Introduction to Controlled Impedance PCBs
In today’s fast-paced world of electronics, the demand for high-speed digital systems and high-frequency analog circuits has increased significantly. As a result, the importance of maintaining signal integrity in printed circuit boards (PCBs) has become paramount. One crucial aspect of ensuring signal integrity is the use of controlled impedance PCBs, which are designed to minimize signal distortion, reflections, and crosstalk.
Controlled impedance PCBs are characterized by their precisely designed copper traces, which have a specific impedance value that matches the characteristic impedance of the connected components and transmission lines. By maintaining a consistent impedance throughout the signal path, controlled impedance PCBs minimize signal integrity issues and ensure reliable data transmission.
What is Impedance?
Before delving into the details of controlled impedance PCBs, it is essential to understand the concept of impedance. Impedance is a measure of the opposition that a circuit presents to the flow of alternating current (AC) at a given frequency. It is a complex quantity that consists of both resistance and reactance, and is measured in ohms (Ω).
In a PCB, the impedance of a copper trace is determined by several factors, including its width, thickness, dielectric constant of the substrate material, and the proximity of other conductive layers or traces. By carefully designing these parameters, PCB manufacturers can create controlled impedance traces that match the desired impedance value.
Why is Controlled Impedance Important?
Controlled impedance is crucial in high-speed digital systems and high-frequency analog circuits for several reasons:
-
Signal Integrity: Controlled impedance PCBs help maintain signal integrity by minimizing signal reflections, distortions, and crosstalk. When the impedance of a trace matches the characteristic impedance of the connected components and transmission lines, the signal can propagate without encountering impedance mismatches, which can cause reflections and distortions.
-
Timing and Synchronization: In high-speed digital systems, proper timing and synchronization are essential for reliable data transmission. Controlled impedance traces ensure that signals arrive at their intended destinations at the correct time, avoiding timing errors and data corruption.
-
EMI and Noise Reduction: Controlled impedance PCBs can help reduce electromagnetic interference (EMI) and noise by minimizing signal reflections and crosstalk. This is particularly important in sensitive analog circuits and high-frequency applications where EMI can degrade signal quality and cause malfunctions.
Designing Controlled Impedance PCBs
Designing controlled impedance PCBs requires careful consideration of several factors, including the desired impedance value, the PCB Stack-up, trace geometry, and the dielectric properties of the substrate material. Here are some key aspects of controlled impedance PCB design:
Impedance Calculation
The first step in designing controlled impedance PCBs is to calculate the desired impedance value. This value is typically determined by the requirements of the connected components and transmission lines, such as the characteristic impedance of a cable or the input/output impedance of an integrated circuit (IC).
There are several methods for calculating the impedance of a PCB trace, including:
-
Transmission Line Equations: These equations, such as the microstrip and stripline equations, can be used to calculate the impedance of a trace based on its geometry and the dielectric properties of the substrate material.
-
Impedance Calculators: Many PCB design software packages include impedance calculators that can automatically determine the required trace geometry for a given impedance value and substrate material.
-
Simulation Tools: Advanced simulation tools, such as electromagnetic field solvers, can provide more accurate impedance calculations by taking into account the effects of adjacent traces, power planes, and other conductive layers.
PCB Stack-up and Material Selection
The PCB stack-up and material selection play a crucial role in achieving controlled impedance traces. The stack-up refers to the arrangement of conductive and dielectric layers in a PCB, while the material selection involves choosing the appropriate substrate and copper foil for the desired electrical and mechanical properties.
When designing a controlled impedance PCB, consider the following:
-
Dielectric Constant (Dk): The dielectric constant of the substrate material determines the speed of signal propagation and affects the impedance of the traces. Materials with a lower Dk, such as Rogers 4000 series or Isola FR408, are often used in high-speed applications to achieve lower impedance values and faster signal propagation.
-
Dielectric Thickness: The thickness of the dielectric layer between the trace and the reference plane (usually ground or power) affects the impedance of the trace. Thinner dielectric layers result in lower impedance values, while thicker layers result in higher impedance values.
