Introduction to PCB fabrication
Printed Circuit Board (PCB) fabrication is a complex process that involves several steps to turn a circuit design into a functional physical board. Understanding the PCB fabrication process is essential for anyone involved in electronics design and manufacturing. In this comprehensive guide, we will demystify the PCB fabrication process, covering everything from PCB design to the final product.
PCB Design and Preparation
Schematic Design
The first step in PCB fabrication is creating a schematic design. A schematic is a graphical representation of the electronic circuit, showing all the components and their interconnections. Designers use Electronic Design Automation (EDA) software to create schematics, such as OrCAD, Eagle, or KiCad.
PCB Layout
Once the schematic is complete, the next step is to create the PCB layout. The layout determines the physical placement of components and the routing of traces on the board. Designers use EDA software to create the layout, following best practices for component placement, trace routing, and signal integrity.
Gerber File Generation
After finalizing the PCB layout, designers generate Gerber files, which are the standard format for PCB fabrication. Gerber files contain all the necessary information for manufacturing the PCB, including the copper layers, solder mask, silkscreen, and drill holes.
PCB Fabrication Process
Step 1: Material Preparation
The PCB fabrication process begins with preparing the base material, usually a copper-clad laminate. The most common base materials are FR-4, a glass-reinforced epoxy laminate, and polyimide for high-temperature applications. The copper-clad laminate is cut to the desired size and cleaned to remove any contaminants.
Step 2: Drilling
The next step is drilling holes in the laminate for through-hole components and vias. CNC machines or laser drills are used to create precise holes based on the drill file generated from the PCB layout.
Step 3: Copper Patterning
After drilling, the copper layer is patterned according to the PCB layout. There are two main methods for copper patterning:
- Subtractive Process (Etching):
- The entire copper surface is covered with a photoresist layer.
- The photoresist is exposed to UV light through a photomask, which hardens the exposed areas.
- The unexposed photoresist is removed, leaving the copper exposed in those areas.
- The exposed copper is etched away using a chemical solution, leaving only the desired copper pattern.
-
The remaining photoresist is stripped off, revealing the final copper pattern.
-
Additive Process (Electroplating):
- A thin layer of copper is deposited on the laminate.
- A photoresist layer is applied and exposed to UV light through a photomask.
- The unexposed photoresist is removed, exposing the areas where additional copper will be deposited.
- The board is placed in an electroplating bath, where additional copper is deposited onto the exposed areas.
- The photoresist is stripped off, leaving the final copper pattern.
Step 4: Lamination (for Multi-layer PCBs)
For multi-layer PCBs, the individual layers are laminated together using heat and pressure. The layers are aligned precisely and bonded using a prepreg material, which is an uncured glass-reinforced epoxy sheet.
Step 5: Solder Mask Application
A solder mask is a protective layer applied to the PCB to prevent solder bridges and protect the copper traces from oxidation. The solder mask is typically green but can be other colors as well. The solder mask is applied using a silkscreen printing process or photoimaging.
Step 6: Silkscreen Printing
Silkscreen printing is used to add text, logos, and component identifiers to the PCB. The silkscreen is typically white but can be any color. The silkscreen ink is applied using a stencil and cured using UV light or heat.
Step 7: Surface Finish
The exposed copper areas, such as pads and through-holes, require a surface finish to prevent oxidation and enhance solderability. There are several surface finish options, including:
- Hot Air Solder Leveling (HASL): A thin layer of solder is applied to the copper areas using a hot air knife.
- Organic Solderability Preservative (OSP): A thin organic compound layer is applied to the copper areas to prevent oxidation.
- Electroless Nickel Immersion Gold (ENIG): A layer of nickel is deposited on the copper areas, followed by a thin layer of gold.
- Immersion Silver: A thin layer of silver is deposited on the copper areas.
Step 8: Electrical Testing
After the PCB fabrication is complete, the boards undergo electrical testing to ensure they function as intended. Automated Optical Inspection (AOI) machines are used to inspect the PCBs for any defects, such as shorts, opens, or incorrect component placement.
