembly company, there are several factors to consider to ensure you receive high-quality services that meet your requirements.
Experience and Expertise
Look for a company with extensive experience in double sided PCB assembly. Experienced companies will have the knowledge and expertise to handle complex projects and provide reliable services. They should be familiar with various PCB materials, components, and assembly techniques.
Manufacturing Capabilities
Assess the company’s manufacturing capabilities to ensure they can handle your specific project requirements. This includes:
- PCB fabrication capabilities (e.g., PCB materials, layer counts, minimum trace width and spacing)
- Component placement capabilities (e.g., types of components, placement accuracy, speed)
- Soldering technologies (e.g., wave soldering, reflow soldering, selective soldering)
- Quality control and inspection processes (e.g., automated optical inspection, X-ray inspection, functional testing)
Quality Standards and Certifications
Choose a company that adheres to strict quality standards and holds relevant certifications. Some common certifications for PCB assembly companies include:
- ISO 9001: Quality Management System
- ISO 14001: Environmental Management System
- IPC-A-610: Acceptability of Electronic Assemblies
- IPC J-STD-001: Requirements for Soldered Electrical and Electronic Assemblies
These certifications demonstrate the company’s commitment to quality, reliability, and environmental responsibility.
Lead Times and Pricing
Consider the company’s lead times and pricing structure. Fast turnaround times are essential for time-sensitive projects, while competitive pricing can help reduce overall project costs. However, be cautious of companies offering extremely low prices, as this may indicate compromises in quality or service.
Customer Support and Communication
Effective communication and responsive customer support are crucial for a successful PCB assembly project. Look for a company that provides clear communication channels, promptly responds to inquiries, and keeps you informed throughout the project.
The Double Sided PCB Assembly Process
The double sided PCB assembly process typically involves the following steps:
-
PCB Design and Fabrication: The PCB design is created using CAD software, and the PCB is fabricated according to the design specifications.
-
Solder Paste Application: Solder paste is applied to the PCB pads using a stencil or screen printing process. This process is performed on both sides of the PCB for double sided assembly.
-
Component Placement: Surface mount components are placed onto the solder paste using pick-and-place machines. The components are placed on both sides of the PCB, with the bottom side components placed first.
-
Soldering: The PCB with placed components undergoes a soldering process to establish electrical connections. This is typically done using reflow soldering, where the PCB is heated in a reflow oven to melt the solder paste and create a bond between the components and PCB pads.
-
Inspection and Testing: After soldering, the assembled PCB undergoes various inspection and testing procedures to ensure quality and functionality. This may include automated optical inspection (AOI), X-ray inspection, and functional testing.
-
Conformal Coating (Optional): In some cases, a conformal coating may be applied to the assembled PCB to protect it from environmental factors such as moisture, dust, and chemicals.
-
Final Assembly and Packaging: The assembled PCB is then integrated into the final product or packaged for shipment to the customer.
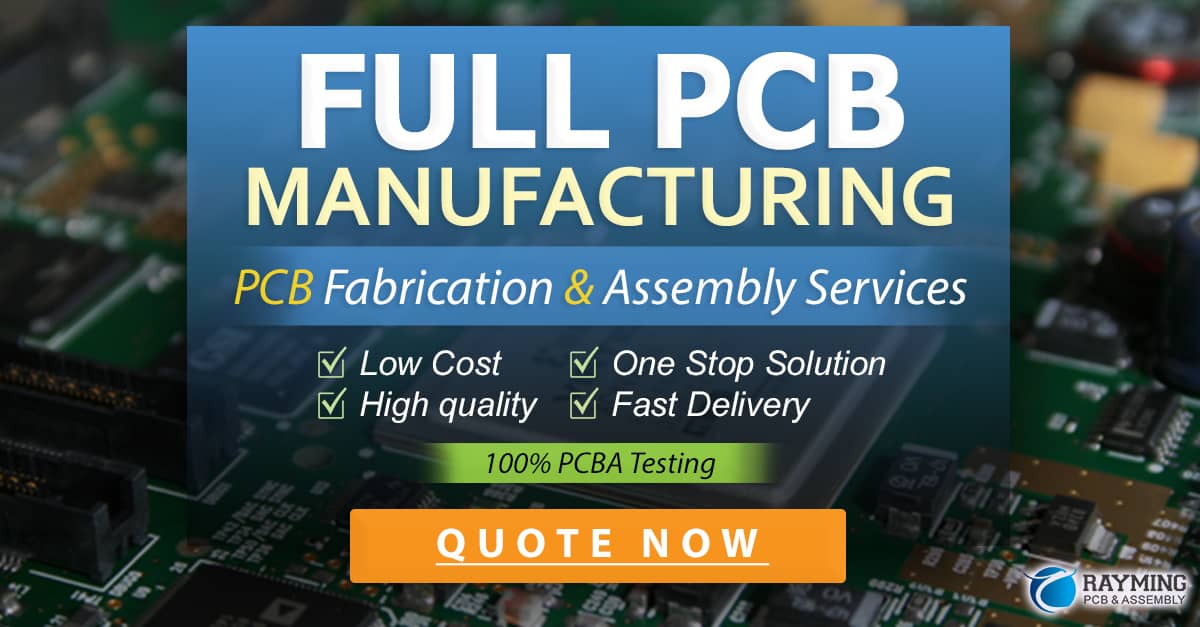
Challenges in Double Sided PCB Assembly
Double sided PCB assembly presents some unique challenges compared to single sided assembly:
-
Component Placement Accuracy: Ensuring precise component placement on both sides of the PCB can be challenging, especially for small or fine-pitch components.