-
Copper Thickness: The thickness of the copper foil used for the traces affects their resistance and current-carrying capacity. Thicker copper foils are often used in power delivery networks and high-current applications, while thinner foils are preferred for high-speed signals to minimize skin effect losses.
-
Reference Planes: Controlled impedance traces require a solid reference plane, such as a ground or power plane, to maintain a consistent impedance along their length. The reference plane should be as close to the trace as possible to minimize the dielectric thickness and achieve the desired impedance value.
Trace Geometry
The geometry of the copper traces, including their width, spacing, and routing topology, is another critical factor in achieving controlled impedance. The trace geometry affects the impedance value and the susceptibility to crosstalk and EMI.
Consider the following guidelines when designing controlled impedance traces:
-
Trace Width: The width of the trace determines its impedance value, with narrower traces resulting in higher impedance and wider traces resulting in lower impedance. The trace width should be calculated based on the desired impedance value, the dielectric properties of the substrate material, and the PCB stack-up.
-
Trace Spacing: The spacing between adjacent traces affects their coupling and crosstalk. To minimize crosstalk, traces should be spaced apart by at least three times their width, or shielded by grounded traces or planes.
-
Routing Topology: The routing topology of the traces, such as microstrip, stripline, or coplanar waveguide, affects their impedance and susceptibility to external noise and interference. Microstrip traces are exposed on the outer layers of the PCB, making them more susceptible to EMI, while stripline traces are sandwiched between reference planes, providing better shielding and noise immunity.
Manufacturing Considerations
Manufacturing controlled impedance PCBs requires specialized equipment and processes to ensure that the designed impedance values are achieved consistently across the board. Some key manufacturing considerations include:
Impedance Testing
Impedance testing is performed to verify that the manufactured PCB meets the specified impedance requirements. This testing typically involves using a time-domain reflectometer (TDR) or a vector network analyzer (VNA) to measure the impedance of the traces at various locations on the board.
The impedance testing process may involve the following steps:
-
Coupon Testing: Test coupons, which are small PCB sections with controlled impedance traces, are often included in the PCB panel to facilitate impedance testing. These coupons are measured to ensure that the impedance values are within the specified tolerance before proceeding with the production of the main PCB.
-
In-Circuit Testing: In some cases, impedance testing may be performed directly on the assembled PCB using specialized probes and test fixtures. This approach allows for the measurement of the actual impedance values in the final product, taking into account the effects of components, solder joints, and other manufacturing variations.
Impedance Control in Manufacturing
To achieve consistent impedance values across the PCB, manufacturers must implement strict process controls and use specialized equipment. Some key aspects of impedance control in manufacturing include:
-
Dielectric Thickness Control: The thickness of the dielectric layers must be tightly controlled to maintain the designed impedance values. This is achieved through precise lamination processes and the use of high-quality substrate materials with consistent dielectric properties.
-
Copper Thickness Control: The thickness of the copper foil used for the traces must be carefully controlled to ensure consistent impedance values. This is achieved through precise etching processes and the use of high-quality copper foils with consistent thickness and surface roughness.
-
Trace Width and Spacing Control: The width and spacing of the traces must be tightly controlled to maintain the designed impedance values and minimize crosstalk. This is achieved through precise etching and plating processes, as well as the use of high-resolution photolithography and laser-direct imaging (LDI) techniques.