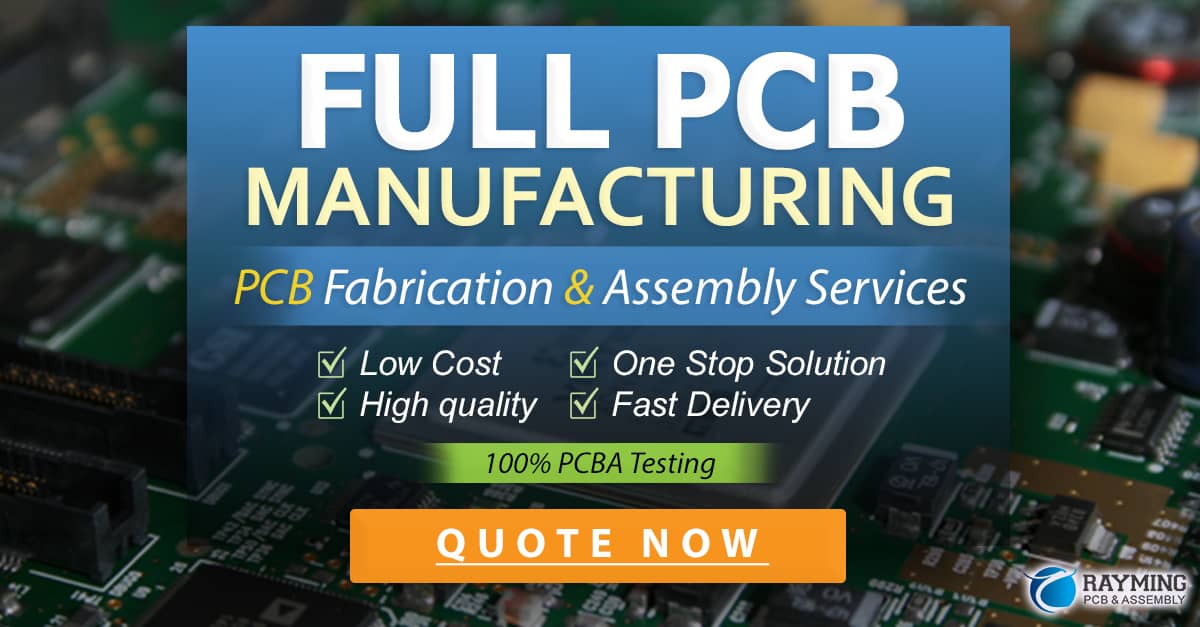
PCB Fabrication Considerations
Material Selection
Choosing the right base material is crucial for the performance and reliability of the PCB. Factors to consider when selecting the base material include:
- Dielectric constant
- Thermal conductivity
- Glass transition temperature
- Moisture absorption
- Cost
Some common base materials and their properties are:
Material | Dielectric Constant | Thermal Conductivity (W/mK) | Glass Transition Temperature (°C) | Moisture Absorption (%) | Typical Applications |
---|---|---|---|---|---|
FR-4 | 4.2 – 4.5 | 0.3 – 0.4 | 130 – 140 | 0.1 – 0.3 | General-purpose, low-cost PCBs |
Polyimide | 3.2 – 3.5 | 0.2 – 0.3 | 250 – 300 | 0.4 – 0.8 | High-temperature, flexible PCBs |
Rogers | 2.2 – 10.2 | 0.2 – 1.5 | 280 – 360 | 0.02 – 0.1 | High-frequency, low-loss applications |
Teflon | 2.0 – 2.1 | 0.2 – 0.3 | 327 | < 0.01 | High-frequency, microwave applications |
Copper Thickness
The copper thickness on a PCB is measured in ounces per square foot (oz/ft²). Common copper thicknesses are 0.5 oz/ft², 1 oz/ft², and 2 oz/ft², which correspond to 17.5 µm, 35 µm, and 70 µm, respectively. Thicker copper layers are used for high-current applications or to improve signal integrity.
Trace Width and Spacing
The trace width and spacing on a PCB depend on the current carrying requirements, signal integrity, and PCB manufacturing capabilities. Typical trace widths range from 0.1 mm to 0.5 mm, while trace spacing can be as low as 0.1 mm for fine-pitch designs.