-
Soldering Process Control: Achieving uniform and reliable solder joints on both sides of the PCB requires careful control of the soldering process parameters, such as temperature, time, and conveyor speed.
-
Warpage and Thermal Management: Double sided PCBs are more susceptible to warpage during the soldering process due to the different thermal expansion rates of the components and PCB material. Proper thermal management and PCB design techniques are essential to minimize warpage.
-
Inspection and Testing: Inspecting and testing double sided PCBs can be more complex and time-consuming than single sided PCBs, as both sides of the board need to be checked for quality and functionality.
Experienced double sided PCB assembly companies employ various techniques and technologies to overcome these challenges and ensure high-quality assembly results.
Selecting the Right Components for Double Sided PCB Assembly
Choosing the right components is crucial for successful double sided PCB assembly. Consider the following factors when selecting components:
-
Package Type: Select components with package types that are suitable for double sided assembly, such as surface mount devices (SMDs) and ball grid arrays (BGAs).
-
Component Size and Pitch: Consider the size and pitch of the components to ensure they can be accurately placed and soldered on both sides of the PCB.
-
Thermal Characteristics: Choose components with thermal characteristics that are compatible with the soldering process and PCB material to minimize the risk of thermal damage or warpage.
-
Availability and Lead Time: Ensure that the selected components are readily available and have acceptable lead times to avoid delays in the assembly process.
-
Cost: Consider the cost of the components and their impact on the overall project budget. However, avoid compromising on quality for the sake of cost savings.
Working closely with your PCB assembly company and component suppliers can help ensure the selection of appropriate components for your double sided PCB assembly project.
Design Considerations for Double Sided PCB Assembly
Proper PCB design is essential for successful double sided PCB assembly. Consider the following design guidelines:
-
Component Placement: Optimize component placement to minimize the risk of interference and ensure adequate spacing for soldering and inspection. Place larger and heavier components on the bottom side of the PCB to prevent tombstoning during soldering.
-
Thermal Management: Incorporate proper thermal management techniques, such as thermal vias and copper pours, to dissipate heat evenly and prevent warpage.
-
Signal Integrity: Ensure proper signal routing and impedance control to maintain signal integrity and minimize crosstalk between layers.
-
Solder Mask and Silkscreen: Use a clear and accurate solder mask and silkscreen to aid in component placement and soldering. Ensure that the solder mask openings are properly sized to prevent solder bridging.
-
Panelization: Consider panelizing the PCB design to facilitate efficient assembly and handling. Incorporate appropriate panelization techniques, such as tab routing and V-scoring, to ensure easy depanelization without damaging the PCBs.
Collaborating with your PCB assembly company during the design phase can help optimize your PCB design for double sided assembly and prevent potential issues down the line.
Table 1: Comparison of Single Sided and Double Sided PCB Assembly
Feature | Single Sided PCB Assembly | Double Sided PCB Assembly |
---|---|---|
Component Density | Lower | Higher |
Circuit Complexity | Simpler | More Complex |
Signal Integrity | Adequate | Improved |
Cost | Lower | Higher (but can be cost-effective for certain applications) |
Assembly Process | Simpler | More Complex |
Thermal Management | Easier | More Challenging |
Inspection and Testing | Simpler | More Complex |
Frequently Asked Questions (FAQ)
- What is the difference between single sided and double sided PCB assembly?
-
Single sided PCB assembly involves placing and soldering components on one side of the PCB, while double sided PCB assembly involves placing and soldering components on both sides of the PCB.
-
What are the benefits of double sided PCB assembly?
-
Double sided PCB assembly offers increased component density, improved circuit complexity, better signal integrity, and can be cost-effective for certain applications compared to single sided PCB assembly.
-
What factors should I consider when choosing a double sided PCB assembly company?
-
When choosing a double sided PCB assembly company, consider factors such as experience and expertise, manufacturing capabilities, quality standards and certifications, lead times and pricing, and customer support and communication.
-
What are some challenges in double sided PCB assembly?
-
Challenges in double sided PCB assembly include ensuring component placement accuracy, controlling the soldering process, managing warpage and thermal issues, and conducting complex inspection and testing procedures.
-
How can I ensure successful double sided PCB assembly?
- To ensure successful double sided PCB assembly, select appropriate components, optimize your PCB design for double sided assembly, and work closely with your PCB assembly company throughout the project.
Conclusion
Double sided PCB assembly is a complex process that requires expertise, advanced manufacturing capabilities, and attention to detail. By understanding the benefits, challenges, and key considerations involved in double sided PCB assembly, you can make informed decisions when selecting a PCB assembly company and ensuring the success of your project.
When choosing a double sided PCB assembly company, prioritize experience, manufacturing capabilities, quality standards, and customer support. Work closely with your assembly partner throughout the project, from design to final assembly, to optimize your PCB design, select appropriate components, and overcome any challenges that may arise.
By partnering with a reliable and experienced double sided PCB assembly company, you can leverage the benefits of this advanced assembly technique to create high-quality, complex, and compact electronic devices that meet your specific requirements.
0 Comments