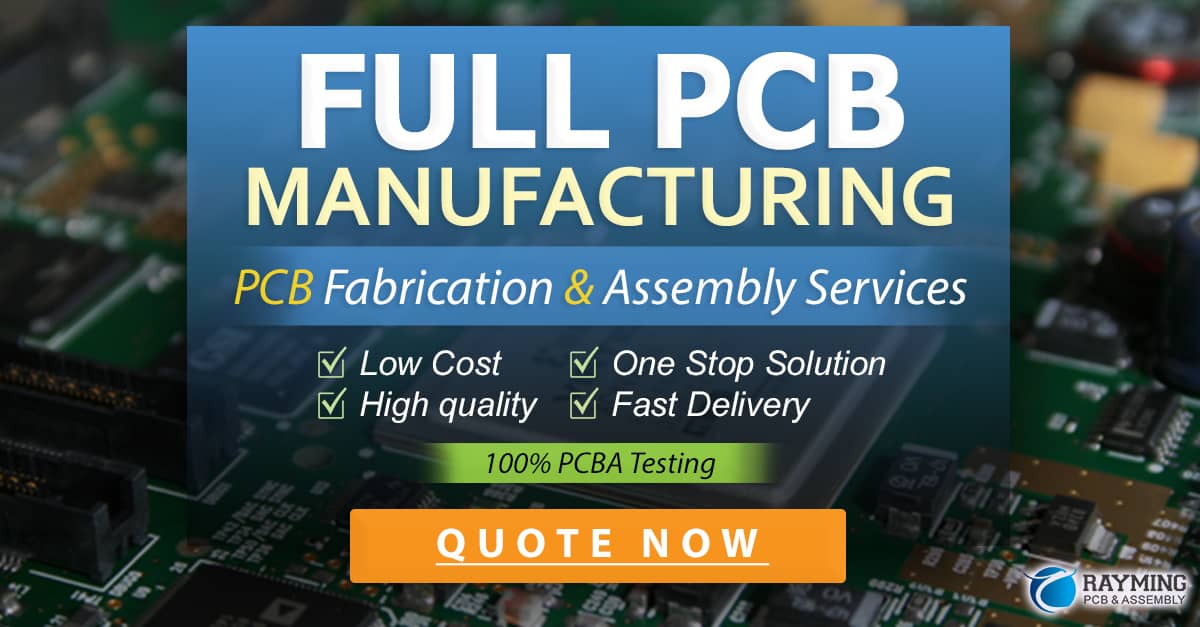
Applications of Controlled Impedance PCBs
Controlled impedance PCBs are used in a wide range of applications where signal integrity, timing, and noise reduction are critical. Some common applications include:
-
High-Speed Digital Systems: Controlled impedance PCBs are essential in high-speed digital systems, such as computer processors, memory modules, and communication interfaces (e.g., USB, PCIe, HDMI), where data rates can exceed several gigabits per second.
-
RF and Microwave Circuits: In radio frequency (RF) and microwave circuits, controlled impedance PCBs are used to ensure proper impedance matching between components and transmission lines, minimizing signal reflections and power loss.
-
Automotive Electronics: As automotive systems become increasingly complex and reliant on high-speed data communication, controlled impedance PCBs are used to ensure reliable and robust performance in harsh environmental conditions.
-
Medical Devices: Controlled impedance PCBs are used in medical devices, such as imaging systems and patient monitoring equipment, where signal integrity and reliability are critical for accurate diagnoses and patient safety.
-
Aerospace and Defense: In aerospace and defense applications, controlled impedance PCBs are used in radar systems, satellite communication equipment, and avionics, where high-frequency signals and extreme environmental conditions demand robust and reliable performance.
FAQ
1. What is the difference between microstrip and stripline controlled impedance traces?
Microstrip and stripline are two common routing topologies used in controlled impedance PCBs. The main differences between them are:
-
Microstrip traces are exposed on the outer layers of the PCB, with a single reference plane beneath them. They are easier to route and have lower manufacturing costs, but are more susceptible to EMI and have higher impedance values compared to stripline traces of the same width.
-
Stripline traces are sandwiched between two reference planes, typically in the inner layers of the PCB. They provide better shielding and noise immunity, and have lower impedance values compared to microstrip traces of the same width. However, they are more challenging to route and have higher manufacturing costs.
2. How does the dielectric constant of the substrate material affect the impedance of a trace?
The dielectric constant (Dk) of the substrate material affects the impedance of a trace in two ways:
-
Signal Propagation Speed: A higher Dk results in slower signal propagation, as the electromagnetic waves interact more strongly with the dielectric material. This can lead to longer signal delays and increased dispersion.
-
Impedance Value: For a given trace geometry and dielectric thickness, a higher Dk results in lower impedance values. This is because the higher Dk increases the capacitance between the trace and the reference plane, lowering the characteristic impedance of the trace.
3. What is the purpose of test coupons in controlled impedance PCB manufacturing?
Test coupons are small PCB sections with controlled impedance traces that are included in the PCB panel to facilitate impedance testing during manufacturing. The purpose of test coupons is to:
-
Verify Impedance Values: By measuring the impedance of the test coupons, manufacturers can ensure that the actual impedance values are within the specified tolerance before proceeding with the production of the main PCB.