Via Types
Vias are used to connect traces on different layers of a multi-layer PCB. There are several types of vias:
- Through-hole vias: These vias go through the entire thickness of the PCB and are used for through-hole components or to connect traces on different layers.
- Blind vias: These vias start from an outer layer and end at an inner layer, without going through the entire PCB.
- Buried vias: These vias connect inner layers without reaching either outer layer.
- Micro vias: These are small vias, typically less than 0.15 mm in diameter, used for high-density interconnects.
Solder Mask and Silkscreen
The solder mask and silkscreen are essential for protecting the PCB and providing useful information. When designing the solder mask and silkscreen, consider the following:
- Solder mask clearance: Ensure adequate clearance around pads and vias to prevent solder bridges.
- Silkscreen legibility: Use clear, legible fonts and ensure that the silkscreen does not overlap with pads or other features.
- Solder mask color: Choose a solder mask color that provides good contrast with the silkscreen and any LED indicators.
PCB Fabrication Troubleshooting
Despite careful design and fabrication, issues can arise during the PCB manufacturing process. Some common problems and their solutions are:
Copper Overetching
Copper overetching occurs when the etching process removes too much copper, resulting in thin or broken traces. To prevent overetching, ensure that the etching parameters (time, temperature, and concentration) are optimized and that the photoresist is properly exposed and developed.
Solder Mask Peeling
Solder mask peeling can occur due to poor adhesion between the solder mask and the copper surface. To prevent peeling, ensure that the copper surface is clean and roughened before applying the solder mask. Also, choose a solder mask material that is compatible with the base material and the surface finish.
Silkscreen Smudging
Silkscreen smudging can occur if the silkscreen ink is not properly cured or if the stencil is not aligned correctly. To prevent smudging, ensure that the silkscreen ink is compatible with the solder mask and that the curing process is optimized. Also, use a high-quality stencil and align it carefully with the PCB features.
Drill Misalignment
Drill misalignment can occur if the drill file is not properly generated or if the drilling machine is not calibrated correctly. To prevent misalignment, ensure that the drill file is generated using the correct parameters and that the drilling machine is regularly calibrated and maintained.
FAQ
What is the typical turnaround time for PCB fabrication?
The turnaround time for PCB fabrication depends on the complexity of the design, the number of layers, and the fabrication house’s workload. Typical turnaround times range from 2-3 days for simple, quick-turn designs to 2-3 weeks for complex, multi-layer designs.
What is the minimum feature size for PCB traces and spacing?
The minimum feature size depends on the PCB fabrication house’s capabilities and the chosen manufacturing process. Typical minimum feature sizes are:
– For standard PCBs: 0.1 mm trace width and spacing
– For high-density interconnect (HDI) PCBs: 0.075 mm trace width and spacing
Can I fabricate a PCB with a non-standard shape?
Yes, PCBs can be fabricated in non-standard shapes, such as circles or irregular shapes. However, non-standard shapes may require additional tooling and may be more expensive than standard rectangular PCBs.
What is the maximum number of layers for a PCB?
The maximum number of layers depends on the PCB fabrication house’s capabilities and the chosen base material. Typical maximum layer counts are:
– For standard PCBs: 12-16 layers
– For advanced PCBs: 24-48 layers
– For specialized PCBs: 50+ layers
How do I choose the right surface finish for my PCB?
The choice of surface finish depends on the application, the components used, and the environmental conditions. Consider the following factors:
– Solderability: HASL and ENIG provide excellent solderability, while OSP and Immersion Silver may require additional processing.
– Shelf life: ENIG and Immersion Silver provide longer shelf life than OSP.
– Cost: OSP and HASL are generally less expensive than ENIG and Immersion Silver.
– Compatibility: Ensure that the surface finish is compatible with the components and the assembly process.
Conclusion
PCB fabrication is a complex process that involves several steps, from design to final assembly. By understanding the PCB fabrication process, designers can make informed decisions about material selection, feature sizes, and surface finishes. Proper design and fabrication considerations can help prevent common issues, such as overetching, solder mask peeling, and drill misalignment. With the right knowledge and tools, designers can create high-quality, reliable PCBs that meet their application’s requirements.
0 Comments