-
Monitor Process Consistency: Test coupons provide a means to monitor the consistency of the manufacturing process, allowing for early detection and correction of any deviations from the desired impedance values.
-
Reduce Testing Time and Cost: By using test coupons, manufacturers can perform impedance testing without the need to probe the main PCB, saving time and reducing the risk of damage to the final product.
4. How can crosstalk be minimized in controlled impedance PCBs?
Crosstalk, which is the unintended coupling of signals between adjacent traces, can be minimized in controlled impedance PCBs through several techniques:
-
Increased Trace Spacing: By increasing the spacing between adjacent traces, the coupling between them is reduced. A general guideline is to keep the trace spacing at least three times the trace width.
-
Shielding: Grounded traces or planes can be placed between adjacent signal traces to provide shielding and reduce crosstalk. This technique is particularly effective in stripline configurations, where the signal traces are sandwiched between reference planes.
-
Differential Signaling: Using differential signaling, where each signal is transmitted over a pair of traces with opposite polarity, can help cancel out the electromagnetic fields and reduce crosstalk.
-
Tight Impedance Control: By ensuring that all traces have a consistent and well-controlled impedance, the impact of any remaining crosstalk can be minimized, as the signals will be less susceptible to distortion and noise.
5. What are the advantages of using a VNA for impedance testing compared to a TDR?
A vector network analyzer (VNA) offers several advantages over a time-domain reflectometer (TDR) for impedance testing of controlled impedance PCBs:
-
Frequency-Domain Analysis: VNAs measure the impedance and other S-parameters of the traces over a wide range of frequencies, providing a more comprehensive characterization of the PCB’s performance. This is particularly useful for high-frequency applications where the frequency-dependent behavior of the traces is critical.
-
Higher Accuracy: VNAs typically offer higher accuracy and dynamic range compared to TDRs, allowing for more precise measurements of the impedance values and S-parameters.
-
Nondestructive Testing: Unlike TDRs, which inject a high-energy pulse into the trace, VNAs use low-power RF signals for testing, minimizing the risk of damage to the PCB or its components.
-
Advanced Analysis Capabilities: VNAs often come with powerful software tools for data analysis and visualization, enabling users to perform complex tasks such as de-embedding, time-domain reflectometry (TDR) emulation, and eye diagram analysis.
However, VNAs are generally more expensive and complex to operate compared to TDRs, and may not be necessary for all controlled impedance PCB applications. TDRs remain a popular choice for many manufacturers due to their simplicity, lower cost, and ability to provide quick and intuitive impedance measurements in the time domain.
Parameter | Microstrip | Stripline |
---|---|---|
Location | Outer layers | Inner layers |
Reference Planes | Single (below trace) | Dual (above and below trace) |
Shielding | Less | More |
Impedance (same width) | Higher | Lower |
Routing Complexity | Lower | Higher |
Manufacturing Cost | Lower | Higher |
Table 1: Comparison of microstrip and stripline controlled impedance traces.
Material | Dielectric Constant (Dk) | Dissipation Factor (Df) | Typical Applications |
---|---|---|---|
FR-4 | 4.3 – 4.7 | 0.02 – 0.03 | General-purpose, low-cost |
Rogers 4350B | 3.48 | 0.0037 | High-frequency, low-loss |
Isola I-Tera MT40 | 3.45 – 3.60 | 0.0030 – 0.0034 | High-speed digital, automotive |
Nelco N4000-13SI | 3.14 | 0.0035 | RF and microwave, aerospace |
Table 2: Common substrate materials for controlled impedance PCBs.
Impedance (Ω) | Trace Width (mil) | Dielectric Thickness (mil) | Dielectric Constant (Dk) |
---|---|---|---|
50 | 15.7 | 7.8 | 4.3 |
75 | 7.9 | 7.8 | 4.3 |
100 | 4.7 | 7.8 | 4.3 |
Table 3: Example trace widths for common impedance values (microstrip, 1 oz. copper, FR-4 substrate).
0 Comments